|
|
Apr 16, 2007 18:29:12 GMT
|
Bear with me, it is retro related.  I know a few of you have studied mech/auto engineering in Uni' and I think CR500DOM is a design engineer in the car industry, so you never know! I have converted the Celica to rack and pinion steering and the rack is mounted in front of the axle centre line. The original steering box and drop links were mounted behind the axle. 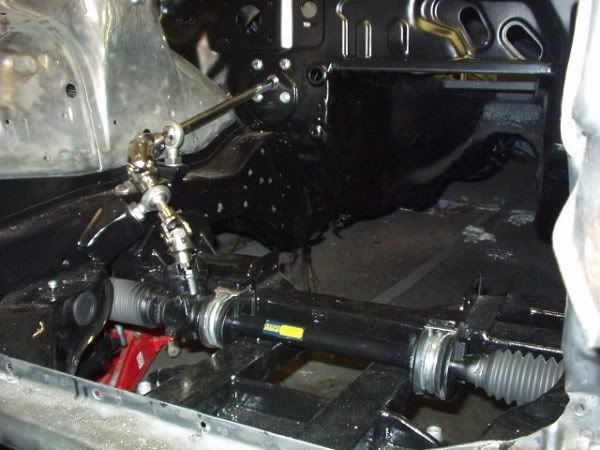 To achieve the correct Ackerman steering angles, the steering arms pivot points have to lay on an imaginary line drawn from the centre of the rear axle through the pivot point of the strut. Keep up at the back....  The up-shot is, that I have had to design new cranked/offset steering arms..... 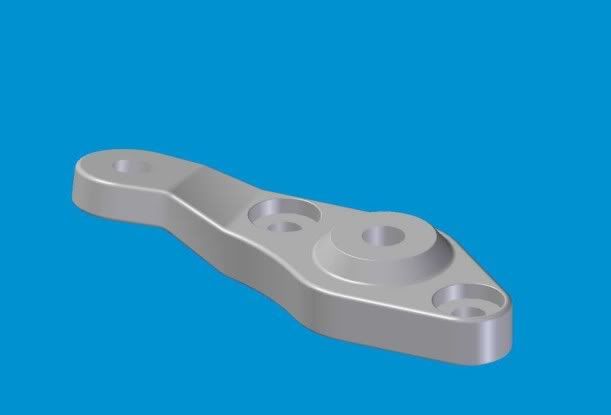 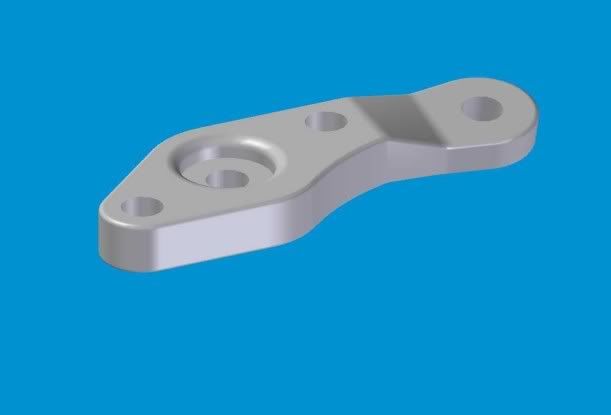 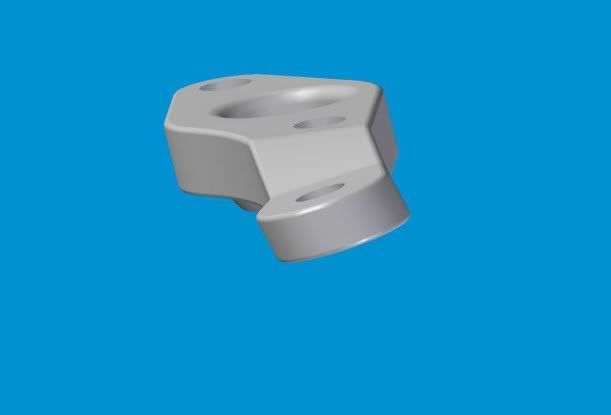 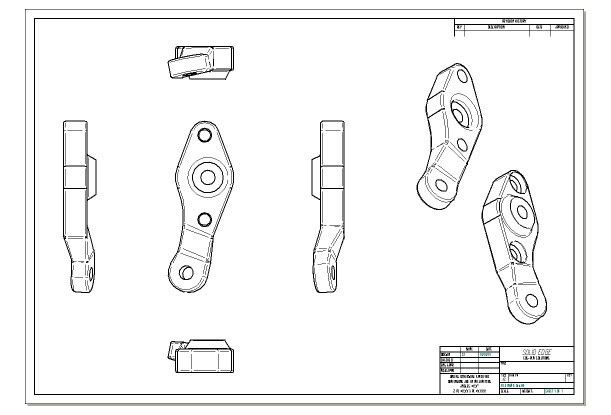 Now it's no problem getting these CNC machined from billet...but there lies my problem. Original steering arms are usually forged or cast and then heat treated - machining from billet will have a different grain structure and hence different mechanical properties etc I know this is a massive subject, but a few things would really help me out..... 1. What is the tensile strength of an existing forged/cast steering arm and any idea of the post forge heat treatments (normalising, annealed etc) 2. Materials. A standard carbon steel with post machining heat treatments or something more exotic like Cro-moly alloy (a lot of the 4x4 crowd in the USA have custom arms made out of this stuff). What I need to achieve is the correct balance between strength and ductility - which takes me back to question 1  Any info' or links would be very much appreciated. I am a design engineer, so I'm not going into this blindly - the arms are designed with more material than the original with careful note note not to design in stress raisers etc. PS. Told you it was long shot... cheers anyway!
|
|
|
|
|
|
|
Apr 16, 2007 19:02:51 GMT
|
what material were the arms originally? Probably a forged steel item i would have thought, do you have a photo of the original items? Have you done any load calculations? what do you think the maximum load the arm will be under? If you can find out the material of the original arms then a strength can be calculated for them, the yeild point of the material will be known and the ductility. From this you can then engineer the new arms around the old ones and include a decent safety factor. More info pls  J
|
|
|
|
|
|
Apr 16, 2007 19:53:00 GMT
|
Cheers J. Unfortunately I don't know the original material spec', other than it's forged steel. Here's some pics of the original (cut about and welded during my R&D stage) 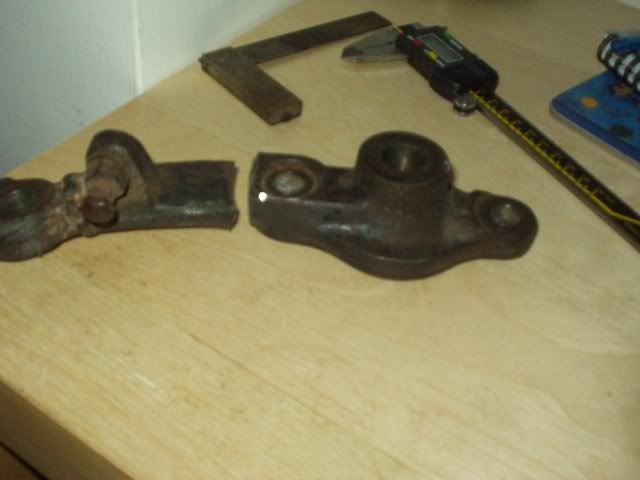 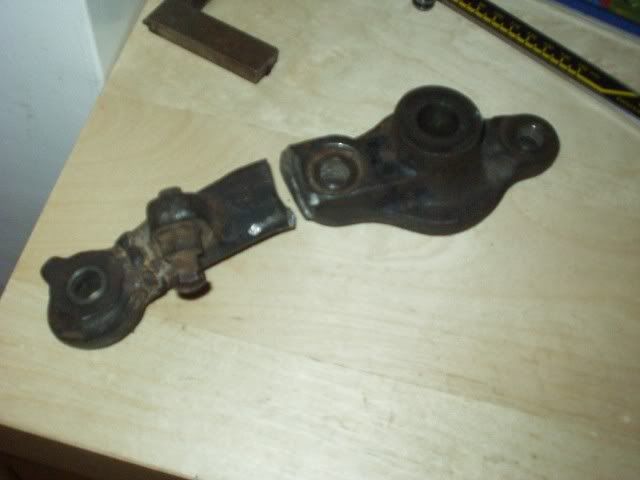 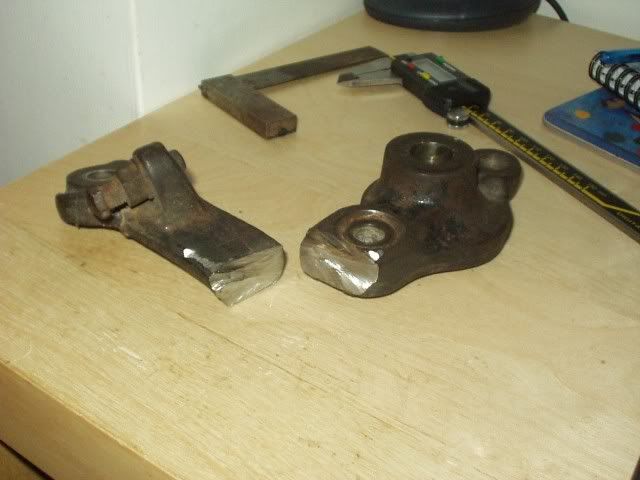 With regards to the loadings - again another unknown at the moment. I guess statically the main loading will mainly be friction (tyres to road) taking into account the length of the arm/lever and the corner weights. Dynamically - guess it can be approximated, but at this point I just don't know. Hence why I've based my new design on the existing design + a bit more material for a safety factor. It's the physical differences between machined from steel billet (and heat treated) and forged steel material I really need. If I can find out the material spec' and heat treatments of a 'standard' forged steel steering arm, I can pump all the data into my FEA software and probably get all the answers I need.
|
|
|
|
|
|
Apr 16, 2007 20:02:42 GMT
|
i might be a bit cheeky at work tomorrow and get some average materail specs for forged suspension items / billet prototype items. The thing is there are ups and downs, the forged item will have a better grain structure, but the design wont be optimal, nor the surface imperfections. The billet item will not be optimal with regards to grain structure but the surface finish will be smooth and free from surface based stress raisers, also the design will be far improved due to manufacturing and cost restraints being ignored  J
|
|
|
|
|
|
Apr 16, 2007 20:09:34 GMT
|
Cheers J, that would be very, very, very interesting to see.
Don't risk your job (obviously) if the data is sensitive!
|
|
|
|
Retrojunkie
Part of things

The drinking team with a racing problem!
Posts: 603
|
|
Apr 16, 2007 20:59:10 GMT
|
I'm still at the back trying to eat my crisps really quitely using the absorb on the tounge technique :lol:
|
|
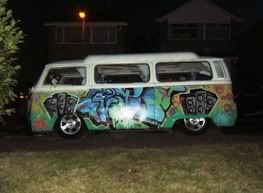 '84 Mk1 Golf GTi Cabby '99 Saab 9-5 Estate (lpg) 2.3 Turbo
|
|
|
|
Apr 16, 2007 21:33:02 GMT
|
For that you can write out 100 times : 4340 (chromoly) normalised alloy steel has a ultimate tensile strength of 186,000 psi and a yield strength of 125,000 psi ....in Latin. 
|
|
|
|
|
|
Apr 16, 2007 21:47:16 GMT
|
and in metric 
|
|
|
|
B-8-D
Posted a lot
 
down to one car!!
Posts: 4,038
|
|
Apr 16, 2007 22:03:23 GMT
|
don't look too technical on it..... test it!! make some rough arms and try and bend um.... sometimes practice is better than theory...!! I'm sure you could go welded tube cromoly and have a sufficient strength.... as for machiened... i don't think you should have any probs..... if its steel then the arms should bend a certain amount (dictated by what steel) to a certain amount rather than sheer like certain alloys would and so the goemetry would change rather than snap so id say destruction test them and youd have a certain answer....... don't rely on theoretical maybe's.... test um....... si
|
|
|
|
|
|
Apr 16, 2007 22:45:29 GMT
|
I know what you mean... This is the only thing on the whole car that has phased me, which is why I've left it until last. Cars I've built in the past and stuff I've done to them, I did just 'cause it felt right, and if it failed just rebuild it better next time and learn from your mistakes. I guess I'm just getting sucked down into the bureaucratic/solicitor dictated culture, that somebody is to blame if it all goes balls up. [Daily Mail Mode] Child hurt in modified car steering test failure accident - BAN THEM NOW[Daily Mail mode] Sad isn't it - hardly the Hotrod spirit ..... 
|
|
|
|
Retrojunkie
Part of things

The drinking team with a racing problem!
Posts: 603
|
|
Apr 16, 2007 23:22:34 GMT
|
I agree with Si...
Build it and test it on a control.
I have always tested everything I have until it breaks and it's at that point that I know I need to fix it, OK I haven't moved out of the boundrys and into where you are and it certainly does need a lot of thought, but as long as it's not on the car when it breaks you should be ok.
However, I can't and never do use a tape measure and I thought a Spirit Level was a overpriced way of serving drinks in pubs. I don't imagine that there are too many guesstimators on here like me though he he
Oh and....
4340 (chromoly) naturalis formalis tribuo chalybs has a atomus intentus vires of 1282.42 Mpa quod a concedo vires of 861.84 Mpa
I think that's right... ;D ;D However I don't speak Latin but my computer does
|
|
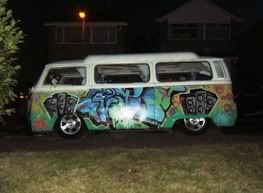 '84 Mk1 Golf GTi Cabby '99 Saab 9-5 Estate (lpg) 2.3 Turbo
|
|
|
|
Apr 17, 2007 17:38:29 GMT
|
Fair play to you for all the technical work here lads, beats my "bluff it, break it, buy the right part" sequence anyway!
My head hurts from reading this stuff though!
|
|
Club Retro Rides Member
|
|
|
|
Apr 17, 2007 17:56:00 GMT
|
right done some reasearch,
If you can get a hardness test done on the surface and the internal portion then i can tell your the material UTS, yeild, and wether its been hardened. I think that the material is probably a forged mild steel that has been carburised.
Once the hardness is known then the material can be matched with a suitable match and hardening sequence.
One thing, i wouldent use cromoly as its quite brittle and more liable to crack and break rather than bend like a mild steel.
CHeers
J
|
|
|
|