Thyck
Part of things

Posts: 21
|
|
|
>> So next month we have another trackday booked ...and then all went wrong, but I'll get to that in a sec. In the meanwhile a question for you guys...as you can see, focus is a bit of an issue for us  For us it's easy to keep posting all the different projects (Lola, RX7, Van Diemen, army stuff, etc etc) here, but maybe it'd be a good idea to split it out?? What's the wish from you guys on that?
|
|
|
|
|
jamesd1972
Club Retro Rides Member
Posts: 2,921
Club RR Member Number: 40
Member is Online
|
|
|
Just keep posting ! Its not hard to follow as the projects are all so different. James
|
|
|
|
|
|
|
I’m with James, just keep posting stuff up.
|
|
|
|
|
|
|
Just keep posting ! Its not hard to follow as the projects are all so different. James I’m with James, just keep posting stuff up. +1
|
|
Last Edit: Nov 3, 2019 3:48:09 GMT by georgeb
|
|
|
|
|
I agree, I just spent a very enjoyable Sunday morning reading through this.
Lots of tea was drunk. Please continue as is!
|
|
|
|
|
|
|
Always a gamble buying “running” rotary engines. Generally you can consider yourself fortunate if a motor yields one good housing. That said,the last three I opened yielded none 🤣🤣
|
|
|
|
|
|
|
Always a gamble buying “running” rotary engines. Generally you can consider yourself fortunate if a motor yields one good housing. That said,the last three I opened yielded none 🤣🤣 Do you think that's why Team Boosted on YouTube built a single rotor engine? Simply because that's the number of housings they'd got?
|
|
1968 Cal Look Beetle - 2007cc motor - 14.45@93mph in full street trim 1970-ish Karmann Beetle cabriolet - project soon to be re-started. 1986 Scirocco - big plans, one day!
|
|
Thyck
Part of things

Posts: 21
|
|
Nov 10, 2019 11:40:25 GMT
|
Ok, Roger Wilco, we’ll just dump everything car related in here Right then, so back to the Lola project. What with having the Van Diemen working and down at my place, it was time to rock on…which started with stripping and binning all the hard work done on the front suspension. We just weren’t happy with what we’d produced. Due to the relatively wide front-end (thanks to our DNA and size 13 feet) and the relatively narrow nature of the T492, the wishbones were comically small…produce a picture in your mind of a T-rex’s arms and you’ll get what I mean. The net result of this would be relatively large fluctuations in the front geometry as the front suspension loads / unloads, which could produce some unwanted behaviour. We’re by no means experts in this area, but it just didn’t feel right…and if we’re going to compromise, it’s not going to be here. So this lot was dumped into the ‘box of shame’ (sigh), which is getting a bit full now… 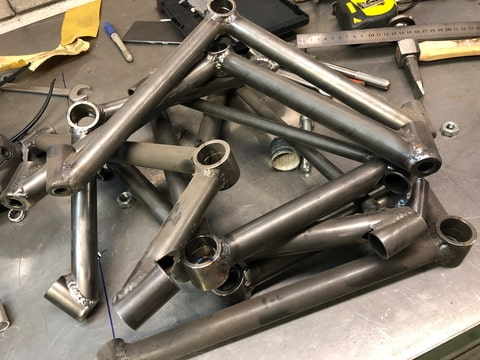 We first got the hubs where we wanted them. This is a case of ‘learning from your mistakes’ as the first entries into the ‘box of shame’ were made by getting our calculations wrong. By mounting the hubs exactly where we wanted them, we were sure to get the rest right…at least, we hoped. 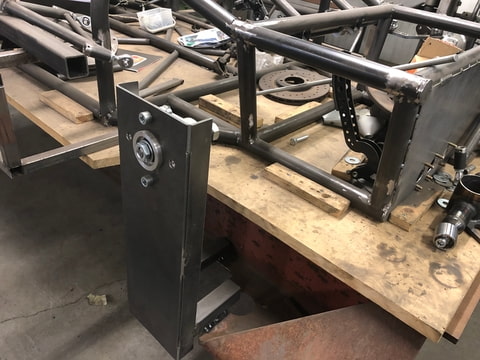 The next part was compromising on a decision we made a long time ago to not have suspension parts within the confines of the main chassis tub. The old ‘Lola limp’ was (in part) caused by wishbones and tie rods punching their way through thin aluminium chassis panels during a crash. We’ve gone for a stronger steel tubular construction (seriously, this thing is built like a tank, maybe we’ve overdone it a bit), but having suspension pickup points within the tub is something we’d still rather not have…however the consequence combined with the relatively wide front-end seems to be that we then end up with the T-Rex wishbones. So we 180 degree turned on that one and decided to just roll with it, we’ll take other measures to ensure we keep our knee caps should anything untoward happen. At this point we’re really starting to see the benefits of 3D CAD (and hindsight!) as you’d come across this during the digital build process, but that’s not something we know much about and we’re more old school types…and have you seen the prices for SolidWorks?! With all that, we shifted the lower pickup points and modified the uprights to suit. This now has to be shorter as the pickup points have effectively moved towards each other in the vertical plane. 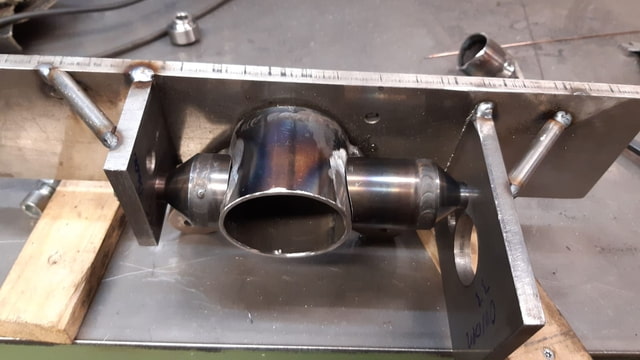 Then it was time foooooor… more wishbones! Thankfully Peter took the strain this time…I mean seriously, this is (I think) the fifth set we’ve made. That possibly says quite a bit about us, but hey, it’s just part of the learning process. 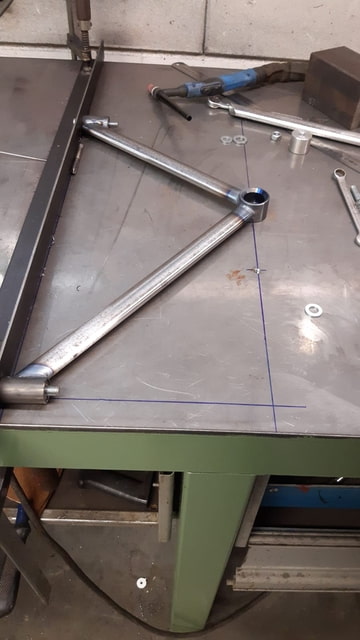 With that and the modified upright in place, we took a look at what to do with the upper mounting points. The front was no issue, but the rear was exactly where the steering arm was, being as the steering rack was already in place. After much ‘umming’ and ‘ahhing’ we decided it had to stay where it was. There just isn’t really any other sensible location that wouldn’t have a detrimental effect on bump steer. For those that don’t know what this is: the steering track rods have a fixed horizontal location on the inside (connection to the steering rack, assuming the steering wheel is not moved) and yet a variable one on the outside (connection to the steering arm) as it follows the arc of the suspension and so moves in and out. This translates to movement of the wheels as the car dives and rolls around turn-in into a corner, ultimately giving unpredictable behavior. You can combat this by specifically positioning the steering rack and steering arm pickup relative to each other…but this, as with everything, results in compromises. So with giving priority to the steering geometry, this meant the upper pickup points had to be elsewhere, resulting in a relatively short upper wishbone. No major problem we’re aware of, but it kinda looks a bit funny. 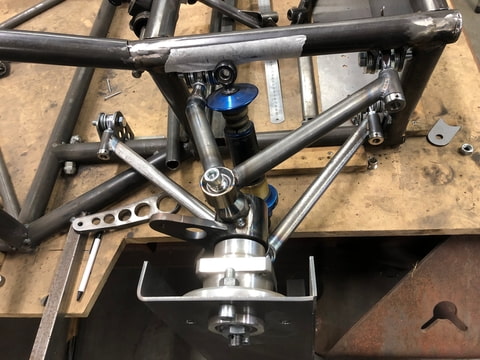 The CNC plasma table (man, I love that thing) was fired up for some new (shorter) steering arms … 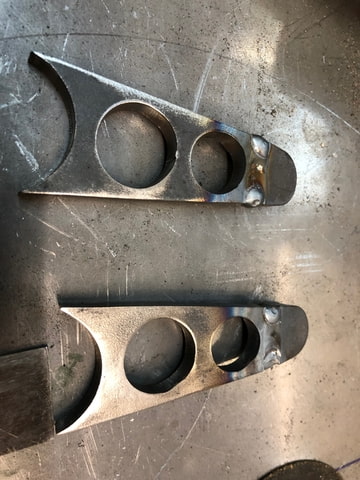 …which were tacked in place onto the modified upright. Then after a couple of pickup points for the shocker, voila! Job’s a good’un and we’re happy (enough) with it. 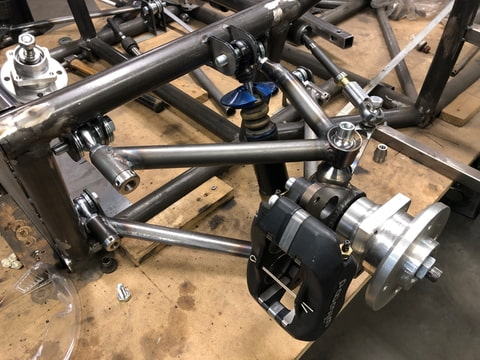 It was well worth checking everything was in the right place, so off with the hub mounts, on with the wheels and bodywork. Hmmmm, looking sweeeet. You really don’t want to know how happy we are to put this bit of the build to bed. 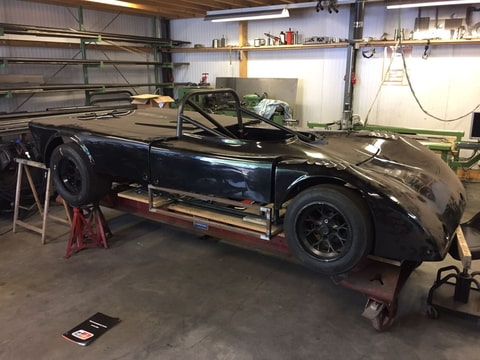 …and then after being very happy about progress made, Murphy came and fudged things up 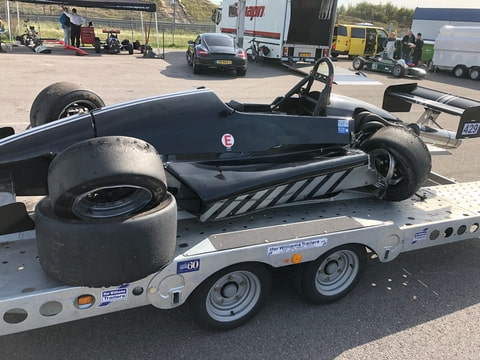
|
|
Last Edit: Nov 10, 2019 11:43:35 GMT by Thyck
|
|
|
|
Nov 10, 2019 20:47:34 GMT
|
Oh dear 
|
|
|
|
|
|
Nov 10, 2019 20:54:28 GMT
|
That needs the tracking doing.
|
|
|
|
|
|
jamesd1972
Club Retro Rides Member
Posts: 2,921
Club RR Member Number: 40
Member is Online
|
|
|
Oops, but if he is ok then it’s just unimportant things like metal and plastic to sort. More learning ! Thanks for the updates good and bad ! James
|
|
|
|
Thyck
Part of things

Posts: 21
|
|
Nov 11, 2019 16:00:43 GMT
|
That needs the tracking doing. You reckon?? I wasn't sure... Oops, but if he is ok then it’s just unimportant things like metal and plastic to sort. More learning ! Thanks for the updates good and bad ! James You're absolutely right, no-one got hurt and that's great, 'cos it was quite a thump. We love building and this way we get to build more Given what we're currently busy with, the Van Diemen will end up that bit nicer, but more about that later this week when I get time to update on that!
|
|
Last Edit: Nov 11, 2019 16:08:08 GMT by Thyck
|
|
|
|
Nov 11, 2019 16:14:11 GMT
|
Well you know the old racers saying, if you don't crash it you are not trying hard enough.
|
|
|
|
Thyck
Part of things

Posts: 21
|
|
Nov 11, 2019 16:35:13 GMT
|
Haha, that's one way of putting it! I had one of these stickers on my previous race car (which was very apt, I can tell you): 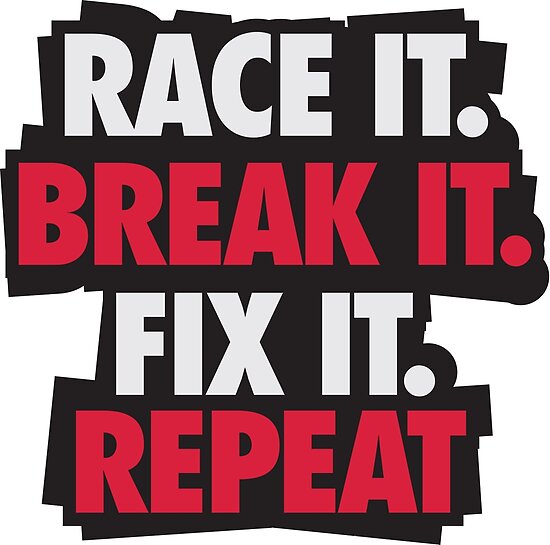
|
|
Last Edit: Nov 11, 2019 16:35:37 GMT by Thyck
|
|
Thyck
Part of things

Posts: 21
|
|
Nov 13, 2019 21:31:08 GMT
|
So what happened? Well, we booked ourselves in for another track day with the HARC (historic race club) towards the end of September. I’d made some improvements since the previous session, particularly being proud of a modern, cutting edge petrol gauge made possible by fabricating a straighter, aluminium filler neck…and grabbing a piece of large dowel with a ‘FULL’ line drawn on it  I’ll have to calibrate that at some point by adding ‘1/4 full’, ‘1/2 full’ and ‘3/4 full’…got to leave some room for improvements somewhere, eh. Simple sometimes just works best…although I can’t take credit for the idea as I copied it off a fellow racer (as the Dutch say: better to properly steal than badly create). The nice, new, shiny (not particularly cheap) rose joint fitted in place of the worn one in the rear suspension gets an honorable mention too. After the success of the last day, we were looking forward to pounding some kilometers around the circuit. It would particularly be my first metres in the new car and I was curious how that would be as I’d not driven a single seater in earnest before. Learning from the last session, we decided to get there the evening before to avoid last minute rush. This wasn’t exactly our first rodeo (we’ve both been racing for some years), but it’s been a while! So we descended upon the circuit and setup camp, with one of our race buddies and his mid 80’s FF2000 Reynard who came and setup next to us. After getting everything in place, enjoying a nice bbq (in the pitch black) and a flipping freezing nights’ sleep in the back of a luton van (we’re going to have to do something about that), we were all ready to go in the morning. Cash was paid to keep the organization happy, all rights were waivered to keep the lawyers happy and scrutineers were convinced of our technical masterpiece so as to keep the insurance company happy…everything ready to go, jobs a good ‘un, Bob’s yer Uncle and we’re ready to ‘go fast’. 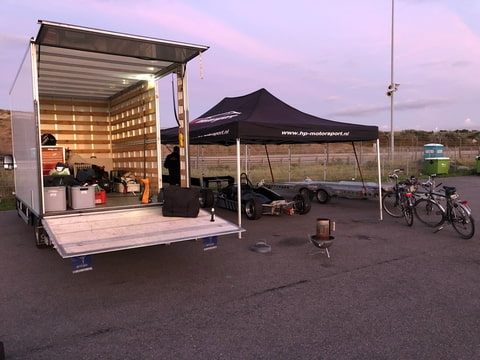 Then picture in your mind a person called ‘Someone’. Well, Someone got to take out the Van Diemen for the first session, so got strapped in (no easy feat in this car, I can tell you), fired her up, trotted off to the pits and then took her out on the first couple of tentative laps. 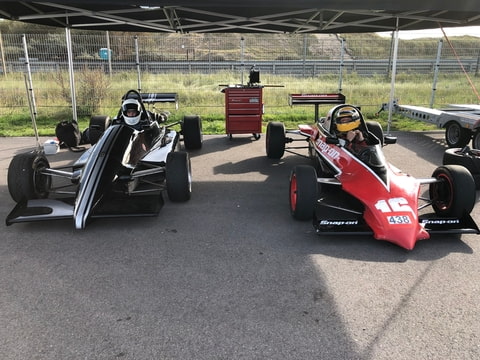 Warming up the engine, tyres and brakes usually takes a little while. Purpose-built race cars like this are not like road cars or ‘normal’ trackday cars. They’re built to operate at a certain temperature and so tend to drive like pigs until everything is where it should be. It understeers too much, doesn’t want to stop properly, you have to hold back with the engine and generally keep an eye on what’s going on more than you would when warmup is complete. So after those first couple of laps, Someone decided it was time to bury the throttle, promptly made it round 9 corners, ran out of track on the 10th, span and then binned it backwards into the armco at racing speed. Someone was pleasantly surprised how ‘smooth’ the journey to ‘Crashville (population: 1)’ had been and was happy to not have any apparent physical issues (which is obviously the most important). After being instructed by the very helpful marshals, Someone was able to relativise the damage, seeing 'only' a left front wheel up in the air indicating damaged suspension, then stood up and looked backwards. Oh. 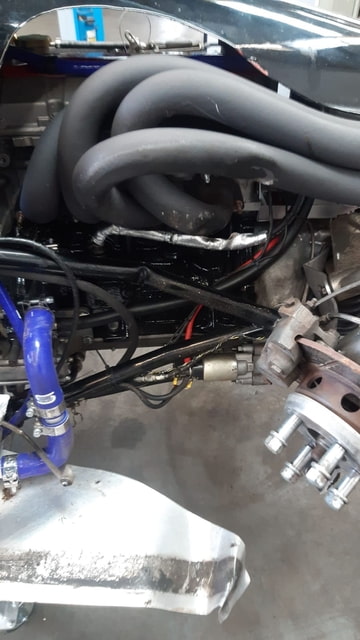 At this point Someone’s mate was standing on top of the paddock area noticing the distinct absence of an angry, black F2000 thundering down the main straight and wondering what was going on. This then turned into concern when the Code 60 (temporary speed limit, a sort of virtual safety car situation) flags were waved…and then light sweating when the red flags (stop the session) came out. Upon consultation with our mate in his Reynard, it was clear all was not well, but Someone was out of the car and safe, albeit giving the thumbs down (duh). Much relief. A very sorry looking Someone got out of the recovery truck and an even sorrier late 80’s Van Diemen was unceremoniously (but, admittedly, carefully) dropped onto the trailer. The time arrived for a good, royal (well deserved) ribbing, a bit of a laugh and much confirmation that it was all part of the game and we’d be back again to fight another day. …and the nice, new shiny (not particularly cheap) rose joint went to rose joint heaven knowing it had given all it could give after a working life of exactly 2.5 laps More to follow about the rebuild and lots of shiny bits! The F2000 will live again…and the Lola will have to be patient… 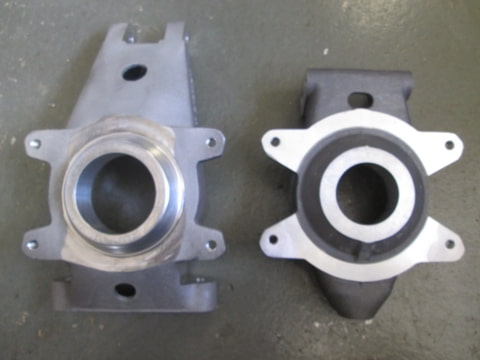
|
|
Last Edit: Nov 13, 2019 21:33:03 GMT by Thyck
|
|
Thyck
Part of things

Posts: 21
|
|
Nov 17, 2019 16:15:57 GMT
|
So the F2000 was dragged back to the workshop and given a good going over. It was clear that the left side was pretty well scrap. Mr Angry Grinder got a good workout as we couldn’t get the nosecone off what with the front suspension being folded up and in the way. 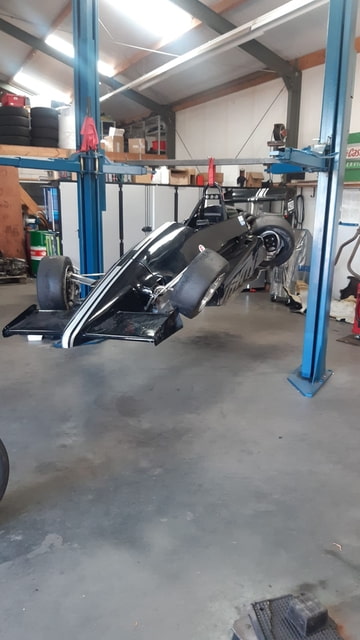 There she is then, stripped down to her undies and looking a bit worse for wear… 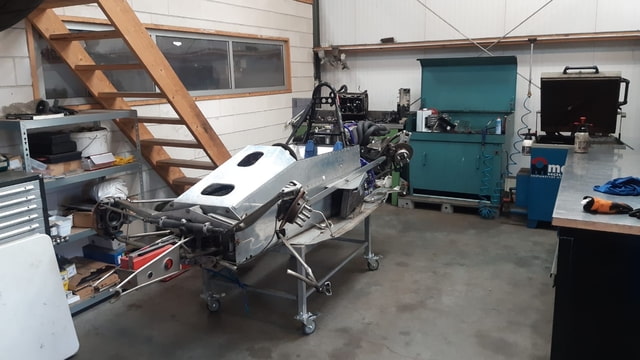 The chassis is straight thankfully… 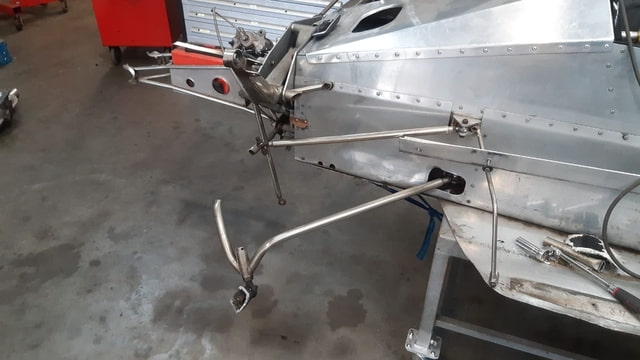 …and the gearbox that supports all the rear suspension is still in one piece… 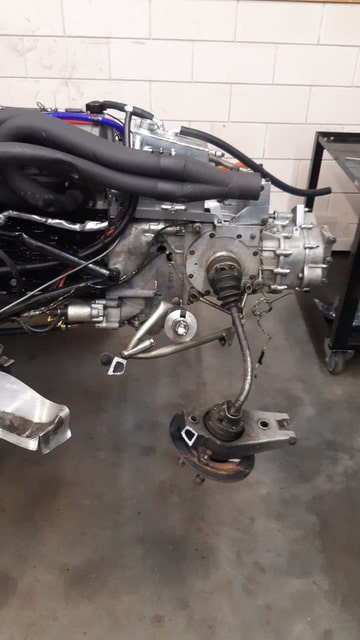 The front suspension mounting plates are bent, though…but rather that than the chassis!  So a day of stripping the ancillaries off ensued…pretty well the only bits that weren’t touched during the rebuild to get her so far! Ah well, at least then the entire car will effectively have been completely rebuilt, knowing me and my need to get everything back to how it should be it was going to happen at some point anyway This all resulted in one big pile of scrap parts…the problem being that you can’t exactly just walk into your local car parts warehouse and order new ones. It was clear we were going have to get into the historic monoposto parts manufacturing business. 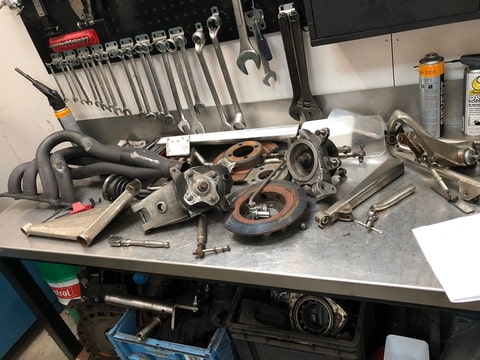 Someone’s box of shame 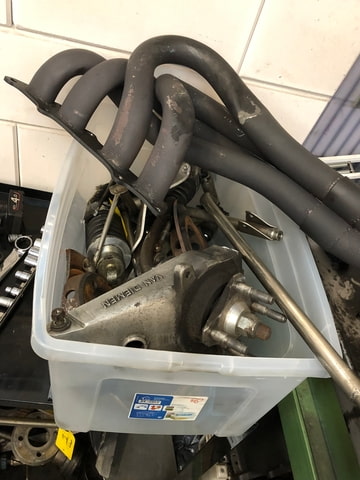 …and here we are left with one sorry looking Van Diemen stripped of most things that make it resemble a race car… 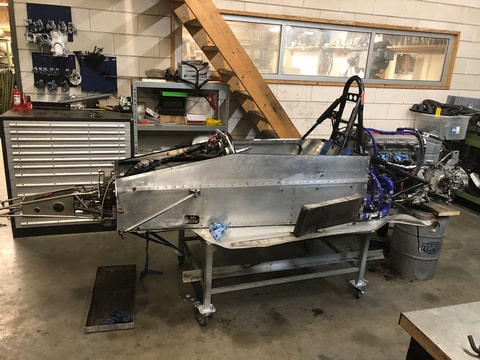 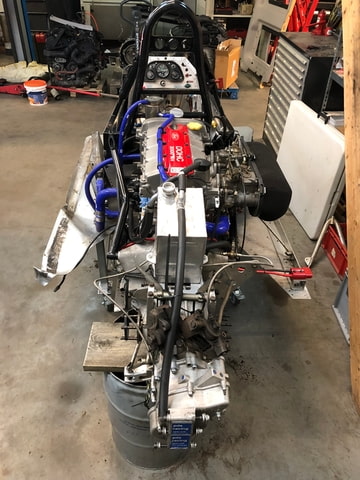 Of course there was one just last bolt that wouldn’t come out. All part and parcel of working with old vehicles, I get it…but just why?!!  There’s a cast ali construction at the front of the car that houses the shockers and the bolt holding the lower shocker mount in place was going nowhere. 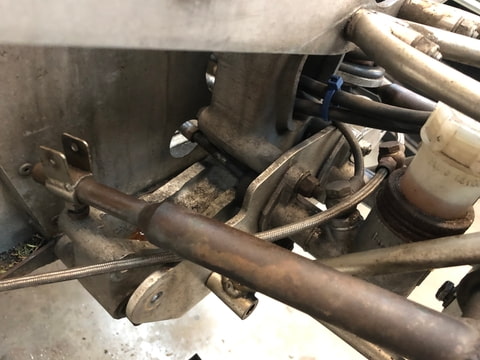 After much coating with penetration oil and even some light heating (meaning: I torched the rubbers on one of the brake master cylinders), it was still going nowhere…grrrrr. Peter suggested I quit before I purposefully torched the whole front-end, so the bolt was left in a bath of penetration oil and I left it for him to fix …which he duly did later in the week, bless ‘I'm! 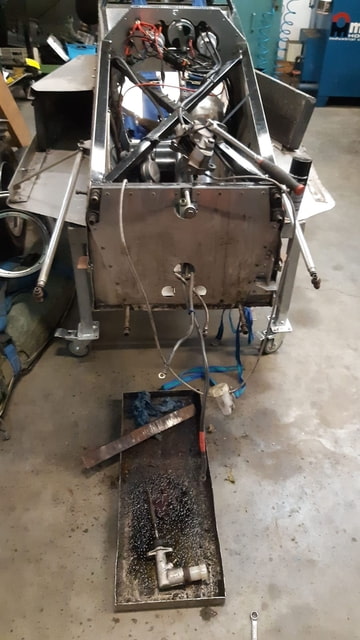 One freed up cast ali suspension housing. I was glad it was still in one piece as these must be like poor quality wobbly children's play pony poo, as I believe they were only fit to a small number of models (F200 / Formula Forward & Formula Vauxhall Junior)… 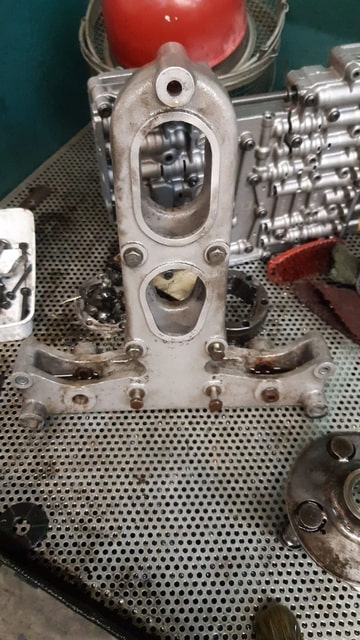 The short and curlies is that the entire left side is scrap, which equates to: 2 wheels & tires, 2 uprights, 2 wishbones, 2 rockers, 1 tie-rod (the front one somehow miraculously survived), numerous rose joints (including the new one), 2 brake discs, 1 shock absorber (the rear one survived thankfully), 3 front suspension brackets, 1 complete drive shaft & joints, 1 engine mount brace, 1 radiator, 1 exhaust manifold, 1 floor tray,...aaaaaand 1 sidepod. Awww, not so bad then!
|
|
Last Edit: Nov 17, 2019 18:17:34 GMT by Thyck
|
|
Thyck
Part of things

Posts: 21
|
|
Nov 17, 2019 16:24:18 GMT
|
…and so the search started for bits. Thankfully there’s a really nice couple of well known guys in the historic racing world (URS – am I allowed to mention them??) who have a whole bunch of stuff in stock and can otherwise source / manufacture about anything you want. So that sorted a number of parts, specifically the most important: two sexy looking aluminium uprights that turn out to be from a 1985 Van Diemen (RF85). 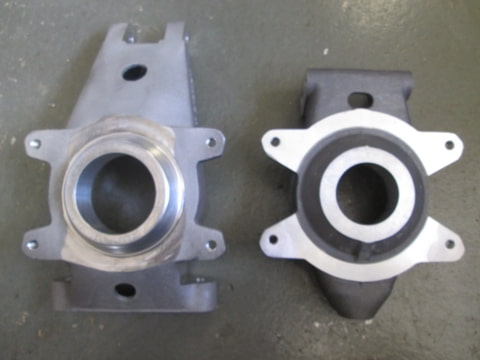 …and would you believe it, they even had not just one, but two of the front cast ali housings, so we took the good one… 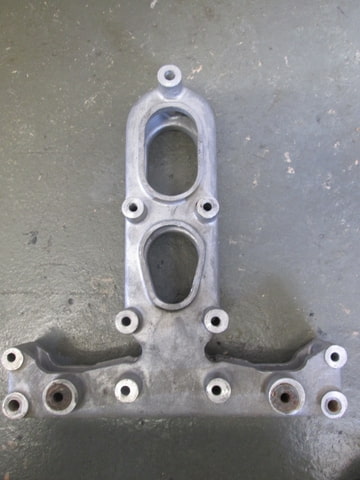 …and next to that, a couple of new radiators… as we may as well change the RHS one at the same time. 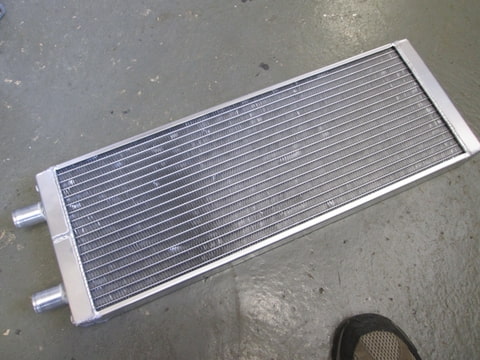 …and there’s a well-known chap that deals in a lot of second hand stuff that drummed up a couple of used driveshafts, shockers, brake discs and a rear ali mount (not broken, but great to have spare). We can't afford to replace everything with new. 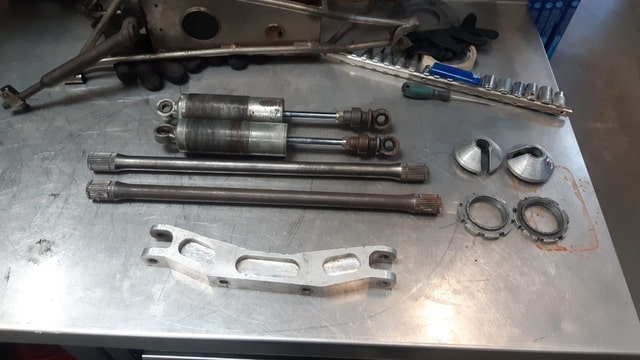 All in all a great result! We’re going to have to make the rest, but that should be quite do-able, albeit time-consuming. ..'cos we didn't have enough to do yet I guess?!
|
|
Last Edit: Nov 17, 2019 17:23:18 GMT by Thyck
|
|
|
|
Nov 17, 2019 16:32:43 GMT
|
Well on the plus-side, we get to share in the rebuild  Glad it’s just bent metal, it obviously did it’s job absorbing the energy even if it’s not very pretty and a lot of work to put right
|
|
|
|
Thyck
Part of things

Posts: 21
|
|
Nov 17, 2019 16:40:06 GMT
|
Well on the plus-side, we get to share in the rebuild  Glad it’s just bent metal, it obviously did it’s job absorbing the energy even if it’s not very pretty and a lot of work to put right Ohhhh absolutely...I'm glad the car did what it was designed to do...and it's also stuff that's easily replaceable, so hey ho we'll just get to work and get it all done. I'm very glad we were able to find the uprights, otherwise I'd be placing an order for a DIY aluminium foundry
|
|
|
|
|