|
|
Dec 30, 2016 10:42:17 GMT
|
Welding. It is something I have always wanted to be able to do.... But if I'm honest I have always been a bit intimidated about giving it a go. It seems to be something that requires a "knowledge", wisdom passed down from one to another.
But I keep reading lots of comments from people who have decided to buy a half decent mig welder and give it a go. Is it really that simple?? Won't I blow myself to bits? I don't expect to be good in a hurry, but how not good is good enough?
The MGB I have just acquired is so bad that it will cost a fortune to do. And I don't for a second mind paying professionals the proper rate to do a proper job. I just figure that it is pretty unlikely I can make it much worse (other than blowing it up - see aforementioned comment).
So is this the right to give it a go? I'm interested to hear other people's experiences....
|
|
Scruffy looking' nerf herder.
|
|
|
Wilk
Part of things

Posts: 528
|
|
Dec 30, 2016 11:02:12 GMT
|
I started by needing to make a hasp and staple lock for a shed. I tried an old stick set but the weld looked like pigeon curse word when done I was then let loose on a mates mig which is much easier to use IMHO Start by practicing on some scrap metal and play with the setting to see what effects they have. Too much power will blow holes in thin stuff so turn it down. You're not gunna electrocute yourself, just make sure you're well covered up and use some ppe to stop spark burns etc Welding thin stuff is more difficult to get right IMHO but is easier if you tack it.... keep spotting one weld onto another. There's plenty of how to videos on YouTube to help out and I find it a lot easier to watch the process than read how to do it HTH
|
|
If it can be fixed with a hammer, then it must be an electrical fault
|
|
edessex
Part of things

Posts: 514
Club RR Member Number: 42
|
|
Dec 30, 2016 11:49:54 GMT
|
I went on an evening course years ago, as I wanted some guidance to start. Then I never touched a welder again until a few weeks back. My welding is terrible now.
Have a quick read up on the tutorials online, and then practice.
Find loads of scrap metal to play with, play with all the knobs and dials, and go from there. Practice makes perfect.
|
|
|
|
ChrisT
Club Retro Rides Member
Posts: 1,670
Club RR Member Number: 225
|
|
Dec 30, 2016 13:13:16 GMT
|
Give it a go, you'll wonder how you managed without once you've got the hang of it. As above, the key is practice, practice, practice and youtube, mig-welding.co.uk etc
|
|
|
|
|
|
Dec 30, 2016 14:00:17 GMT
|
I went on an evening course years ago, as I wanted some guidance to start. Then I never touched a welder again until a few weeks back. My welding is terrible now. sounds like me...although i've never tried since!
|
|
|
|
|
|
Dec 30, 2016 16:03:31 GMT
|
I did arc and gas welding at college many many yrs ago ..... hated gas welding,never got on with arc ...... fast forward a decade or so, i bought myself a gasless mig welder and just played around with it. Fast forward another few yrs and a complete job change,working in the tool and equipment hire game ... used to inspect and test all the gear before it went back out on hire,this included various engine powered arc sets. Got quite good at arc welding then. Still had the gasless mig,but now upgraded to run on Argoshield gas ( benefit of the job ......) still have it to this day,only a 100amp Clarke job,but it works for what i need it for.
( neighbour who is a 'proper' welder borrowed it the other week .... suffice to say i cant blame the welder anymore ......... )
As said above ...... practice practice practice ..... but getting good advice is crucial,i'm self taught and it shows ......
|
|
|
|
Paul Y
Posted a lot
 
Posts: 1,951
|
|
Dec 30, 2016 16:26:48 GMT
|
Like others I learnt as an apprentice how to glue bits of metal together with pigeon poop... My big breakthrough came when I needed to repair our garden tractor and a Snap on Mig popped up for sale on R & S 10 minutes from home for £100 including a full bottle of gas. I would class myself as a competent welder right up until I turn into a rank amateur... The biggest tip I can give you is don't make your first weld of the day on the item you actually want to weld... Also, your welds will not look like the ones on YouTube, weld porn and the like... The 2 bits of advice I have been given when welding are the following:- If you can't weld well, weld lots. There are only 2 things in the World where penetration is important, welding is one of them... And finally, I have actually found that i have more problems occur when I try and grind back, or dress, the welds! Practice lots, but rather than just on a bit of scrap try and make something, it teaches you how to approach the practical side of welding - helped me tremendously. What ever, enjoy! I do. P 
|
|
|
|
|
|
Dec 30, 2016 17:23:50 GMT
|
Like others I learnt as an apprentice how to glue bits of metal together with pigeon poop... The biggest tip I can give you is don't make your first weld of the day on the item you actually want to weld... yes i should have thought of that ...The 2 bits of advice I have been given when welding are the following:- If you can't weld well, weld lots. works for me!And finally, I have actually found that i have more problems occur when I try and grind back, or dress, the welds! mine need it!Practice lots, but rather than just on a bit of scrap try and make something, it teaches you how to approach the practical side of welding - helped me tremendously. What ever, enjoy! I do. P  You can tell the difference from my first effort,to my last weld of the day .... By the time i had got to this point,i was tired cold,(very cold) and my back was hurting,i should have called it a day earlier on,and stopped. And if i had, i would have realised the welders earth plug had loosened and was only just making contact. Rather than just persist and think 'it'll get better' .... just made a whole load more work for myself!
|
|
|
|
|
|
Dec 30, 2016 17:29:38 GMT
|
Resist the urge to buy a cheap / curse word welder as the difference between a poor set and a good set is night and day and makes learning to weld much harder. have a go with someone elses before paying money if you can. Stick welding is actually quite easy with modern inverter welders but still not great for thin stuff like bodywork, so best bet is still a mig welder. You want one with low minimum amps so make sure it does 30a or less as a minimum for the thin stuff. As with anything you will need to do some practice before doing any real work with it and get an understanding of what is going on and what it sounds like when running nice and when it's not happy, so yes, practice. If you are sensible and safety conscious then there's no need to avoid it. have a read on www.mig-welding.co.uk/ for guides and the forum for any help and suggestions.
|
|
Last Edit: Dec 30, 2016 17:37:56 GMT by sausage
|
|
skozra
Part of things

Posts: 175
|
|
Dec 30, 2016 18:18:35 GMT
|
I was in the situation where the guy who had been doing the welding on my Capri had basically given up on it after doing great work and making good initial progress. He just had no time, so after a year of it just sitting in his yard gathering dust and grot, I paid him for the work he'd done, took the car back and finished it off myself. I'd been practicing welding by making a couple of propane cylinder woodburning stoves with my newly acquired clarke mig welder. That was about the extent of my welding before tackling the car, but I just got stuck in, took my time and it paid off in the end.
It took me a couple of months to finish it to a standard I was happy with, but the end result is an mot'd car that I can drive - over six years after buying it.
The uk mig welding site mentioned above is a godsend, plus there are some awesome mig welding videos on youtube. All of these helped me no end. As has been said already though, practice practice practice.
So yeh, give it a go. I used a Clarke 151en with lincoln welding wire and argon/co2 gas (in a large rental cylinder)
|
|
93 Volvo 240 Torslanda Estate, 01 Subaru Impreza WRX Saloon & 86 Ford Capri 2.8i (with Weber 38 carb fitted)
|
|
|
Wilk
Part of things

Posts: 528
|
|
Dec 30, 2016 18:51:56 GMT
|
I was always told that if you're running a decent weld of any length then it should sound like bacon frying.... a nice sizzling sound 👍
|
|
If it can be fixed with a hammer, then it must be an electrical fault
|
|
Paul Y
Posted a lot
 
Posts: 1,951
|
|
Dec 30, 2016 20:10:37 GMT
|
Oh yes, and another thing that was the sort of epiphany... Sound. People talk a lot about the 'sizzling bacon' sound when you get the amperage and wire feed right. I always thought it was one of the things the pro's talk about because they like the sound of their own voices. How wrong was I! When you get it right, puddle, wire feed, hand movement, surface clean etc it really does 'crackle' like frying bacon. It really is very satisfying. Let us know how you get on. P. 
|
|
|
|
|
|
Dec 30, 2016 21:36:09 GMT
|
Thank you all!
Definitely going to go for it. Am going to take the doors and curse word wings off the mg, cut them up and practice for at least a couple of months. Then I am going to Sir back, have a look and decide whether or not I am ready to try something on the car. I don't have to complete the mg in any particular time frame, so if I am not ready I'm not ready.
Thank you all for taking the time to give me your thoughts and tips!
|
|
Scruffy looking' nerf herder.
|
|
|
|
Dec 30, 2016 21:44:55 GMT
|
Played with oxy-acetylene a bit in sixth form workshop tech class almost 35 years ago and though I'd got reasonably good at brazing stuff. Had a go with a mig and a plasma cutter once at a demonstration night also in the '80s and been promising myself a mig ever since. Still hasn't happened. Will have to make sure my youngest boy learns to weld properly at school then get some gear so we can do projects together. He's keen to build a car but he's only 11 so plenty time yet.
|
|
|
|
|
|
Dec 30, 2016 21:48:52 GMT
|
The short answer, as many have already said, is to do as you are doing and have a go. You my surprise yourself. Or you may be like a neighbour of ours in the '70s who bought an arc welder with no training at all and took all of the first day to join two pipes together. He became pretty competent with practice though. A lot of the steel farm gates he made are still in service.
|
|
|
|
tofufi
South West
Posts: 1,463
|
|
Dec 30, 2016 21:57:06 GMT
|
I got started after buying a 40 year old car as my first car, and it promptly failing the MOT on 'At least a grands worth of welding'. Took the car home, and got a couple of friends to show me how to weld  Take the advice above, buy a reasonable MIG welder with gas (I wouldn't bother with gasless) and practice on scrap until you're comfortable with it. An auto darkening helmet/mask will help no end, too 
|
|
|
|
awoo
Posted a lot
 
Posts: 1,507
|
|
Dec 31, 2016 13:50:56 GMT
|
having someone show you what to do and practice make all the difference.
theres quite a lot to balance, so to speak. torch angle, amps, distance from the work piece, thickness of the metal, finishing and spacing of the bits you're welding together, etc.
it can be perfect when everything is right but super frustrating when not.
welding tips and tricks on youtube is a goldmine for info
also buy the best quality welder you can afford, the cheap gear is a false economy
|
|
|
|
|
|
Dec 31, 2016 17:25:43 GMT
|
Pulled the pin and bought an entry level draper to start to learn with. When I am ready to move on to the car I'll invest in a decent setup.
Thanks again for all of your responses. As ever, a very inspiring place!
|
|
Last Edit: Dec 31, 2016 17:27:07 GMT by ellwood
Scruffy looking' nerf herder.
|
|
alecf
Part of things

Posts: 424
|
|
|
Sorry if what I type has been said already as I've not read through the lot. I would suggest starting mig with the thickest metal you have and practice with the settings and making sure the gas regulator is set right. Then work your way down on the metal size. The thicker the metal the easier to gauge if you are doing it right. As too much heat it blows holes too little hear it will not penetrate and will break off.
I was lucky enough after years of being alright at it to meet a fella who's now become good mates of mine and he's a fabricator by trade so spends hour and hours a day mig tig alloy stainless etc and I've learnt tons from him. Setting the welder up correctly is half the battle
|
|
|
|
Wilk
Part of things

Posts: 528
|
|
|
To help there's a really good phone app that gives you settings for different weld types 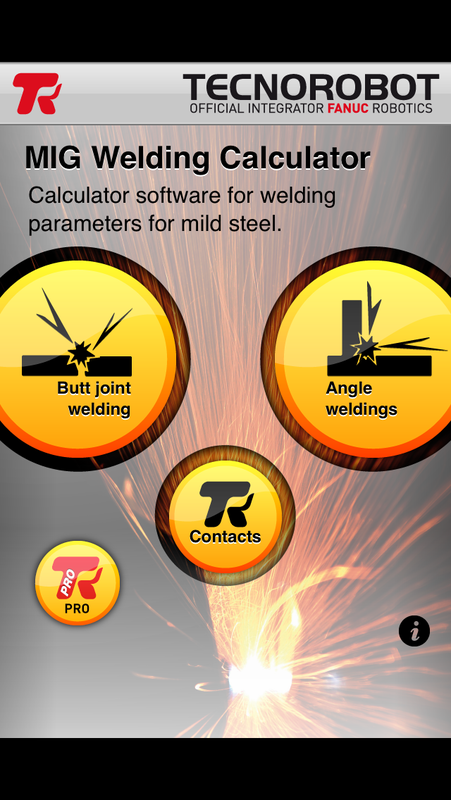
|
|
If it can be fixed with a hammer, then it must be an electrical fault
|
|
|