|
|
|
Apologies for the limited description in the last few posts, I didn't take many pics and was too knackered to describe the action in much detail!
Just flipped to the first page and it turns out we've been beavering away on the track car for a year now! To be fair, progress was slow at first, it's picked up a bit in the last 6 months.
Remaining jobs, in no real order:
Rebuild one of the calipers and bleed the brakes.
Change the clutch.
Change the cambelt and waterpump.
Change oil seals
Design and build an exhaust system.
Change all fluids.
Fit bonnet vent to funnel air at the oddly placed filter.
Finish the body prep.
Paint.
Fit battery cut-off switch.
Fit bonnet and boot securing latches.
Fit tow hooks.
Drive to Oulton Park.
Rag it around the track.
|
|
|
|
|
|
|
May 18, 2016 14:46:47 GMT
|
Nice work. A modern Elan :-)
Bookmarked.
Slight concern re the cage. There appears to be no triangulation, apart from the slight angle of the rear braces. Are you sure that this is sufficient in the event of a roll over? It doesn't look enough to me and I don't think it would pass a proper scrutineering session as it doesn't comply with the blue book. Not a problem if not racing but I am concerned that it would collapse in the event of a roll over which wouldn't be good.
I am sure there are better informed guys on here that can put me right if I am incorrect :-)
|
|
Last Edit: May 18, 2016 14:47:01 GMT by nalesutol
|
|
|
|
May 18, 2016 20:31:16 GMT
|
Have a look on the TR Lane website,their roll bars seem to be a similar design without further bracing. I personally would stick some triangulation in to strengthen the feet.
|
|
1965 Morris Minor 1000 soon to be 1380 1997 MK1 MX-5 1.8 (sold) 2009 MK3 MX-5 2.0 (sold) 2008 Mini Cooper (sold) 2003 Mini Cooper S (sold) Fixed wheel Raleigh Clubman (sold) 1982 Yamaha RS125DX (sold)
|
|
|
|
May 18, 2016 21:11:29 GMT
|
Hmmm, they must know what they are doing.......however, The first one has no angled brace and the other two have the brace too high on the lower ends (not at the hoop mounting point), so a sideways force will bend the bar at this point. The last photo shows how the brace should be located, IMO. Please advise me what is wrong with my take on this, I must be missing something in their cage designs.
|
|
Last Edit: May 18, 2016 21:18:13 GMT by nalesutol
|
|
meltedcheese
Part of things

Please, Don't Sqeeze the Volvo!
Posts: 403
|
|
May 18, 2016 21:13:55 GMT
|
Nice work. A modern Elan :-) Bookmarked. Slight concern re the cage. There appears to be no triangulation, apart from the slight angle of the rear braces. Are you sure that this is sufficient in the event of a roll over? It doesn't look enough to me and I don't think it would pass a proper scrutineering session as it doesn't comply with the blue book. Not a problem if not racing but I am concerned that it would collapse in the event of a roll over which wouldn't be good. I am sure there are better informed guys on here that can put me right if I am incorrect :-) Thanks for the comments and concern nalesutol, The car is going to be an MOT'd and used on the road as well as for track days, as much as we would like the car to comply with the blue book the soft top makes this impossible, the FIA compliant MX5's run without the soft top to meet regulation. The design used I have seen before, now that you have cast a bit of doubt I think I'll run it through a stress analysis in work just to see what the frame is capable of. A bit of torsional stiffness wouldn't hurt but I would have thought the current design should do the job for the moment, we do have plans to extend the cage, that would be a good time to add some secondary stiffeners to the frame perhaps.
|
|
|
|
|
|
May 18, 2016 21:28:02 GMT
|
Just had a closer look and realise that the hoop bolts to the car's structure just below the bends (not down to the floor as I thought). With the short section of straight tube below the bends second thoughts make me think that this design isn't so bad after all :-)
My concern was not MSA approval, rather your head's well being :-) No point in adding weight if it doesn't do anything.
Mind you, a 45mm (or even 38mm) diagonal still wouldn't go amiss, although it would restrict rearward visibility somewhat but rather fit it now than regret it from a hospital bed. I will be very interested in seeing the stress analyse results.
Not knowing anything about MX5's structure, I assume that the cage mounting points are up to the job. Are any strengthening plates added to the mounting areas?
Photos aren't that clear on the mounting brackets, is the main hoop bolted on using only one bolt each side?
|
|
Last Edit: May 18, 2016 21:34:43 GMT by nalesutol
|
|
meltedcheese
Part of things

Please, Don't Sqeeze the Volvo!
Posts: 403
|
|
May 18, 2016 22:14:38 GMT
|
Just had a closer look and realise that the hoop bolts to the car's structure just below the bends (not down to the floor as I thought). With the short section of straight tube below the bends second thoughts make me think that this design isn't so bad after all :-) My concern was not MSA approval, rather your head's well being :-) No point in adding weight if it doesn't do anything. Mind you, a 45mm (or even 38mm) diagonal still wouldn't go amiss, although it would restrict rearward visibility somewhat but rather fit it now than regret it from a hospital bed. I will be very interested in seeing the stress analyse results. Not knowing anything about MX5's structure, I assume that the cage mounting points are up to the job. Are any strengthening plates added to the mounting areas? Photos aren't that clear on the mounting brackets, is the main hoop bolted on using only one bolt each side? Bloody hell your all over this  Figured using the MSA would be good enough guidance to keep the old noggin safe as it does give some pretty decent tube arrangements and ergonomic clearance data. Would probably keep with the 45mm x 2.6mm tube for the main contours and hoop and 38 x 2.6 tube for diagonals and anything else. We do have cheek plates for the main hoop but haven't fitted them yet (time has been tough with the amount of fab work we have taken on ourselves), addition plate will be added from under the car. I'll post some analysis images hopefully tomorrow after lunch. Thanks for the concern and interest 
|
|
|
|
|
|
May 18, 2016 22:48:37 GMT
|
:-) A dog with a bone, me. It is a subject I actually know a little bit about, but always willing to learn more. I have seen a lot of cages that only add weight rather than safety.
My initial concerns were based on the hoop reaching the floor as there would have been very little resistance to sideways movement. It is a lot stronger than I first thought, should have looked a little closer :-)
I would still like to see the stress analysis results.
|
|
Last Edit: May 18, 2016 22:51:34 GMT by nalesutol
|
|
meltedcheese
Part of things

Please, Don't Sqeeze the Volvo!
Posts: 403
|
|
May 19, 2016 12:19:45 GMT
|
:-) A dog with a bone, me. It is a subject I actually know a little bit about, but always willing to learn more. I have seen a lot of cages that only add weight rather than safety. My initial concerns were based on the hoop reaching the floor as there would have been very little resistance to sideways movement. It is a lot stronger than I first thought, should have looked a little closer :-) I would still like to see the stress analysis results. Haha nothing wrong with asking why! Run some FEA on the cage today based on the material spec being to CDS - BS EN 10305-1 : 2010 E235+C, I didn't go overboard on this as I did it in my lunch hour, yield is 384N/m tensile is 480N/m. Basically run a uniform load on the hoop cross bar, then did the same with the addition of a diagonal, results are interesting yet fairly predictable. On the second test similar format however loaded up the hoop bend to give a bit of lateral instability. Failure results are indicated at the top of each image, as I say time is tight so couldn't spend much time on it. Bar without diagonal, 30 degree downward loading (car overturned sliding forward??) exceeds material yield @ 2.6T 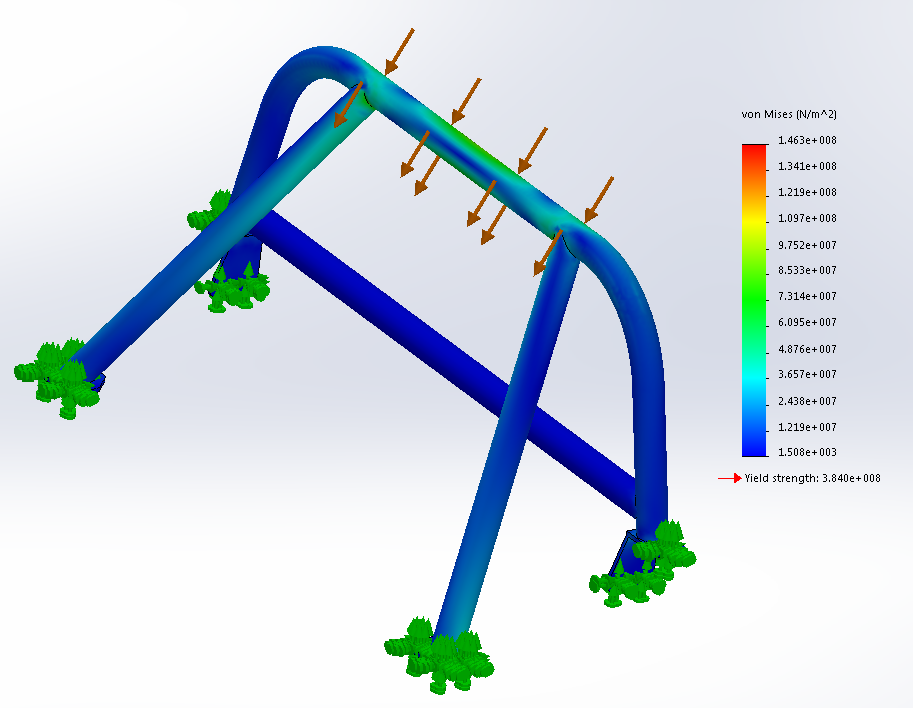 Bar with diagonal, 30 degree downward loading (car overturned sliding forward??) exceeds material yield @ 2.7T (resulting in 3.7% difference) 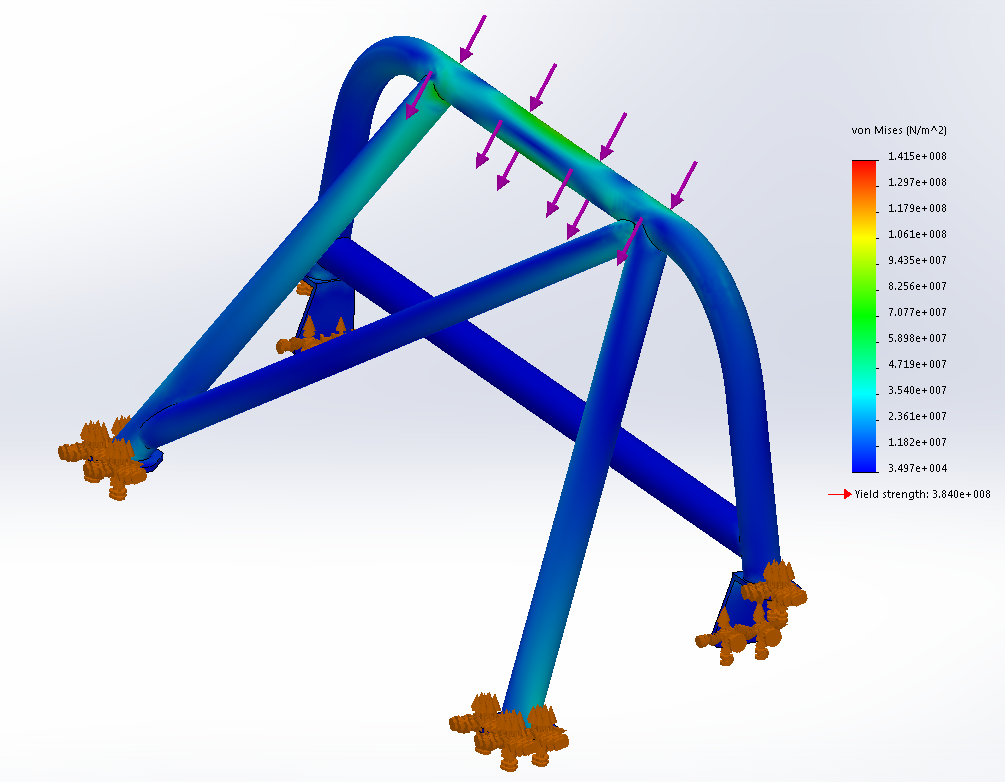 Bar without diagonal, corner/radius loading on hoop (car lateral roll impact??) exceeds material yield @ 2T 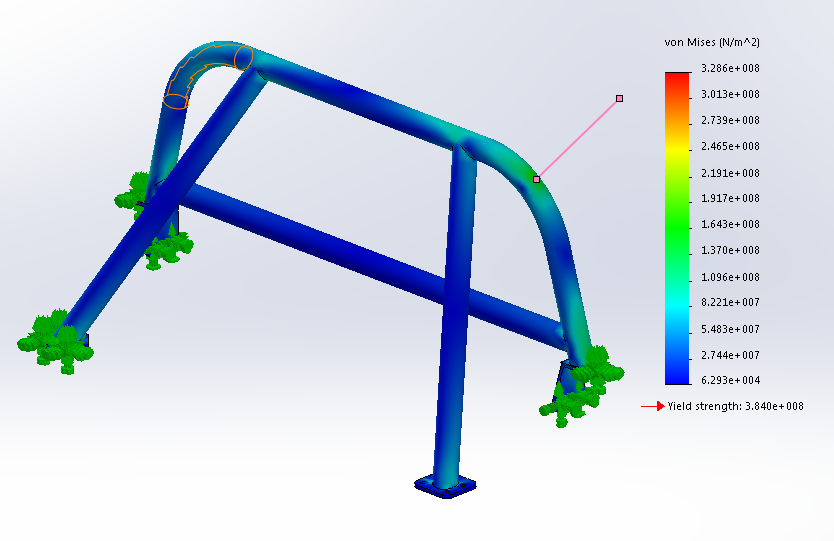 Bar with diagonal, corner/raduis loading on hoop (car lateral roll impact??) exceeds material yield @ 2.5T (resulting in 20% difference) 
|
|
|
|
MiataMark
Club Retro Rides Member
Posts: 2,971
Club RR Member Number: 29
|
|
May 19, 2016 14:53:25 GMT
|
I've got a TR Lane roll bar, but I went for the cross brace with harness bar GPX). Haven't had to test it yet...
|
|
1990 Mazda MX-52012 BMW 118i (170bhp) - white appliance 2011 Land Rover Freelander 2 TD4 2003 Land Rover Discovery II TD52007 Alfa Romeo 159 Sportwagon JTDm
|
|
|
|
|
May 19, 2016 16:43:11 GMT
|
I would love that sort of analytical software :-)
My main concern was sideways deformation caused by a roll, which I would have thought is more likely than a forward slide.
|
|
|
|
|
|
May 19, 2016 16:44:19 GMT
|
I've got a TR Lane roll bar, but I went for the cross brace with harness bar GPX). Haven't had to test it yet... That looks as though it would rip out of the car before it fails :-)
|
|
|
|
meltedcheese
Part of things

Please, Don't Sqeeze the Volvo!
Posts: 403
|
|
May 19, 2016 20:07:51 GMT
|
I would love that sort of analytical software :-) My main concern was sideways deformation caused by a roll, which I would have thought is more likely than a forward slide. It's a pretty useful bit of kit, the forward slide scenario was just an idea it also it confirms the sort of static load the frame can handle. Calculating the dynamic shock load from a roll is a fair bit more complicated but in the images above you can see the impact on the bend, this would be the location of the first and the hardest point of contact where the tube would meet the tarmac during a roll. Again this is likely to be different with a full cage as it also has to account for side impact etc... I'm pretty sure shock loading can be greater than the applied static but I'm not sure how much, may have a look into that, as when you consider the speed/g x mass the forces can be huge. The thing that does present a bit of comfort to the study is a general rule of thumb for factor of safety (FOS) is usually 1.6 or greater, based on the percentage comparison of the different designs they both end up above 1 x FOS.
|
|
|
|
meltedcheese
Part of things

Please, Don't Sqeeze the Volvo!
Posts: 403
|
|
May 20, 2016 11:24:41 GMT
|
Sorry to keep labouring on the roll bar subject, but just another quick note, managed to find a shock loading calculation, if anyone is interested I would be happy to post the test images of the deflection/distortion that the cages would suffer during a collision at a range of speeds.
Not to be taken to seriously but quite interesting to see.
|
|
|
|
|
|
May 20, 2016 14:04:52 GMT
|
Yes please :-)
|
|
|
|
|
|
|
Of course I am interested!
|
|
194? Willys Jeep MB 1965 Volvo 544 Special 1968 Opel Rekord 1975 Opel Kadett Estate 1985 Mercedes-Benz 230E 1985 Datsun 720 King Cab 4x4 diesel 1997 Volvo S70 2.5SE (ex. "Volvo544special65" - changed to more reader friendly username.  )
|
|
meltedcheese
Part of things

Please, Don't Sqeeze the Volvo!
Posts: 403
|
|
May 22, 2016 20:13:25 GMT
|
I'll try and get a bit of time to run the calcs of a lunchtime sometime this week gents!
|
|
|
|
|
|
May 23, 2016 10:27:03 GMT
|
Ideally you'd run the rear braces up to the centrepoints of the bends and then a diagonal between them.
Also, when modelling for stresses, don't forget that the material on the bend is thinner than the rest.
|
|
|
|
|
|
May 25, 2016 19:18:44 GMT
|
I'm pretty sure shock loading can be greater than the applied static but I'm not sure how much, may have a look into that, as when you consider the speed/g x mass the forces can be huge. The thing that does present a bit of comfort to the study is a general rule of thumb for factor of safety (FOS) is usually 1.6 or greater, based on the percentage comparison of the different designs they both end up above 1 x FOS. The Mira tests our cages went through for dynamic shock loading were for a minimum of 7.5G + 562.5kg (driver weight * 7.5) - so for an MX-5 that's about 8000kg vertically, longitudinally (both forwards and back) is 5.5g + 412.5kg - so about 6000kg, and 1.5g lateral (as the car is likely to keep rolling with more force than than applied - so approx 1600-1700kg. Point loadings of the above are also applied across 250mm sections and deflection needs to be less than 50mm and ideally under 25mm around any parts that may bend close to the head area.
|
|
|
|
meltedcheese
Part of things

Please, Don't Sqeeze the Volvo!
Posts: 403
|
|
May 27, 2016 11:59:04 GMT
|
Ideally you'd run the rear braces up to the centrepoints of the bends and then a diagonal between them. Also, when modelling for stresses, don't forget that the material on the bend is thinner than the rest. Both good points Phil, the angle on the cage has come about mainly due to the decision to keep soft top, this was the best for our situation, compromise always seems to leak into this sort or project  The software does do a pretty good job at over compensating in general for these kind of factors, do you know what percentage of material thickness you would loose of a 90 degree bend by any chance? Great build thread btw! That is pretty insane! Great to get some info from the horses mouth, I'm pretty new to automotive based stress analysis I'm more used to adhering to marine so any info is appreciated, I'm guessing the sortof loadings your talking about is for a full cage not just a roll bar or is it across the board?  Thank you for the info, didn't get round to posting the FEA of the deflection but it looks pretty good, it certainly highlights the need for a bit of torsional stiffness though! I'll get it up next week!
|
|
|
|
|