Enbloc
Part of things

Posts: 399
|
|
|
Well, I can’t put it off any longer. A home was needed for the ECU and also the auxiliary fuse/relay box that I had specified with the pre-made loom. I wanted to put the ECU on the passenger side as there was slightly less junk on that side to contend with but I still had the wiper motor, the backside of the battery box and that bloody Lincoln Zephyr dash centre section to contend with. This only really left two workable areas the glove box and the footwell. The footwell was ruled out as it would put everything on display, I would have to takes chunks out of the carpet and would be generally more prone to be kicked and bashed. So, the glove box it is. Things were made easier mounting the ECU here as there wasn’t any box here anyway. Smoke and mirrors and all that. Using CAD I started to mock up a kinda shelf arrangement that would pick up on the existing glove box door hinge fixings and a third fixing point tucked up behind the dash front. The ECU would sit on the top side and the fuse/relay box would mount on the underside of the shelf. The CAD was transferred to some 2mm aluminium. Cut out the panel had the fold put in with my hokey bench top folder. I thought it would struggle with the 2mm but it worked fine. I purposefully left excess material because it needed a series of whoopdies to weave around and line up to various faces with all the different angles. Any excess was removed at the same time. The original fixings were 10/32” unf. They would now be too short with the extra added layer. Digging through the oddments box found me a bag of these raised countersunk 10/32” screws which proved perfect as they were the right length and I could reuse the old hardware. The panel was drilled and countersunk for the fixings. I needed a way of fixing the two components. Luckily the fixing points for both were completely opposite to each other so nothing clashed but because of each component being mounted in opposite directions meant any sort of captive nut would stick out on the opposite side and look rubbish. In the end I just went with simply tapping the panel for the same raised countersunk screws which were cut down so they were flush when fitted. All mounted ready for a trial fitting. Ahhh, my eyes! Trial fitting successful the protective plastic was removed. This wouldn’t do so it was scuffed and spray bombed. Final fitting. Now you see it… Now you don’t.
|
|
|
|
|
Enbloc
Part of things

Posts: 399
|
|
Jul 11, 2023 20:58:24 GMT
|
When I purchased the Haltech ECU I also got one of their pre-made looms. They have two loom options a basic loom and the deluxe loom that has the auxiliary fuse and relay box. I had the deluxe version as it was always my intention to have all the new engine wiring to be on its own loom and fuse box, leaving the current car loom intact and untouched. In hindsight I would have been better off with the basic loom as I’m only using one relay in the fuse box even that I could have got away without using. I thought about swapping it out but it was there and I wanted to get going with it so just carried on with what I had. Out the box the loom is quite a lump but I knew alot of this would be going in due course. I initially got a bit lost trying to identify and follow what I did and didn’t want to keep. The answer was actually starring me in the face the whole time. Each function had already been bunched and labelled! Off and running now I split off the ones I would need, which are on the left. The ones I didn’t need or I think I didn’t need were pulled back through the loom. With most of the wires making their way back to the main 34 pin plug, any that aren’t needed can simply be de-pinned and pulled back out the loom. If in the future they are needed then can be re-pinned. Using the excellent supplied instructions and wiring diagram the correct pin is located and releasing the lock tab on the plug the pin can be pulled free and the lock tab pushed closed again. What I didn’t account for was the common feeds and grounds were actually piggy backed within the loom which complicated matters a little with removing the unused bundles. The grey/red bundle are 12v feeds, the orange are 5v sensor feeds and the black/white are grounds. The only way forward with this is to cut them. Not something I was happy doing but not the end of the world to reattach if needed. As they say, the first cut is always the hardest and with that out the way there was no stopping me! Things are looking much more manageable now. The rolled up orange wire is a heavy feed wire for a fuel pump, which I don’t need but it’s hard wired into the fuse box and I didn’t fancy cutting it so it sits there now or until I get fed up with it and cut it back! The loom could now be moved to the car. I needed to locate a hole in the firewall for the loom to feed through. Again looking for a position that missed fixed objects and also wanting to keep it tucked up behind the dashboard. Mmm… Taking a 2” holesaw to a freshly painted firewall. Firewall grommet fitted and wires pulled through. Before I started running the new wires I cleaned up the old wires that I wouldn’t be needing. This consisted of the coil wire, rev counter signal wire and a rolled up wire that I’m even sure what it’s for? Maybe an unused warning light? These got fed back through the firewall and rolled up so they can be reinstated in the future if needed. Starting to rough out the wire runs.
|
|
|
|
Enbloc
Part of things

Posts: 399
|
|
|
Before running the new wires I thought I should deal with the old ones first. These are obviously part of the original loom which is still present. Some would need to stay like the sender wire but others could be removed like the coil and rev counter wire. These were pulled back through and coiled up behind the dash for possible future use or reinstatement. Starting off easy, main feed and ground run straight to the battery. I dug out all the various plugs for all the various sensors and injectors. All these plugs take terminals that need the heart shape crimp. As I had so many to do I bought myself some new crimps. I tried them on some bigger terminals I had spare as practice and everything was good. Starting with water sender I crimped the first terminal and completely bongo’d it beyond any usable state. Tried a second one and had the same outcome. 🤬 Came to the conclusion that my new crimps were absolute dog s**t on the smallest crimp jaws. Annoyed and frustrated I tried some multi crimps that were in the electrical box and they actually gave a half decent crimp, so continued with those. I went to clip them into the plug housing and they didn’t want to go. When in doubt consult the instructions. Doh! On this style of plug the wire goes through and the terminal is pulled back into the housing! Second or is it third attempt? Success! My first completed weatherproof plug. Throttle position and air temp completed easily. And the trigger wheel pickup. Injectors next. These would need the single live split to each injector and the individual signal (grounds) wires. I only needed two of the supplied signal wires so the unused ones were pulled through and de-pinned in the name of neatness. You might notice there is actually 4 wires here? The loom covers 2 levels of ECU so actually has 6 injector wires pinned and run in the loom, even though the wiring diagram only shows 4. Completed. There was an ignition live that needed connecting. I remembered that I had just removed the old coil ignition live from the engine bay so this got repurposed already with a change of terminal.
|
|
Last Edit: Jul 19, 2023 1:20:31 GMT by Enbloc
|
|
|
|
Jul 19, 2023 11:32:10 GMT
|
Good stuff so far. What's the plan for covering the loom?
|
|
Proton Jumbuck-deceased :-( 2005 Kia Sorento the parts hauling heap V8 Humber Hawk 1948 Standard12 pickup SOLD 1953 Pop build (wifey's BIVA build).
|
|
Enbloc
Part of things

Posts: 399
|
|
Jul 19, 2023 18:26:25 GMT
|
Good stuff so far. What's the plan for covering the loom? Thanks. Nothing special, just loom tape or wrap.
|
|
|
|
Enbloc
Part of things

Posts: 399
|
|
Jul 21, 2023 22:22:28 GMT
|
Moving onto wiring the 8 individual ignition coils. Each coil has 4 wires going to it, a live, signal (ground) and 2 grounds. This would start to add up fast so I made the decision early on to have the coil wiring on another sub loom. The supplied lengths weren’t going to be enough so I had to order more wire. The pre-made loom used modern-ish high amp, thin wall insulation cable, so I ordered the same. 1mm black for the grounds and 2.5mm red/yellow for the lives. The 3 metres of black I purchased were quickly swallowed up before I’d even managed to complete one side! The lives to the coils would be paired as they made their way back to the main feed. The pairing is different on each bank to try and avoid pairing coils/cylinders that fire consecutively. I don’t know if this is needed but it seemed the right thing to do. I ran the lives and had a real battle trying to crimp and fit the the 2.5mm into the terminals and plugs. After completing one side I realised where’d I’d gone wrong and why it had been such a struggle. The crimp terminals, seals and plugs are only really designed for 1mm wire, so forcing 2.5mm through everything was way overkill for the individual coil runs. I decided to scrap what I’d done but what I had done had used up the supplied terminals and seals and the terminals were also locked into their plugs. I needed to unpin the terminals which meant finding a crappy old screwdriver in the bottom of the toolbox and grinding the end into a pokey tool. Which worked a treat. Another order was placed for yet more wire, all 1mm this time and a packet of replacement terminals and seals. I revisited the grounds I’d run. Having 8 individual grounds on each bank was stupid so I paired these up as well leaving me with a more manageable 4 which I could squeeze into a single ring terminal that is bolted down under one of the inlet manifold bolts. The lives redone in 1mm went much cleaner. A further development of the idea of a separate coil loom was the idea of being able to disconnect it at the firewall. Removing the engine in the future should mean unplugging the sensors and unplugging the coil loom as a whole which would stay with the engine. The main feed is on a single 30amp plug and the signal wires on smaller 16 amp 4 pin plug. With the plugs positioned I could finish running and connecting up the lives. The signal wires had a little more complication to them. As already shown there are only 4 coil drivers but I have 8 coils! The work around to this is a wasted spark system where 2 coils are wired from the 1 driver. Obviously you want one cylinder to be on the compression stroke and the second paired cylinder to be on the exhaust stroke. This is dictated by the firing order of the engine and means each signal wire is running from its source and cross crossing to each cylinder bank. With (hopefully) all the wires taken care of everything was bundled together. And removed…. … for wrapping. Back in place everything else was tidied up to complete.
|
|
Last Edit: Jul 21, 2023 22:28:00 GMT by Enbloc
|
|
|
jamesd1972
Club Retro Rides Member
Posts: 2,921
Club RR Member Number: 40
|
|
Jul 22, 2023 14:36:03 GMT
|
Looks great. When’s the big start up?! James
|
|
|
|
Enbloc
Part of things

Posts: 399
|
|
Jul 23, 2023 21:52:54 GMT
|
Thanks! Looks great. When’s the big start up?! James Soon... Very soon 
|
|
|
|
Enbloc
Part of things

Posts: 399
|
|
|
Remember last year when I stripped the car the complete front clip got dumped on the patio for storage? Well.. Winter turned into spring and spring into summer and it was now in the way being moved around a few times until it ended up the lawn. I wasn’t too fussed as I knew the time was imminent for its re-coupling. The hold up was finishing the wiring in the engine bay as it was a lot more comfortable sitting on the front tyre terminating wires than bent over the front wings. The re-coupling happened rather quickly as it’s a 2 person job and when help comes it’s all go. The only real prep was to grind the tacks off them disastrous shock mount extensions I made and still hadn’t removed and mount the radiator as the front panels partially hang from the rad itself. This was the first time the car had been complete with the new motor set-up and it always comes as a shock how tight everything becomes after working around an open engine bay. With the front clip on I could finally get on with the final section of exhaust from the turbo. It was always my intention to send the exhaust under the firewall and under the car like a conventional system but the mass of stuff that had accumulated in that corner and the 3” exhaust pipe meant that idea was now a no go. Plan B was to now send it out via the inner wing panel. When the front clip was bolted on it was done without the inner panel on that side. Now, I could just run it without the panel which would mean all the water and curse word off the road entering the engine bay but worse is the panel ties a lot of the other panels together and these cars are terrible for stress and fatigue cracks at the best of times so losing so much support was going to be disastrous in the long term. Cutting up my original panel was out of the question. I thought about making a copy of the panel with the necessary clearance but it’s a complicated thing to copy. This left me the only option but to try and source a sacrificial replacement. I’d been down this route before with no luck sourcing one in the past. I tried one more time before having to bite the bullet of shipping one from the US. I got lucky the second time! I also got myself a pile of exhaust bends to get started with. A quick mockup showed the exhaust would end up in the back corner, which suited things nicely. The panel got chopped. I only lost 2 of the least important fixing points. I also remembered to drill the horn mounting holes. Bolted up it still wasn’t enough clearance to be comfortable. Back off I took another cut, the furthest louvre. Which gave a more comfortable space to work with. I could then lay out the first section of exhaust. 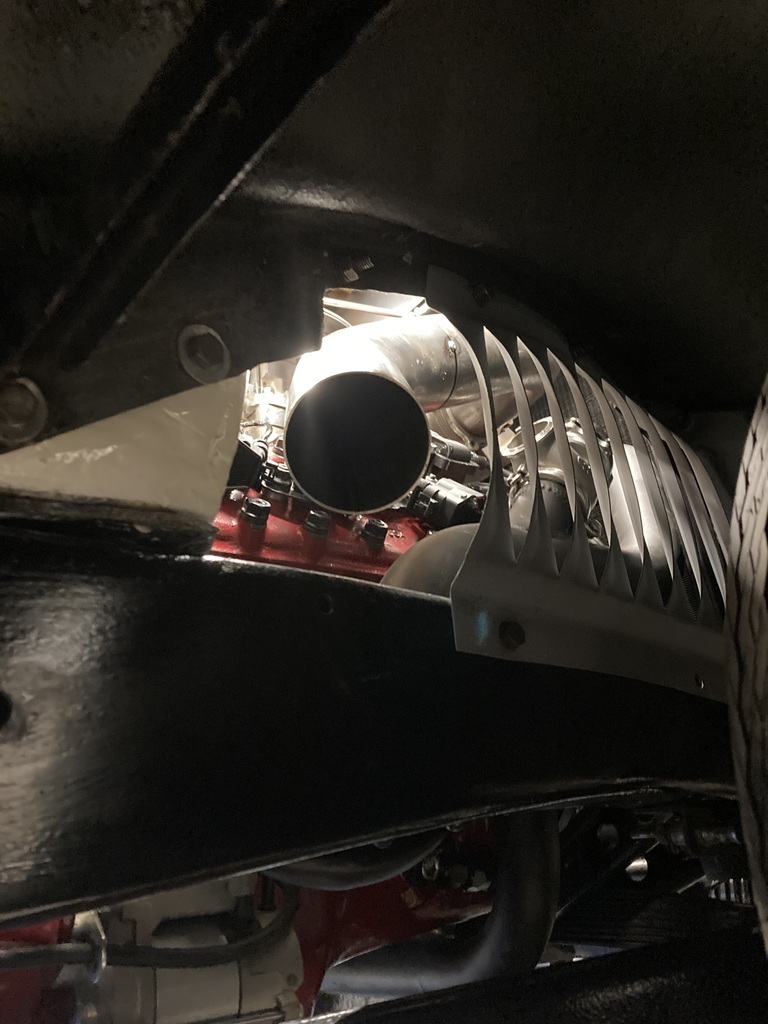 A short, straight section was added to get me beyond the chassis rail and into the arch. I was tempted to pretty much finish it here but the novelty of that would wear off in about 10mins. I didn’t take it much further, managing to squeeze a stubby silencer under the arch. There end the exhaust system!
|
|
Last Edit: Jul 28, 2023 2:47:50 GMT by Enbloc
|
|
|
Enbloc
Part of things

Posts: 399
|
|
|
Doing the initial exhaust down pipe was only really the start. I needed to connect up the wastegate which now sits under the down pipe. When I fitted the wastegate to the feed side it used 2” exhaust tube. Digging out that same tube to make the exit side it didn’t fit the v-band, being too big. I had a quick scan of the instructions and yep, 2” in, 1 3/4” out. Annoying as I had to pick up a length of 1 3/4” just for that short stub. It was a tricky piece to get an idea of what was needed as I was pretty much working blind. After a couple of rough measurements as a starting point I gradually crept up on the fit after many, many mock ups. When I was happy with the fit and final mock up I marked its position. I could then open up the pipe. Mocked up again everything got tacked in position. And the final blending of the transition. Since the front clip had gone on and finalised how much space I had to work with it became very apparent that an air to air intercooler and associated plumbing setup was out of the question. I think an air to water charge cooler is going to be the future route but that is more than I want to be getting involved with at the moment. A theme that’s going to appear more as I race to get everything finished! What has this got to do with the exhaust? Well, not having a means to cool the intake charge means I’ve had to rein in the the potential boost levels. The wastegate came with 2 springs, a 5 lbs and a 10lbs. Using them individually or in combination gives 5, 10, or 15psi boost ratings on the wastegate. My hope was to start with the 10lbs spring and maybe step up to the full 15psi if everything went well. Running just the 5psi is a bit pointless and the 10psi may be too much. GFB have available a 7lbs spring so I went with this for the moment as a happy compromise. While I was messing with the wastegate it was a good time to swap springs. Another add on to the exhaust down pipe was the boss for the lambda sensor. I had the Haltech wide-band lambda add on kit. I kinda shot myself in the foot with this as I needed to mount the control box which I should have incorporated it into the ECU mount when I did that. Luckily, I could still squeeze it in with the cables being plenty long enough. The tray and glove box door were all unbolted again (joy) and the same mounting procedure of drilling and tapping for 10/32 “ UNF screws. There was some deliberation over the actual lambda placement. I wanted it tucked away on the underside but it meant the lambda would be running downhill which is a no, no as condensation can collect and run back into the sensor. It was relocated to the topside and actually got moved again last minute from the when the picture was taken. That completed the down pipe so it got removed again for final welding. And painted in high temp. Fitted back on. Everything still fitted. I needed an exhaust mount to support the weight of the silencer. Handily the end of the silencer lined up where the flanges of the front wing and running board meet. Using the hardware already there a CAD template was made to support a rubber cotton reel. This was copied to 2mm steel with an added support brace. A braced arm was made and welded directly to the silencer. This short length of exhaust and silencer is another rush job. I think eventually it be run all the way to rear of the car as side exit exhausts generally suck and their novelty wears off quite quickly.
|
|
|
|
Enbloc
Part of things

Posts: 399
|
|
|
Addressing the engine breather system I total rethink was needed. Flatheads, like all engines from from the 30’s era, had pretty much non-existent crankcase ventilation systems. The best you got was a hole to atmosphere. The aftermarket comes through in modern times with retrofit PCV setups, which I’ve run on my previous NA builds. How good they work, I’m not so sure? The PCV setups still vent to atmosphere which is an issue when competing in motorsport. This issue I tried address previously with my sealed system. As documented at the beginning of all this all I managed to achieve was to strangle the whole system which blew the inlet gasket out! Anywho… This has all gone out the window now there is a turbo strapped to the motor. First idea was to go back to a stock baffle, breather/fuel pump stand and vented cap. The opening of the stand was looking a little worse for wear. So that got a little tappey tappey tap tap. The baffle tube was given a good clean and dropped in the hole. The stand then got bolted down over the baffle with a fresh gasket. I needed a breather catch can, picking up an OBP one. Finding a mounting spot proved troublesome. An area of firewall was earmarked which meant removing the old fuel block which I’d only really kept for old times sake. I tried the catch can and it was a fail all round. The barbs were in the wrong locations, too small and more than I wanted. I didn’t want the sight tube either. So that went back. I found a cheap Cheap one on EBay that had just two -10 fittings on the front which was what I wanted. When it arrived it looked like this…! You can’t make this stuff up. I still couldn’t get my head around using the factory upstand or an effective means of creating a sealed cap so I dug out the old sealed one that I’d made before that was too restrictive. Problem was, I was now using the drop-in baffle tube so the replacement upstand sat proud on the baffle lip. The factory pair work together because of recess cast into the upstand. To get around this I used some of that thick gasket paper again which fitted perfect. I then got thatshgr high random -10 weld-on fitting that came with the turbo kit welded on as a replacement to the undersized barb’d fitting. From what I’ve been told a turbo’d motor will push out a fair amount of oil via the breather. This would mean any catch can would have to drained via the tap on the bottom periodically. This sounded like a faff so I always had the idea of running a drain from the catch can back into the sump. Luckily, I’d added that extra 1/2 NPT bung to the sump. This is why I was trying to mount the catch can high on the firewall even though it was ugly and messy. I found I could squeeze the new catch can into an area under the master cylinders. Which was a win all round. A couple of aluminium spacers were made to move it directly off the firewall for clearance of the brake pipes. Then went down and dirty with *cough* metric rivnuts. I managed to find two countersunk M6 rivnuts so the spacers would sit flat on the firewall. All fitted up.
|
|
|
|
Enbloc
Part of things

Posts: 399
|
|
Aug 21, 2023 23:05:15 GMT
|
With the breather/catch can located it meant I could now put in another order for fittings and Teflon hose. Not only for the breather lines but also the oil feed line for the turbo, turbo drain back and catch can drain back. Straight away there was a problem! Some idiot had mounted the turbo so close to the top of the manifold that there wasn’t enough clearance to screw a fitting on the drain back outlet. A little thought later it might just fit if the bend was mounted direct to the flange. That was sent off and this is what I got back. It’s bloody close but it all clears. A lucky escape. The Teflon hose goes straight onto the turbo fitting and is permanently fixed, loops around the front corner of the block and down to a 90 degree elbow connected to the threaded bung on passenger side of the sump. The oil feed line was straight forward made in -4 hose. The oil feed is taken from an unused port at the rear of the block that feeds straight from the main oil gallery. I mentioned previous that I didn’t want the faff of potentially having to drain the catch can of oil. Having located the catch can to the drivers side of the engine bay gave me a straight shot to the second threaded bung on the drivers side of the sump so I could create a recirculating breather system. I simply replaced the supplied NPT drain tap in the bottom of the catch can with a NPT to -4 adapter and a line back to the sump. The breather pipe from the up stand was simple enough being a straight run across the engine bay. I didn’t feel that a single -10 was enough breathing capacity so I looked into running a second -10 line. A prime candidate was a threaded boss on the manifold at the front of the valve chest that had a blanking plate over it. But, we’ve been here before… Using the same trick as before I could just squeeze in a second fitting. A standard 90 degree fitting was dismantled. Removing the hex left a nice round stepped lip. The original blanking plate was drilled for the fitting. It hasn’t been drilled curse word, honest! The original cast hole in the manifold is considerably off centre but that did me a big favour as following the position of that original cast hole moved the fitting down and over giving me some much needed clearance. Again that was sent off for welding and returned and fitted up. To finish the plumbing was a vacuum line from the common plenum of the inlet manifold to the MAP sensor built into the ECU. I already had a blanked off 1/4” NPT port drilled and tapped into the plenum portion of the manifold. I eventually found a 90 degree 1/4” NPT to 4mm barb fitting, a weird collection of features I guess. Which then wouldn’t fit as there wasn’t enough space to swing the fitting. 🤦♂️ I wasn’t too sad about this as it wasn’t in the best location. A new hole was drilled and tapped in the carb/throttle body spacer on an alternate face instead for a neater installation.
|
|
|
|
|
|
|
Super-duper work, melding new with old and squeezing 15lbs of stuff into a 5lb bag.
John
|
|
|
|
v8ian
Posted a lot
 
Posts: 3,832
|
|
|
Nice work as usual, but I see a possible issue with the return pipe running so close to the hot side, I would guess its a teflon lined pipe, and very close to heat, they never get on well together, the outer sheath is nylon inner is teflon, with a bit of ss braid in between. I can see that melting, would it be possible to extend the stem away from the heat in steel pipe before going with the braid? or something like thermo-tec heat proofing for spark plug wires?
|
|
Atmo V8 Power . No slicks , No gas + No bits missing . Doing it in style. Austin A35van, very different------- but still doing it in style, going to be a funmoble
|
|
Enbloc
Part of things

Posts: 399
|
|
Aug 22, 2023 10:23:34 GMT
|
Nice work as usual, but I see a possible issue with the return pipe running so close to the hot side, I would guess its a teflon lined pipe, and very close to heat, they never get on well together, the outer sheath is nylon inner is teflon, with a bit of ss braid in between. I can see that melting, would it be possible to extend the stem away from the heat in steel pipe before going with the braid? or something like thermo-tec heat proofing for spark plug wires? Yep, it is all a little too close for comfort heat wise. I’m at a point now of just throwing stuff together for that final push. A steel hardline is definitely the mark II version.
|
|
|
|
v8ian
Posted a lot
 
Posts: 3,832
|
|
Aug 22, 2023 10:52:20 GMT
|
what about having a looksy at PAS fittings, often ridiculously tight steel bends and use JIC fittings,
|
|
Atmo V8 Power . No slicks , No gas + No bits missing . Doing it in style. Austin A35van, very different------- but still doing it in style, going to be a funmoble
|
|
v8ian
Posted a lot
 
Posts: 3,832
|
|
Aug 22, 2023 12:58:19 GMT
|
Thinking again, I know, not good for me, what about make a thick manifold block, be inventive and you could make the pipe come out almost anywhere, or perhaps use a 6mm plate, tap a suitable thread then use a low profile banjo, torques do them,
|
|
Atmo V8 Power . No slicks , No gas + No bits missing . Doing it in style. Austin A35van, very different------- but still doing it in style, going to be a funmoble
|
|
Enbloc
Part of things

Posts: 399
|
|
|
This brung me up to pretty much the last job before attempting to start the engine for the first time, connecting the turbo outlet to the carb hat. I’ve been dreading this job as I knew it would be a nightmare and it didn’t disappoint. I mentioned previous that I had abandoned the idea of fitting an intercooler setup. Firstly I don’t think it was even possible with the space available and secondly I’ve lost patience now and just want the thing running. Running no form of intake cooling is certainly not idea and also quite limiting in how far I can take things. A job for the future that has me now looking at charge cooling (air to water) but that’s a story for another day. This is where I was at with the two components. I roughly worked out a 30 degree angle from turbo outlet to the horizontal, which had me ordering a length of 63mm beaded aluminium tube to match the turbo outlet and a 63mm silicone bend to join the two. To hopefully look something like this. This is when it all started going downhill rather fast. Every surface was a curve or an angle. There was nothing to work from so it just became an educated guess of where to put a hole in the dome…. And I don’t even think that was right. That is where the pictures dry up because… I spent 2 days stomping round the garage making the tube fit worse and worse and even struggling to squeeze it all together on the motor as everything was so close together. It took all my self control to not stamp the hateful thing flat and frisbee it out the door. In the end and out of sheer desperation I passed it on to people better than me who managed to actually salvage something from the steaming turd I’d handed over. I could finally bolt down the base plate for good. This was all that was left of the joiner hose. I had to scallop the hose to get more hose surface area on the hat for the hose clip to grip onto. All fitted up. Notice the rad hoses are now in place as well. These stainless water tubes with rubber joiners are my old setup. I changed over to one piece rubber hoses some time ago but space is so tight over the the top of the turbo that the smaller diameter stainless tubes compared to the thick rubber hose gained clearance and the fact they are metal with water coolant inside means there shouldn’t be any melty issues.
|
|
|
|
Enbloc
Part of things

Posts: 399
|
|
Sept 3, 2023 21:34:53 GMT
|
With the last bits buttoned up there was, in theory, nothing stopping me starting the motor. It was my intention to have the Haltech tech guys walk me through the initial setup but of course it was now Friday afternoon. Impatience got the better of me so I thought I’d just give it a go myself. After reading through many ‘help’ pages, following all the instructions and watching hours of YouTube videos I finally got it to cough to life on what felt like half the cylinders. The following week then became the steepest learning curve I think I’ve ever experienced in my life. Every time I scratched the surface of an area there was another setting to adjust, another parameter to set, another value to input and that was just the software side of it! I kept losing voltage in the battery because of all the cranking leading to this double battery concoction. 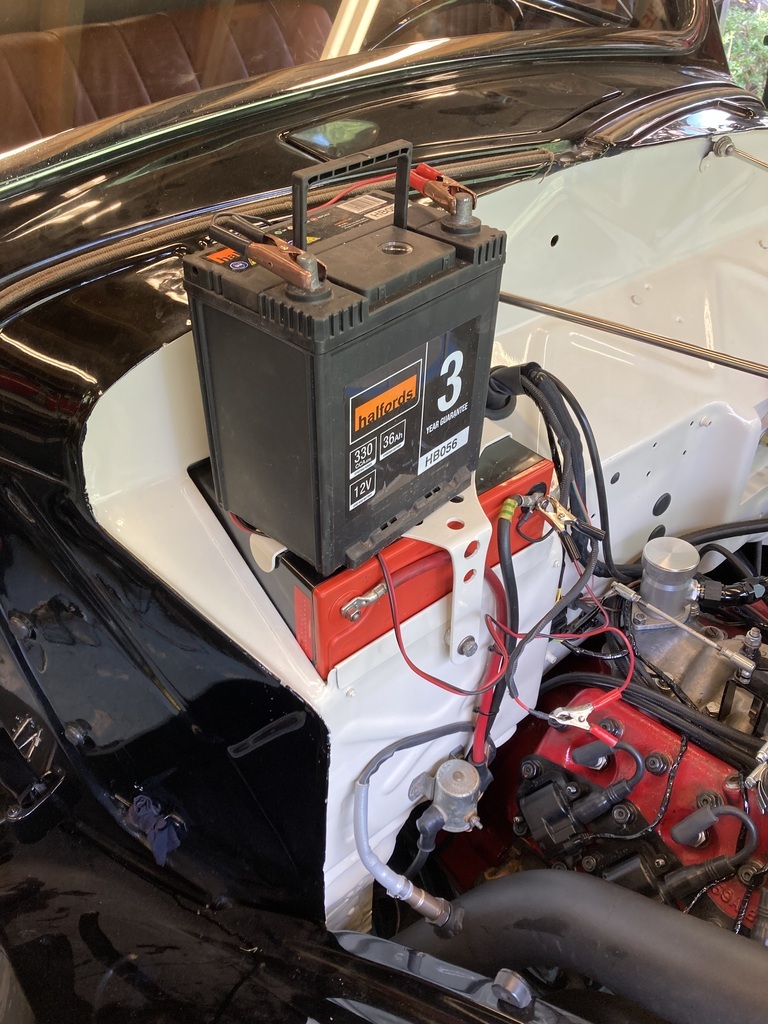 Another issue I chased for days was not having a consistent TDC timing flash from the timing gun. At one point I had 4 different timing lights in my possession! I finally realised my crank sensor air gap was too big as I’d set it up as a Hall effect sensor rather than the reluctance style that it was. This is led to how do you adjust the non-adjustable sensor mount that I'd made? After messing with bending it around and making plastic shims from takeaway cartons I realised I had slotted the mounting holes for adjustment.🫤 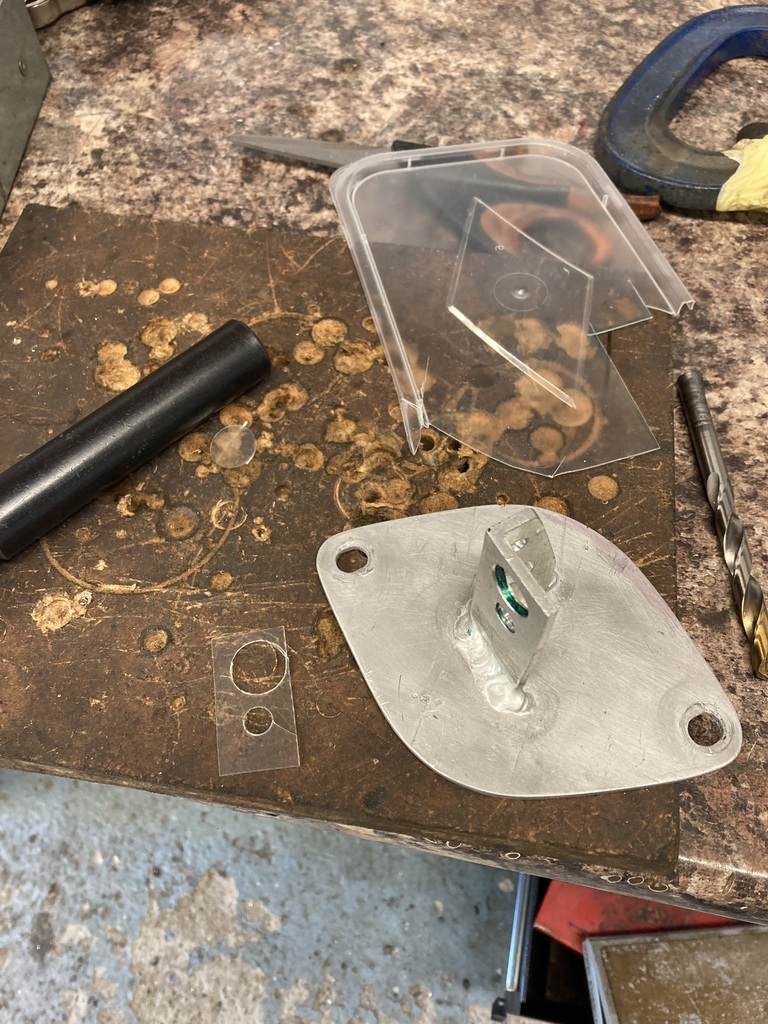 That’s how frazzled my brain was and this pretty much summed things up by the end of the week. 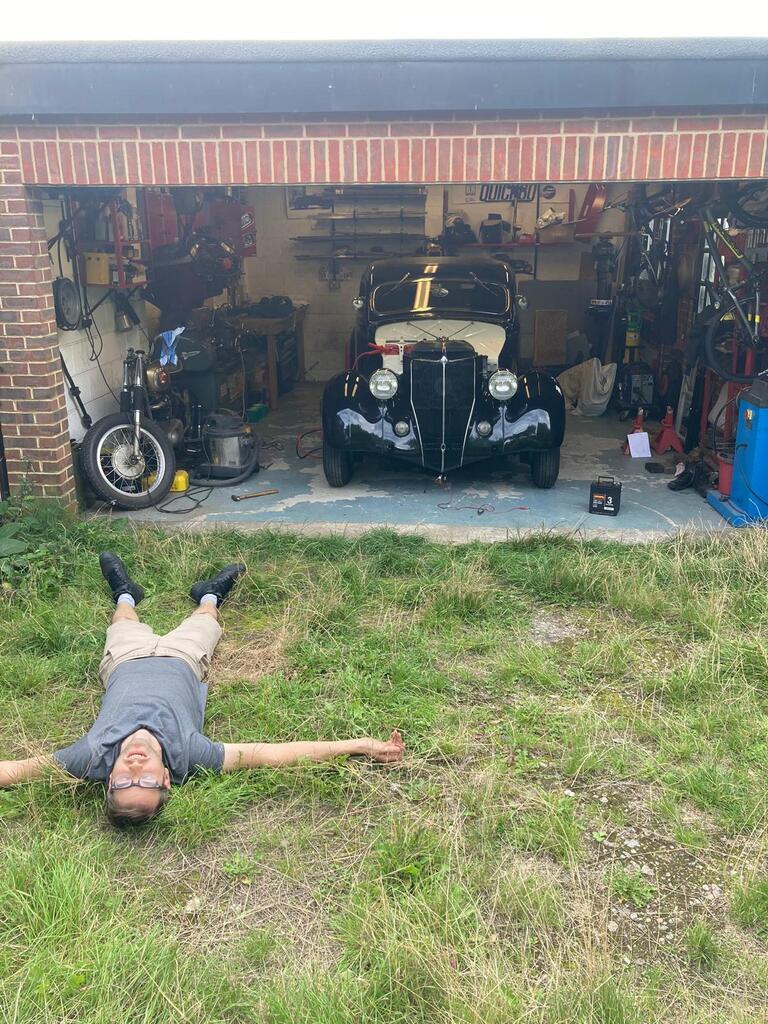 By this time I’d managed to hook up with the Haltech tech… in America, who rang me back on my mobile (whhaat!!😮), remotely logged into my laptop from Kentucky, finished the setup and had it running and idling in 20 minutes! Isn’t technology wonderful, sometimes… So this happened…
|
|
Last Edit: Sept 3, 2023 21:40:45 GMT by Enbloc
|
|
|