Kieran
East of England
Posts: 148
|
|
Nov 26, 2018 15:58:34 GMT
|
Thanks! Good question, I tried to position the return pipe bung close to the top edge of the pan, I couldn't see how it could be positioned much higher than that, due to the overhanging lip on the pan and the fact that I'll need to get a 10AN nut on the thread as well... I located it on the front side of the pan so it exits between the oil filter and exhaust manifold, again I couldn't see any other position where it could practically live. It looks fairly consistent with other oil return setups I've seen, indeed higher up than some, but I'm no expert, always open to advice 
|
|
Last Edit: Nov 26, 2018 16:00:16 GMT by Kieran
|
|
|
goldnrust
West Midlands
Minimalist
Posts: 1,889
|
|
Nov 27, 2018 21:42:19 GMT
|
Looks like this is coming on well! I've got a feeling it's gonna look pretty mean when you've got the new wheels on with the front lip and lowered springs.
It's been a while since I was doing my research for turbo-ing my mx5, but if I remember correctly, in theory you do want the oil drain to enter the sump above the oil level. The risk with it going below the oil level is that the oil flow could be restricted, causing potential turbo seal issues. I also read some stuff about oil coming back from the turbo being potentially frothy and that if the drain returned below the oil level the brother would get mixed with the main oil and potentially sucked into the oil pump, no idea how much of that was just conjecture though.
That said, looking at your build, your oil return has gotta be close to the top of the oil level, as you say you couldn't put it much higher, and with your turbo mounted up high, there will be a good drop for the oil to drain down to the sump so I'd think flow wouldn't be a problem. It would have to back up a long way to cause any problems. Lots of home-brew turbo set-ups have less than optimal oil returns and they dot often seem to run into problems.
|
|
Last Edit: Nov 27, 2018 21:55:22 GMT by goldnrust
|
|
Kieran
East of England
Posts: 148
|
|
Nov 28, 2018 10:29:48 GMT
|
Thanks, it's been slow but steady progress. I do want it to look a bit meaner than it has, without being too OTT. I think the '6 does need a lip as there is nothing there as standard, not sure what to do about the rear spoiler situation yet as I don't like the standard one. Interesting comments regarding the oil drain, I guess I will pretty much have to run it and see. As you say, the drain hose is long-ish, and it's a decent diameter at 10AN. The pan doesn't seem to be very deep compared to some on other engines, so even though the drain is positioned close to the top lip it doesn't appear as high as the pan looks quite shallow. I've tried to do my research on the turbo conversion but it's not particularly well documented out there. The best resourse is a guy in the states who's successfully built a turbo MX6 V6 and did a series of youtube videos on the build, which I've watched multiple times. He used a sump pan with a drain bung that appeared to be in a similar poistion to where I located mine, so that gives me a bit of confidence at least... Here's pan after the wire brush and paint treatment. 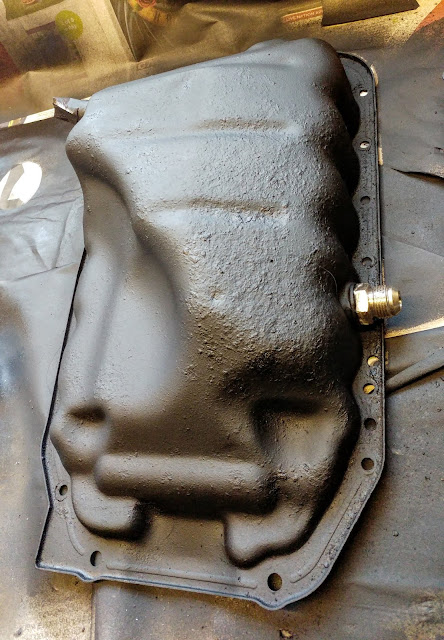 Also, I've received the final piece of the puzzle, I think I have all the parts I need now. It's an OBX Racing 12:1 FMU, another part unavailable here in the UK so I had it shipped from the states. For anyone who hasn't come across one, basically it provides a mechanical means of increasing fueling under boost, it's a rising rate fuel pressure regulator that ups fuel rail pressure in line with rising boost pressure. The 12:1 ratio means 12psi of fuel rail pressure for each 1psi of boost (in theory). 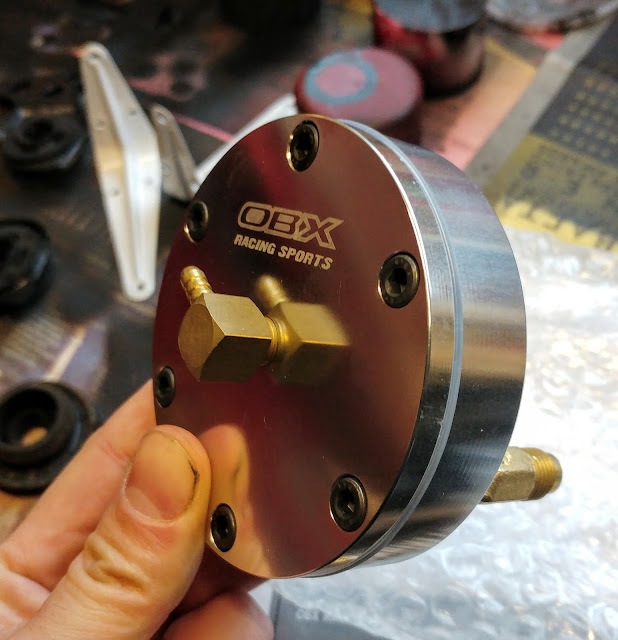 There is obviously limit to how much extra pressure your going to want in your fuel lines, so these are only really suitable for low boost applications. I'm going to initally be running circa 4psi so this should be a simple way to get things going. I've also larger injectors which means the base fuel pressure will be lower than standard, so boosting it will be less of an issue. As I mentioned previously, I've a piggy-back board to work with the standard ECU to convert to a MAF sensor and control fueling at idle and cruise.
|
|
Last Edit: Nov 28, 2018 12:45:35 GMT by Kieran
|
|
|
|
Nov 28, 2018 14:52:16 GMT
|
So 4 psi of boost will be an additional 3.3 bar of fuel pressure. the maths seem a little odd?
|
|
Last Edit: Nov 28, 2018 14:55:56 GMT by darrenh
|
|
Kieran
East of England
Posts: 148
|
|
Nov 28, 2018 15:01:26 GMT
|
Yeah pretty much, in theory a 12:1 FMU at 4psi will give you 4x12psi of additional fuel rail pressure. I'm thinking my base pressure will be set at around 30, so at 4psi that will be about 78psi of fuel pressure. It basically sits in the fuel return line and has a diaphragm that acts to pitch off the return to back flow the injectors. Actually one part I still need to buy and fit is an uprated fuel pump, the standard one won't be able to cut it...
|
|
|
|
|
|
Nov 28, 2018 15:56:50 GMT
|
|
|
'The reason i have pulled you over is to say how incredible and absolutely awesome that is'
Mercedes W109, Mercedes W140 S280 SWB & S320 LWB, W201 cosworth kitted, clk230 Kompressor, w109 300sel, Lincoln Continental 1964, BMW E30 Tech II tourer, MK1 Golf Clipper, BMW E31 840ci sport, JAGUAR XJ40 3.6, Kangoo van, Volvo 740GLE estate, Maserati Quattroporte GTS
|
|
Kieran
East of England
Posts: 148
|
|
Nov 28, 2018 16:36:48 GMT
|
Thanks Dean, I'll definitely give the link a squint!
|
|
|
|
goldnrust
West Midlands
Minimalist
Posts: 1,889
|
|
Nov 28, 2018 20:58:31 GMT
|
So 4 psi of boost will be an additional 3.3 bar of fuel pressure. the maths seem a little odd? The maths is more complex than it seems. 4psi is approximately 0.3 bar, which means the engine will be flowing 1.3x the normal amount of air. On top of that you'll need to go from 14.7:1 AFR to 12.5:1 AFR to be safe, which his about 1.2x increases fuel flow. Multiply those two factors together and you end up with a fuel need of 1.5x the normal flow. As the injector base pressure is 3bar, in a simplifed world you'd want 1.5x 3 bar, so 4.5 bar total fuel pressure, to supply enough fuel. What that doesn't take into account is that those injectors are now spraying into a pressurised environment, so they need a further 0.3 bar of pressure to keep the same flow rate, so now we're at 4.8 bar fuel pressure. On top of that, injectors are designed to run at that kinda 3bar pressure, so there may be a restriction inside the injector itself limiting flow rates, meaning that even if we have 1.5x standard pressure at the injector it still wont flow 1.5x the standard rate, so add in a bit of extra pressure to make up for that and it's easy to see why you might want an extra 3bar or more of fuel pressure. It's crude but will work to get you safe. Chances are you'll end up rich and the drivability at part throttle wont be great, but again from the mx5 turbo scene lots of people, including myself, ran them and it will work as long as you keep the boost low. I was able to use a RRFPR to keep my mx5 running safe upto 6psi with my stock fuel pump and upto 8psi with a Walbro 190LHP (which was the high pressure version). If your MAF doesn't top out, and you've got bigger injectors and a piggyback, will that not cover the feeling on it's own? Normally you'd use a RRFPR to force enough fuel into a turbo engine when using stock ECU and injectors. I would highly recommend investing in a Wideband o2 sensor/gauge to keep an eye on things 
|
|
Last Edit: Nov 28, 2018 21:00:42 GMT by goldnrust
|
|
Kieran
East of England
Posts: 148
|
|
Nov 28, 2018 21:44:16 GMT
|
Thanks for the info Goldnrust, interesting to know. I appreciate any advice as while I've done a fair bit of research, I've not built a turbo car before.
I went for the 12:1 FMU as I found that they'd been used with apparent success on a good number of other KL-DE turbo setups, I wanted something simple to get the motor running on low boost. I know it's something of a crude way to go but am hoping it will do the job. I take your point about not needing bigger injectors for an FMU, down the line I'd like to run an aftermarket ECU like Megasquirt or try a Speeduino, but they seem a bit of a project in their own right.
The piggyback ECU I'm going to use is a VAF to MAF converter, the standard VAF is restrictive. It basically takes the MAF signal and maps it to a VAF signal for the standard ECU, the converter has bluetooth and is controlled by an android app that allows you to map it. You can connect a narrowband or wideband lambda sensor to it to get an accurate map.
I've got a wideband gauge fitted in my three gauge panel, think it's pictured somewhere on the thread, along with a boost gauge. I was thinking of maybe adding a fuel pressure or oil pressure gauge for the third...
|
|
Last Edit: Nov 28, 2018 22:04:19 GMT by Kieran
|
|
goldnrust
West Midlands
Minimalist
Posts: 1,889
|
|
Nov 28, 2018 22:14:45 GMT
|
Sounds like you've done your research  My knowledge is all from my experience of turbo-ing my mx5 nearly 10 years ago, so different engine and probably some ideas that might be considered out of date now! Totally with you on having a simple set-up to get you started. I've built several Megasquirts, and they're brilliant, but as you say a big project in their own right. Last thing you wanna be doing right now is spending weeks trying to replicate what the factory ECU does by just getting the car to start and idle properly!
|
|
|
|
|
|
|
Nov 28, 2018 22:42:10 GMT
|
Apologies for negativity, I just couldn't get my head round a product designed and advocated, which sends injector pressure north of 6 bar.
|
|
|
|
|
|
Nov 29, 2018 11:36:44 GMT
|
Cracking project. How long until you build a low pressure forged engine, fit a ceramic bearing hybrid turbo and TURN UP THE BOOOOOST!!!! Watch out for "Danger to Manifold" tho..... Lol Always liked the shape of these, they should have been rwd
|
|
|
|
Kieran
East of England
Posts: 148
|
|
Nov 29, 2018 11:59:05 GMT
|
Sounds like you've done your research  My knowledge is all from my experience of turbo-ing my mx5 nearly 10 years ago, so different engine and probably some ideas that might be considered out of date now! Totally with you on having a simple set-up to get you started. I've built several Megasquirts, and they're brilliant, but as you say a big project in their own right. Last thing you wanna be doing right now is spending weeks trying to replicate what the factory ECU does by just getting the car to start and idle properly! I think you're knowledge seems sound, an FMU is a low-tech device isn't it, '70s/'80's technology really so I don't think thre is anything new to know about them. I'm attempting to keep things as simple as possible at least for starters, I think I could do a Megasquirt setup and who like to give it a go at some point. Apologies for negativity, I just couldn't get my head round a product designed and advocated, which sends injector pressure north of 6 bar. No worries Darren, I didn't take it that way, but in any case I'd much rather critical/neagative comments than no comments!  I do see your point, significantly raising the fuel pressure so much over standard does seem a little dicey on the face of it. The general rule of thumb seems to be that 100psi is a limit that you don't want to surpass, these FMU's have been used successfully by many so that do work with standard fuel lines apparently.
|
|
|
|
Kieran
East of England
Posts: 148
|
|
Nov 29, 2018 12:07:25 GMT
|
Cracking project. How long until you build a low pressure forged engine, fit a ceramic bearing hybrid turbo and TURN UP THE BOOOOOST!!!! Watch out for "Danger to Manifold" tho..... Lol Always liked the shape of these, they should have been rwd Ha!  Well as fun as that sounds I will try and resist the temptation to go too wild, I think around 300 horse will be the absolute limit on the standard motor and tranny... Yeah the MX6 is wrong wheel drive, but if it wasn't it would be popular with drifters and significantly more expensive, and I wouldn't be messing about doing a budget turbo one! Have you seen the prices of '90 RWD stuff like 200SX's recently?? Yikes.
|
|
|
|
|
|
Nov 29, 2018 12:10:03 GMT
|
I do see your point, significantly raising the fuel pressure so much over standard does seem a little dicey on the face of it. The general rule of thumb seems to be that 100psi is a limit that you don't want to surpass, these FMU's have been used successfully by many so that do work with standard fuel lines apparently. thats exactly it, peoples real world experience is greater value than my theory crafting. the reason i bought it up is that i've had a set of OEM bosch injectors (multi hole disk type) on a test rig, initially for post cleaning flow test, but turned into this might be interesting kind of thing. ramped the pressure up from their natural 3 bar to 6 (my pump locks out internally at 7.7). by 5 bar the spray pattern had disappeared into a squirt and by 6 bar two of them were not even closing fully. (they were being pulsed) but i agree with goldenrust, if you can achieve the delivery from larger injectors and altered dwell, while not going crazy on fuel pressure....
|
|
Last Edit: Nov 29, 2018 12:10:30 GMT by darrenh
|
|
Kieran
East of England
Posts: 148
|
|
Nov 29, 2018 13:45:37 GMT
|
That's very interesting about the injector spray patterns... I will aim to run the injectors at a better fuel pressure in the medium/long term. I've been giving some thought to what Goldnrust said above: If your MAF doesn't top out, and you've got bigger injectors and a piggyback, will that not cover the feeling on it's own? Normally you'd use a RRFPR to force enough fuel into a turbo engine when using stock ECU and injectors. If I can map the piggyback ECU to control the larger injectors so that they provide enough extra fuel with standard or somewhat raised fuel pressure, then I may not require the FMU, or if I did then maybe a lower ratio giving less of a fuel pressure rise. My thoughts were that I'd use the piggyback to provide good AFR's at idle and cruise, then the FMU would dump in the additional fuel under boost. I'm not sure how much airflow the MAF I'm planning to use will be able to handle, it's actually from a Mazda Xedos 9 which has the same basic KL-DE V6 motor which is why I chose it (the MX6 has a VAF as standard). I might have already mentioned this, but the standard MX6 injectors are about 220cc, the ones I have from a Mazda Millenia S are about 310cc.
|
|
Last Edit: Nov 29, 2018 13:47:58 GMT by Kieran
|
|
andyw
North East
Posts: 238
|
|
Nov 29, 2018 16:04:15 GMT
|
Cracking project. How long until you build a low pressure forged engine, fit a ceramic bearing hybrid turbo and TURN UP THE BOOOOOST!!!! Watch out for "Danger to Manifold" tho..... Lol Always liked the shape of these, they should have been rwd Ha!  Well as fun as that sounds I will try and resist the temptation to go too wild, I think around 300 horse will be the absolute limit on the standard motor and tranny... Yeah the MX6 is wrong wheel drive, but if it wasn't it would be popular with drifters and significantly more expensive, and I wouldn't be messing about doing a budget turbo one! Have you seen the prices of '90 RWD stuff like 200SX's recently?? Yikes. Totally agree - if my Ford Probe had been rear wheel drive I'd be asking more for it but then again I wouldn't have picked it up so cheap in the first place.
|
|
|
|
Kieran
East of England
Posts: 148
|
|
Nov 29, 2018 16:17:32 GMT
|
RWD is fun and I've had quite a few RWD cars in the past, but it's not the be-all-and-end-all, I've had fun with FWD hot hatches and the like too. I'd prefer RWD for a track car but for lower powered cars for fast road driving I like FWD as much.
|
|
|
|
Kieran
East of England
Posts: 148
|
|
|
A bit more done this week, I've started nailing things back on. I got the modified front engine mount back on, it had to be cut in places to clear the turbo exhaust downpipes. 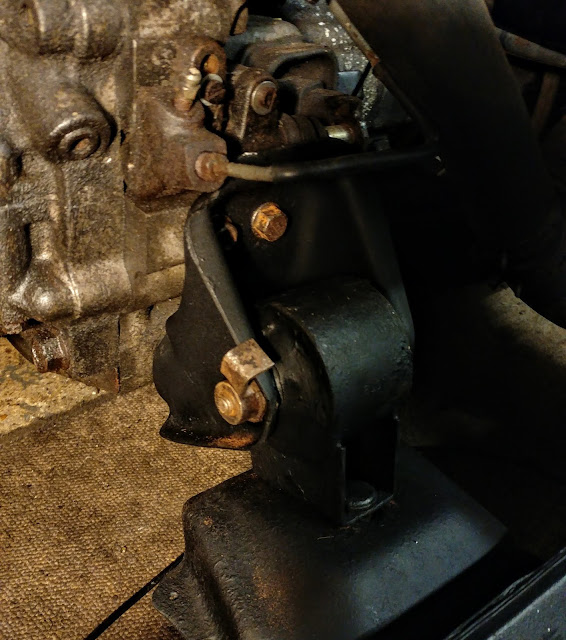 Did a mock-up for intercooler positioning, used a shelf bracket I had laying around. I wanted it mounted close behind the air intake opening in the front bumper, between the fog lights. It's offset to the left somewhat to allow for the couplers and pipe bends to fit. 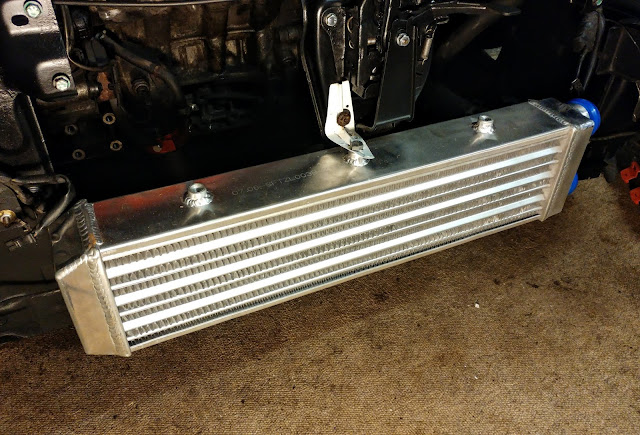 Found a position I was happy with so I decided to fabricate up some brackets, I bought some 30mm wide, 4mm thick steel bar for the purpose. Plenty strong enough, took quite a bit of hammering to form. 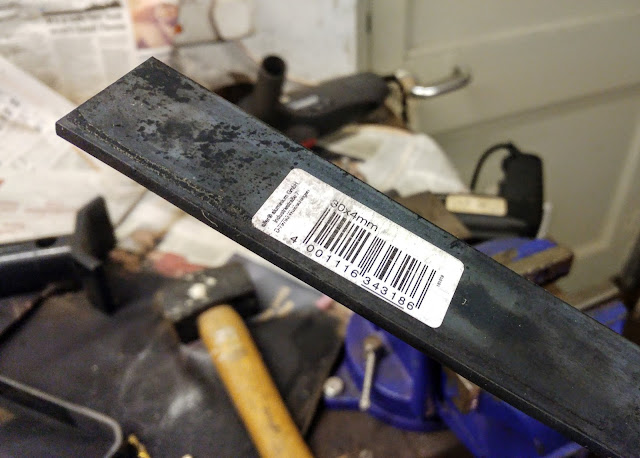 I made three brackets to support the intercooler from the underside and one for the top side. I'm mounting the brackets using M5 threaded holes that are already in the frame, the intercooler has bosses with M8 threaded holes. I need to finish drilling the holes in the brackets and give them a few coats of satin black. 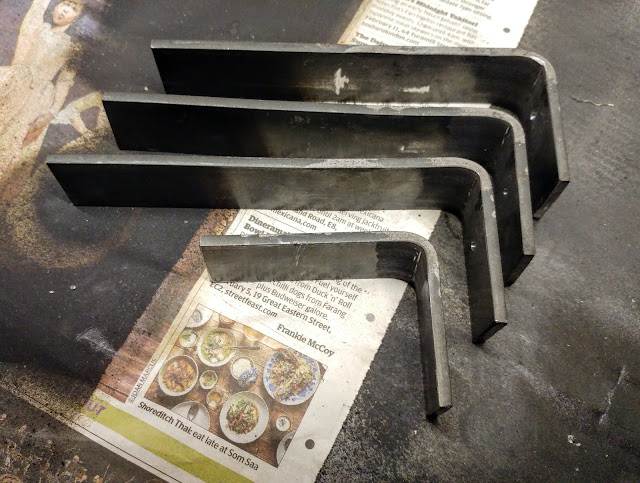
|
|
|
|
Kieran
East of England
Posts: 148
|
|
Dec 11, 2018 13:55:49 GMT
|
The intercooler is securely mounted now so I've started work on properly installing the exhaust and chopping up the charge pipes for installation. 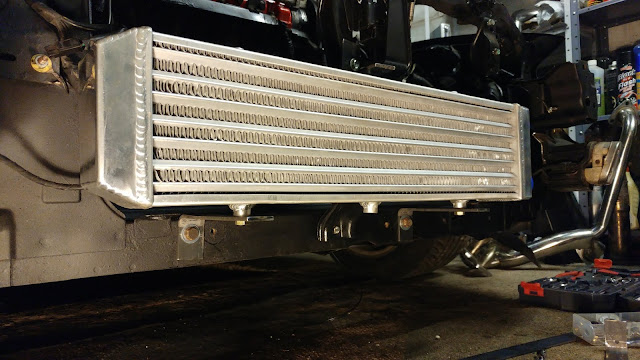
|
|
|
|
|