|
|
|
"Only a door"....well maybe, but you´re not only getting it to fit properly, but I keep reminding myself that you said they didn´t even do that when new. Not only fix it, but make it better than it´s ever been. Are the doors generally at least the same sort of length side for side? More or less but its not unusual to have 3 - 4 mm difference - does not sound a lot but that 3 - 4 mm can be the difference between having a door that takes paint off the aperture edge when you open / close it - or a door gapping aperture that looks like you could drive a bus through it
|
|
|
|
|
|
|
|
Todays progress included sorting the repair section for the base of the A post I cant weld anything permanent until I have both sides aligned - both doors fitting etc But just about at the stage on this side where I cant progress further until the offside is aligned & the door hung But it would be a good idea to ensure that the door lock / catch & striker plates all correspond at this stage - which is where the diligence in marking / bagging everything up comes into play The combined dovetail striker plate & door keep with the original having seen better days - the club spares team had recently sourced a new batch and I ordered 2 of them at the time knowing that they would be needed on this rebuild The B post had been played around with at some stage with 2 sets of drilled / tapped holes - one of which contained a broken stud A combination of a hard rubber / wood shims had been previously utilised I made a new set up from alloy plate Getting this correct is a critical point has there is no adjustment on either the lock or striker / catch plate (which is why you don't want any sag in the hinges / door when its hung) The doors don't fit tight into the aperture frame either which is factory standard Internal face repair panel for the A post is all but completed - so that's it for the nearside for now 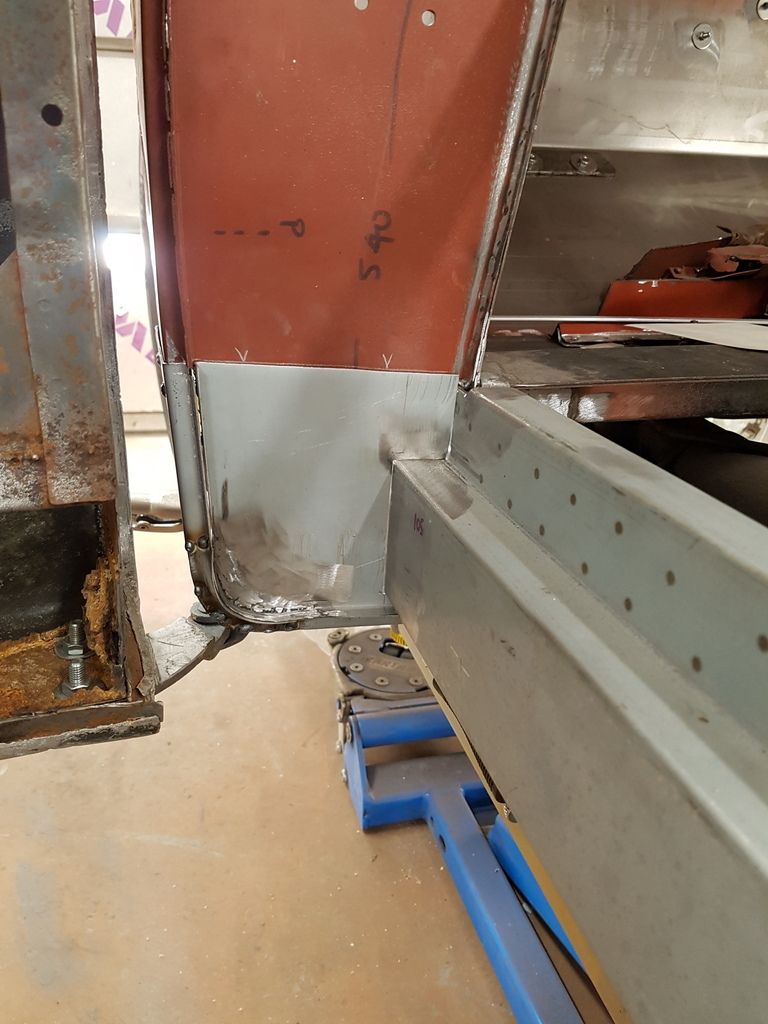 The sill section for the offside could be marked up & trimmed back Then trial fitted Sill panel removed & the rear taper welded up ready for dressing back tomorrow And on that note more tomorrow
|
|
Last Edit: May 4, 2020 19:40:47 GMT by Deleted
|
|
|
|
|
attention to detail!
that striker plate was so mangled, it hardly looked like the new one anymore.
JP
|
|
I know its spelled Norman Luxury Yacht, but its pronounced Throat Wobbler Mangrove!
|
|
|
|
|
Hi grumpynorthener, slight deviation from your excellent and informative thread. I have noticed your lift, I have a BMW E46, and a Daf 33, both of which will require work that involves removing the suspension on them. What make & model is it, and how high will it lift the vehicle?
|
|
|
|
|
|
|
|
Offside then - only this time a quicker version than the nearside - its a near identical process Door rebate had also been messed about with Hence the front section got removed prior to hanging the door to ensure that it did not contact the sill panel Needless to say that the hinge reinforcing web is in a very similar condition to that of the nearside door - i.e. not fit for purpose and will be getting replaced Upper door hinge someone has certainly been here before me - note the elongated holes for moving the hinge well over in order to gain the door fit Door fastened to the top hinge only and loosely fitted to the aperture to allow me to assess what direction I need to head in with the repair panels A few close ups of the challenge Again I made a face & base repair section for the bottom of the A post With the hinge mounted to the door and positioned I could now drill the base of the repair panel to accept the hinge mounting Gapping between the Door & A post - far from perfect but something that I can work upon to gain an acceptable tolerance B post next - its too tight But with a little work & adjustment - its mirroring the nearside So what some considerable hours on the nearside took half a day on the offside Just the door lock & striker plate to fit tomorrow in order to confirm the door fit - then is a matter of taking a lot things apart again in preparation to join / weld the bulkhead to the rear superstructure More tomorrow
|
|
Last Edit: May 5, 2020 19:04:28 GMT by Deleted
|
|
|
|
|
GN, do you think that hinge/mount system was commonplace in that era, or is it unique? It's not so much the lower hinge that makes me ask as to the lower A-pillar design and the sill which make me wonder. Not that I'm encyclopedic in my knowledge, but I've never seen anything like it. Did Jag XK's compare?
That must have been a fascinating and vital era in the car biz; all the innovation accelerated by the war and pent-up demand making it a seller's market.
As always, this is a thread I look forward to reading every day. John
|
|
|
|
|
|
|
GN, do you think that hinge/mount system was commonplace in that era, or is it unique? It's not so much the lower hinge that makes me ask as to the lower A-pillar design and the sill which make me wonder. Not that I'm encyclopedic in my knowledge, but I've never seen anything like it. Did Jag XK's compare? That must have been a fascinating and vital era in the car biz; all the innovation accelerated by the war and pent-up demand making it a seller's market. As always, this is a thread I look forward to reading every day. John John - The Jag Xk's were a little more complex but many cars of the era were still quite agricultural in design - ply timber floors were still being fitted in things like the MGA up into the early 1960's (until the MGB replaced it in 62') and timber frame construction was still being utilised on commonplace vehicles like the Morris Minor Traveller up into the 70's - compare this to some of the ground breaking strides that were being made like the first ABS braking system being fitted to the Jenson Interceptor FF in the late 60's - nothing really surprises me - the era 1945 through to 1960 where the motor industry moved from separate chassis vehicles to unitary constructed bodyshells whilst at the same time ditching the side valve engine in favour of the overhead valve engine has always interested me - to great extent it was one of the milestone turning points of the entire motor industry Thanks for reading / comments - Chris
|
|
|
|
|
|
|
I know it goes against originality, but have you, or anyone, put a metal floor in a car that had a plywood floor? Btw, I see what you mean regarding the lifts cost! One of those on the suggested sites will do, also, they will be better for access in the middle, for clutch change etc.
|
|
|
|
|
|
|
I know it goes against originality, but have you, or anyone, put a metal floor in a car that had a plywood floor? Btw, I see what you mean regarding the lifts cost! One of those on the suggested sites will do, also, they will be better for access in the middle, for clutch change etc. You are not really gaining anything by replacing a ply floor with a metal one - all the ply floor cars that I have worked on are based on a substantial chassis so the requirement to add strength is not required (that is unless your body structure that is sat upon the chassis is that rotten - but you are not resolving the issue by adding a metal floor pan - merely undertaking a cross between patch up & lash up job) - Secondly with the ply floor removed it allows clear access should you ever require it for access to the topside of the chassis without the requirement for removing the entire body of the vehicles chassis
|
|
Last Edit: May 6, 2020 18:49:16 GMT by Deleted
|
|
|
|
|
|
Old door striker / catch plate vs the new one and would you look at the size of that shim that they had in there '6mm'  Still had to shim the new plate up but only to a more acceptable 3mm It needs a decent slam to get the door to catch - but there is a lot movement currently in the B post - once this is welded back to the sill & rear structure of the car the B post shall be a lot more solid and the door easier to close I wanted to secure the radius on the A post repair sections prior to then being removed to allow for the sill to be welded to the bulkhead side return panel - I formed the radius flanges separately and then welded them in I need to mark up all the reference points for the rear structure up prior to its removal - once fully fitted and welded to the sills the rear superstructure is clad with the rear shroud panel Which directly covers most of the steel work Which makes it next to impossible to apply any paint / treatment to structure - hence the structure now needs to come back off the chassis and be primed / painted Access is also required to paint the inner rear wings / splash panels which again with the rear shroud panel fitted would be very difficult to access Along with the battery boxes And the rear support rail for the shroud panel All prior to joining the front half of the body with the rear half via the sill panel More tomorrow
|
|
Last Edit: May 6, 2020 19:10:35 GMT by Deleted
|
|
|
|
|
So time to release the rear superstructure from the chassis Then some prep work to key the back the base primer & the new panels Then suspended the entire superstructure and washed it down with panel wipe Then applied a 2 pack primer The Jupiter was built in a era when little thought was given to prolonging the life of new vehicles - Not just Jowett - all vehicle manufactures - seam sealer & underbody protective coatings were not even thought of Seams were just left open to the elements for water to ingress into and create acres of rust Everywhere Hence for little effort with a little seam sealer All the seams were sealed Once painted and then the underbody protection applied the car should see many decades of future use without issue More tomorrow
|
|
|
|
vitessetony
Club Retro Rides Member
Posts: 1,055
Club RR Member Number: 114
|
|
|
Superb as always 👌
|
|
|
|
samta22
Club Retro Rides Member
Stuck in once more...
Posts: 1,276
Club RR Member Number: 32
|
|
|
What a difference just having it in one colour makes. Looks spot on.
|
|
'37 Austin 7 '56 Austin A35 '58 Austin A35 '65 Triumph Herald 12/50 '69 MGB GT '74 MGB GT V8'73 TA22 Toyota Celica restoration'95 Mercedes SL320 '04 MGTF 135 'Cool Blue' (Mrs' Baby) '05 Land Rover Discovery 3 V8 '67 Abarth 595 (Mrs' runabout) '18 Disco V
|
|
ivangt6
Part of things

Posts: 776
Club RR Member Number: 132
|
|
|
@grumpynorthener Hi Chris. Paint question. What sort of 2k primer have you used? I'm at the stage where I'm applying just aerosol red oxide primer as I do little jobs just to keep the rust off. Am I better off stripping that back, then applying an epoxy primer, then a high build poly or can I key that stuff back then apply an epoxy or go straight for high build. This is mainly for underneath and inside where I'm not too bothered about finish, more durability and rust proofing. The outer panels I am planning on stripping back and starting with an epoxy 2k primer Many thanks Ivan
|
|
1979 Mini 1000 1972 Triumph GT6 2007 VW Golf GTi 1979 VW T25 Leisuredrive 1988 Range Rover Vogue SE
|
|
|
|
|
@grumpynorthener Hi Chris. Paint question. What sort of 2k primer have you used? I'm at the stage where I'm applying just aerosol red oxide primer as I do little jobs just to keep the rust off. Am I better off stripping that back, then applying an epoxy primer, then a high build poly or can I key that stuff back then apply an epoxy or go straight for high build. This is mainly for underneath and inside where I'm not too bothered about finish, more durability and rust proofing. The outer panels I am planning on stripping back and starting with an epoxy 2k primer Many thanks Ivan Ivan - You could just key the red oxide up and apply your epoxy - on the underside I would not bother with a high build and would concentrate more on something that is going to provide you with a good durable / impact resistant finish - Dinitrols 4941 underbody wax is superb for this job & for the cavities Dinitrol ML - on the internal panels just a key up the red oxide before applying your epoxy - no need for it to go back to bare metal (providing it's been applied correctly i.e. to a keyed base that is free from contaminates) Hope that this answers your questions - but if not please don't hesitate to bug me further - Chris
|
|
|
|
|
|
|
It is so good to see this coming together with such care and attention to detail. Impressive as ever!
|
|
|
|
|
|
|
It seems the seam sealer seals seamlessly ..... 
|
|
|
|
|
|
|
It seems the seam sealer seals seamlessly .....  Mark - Finding a good seam sealer is difficult - this one brushes / flows out really nicely - replacing a factory type finish but there are so many rubbish ones on the market that don't apply easily / string a lot and don't adhere very well - I would never consider using the dip your brush in a tin type stuff - its pure rubbish - the good ones are all low modulus & cartridge gun applied
|
|
|
|
|
|
|
Keyed the primer back and gave it all a wash down with panel wipe Then 3 coats of 2K satin black Should do the job - it will all get sprayed with a transparent cavity wax once the car is completed Once cured the superstructure could be reunited with the chassis Use of the vehicle lift under the suspended structure paid dividends in placing the structure back to the chassis in a damage free condition Back on Temporary support frame refitted And the door apertures realigned - I can now start to look at completing the structure by adding the sill sections and completing the structural steelwork More tomorrow
|
|
|
|
|