sowen
Club Retro Rides Member
Posts: 2,245
Club RR Member Number: 24
|
|
|
It really does make an epic noise, I drove it just after the supercharger was fitted and the turbo hadn't been plumbed in and the noise and performance was just astounding for a tdi! More video's do need to be arranged 
|
|
|
|
|
sowen
Club Retro Rides Member
Posts: 2,245
Club RR Member Number: 24
|
|
|
I was originally going to do this setup on my 300tdi in my series, using a Holset HX35 and Eaton M90, because with the pump wound up as far as it would go and advanced fully I found it so frustratingly slow.
I now have my Mercedes OM606 instead which makes a far cooler noise, which may end up supercharged too!
|
|
|
|
lowen
Part of things

Posts: 50
|
|
|
Thank you all. I reckon most of it would fit a Rangie if packaged a bit nicer, the charger mounts quite low down just all the plumbing takes up the room. Would certainly terrorise all the 50k upwards brand new Vogues on the roads! I do agree more videos are required, apart from a lack of light I've not touched the pump properly so it sounds like it struggles compared to it's potential. I've been heard almost a mile away whining so I'm quite impressed, but really I want to stick to the Land Rover engine to prove it's not a bad engine for tuning, but not the best obviously. New turbo arrived finally! It was abit of a pot luck guess on ebay as it was just described as a recon daf 65 lorry turbo, researching led me to believe it to be a T04 and I found it was so. From a 5.9L Cummins euro 2 diesel (90's era I think), so my logic was the supercharger and T25 would turn the 200 into a 5L engine, a lorry would get full boost below 2000rpm, add in realism factor and I would expect 2500-3000rpm it should be fully spooled ideal for motorway accelerating etc - I'm no turbo expert so only guesswork. An added bonus is lorry turbos will run for a long life and that this one is a recon too! 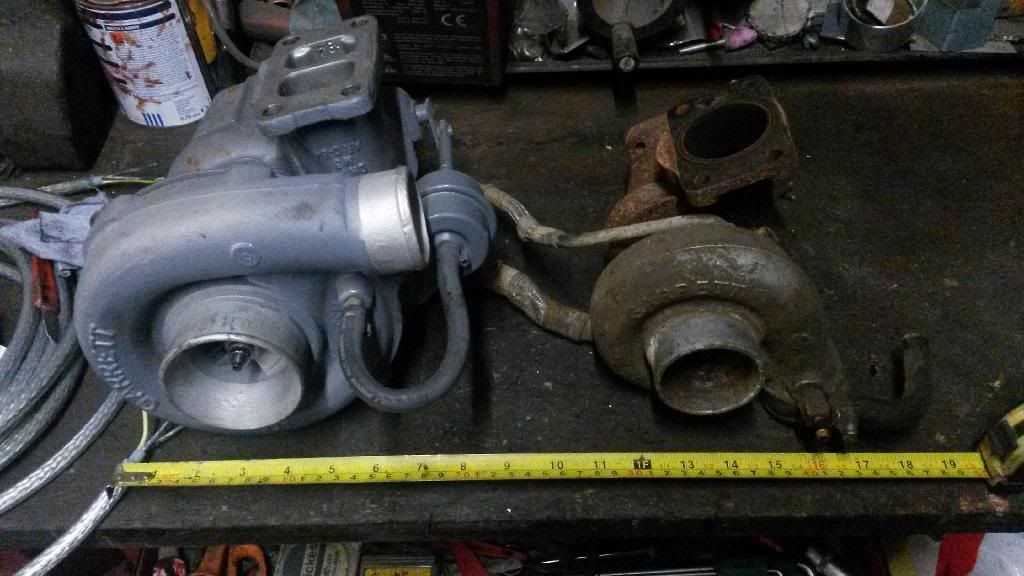 My current set up works well up til high range revs so I want to keep that, therefore I've decided that it wouldn't be much more work to keep the standard turbo in the set up to create compound turbos compounding into the supercharger, a seamless lag free experience. Here's the schematic doodle with some comments about how it works, I'm open to suggestions however my goal is to avoid electronics as much as possible and keep it simple. A temporary name I've come up with is Bi Compound Charging. 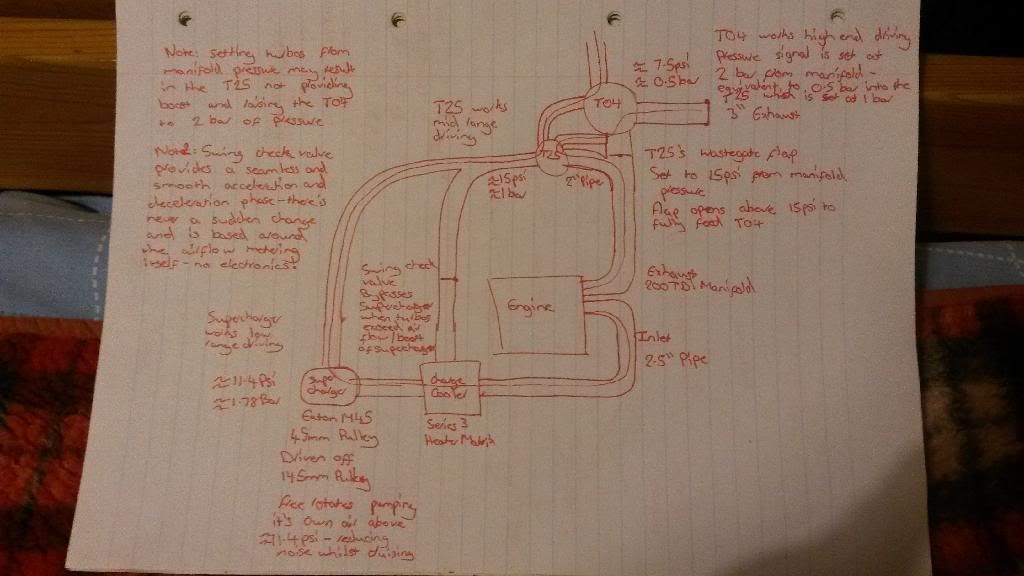 The supercharger does all the work til the T25 is able to take over the airflow capacity. When it pumps more than the eaton air will flow through the check valve decreasing heat from the supercharger as well as cruising noise. The exhaust gases continue to pass through the T25 til 15psi where the external wastegate I shall be making opens up, thus giving the T04 all the best for making the correct airflow. Then when decelerating and the turbos spool down the wastegate will close below 15psi to keep the T25 spinning, then the check valve will close as the T25 pumps less air than the eaton. To me it's a very simple layout and hopefully effective. If I struggle with making the external wastegate then I'll resort back to the original T25 one. Whilst waiting on exhaust flanges and adaptors to arrive I decided it was finally time to tweak my injector pump properly. I'd previously read Land Rover forums saying turn the bosch ve boost compensator diaphragm 90° and it'll be a rocket, I did this last april but wasn't enough so I set about changing it some more. It's now about 120° clockwise from stock - running on the steepest side of the cone for more fuel on boost. To give it some more travel I'd read keep the 4mm thick plastic washer safe in the bin. As advised by my brother when he turned his pump up, I found that leaving the plastic washer out just catches and bottoms out on the pin it rubs against when on high boost, so instead I fitted an offcut of 1mm aluminium that was lying around in it's place giving 3mm of extra movement, a big increase of this pump. Then I put it back together making sure I was going to use the steepest ramp on the cone. I also moved the maximum throttle stop back to allow greater throttle travel and hopefully more fuel delivery and power / torque. 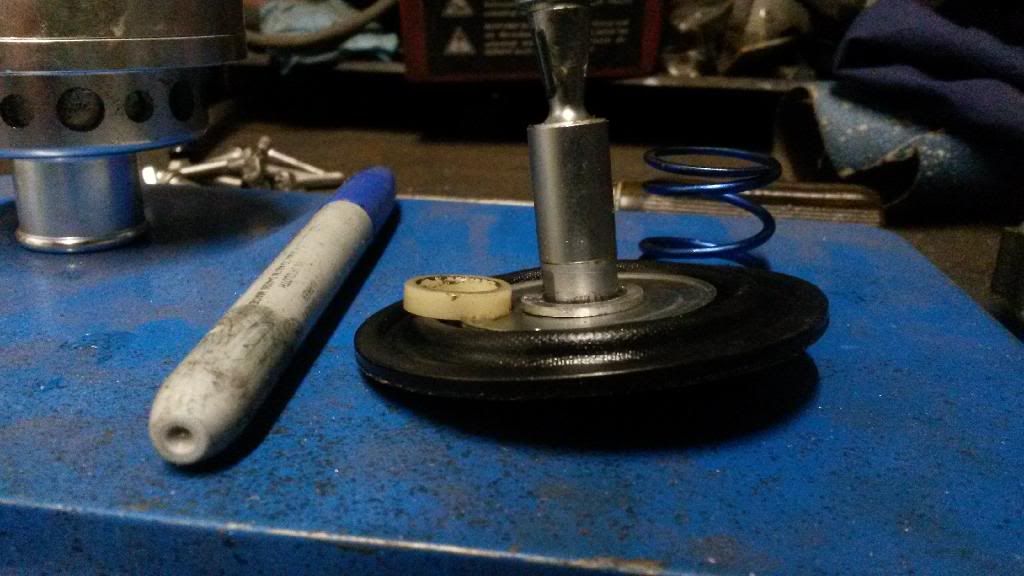 My goal is to max out the fuel flow of this certain bosch pump to find out what potential it actually haves - seen as most land rover forums suggest the engine will implode from anything over 1 bar of boost or that a bigger intercooler, is the main engine mod, there doesn't appear to be much knowledge of what the engine can handle safely or how to upgrade it. From this all the screws are being maxxed out so that my foot does what the governor used to do, except I have the choice when to put more fuel in and when not to. A quick test drive of it's current state and it goes ridiculously well for an old Land Rover! I should think it could match quite alot of cars at accelerating away from traffic lights now. This test drive also gave the un plumbed chargecooler a chance to warm up or stay cool (was single figure ambient temp tonight). After 10 mins I couldn't touch the water pipes for the cooler but the rest of the engine was still only warm and the chargecooler box was midway between the two roughly. This suggests that it absorbed alot of heat in a short drive so plumbing it in and measuring temperatures should be quite interesting...
|
|
|
|
pork
Posted a lot
 
Posts: 1,665
|
|
|
Awesome stuff
Where'd you get the swing check valve ?
|
|
|
|
lowen
Part of things

Posts: 50
|
|
Jan 10, 2014 19:07:08 GMT
|
I haven't got one yet, for the cost of buying one like this: www.ebay.co.uk/itm/370972832392?redirect=mobile I could make one a bit cheaper and much shorter to fit in the space I have available. Plus not in plastic! Incase it seems it, the round thing is from my injector pump
|
|
Last Edit: Jan 10, 2014 19:08:51 GMT by lowen
|
|
|
|
Jan 10, 2014 22:30:33 GMT
|
I've just read through the whole thread... very interesting project. I like the way that you are trying to use as many Land Rover derived parts as possible. The checker plate bonnet scoop (with some added mesh on the front) and the snorkel style air filter are both in keeping with the style of vehicle in my opinion, and your mounting of the supercharger looks nice and solid. I have a couple of observations that might be helpful. First, there is nothing wrong at all with finding and utilising whatever parts are available to you at reasonable cost,this is also part of my own philosophy, but with things like the turbos and the supercharger it is definitely worth doing some initial checks on their suitability for the job. On the supercharger, when used on a relatively low revving diesel engine like this rather than a petrol engine it may well need to be geared at a ratio of 3:1 to do the buisness even within what for it would be normal operating speeds, and with a turbo coming in at higher rpm as well it really only needs to make boost at lower engine speeds. It would most definitely be worthwhile getting hold of a compressor flow map for that unit and aiming to get your required airflow rate and boost pressure to coincide with its areas of greatest efficiency. The new driven pulley that you have looks like it will have a considerably shorter circumference, and if you aren't careful you could find that the supercharger is being run far too quickly where it will be very inefficient, produce a lot of heat, and itself be less mechanically reliable or run into other problems. The stock turbo should already work with this engine, but it is probably just a half-way house on size now. The supercharger will overlap its operating rpm at lower rpm by quite a bit, and a bigger turbo will surpass it at the upper end of the rev range. It would most likely be better to do away with the stock turbo completely and select a bigger one that would do a better job of taking over from the supercharger and giving more top end performance with less exhaust restriction. Keeping the stock turbo in circuit would just choke up the exhaust flow and prevent a bigger turbo from working without offering any real benefit. Arranging for bypassing of the compressor side plumbing is quite easy, but staging the exhaust flow to two differently sized turbine sections without defeating the purpose would be very difficult. Again on the larger turbo, it would have been better to get hold of a compressor flow map for it from the internet and do some basic calculations to see how well it would work in this application first. I'd guess that it is likely to be far too big to operate well even at the upper end of the engines rpm range if good all round performance is the main priority, but only checking against a map can show how good or bad at this job it is really likely to be. It isn't so much that this turbo won't work on your engine, but that it is very likely that it won't work as well as a properly selected turbo would. Even two very similar looking turbos can give very different characteristics, it just isn't possible to judge on appearance alone. On the plus side it isn't too late to check this out before getting involved in making new manifolds, and there might well be a healthy resale market for the big turbo if you do decide against using it. This pulley and drivebelt selection calculator might help to decide if your new driven pulley will be OK for this purpose without overdriving the supercharger excessively... www.csgnetwork.com/pulleybeltcalc.html
|
|
|
|
|
|
Jan 11, 2014 13:41:51 GMT
|
two turbos and a supercharger is a bit mad. the bosch ve4 pump is used in a lot of other engines, since your going mad on power maybe convert it to hybrid 11mm: 306oc.co.uk/forum/thread-212.htmlalso i'd start with a prima80t pump ve4/11F2500R229, that will raise the rpm limit to 5000 (stock limit is 3800rpm) www.vepump.com/
|
|
|
|
lowen
Part of things

Posts: 50
|
|
|
The bonnet needs redoing and painting when everything is packaged in, my goal is to make it look like the current defender puma bonnets that are raised to try and hide what's underneath - even if the noise gives it away. Oddly enough the scoop was a temporary solution 18months ago, ha. I have a surplus of the eatons from buying them up a few year back for my mini, the new pulley ratio is 2.96:1 from 2.66:1 which I find coincidental you mention 3:1, I'd like it to be 3.5:1 for the extra noise and that my driving range is no higher than 3500rpm (not fond of revving engines as I prefer torque) but without extra belts I can't go anymore otherwise my crank pulley will get knocked on the axle. On the flow map I work it out as being in the 60% region once cruising at 2500 but the turbo will be doing the work at this rpm anyway, but on the way upto that it actually crosses straight through the 67% area (maximum efficiency). Driving it it feels right, with the new pulley it is actually very revvy now, a vast improvement without the blower fitted from before which is what counts in my books. The idea is the supercharger deals with getting the standard turbo going, which isn't capable of making much boost below 2000rpm by itself. Now it happily spools up just over idle on light throttle which is what I want and it does the main work when cruising. However as it can't flow much air the bigger one is needed which I reckon to be about the right size, and will outlast the engine, I've found it will flow between 500 and 600cfm upto 2bar boost - just above my goal. The concept is that I want as much air as possible going in to ensure all the fuel is burnt, being a diesel its much more tolerant than a petrol in terms of heat so its just the density problem will end up as my long term tinkering. I understand selecting flow maps for petrol engines cause of detination, but alot of big diesels don't cool the air down, they just pump a big volume through. I've ordered all the flanges I need for the exhaust  I'm going to exploit the twin scroll of the T04 and divert gas through the small turbo into one side, then have a flap on the other scroll side which opens to partialy bypass the small turbo but to keep them both spinning, ensuring that when backing off the small turbo is still spinning but can't over restrict the exhaust flow. Then the inlet side is just a simple swing valve to bypass the blower, no electrics to go wrong so will cause me no grief and isn't essential, will just quieten cruising noises. That's a handy site, I've not tried finding out what size the land rover pump is, but I'll have it apart one day to find out. The other concern is the size of the injectors being big enough or not. Got the new pulley fitted, standard size is 65mm, the new is 49mm. Decided to cut apart the standard pulley and make it fit to the new pulley rather than trying to press off pulleys and mess up an adaptor that is too big. If it fails it only cost me £17.50 and a bit of time. 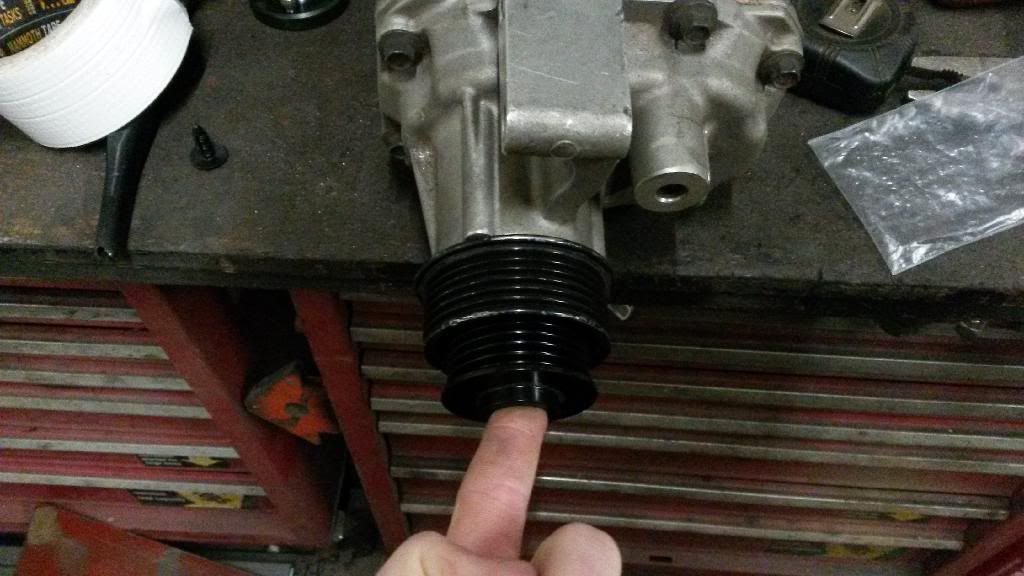 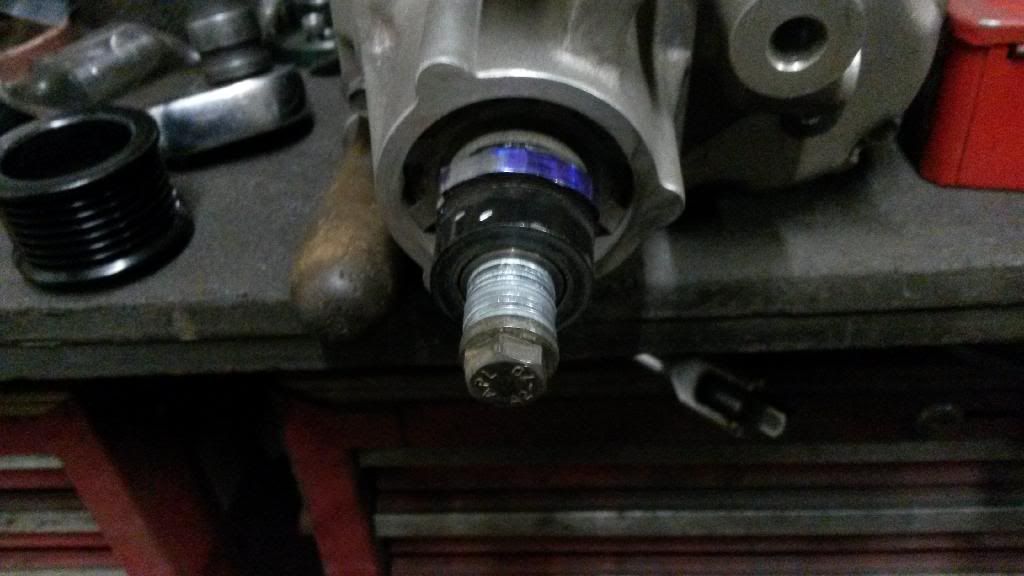 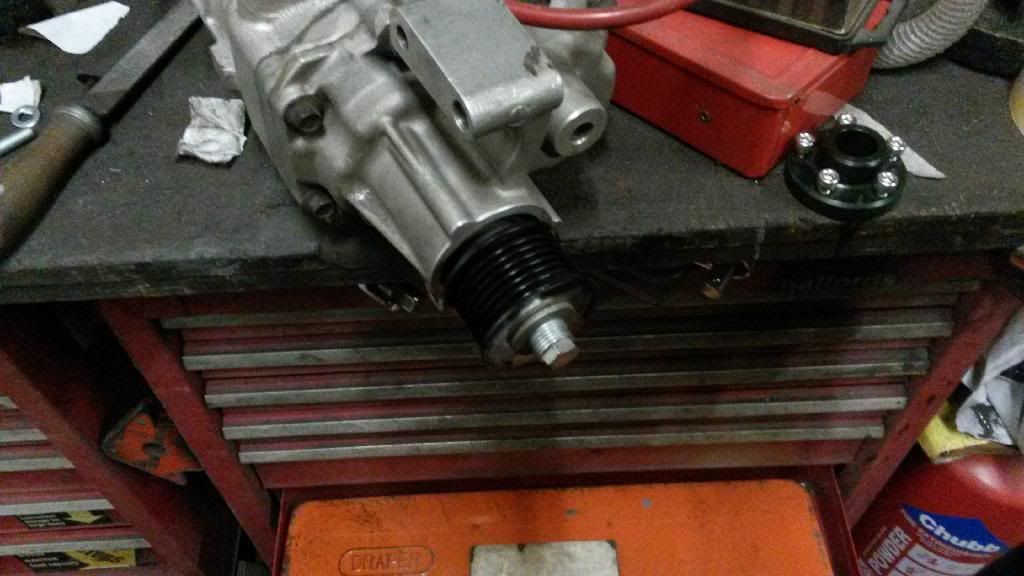 It now gives 3psi at idle and a much louder whine, and a light rev can get the turbo spinning quite easily so I'm happy with the supercharger for now.
|
|
|
|
|
|
Jan 17, 2014 12:43:22 GMT
|
Is the adaptor that you didn't use going to be available ? I need to go bigger on my pulley size and the ability to just get some standard pulleys turned (Rather than the collet type arrangement I currently have) would be quite useful, not to mention a lot cheaper
|
|
|
|
lowen
Part of things

Posts: 50
|
|
Jan 17, 2014 13:44:41 GMT
|
You've got a message  It'll only end up lost in the garage
|
|
|
|
|
lowen
Part of things

Posts: 50
|
|
Jan 17, 2014 17:01:55 GMT
|
Because it's the in thing currently, here are two vids I took on the way home from work today, demonstrating the current whine when revved with the new pulley. At the wrong rpm the sound can be very ear piercing when driving along!
Hopefully soon I'll get some outside driving videos taken
|
|
|
|
Copey
Posted a lot
 
Posts: 2,845
|
|
Jan 17, 2014 20:16:44 GMT
|
love this! real bit of fun! nice one
|
|
1990 Ford Sierra Sapphire GLSi with 2.0 Zetec 1985 Ford Capri 3.0 (was a 2.0 Laser originally)
|
|
lowen
Part of things

Posts: 50
|
|
May 18, 2014 18:49:54 GMT
|
Not much progress lately partially due to not being decided on how to make everything fit but have decided where the DAF turbo is going to fit after a while of tilting the housings around: 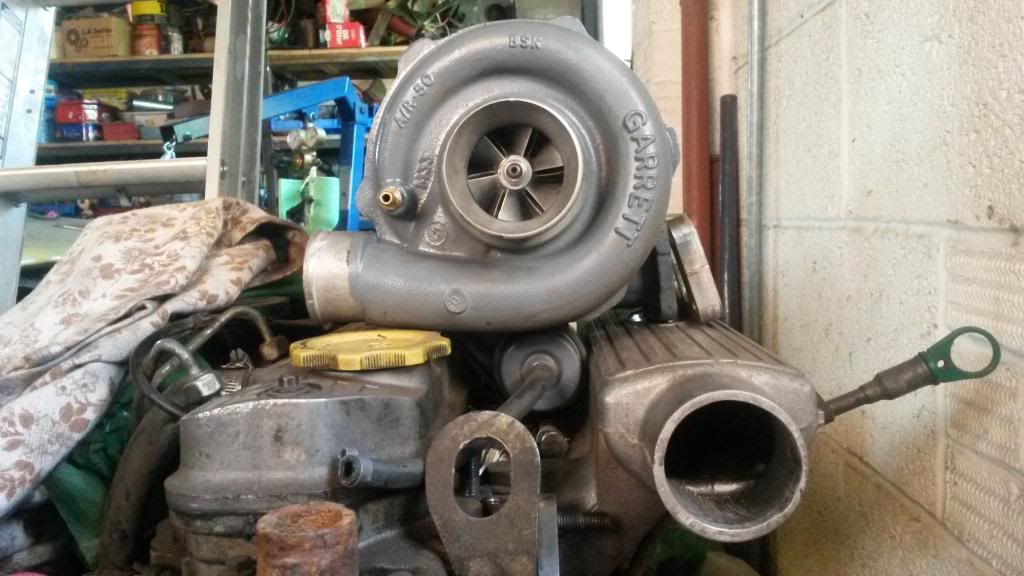 Will be higher up by 2 inches to allow for hoses and pipework that goes underneath, giving 9 inches height from the rocker cover to the top of the turbo, just enough to sit under a 2 inch bonnet bulge. Then if the small turbo is needed to help give the big one an extra push to get started, there is still the original location of the 200 turbo that can be added to the exhaust manifold. Making a custom exhaust manifold means it should all fit and I don't have to modify the inlet manifold unlike using the 200 exhaust manifold. To do list is build the mainfold, join all the pipes together, fit everything like the exhaust where it can fit and then it'll make noises  The makeshift pulley seems to be performing well so I'm happy with that being as it cost £17.50. Eventually I need to make a new supercharger plate so that the silencer ports are blocked off, it's getting rid of some of the noise and I reckon is why I'm only getting 2 - 3 psi at idle.
|
|
Last Edit: May 18, 2014 18:53:41 GMT by lowen
|
|
lowen
Part of things

Posts: 50
|
|
May 22, 2014 22:10:46 GMT
|
|
|
|
|
pork
Posted a lot
 
Posts: 1,665
|
|
|
Utterly insanely badass!
|
|
|
|
|
|
May 24, 2014 14:05:44 GMT
|
Loving this. I have a 300tdi in a Discovery and I've already tweaked my pump, lost the cat and exhaust boxes and wound the wastegate pipe in as far as it will go...but I still crave more power! I realise it will never be a rocket but a few more horses would make it so much more of a pleasure to drive. I may have to copy your super charger idea! Great work. Keep the updates coming.
|
|
|
|
benzine
Part of things

Posts: 337
Club RR Member Number: 87
|
|
|
I love this beast! I'd love to hear it in the flesh with a straight through exhaust
|
|
|
|
smart
Part of things

Posts: 134
|
|
May 25, 2014 18:59:22 GMT
|
What's your cruising speed on motorway? My dads just finished rebuilding his swb series 3 after putting a Perkins prima turbo diesel in. Engines great, needs furling turned up low revs to compensate for turbo lag, surprisingly quiet and not bad on vibrations either. Gearbox has been rebuilt and is nice and tight. Problem is low 40s mph is all you'd want to do out of overdrive, once you put the fairey in revs drop nicely but the overdrive screaming becomes unbearable at 50mph! What diffs you have fitted?
|
|
1998 Rover 400 Derv
|
|
lowen
Part of things

Posts: 50
|
|
Sept 2, 2014 22:25:16 GMT
|
Forkliftfred - the current supercharger and bracket could be up for grabs eventually, my update will reveal... Benzine - I've ran it with no silencer to check the volume of if, it sounded rough and quite nasty but that small silencer cleans the noise up with 2.5" tube all the way, great when driving past a wall or lorry and the sound bounces back. It's much quieter than most Disco's running round, I believe because my exhaust is short in comparison the sound doesn't echo in the tube unlike Disco exhausts. The new turbo will be treated to a 3" exhaust. Smart - when I had an overdrive fitted last year 70 was withstandable as I have foam insulation inside, but I'd happily sit at 60 as fuel useage was much lower. I've got 32" tyres with 3.54 diffs and used to have an overdrive so I used to get into the mid - high 30mpg's on the motorway but had enough pulling power to keep at 60 on the hills before I touched the pump. My overdrive whined and was unbearable, last year it dropped all it's oil on the way home from holiday and pulled the teeth off one of the gears so I've not been above 50mph since then as it's just too loud inside. Update time!I thought it time for an update so here's one.
Lighting Upgrade And De - Clutter
Currently this is my daily drive whilst my Rover 400 is off the road to fit a smaller turbo, doing 7 mile trips to work through villages and country roads with 10% diesel, 10% waste oil and the rest cooking oil I'm getting 22 - 25mpg out of it (and been terrorising all the local disco's that have wound up pumps and emit big smog clouds) , last month was MOT time and on the way to the test station one of the indicator bulbs fell out of the holder over a bump, otherwise it passed with no issues. This and the lack of nightime visibility has pushed me to purchase all round LED lights as driving with candles is not what I would class as fun. They were pricey but worth the investment, at the same time I decided that I would try to improve the wiring by fitting Bosch Superseal plugs to all of the lights to try and keep the damp out then later add in an additional earth wire to a dry location to make sure the lights are earthing properly.
They came in a box wrapped in warning labels that must have been tempting the couriers to do exactly the opposite lol
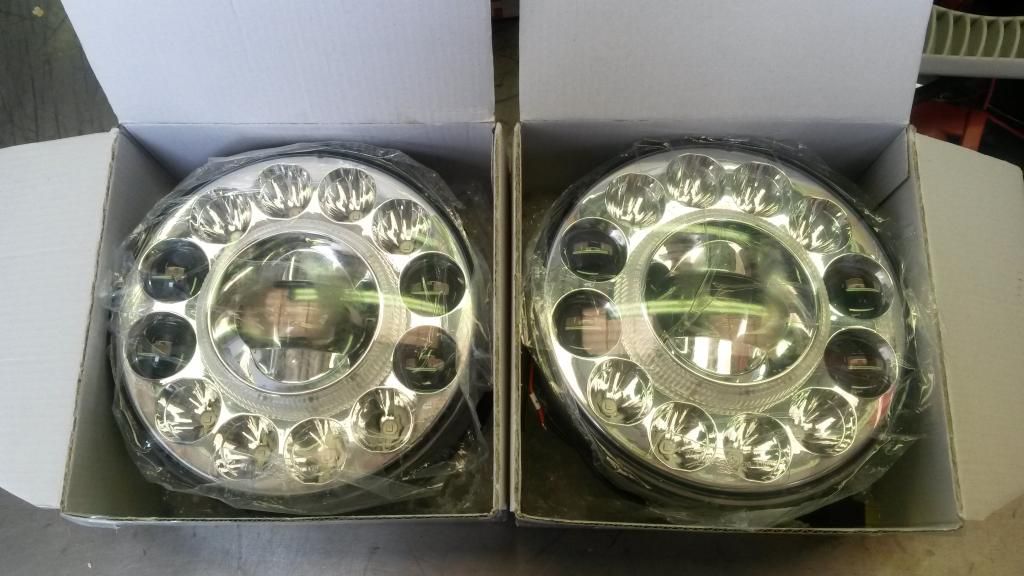
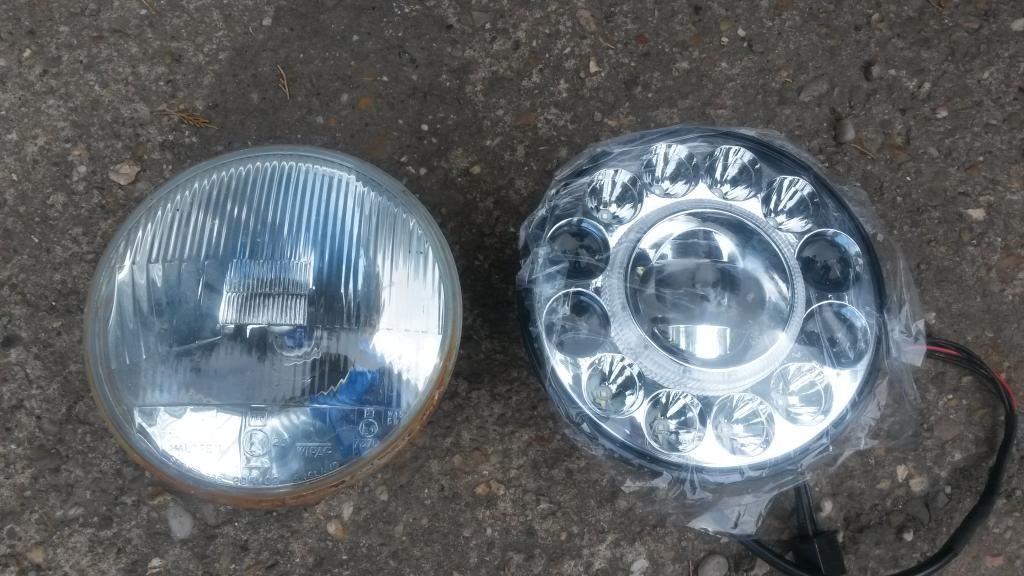
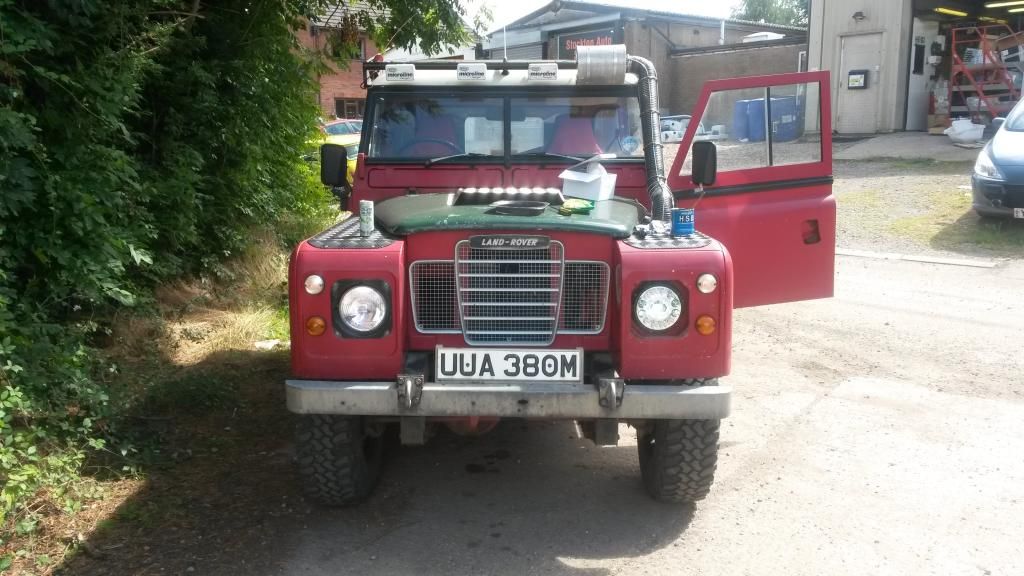
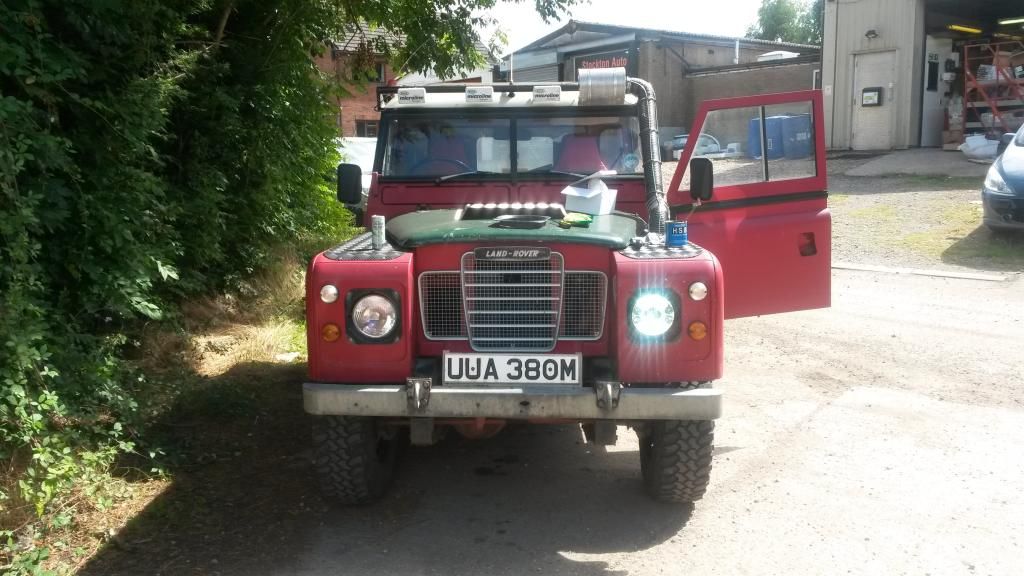
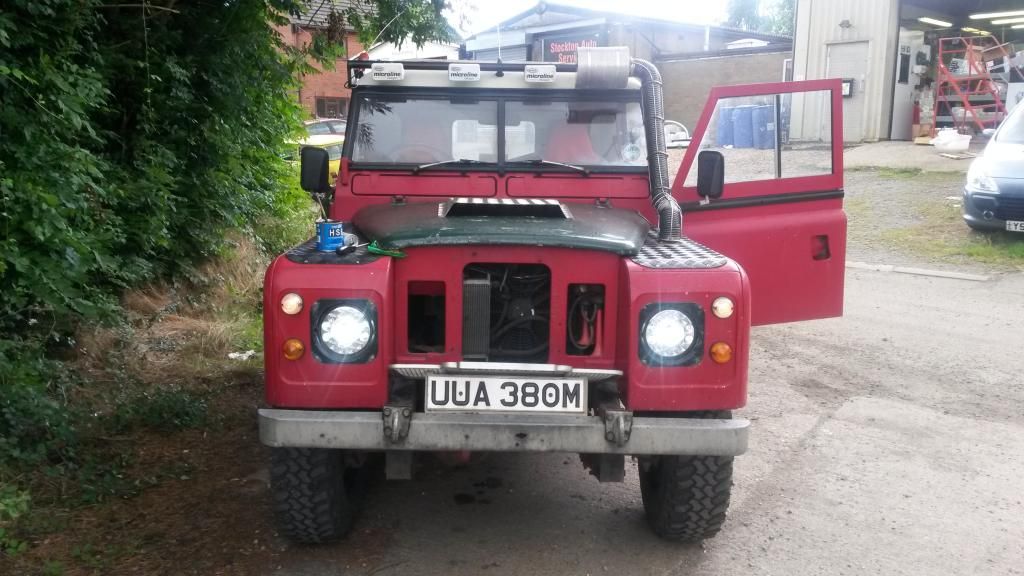
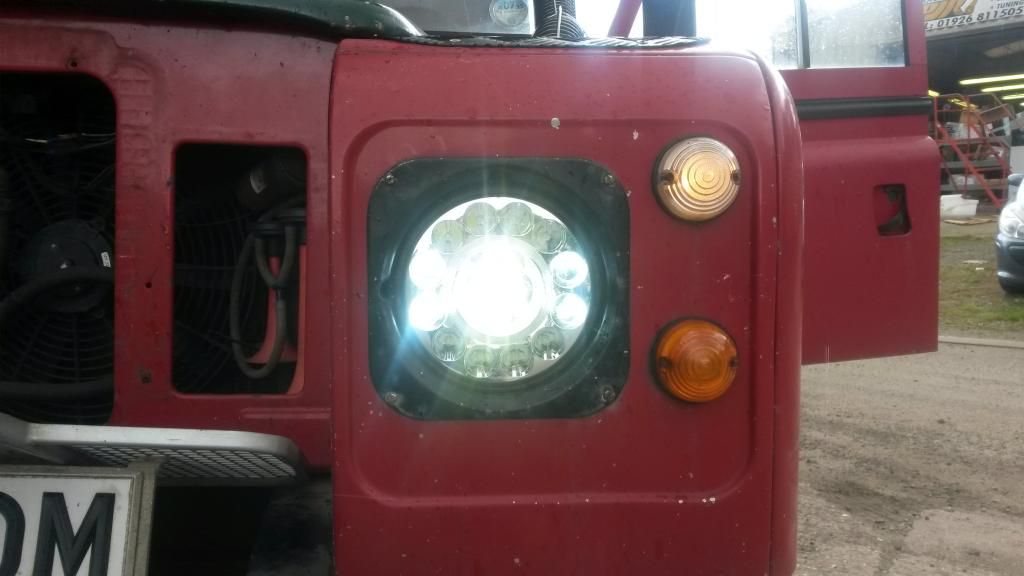
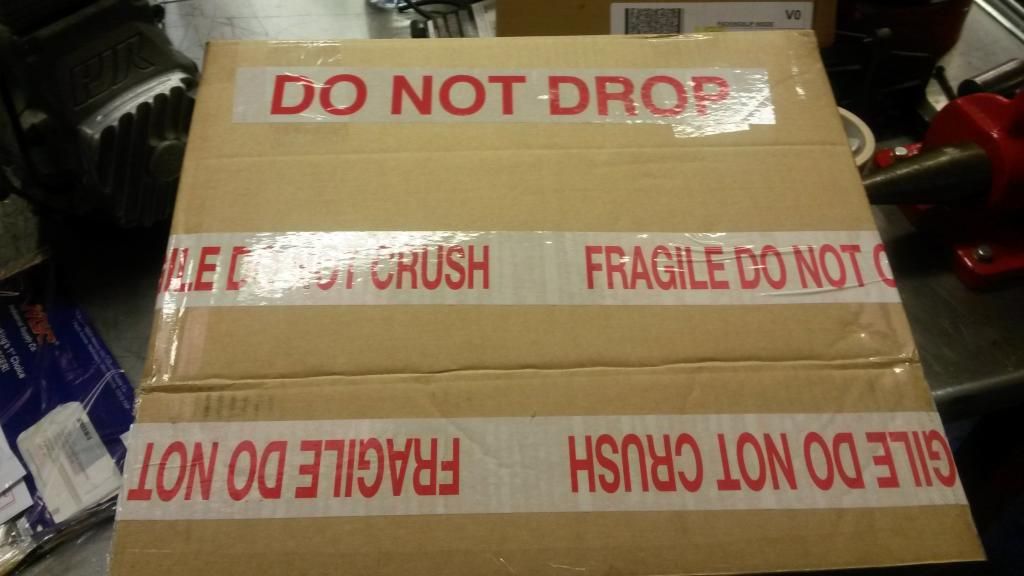
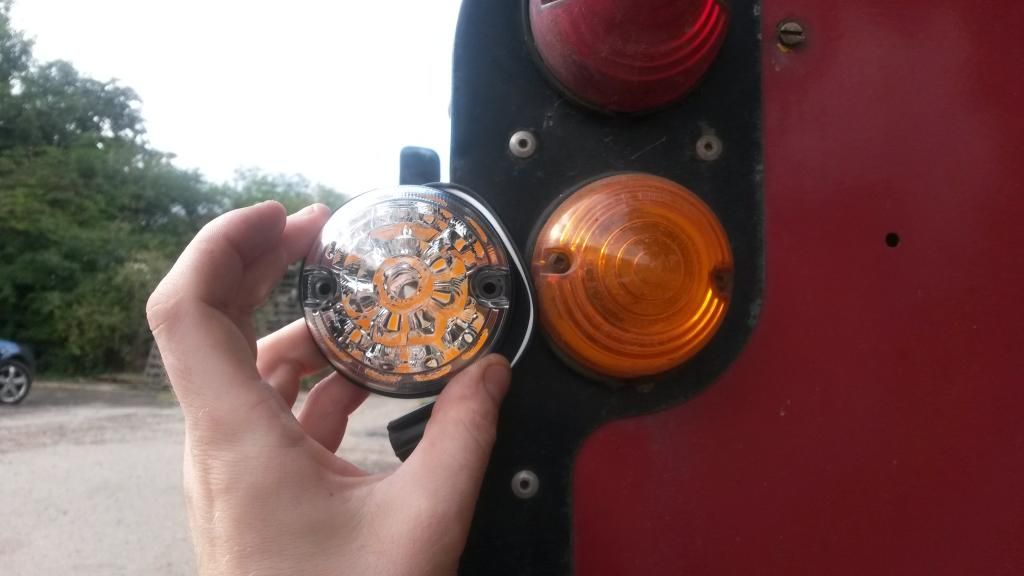
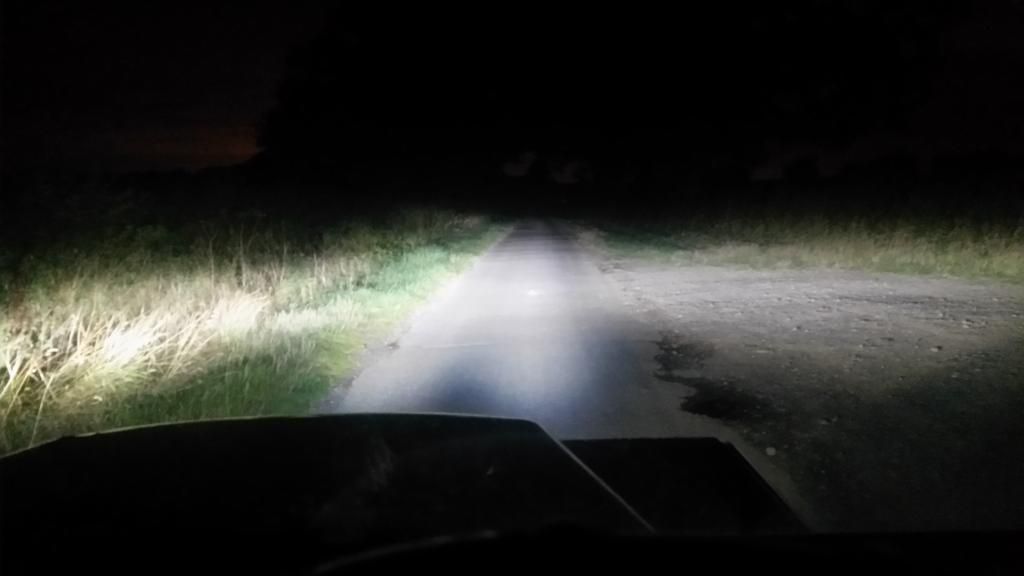
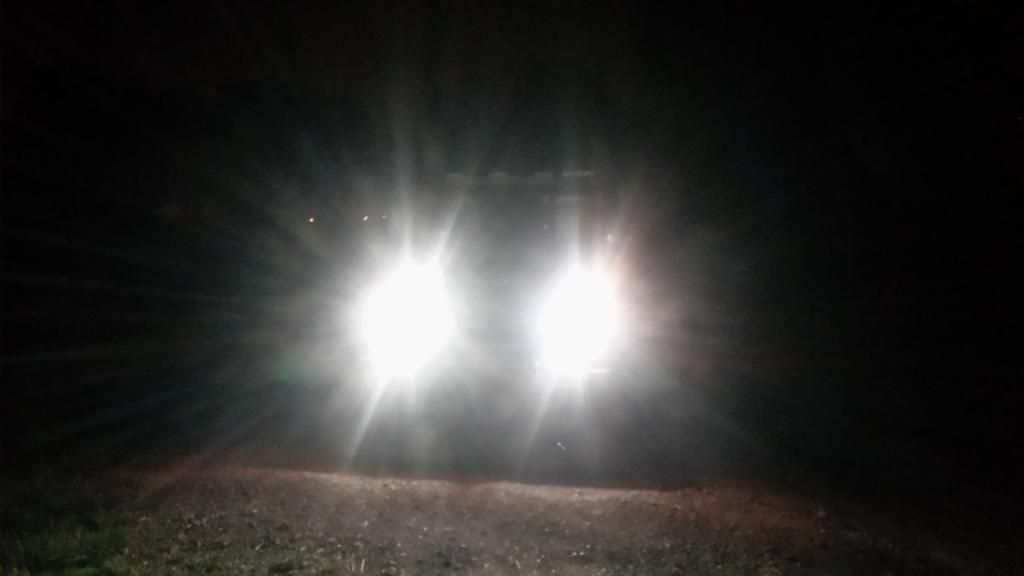
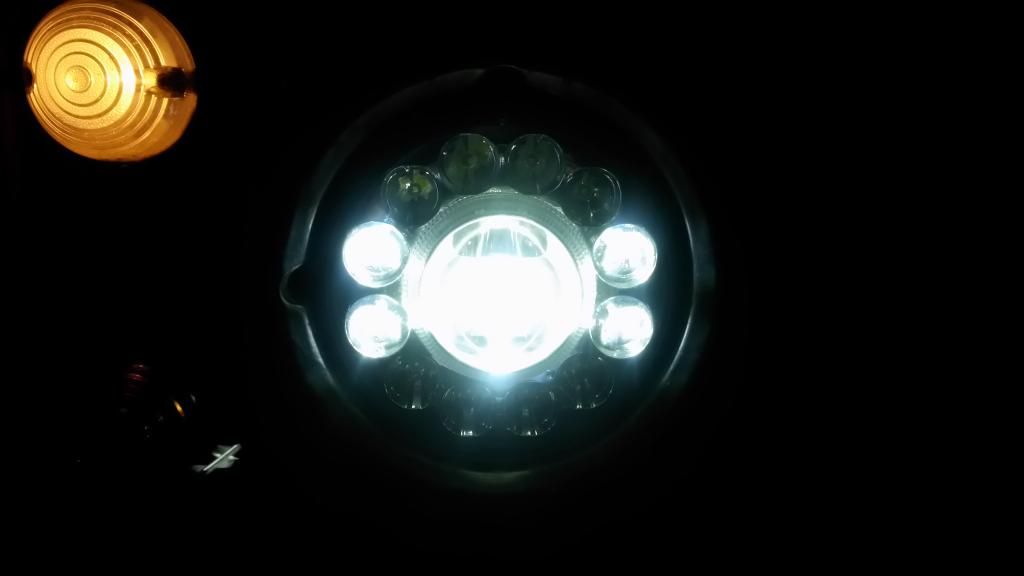
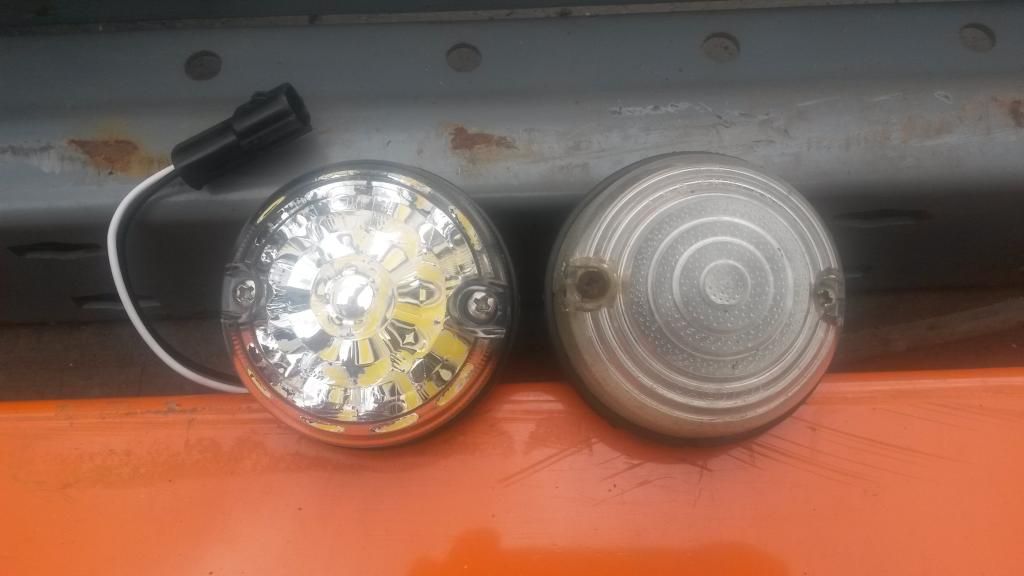
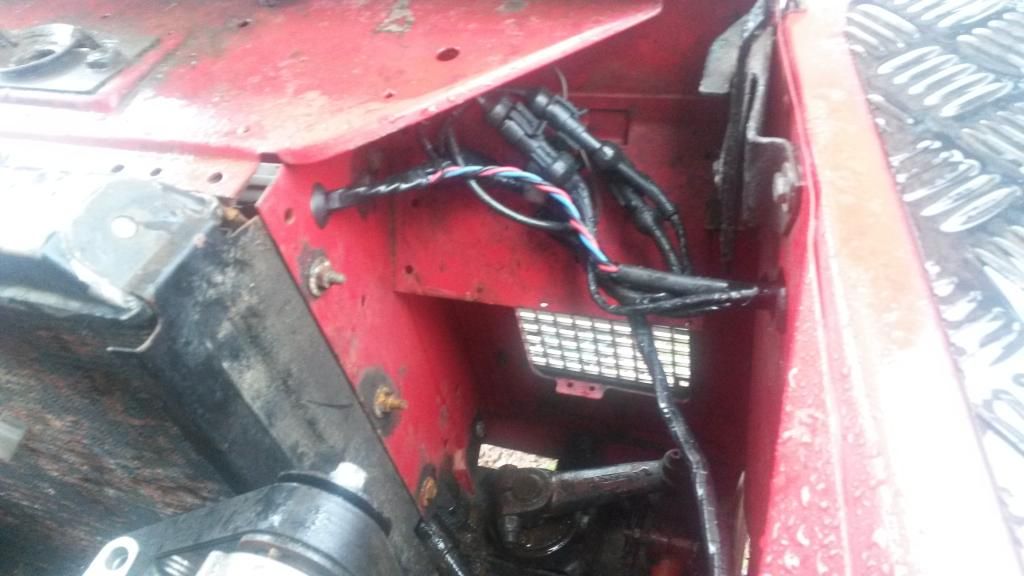
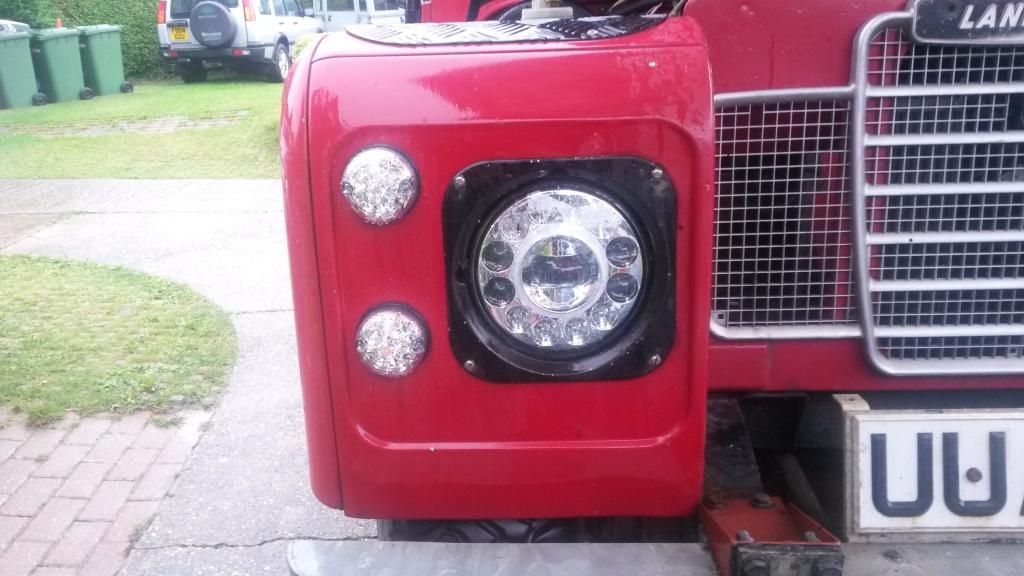
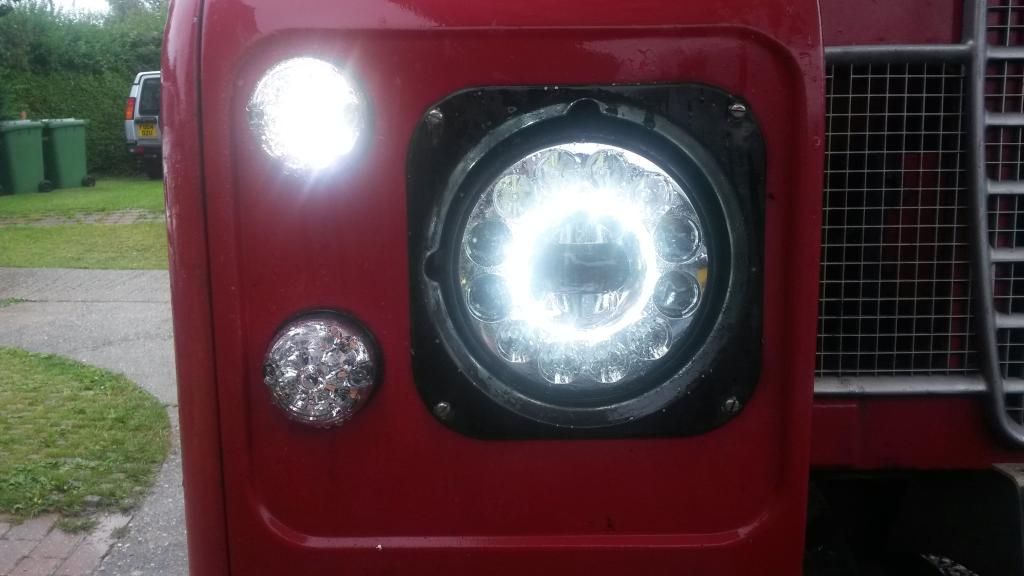
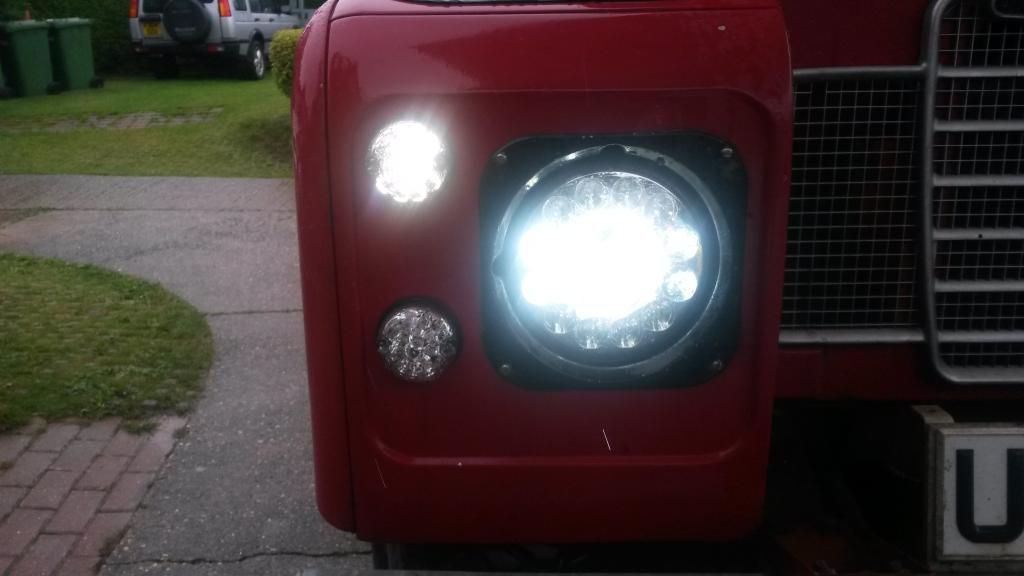

And with the lights being much better and like driving in daylight I decided it was time to de - clutter some of the parts I had fitted that went against the "old Land Rover" look. This included the spotlights as they hadn't worked for two years anyway, began tidying up the wiring around the grill panel and I also removed the washer bottle as I intend to move it inside the cabin along with the heater to make the heating better but also to free up some much needed engine bay space.
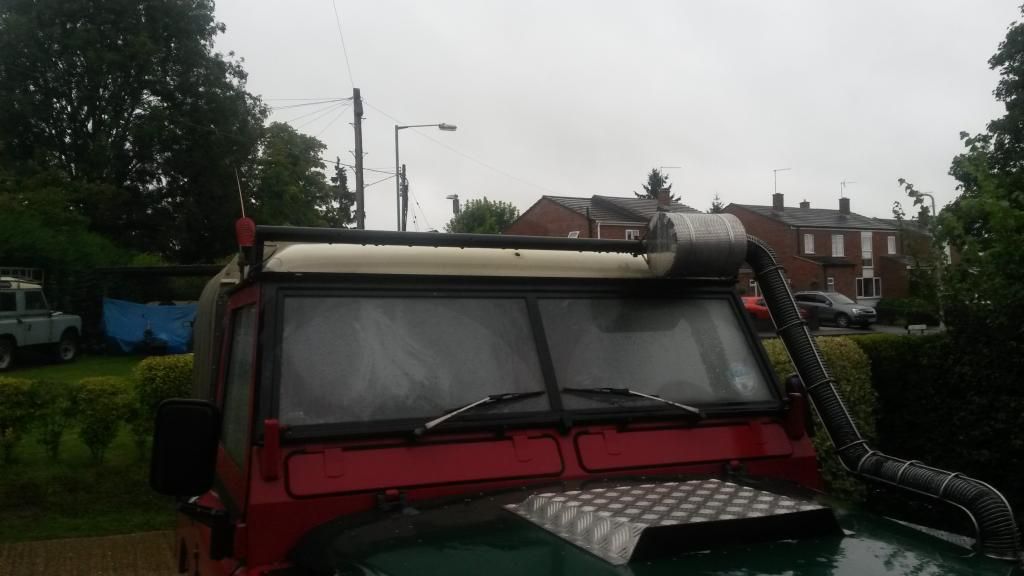
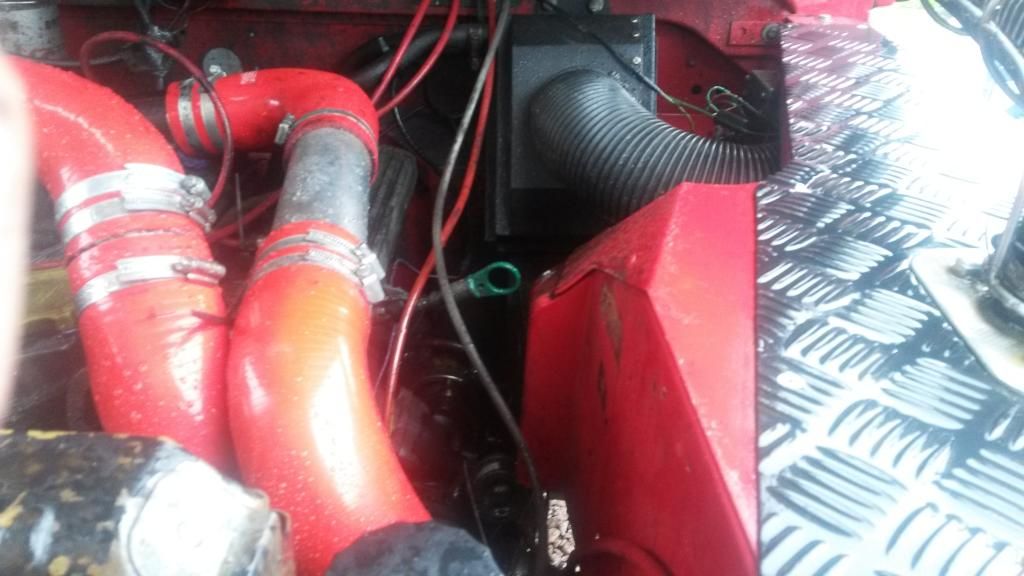
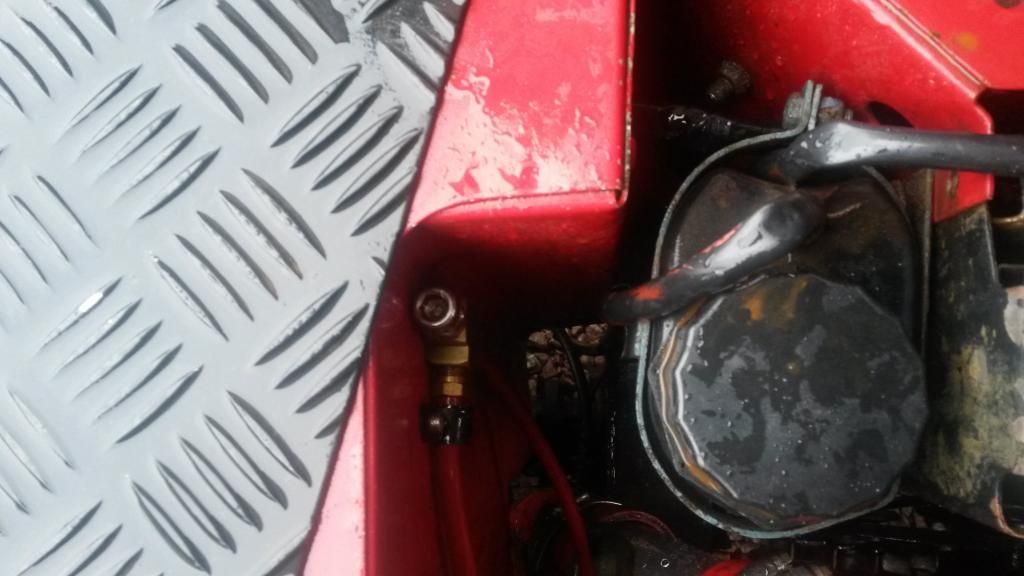
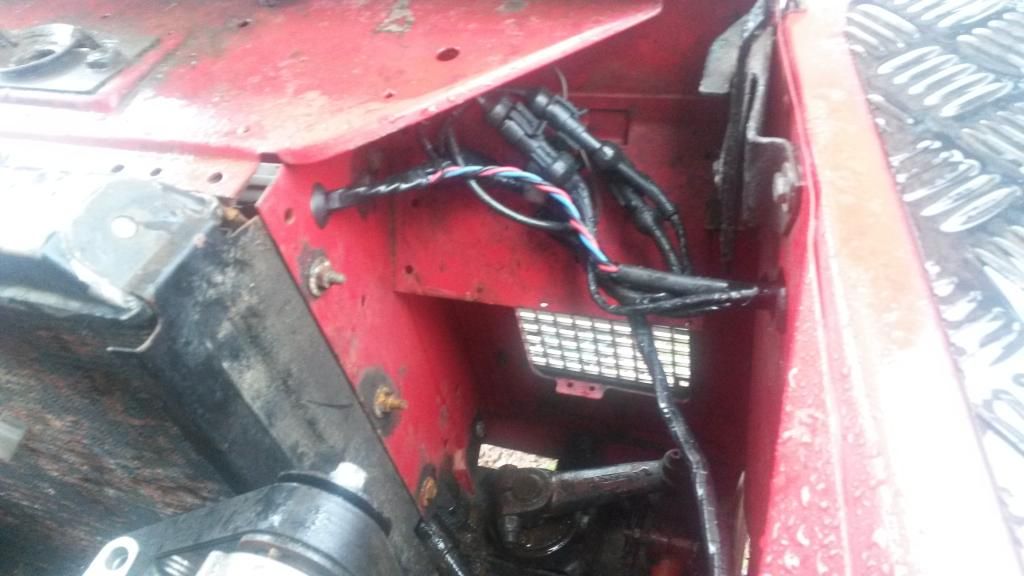

|
|
Last Edit: Sept 2, 2014 22:32:07 GMT by lowen
|
|
lowen
Part of things

Posts: 50
|
|
Sept 2, 2014 22:55:14 GMT
|
Transfer Box Upgrade And RebuildWith the lack of overdrive 50mph is as fast as I've been wanting to go recently, and getting there has been very easy with the current gearing of bigger tyres and 3.54:1 diffs over 4.7:1 diffs - Very rarely have I been using 1st gear as it's just too low now. Ashcroft transmissions sell a gear kit to raise the transfer box high ratio by 32%, with an overdrive somewhere near 28% I think. Repairing my overdrive with new gears, seals was going to be costly and just another part to leak oil on the driveway so I decided that I would try their gear kit then machine it myself to suit these gears, they do convert the cases on an exchange basis however I wanted it doing as soon as possible so used the instructions from their website. Upon dismantling my spare transfer box I found a nice big crack in the casing, so decided that I would finally have a go at TIG welding aluminium. Uptil earlier this year I used to TIG weld stainless at work so had the interest to try aluminium. I cleaned the casing up at work an got it like new again, grooved the crack to give room for new metal to be added into, heated the casing up in the oven, played around with the power settings on the welder and ended up maxed out at 200amps but at this power it welded nicely and could get a good weld pool going before running out of metal to weld to. Then after welding gave it some good taps with a chisel to make sure the weld was attached and not going to fall off and was quite pleased with my first attempt. I'd definitely like to weld some more aluminium parts in the future as I find TIG welding enjoyable and satisfying once you get the setting right and into a good rythmn. I just wanted to make sure the casing wasn't going to peel open and leak oil everywhere. Luckily I also escaped without any distortion issues! 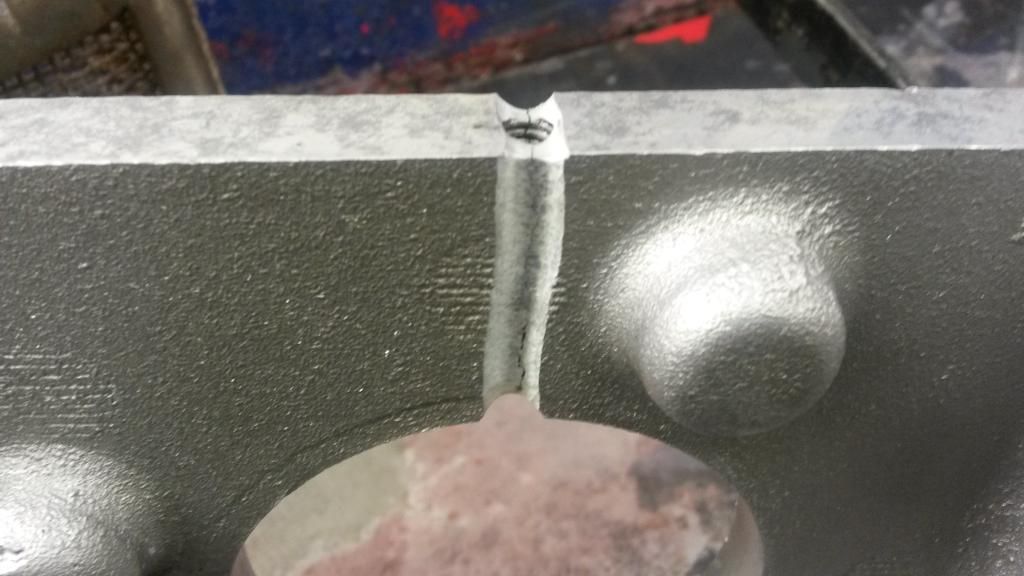 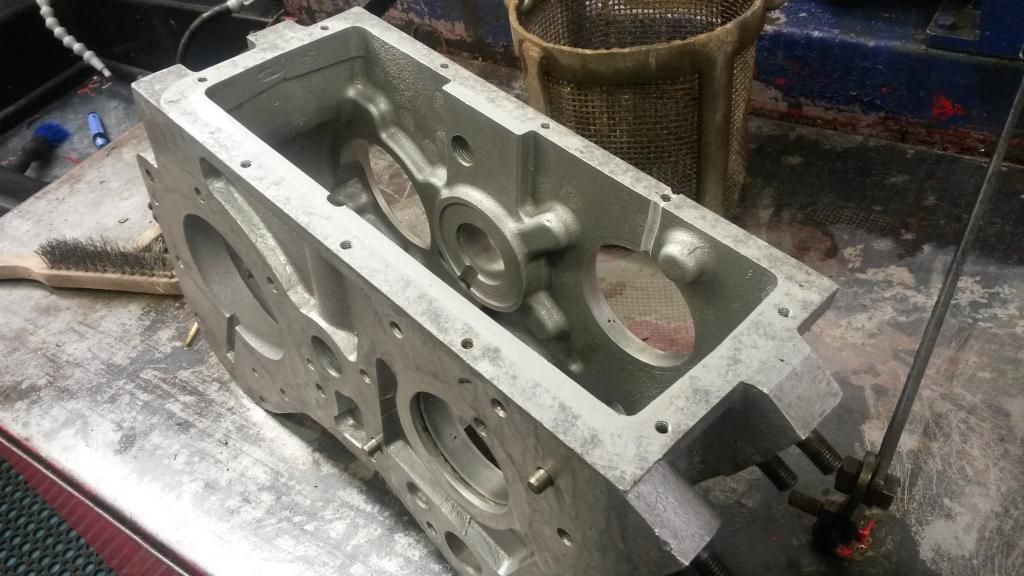 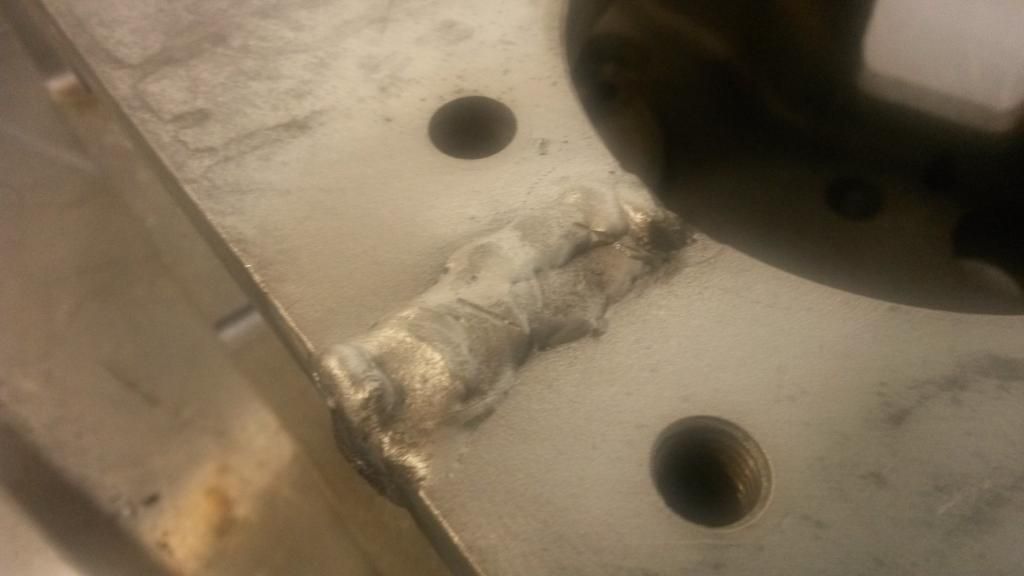 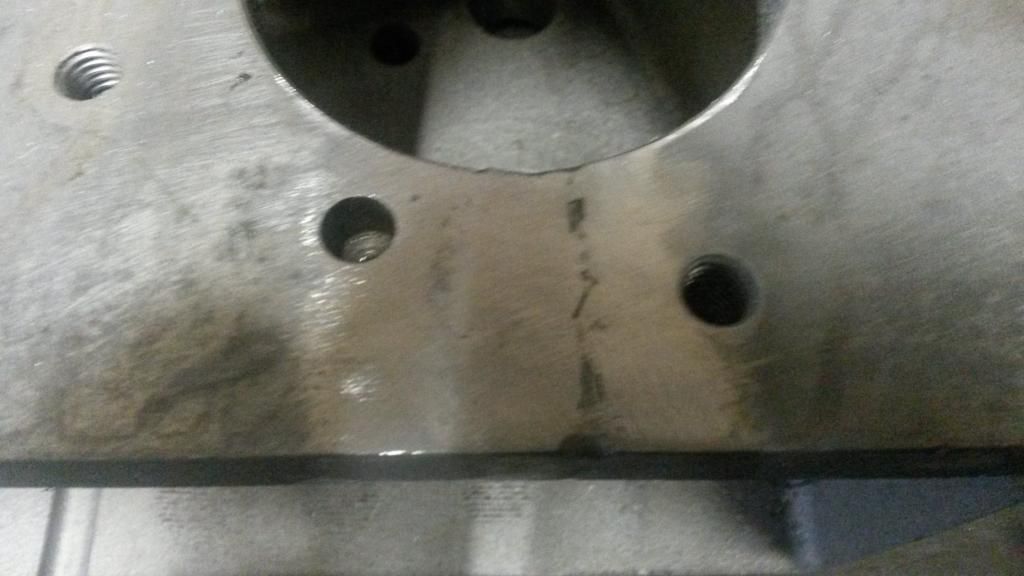 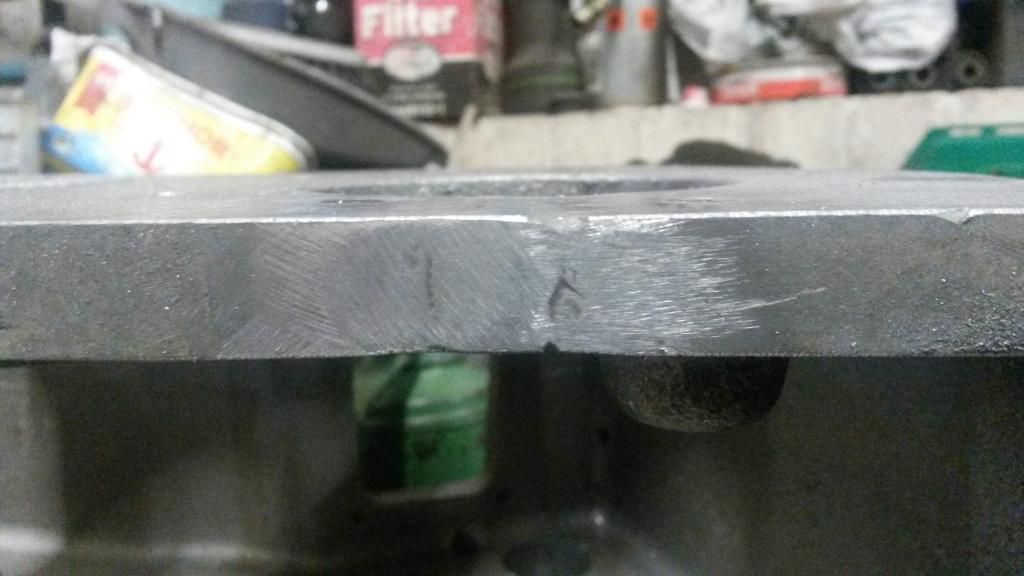 After I got the crack repaired it was time to machine the casing. The intermediate gear pin needed to be moved to compensate for the different gear sizes so also had some practice at machining to close tolerances after working out how to adjust the play out of the machine bed as it's been sat in the same position for many years. Green loctite and a minor interference fit hold these offset bushes into the casing, they work be coming out easily! Plenty of sealant was used upon reassembly along with the gaskets, it's a real motivation killer having to work underneath and come out looking like you've been working in an oil well. I decided to try fitting the new casing just before retrorides gathering and was motivated to get it done so I could make the show but ended up handicapping one finger on one of the shaft shims so had to build the box using one hand whilst keeping the other away from leaking blood all over the clean casing. 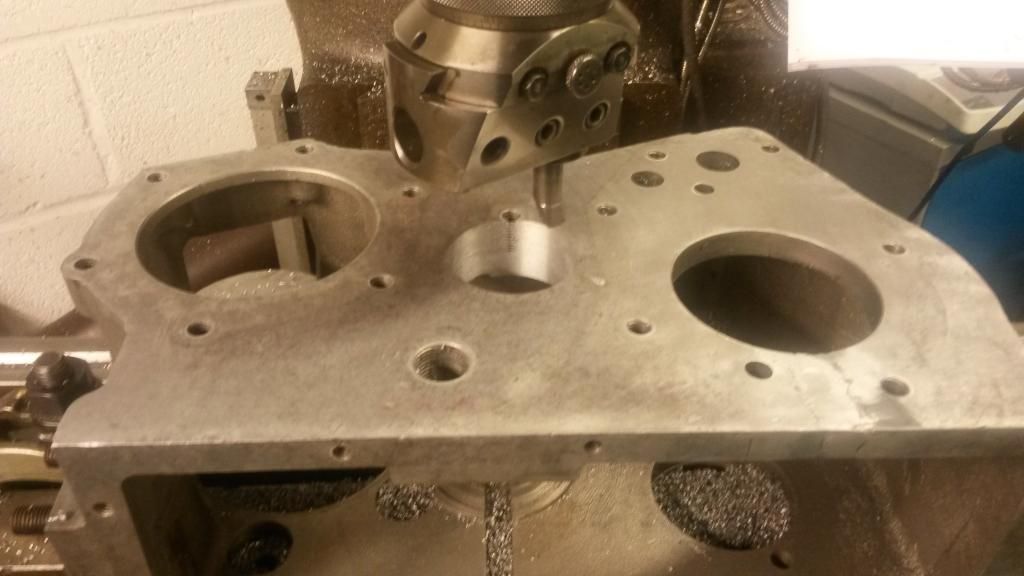 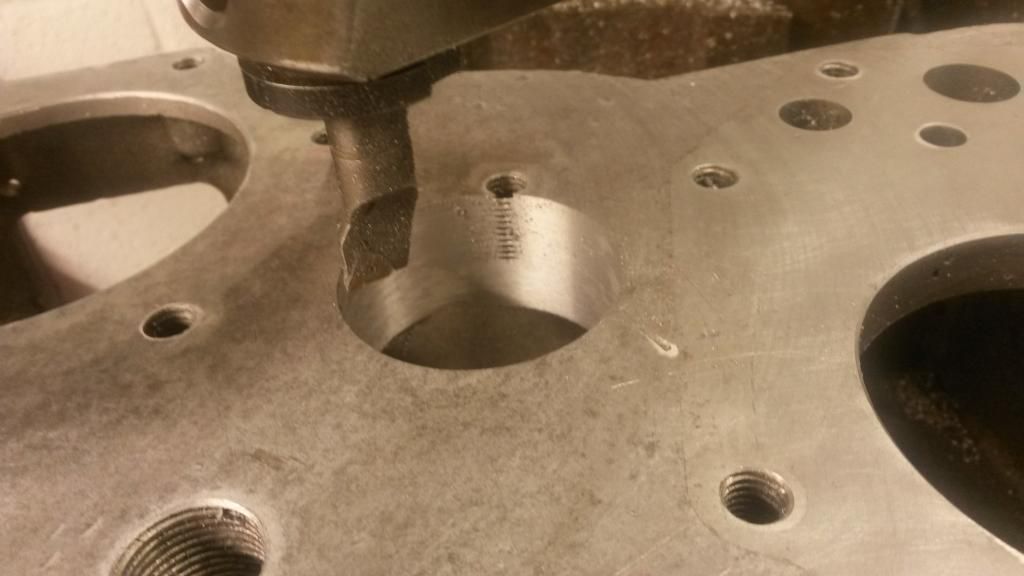 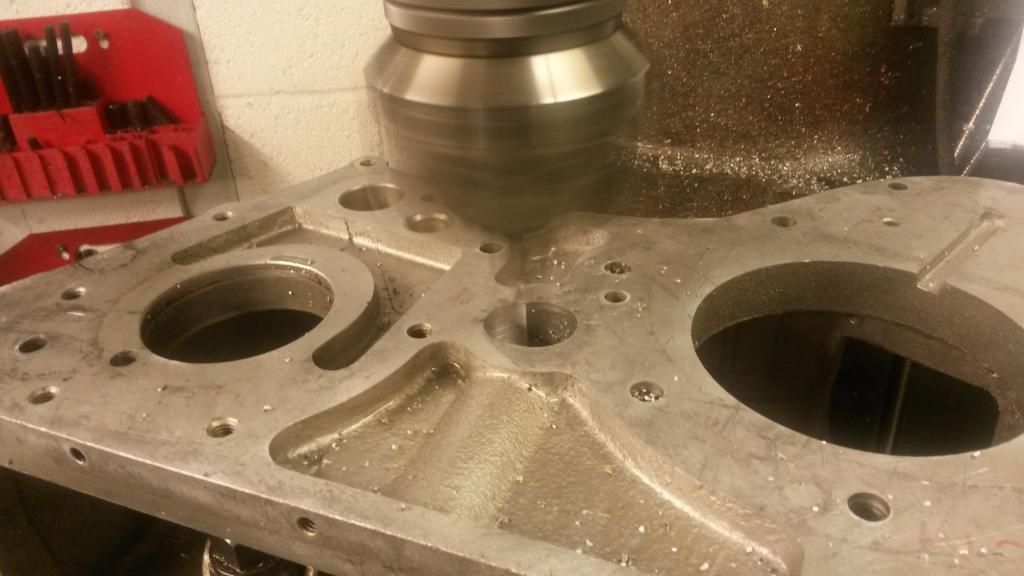 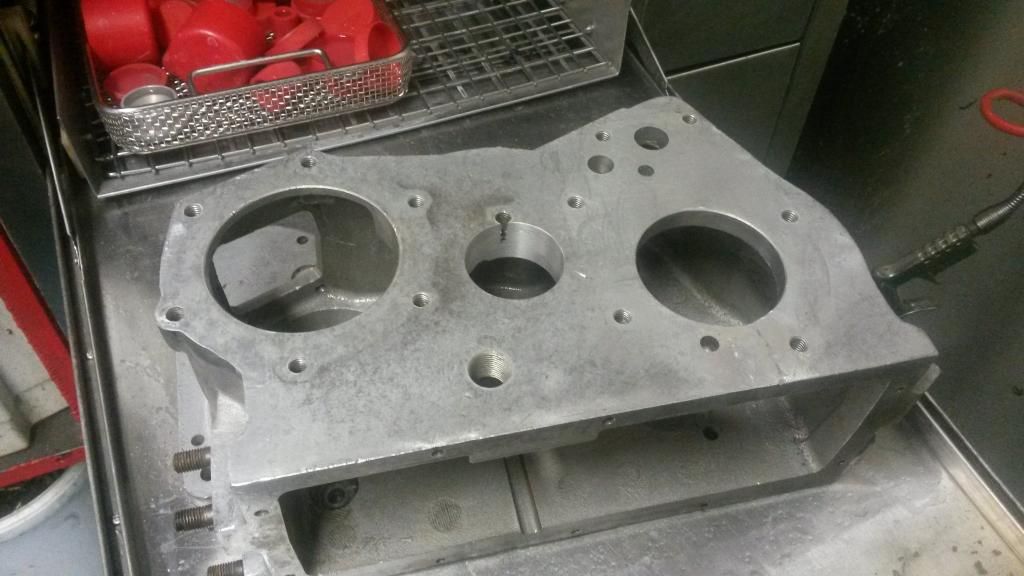 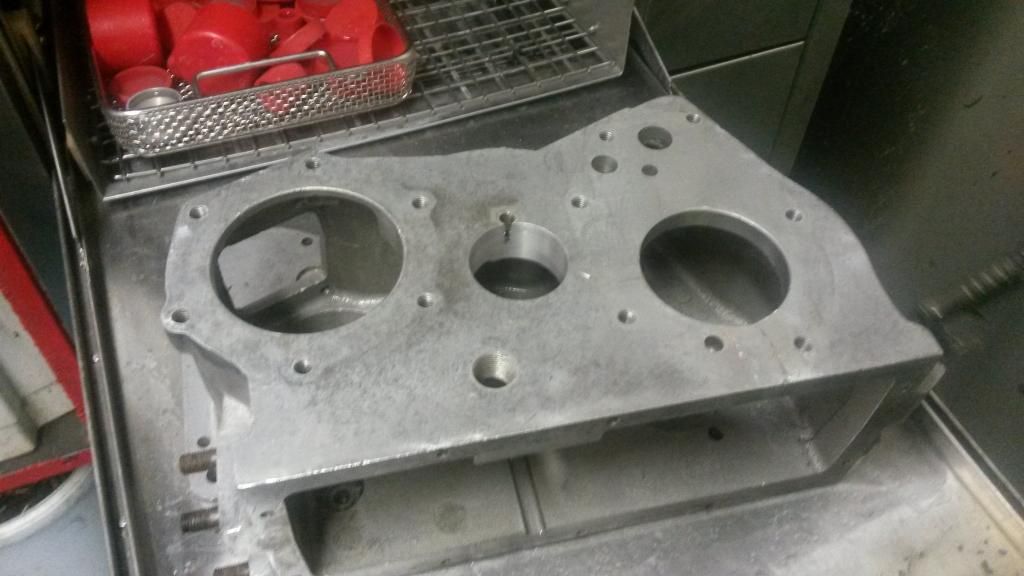 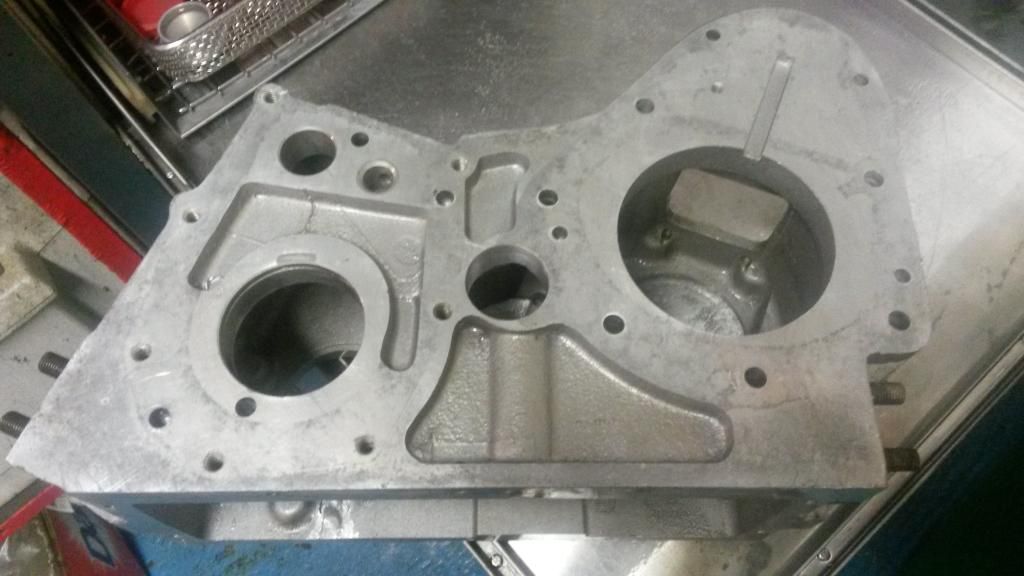 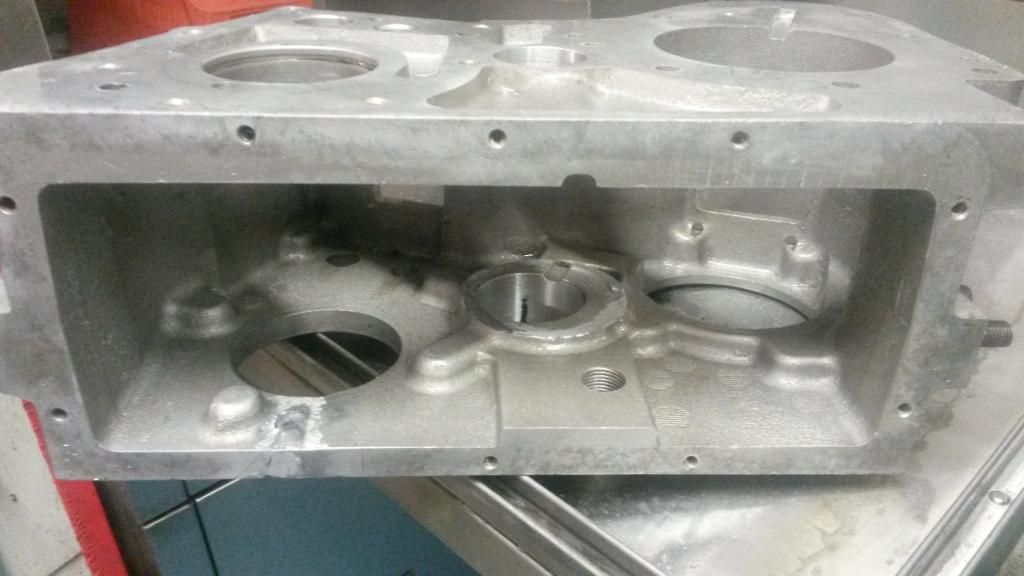 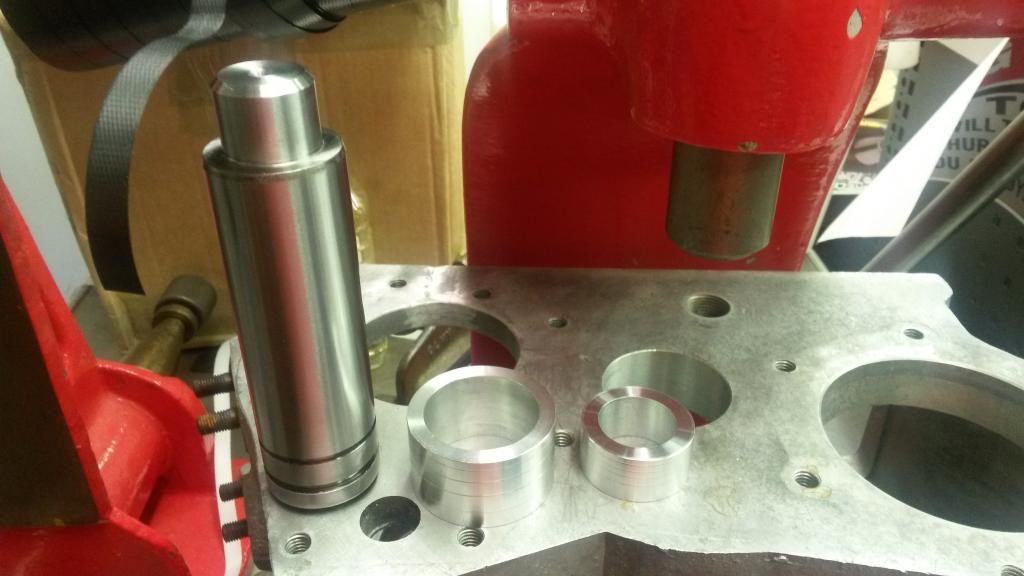 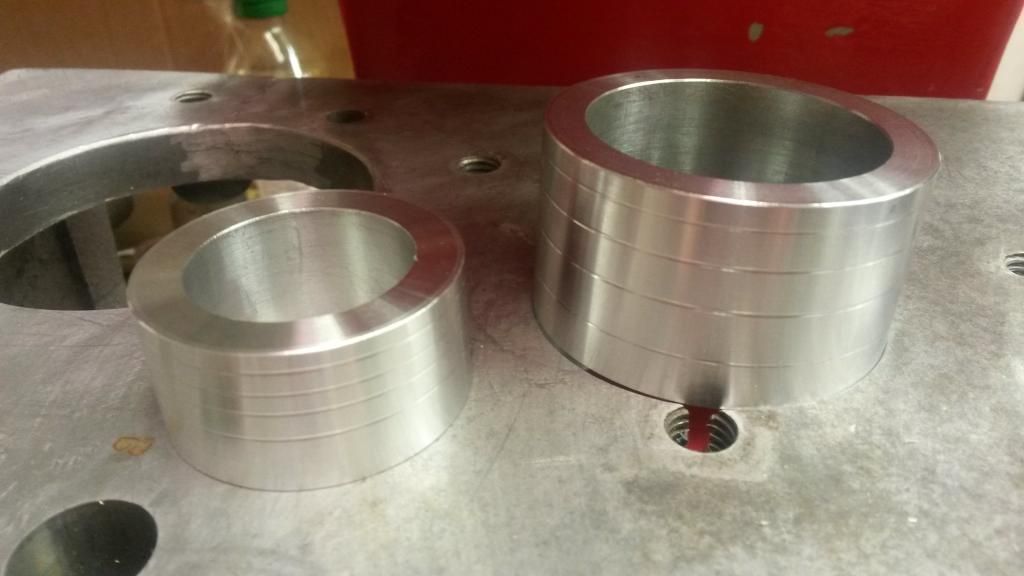 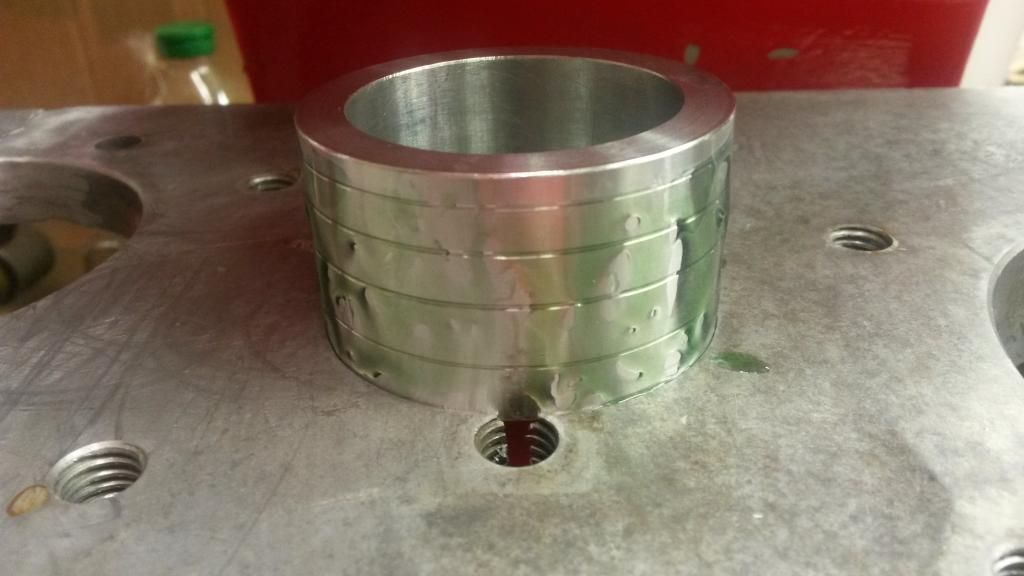 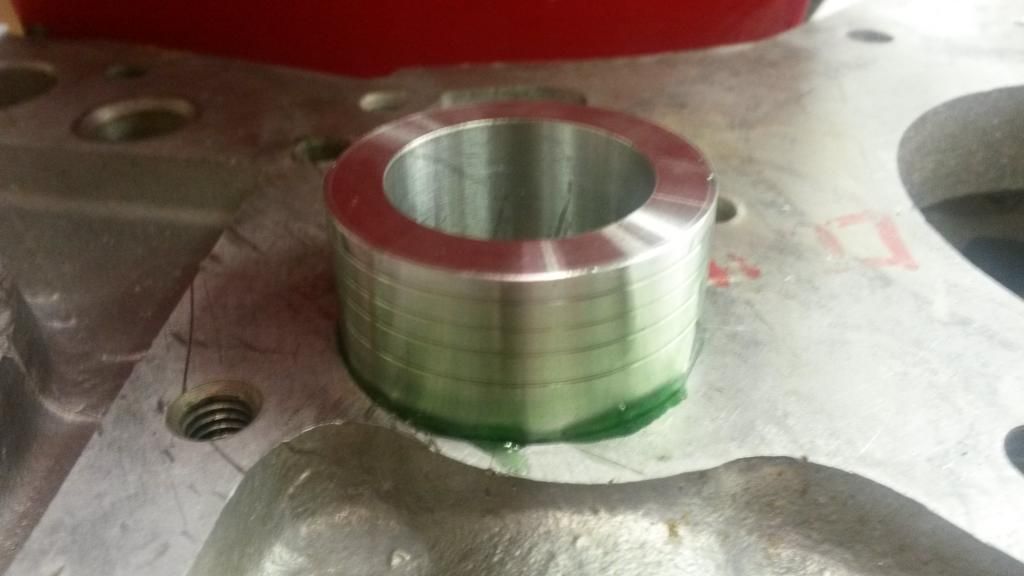 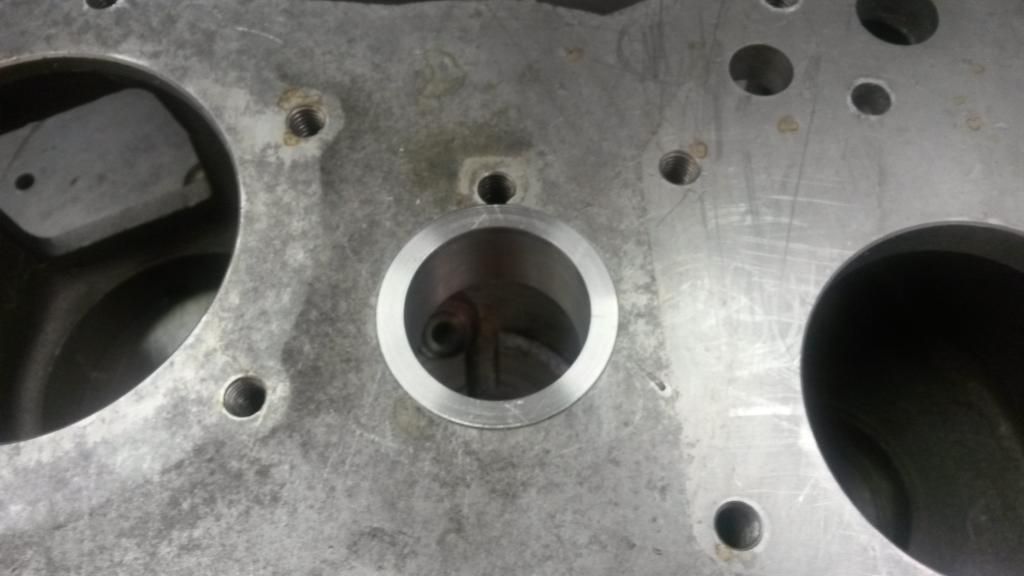 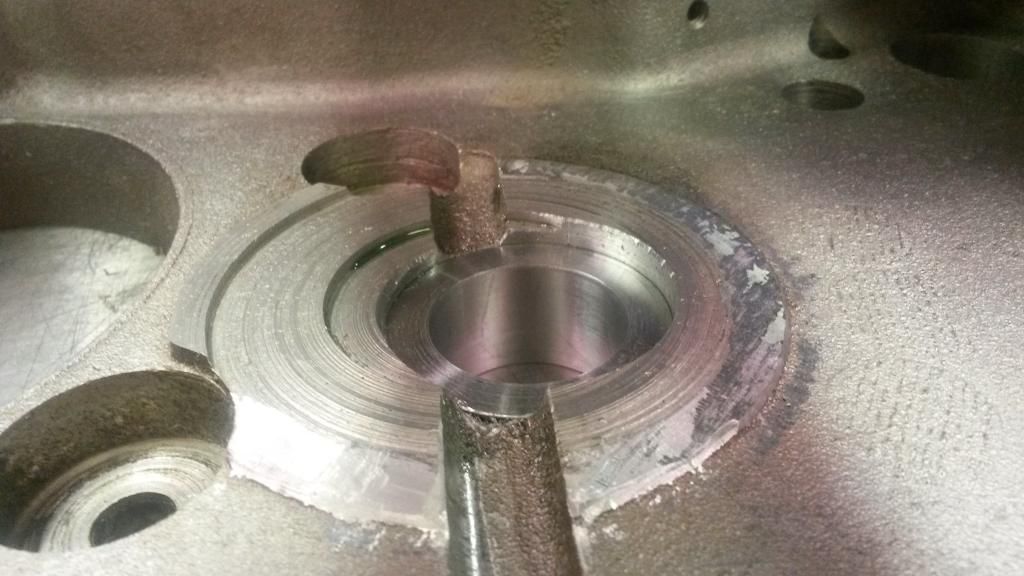  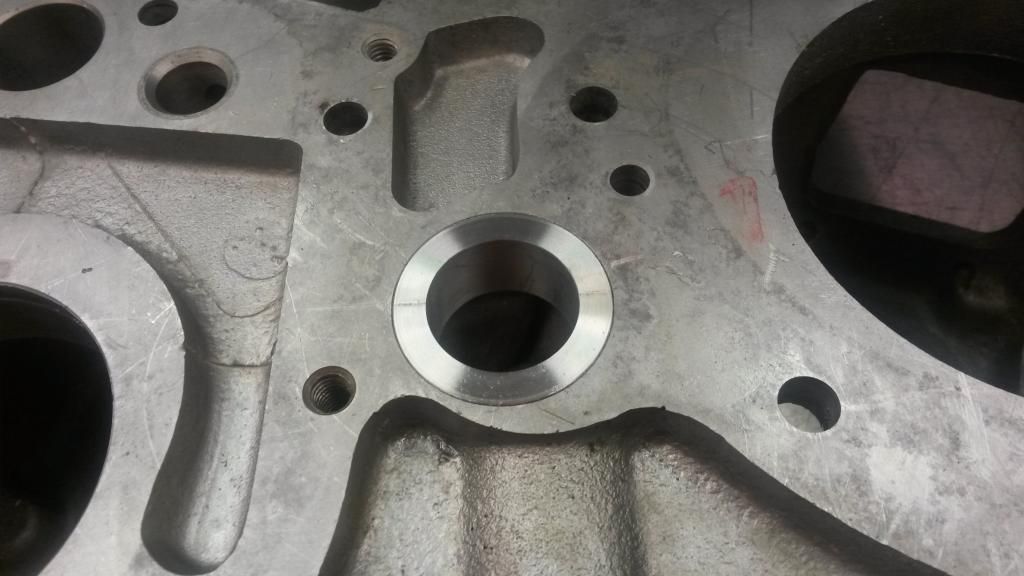 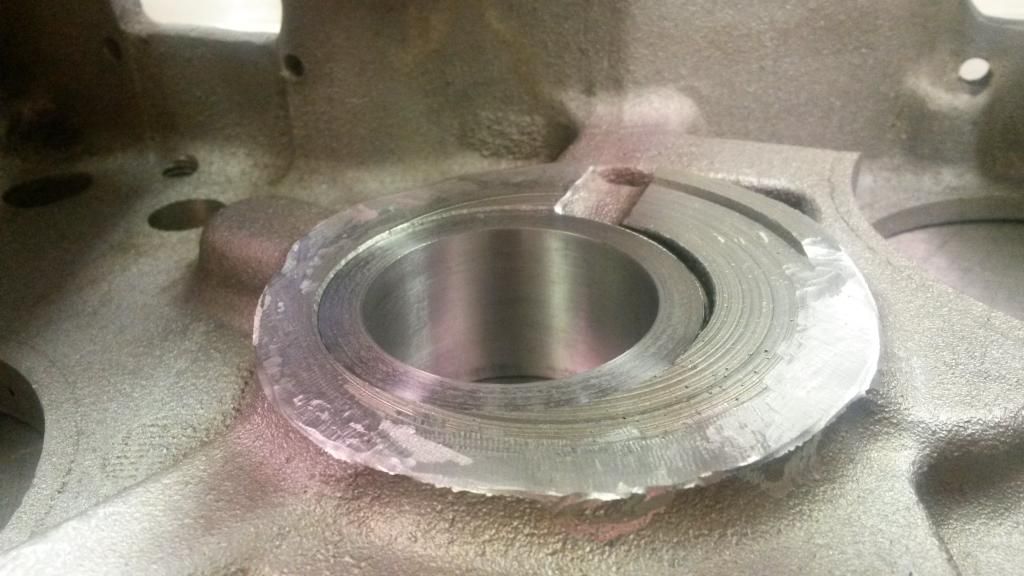 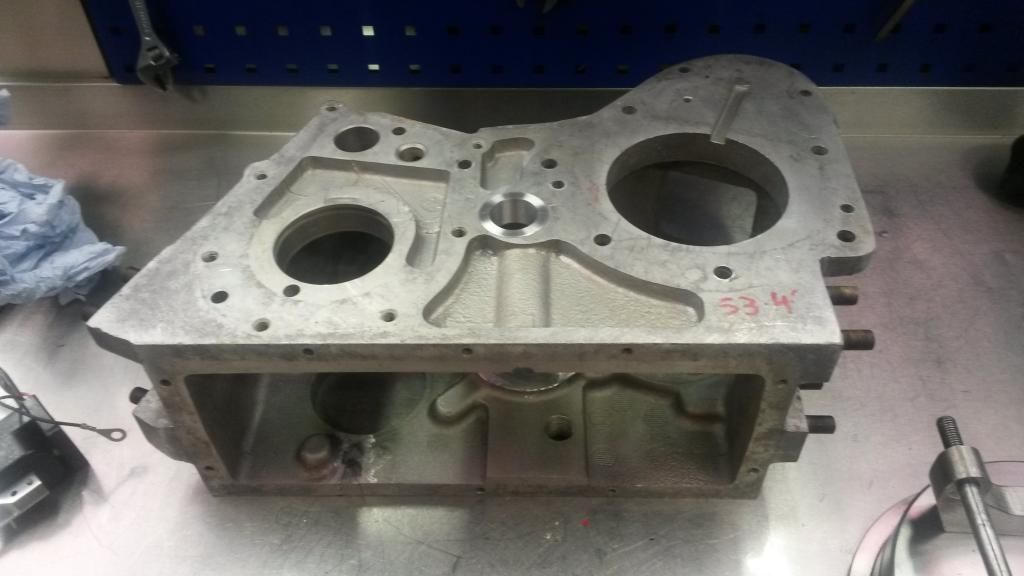 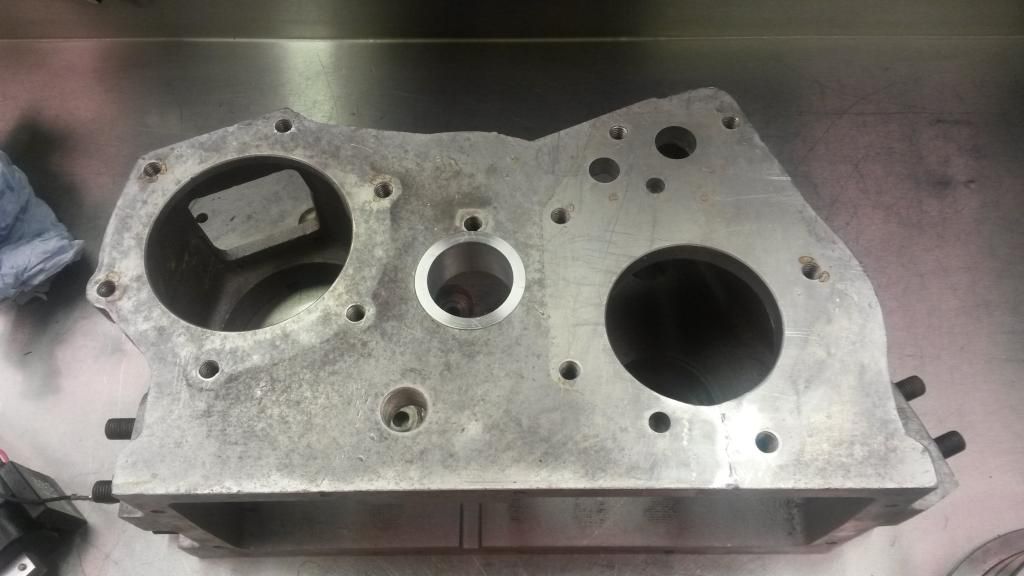 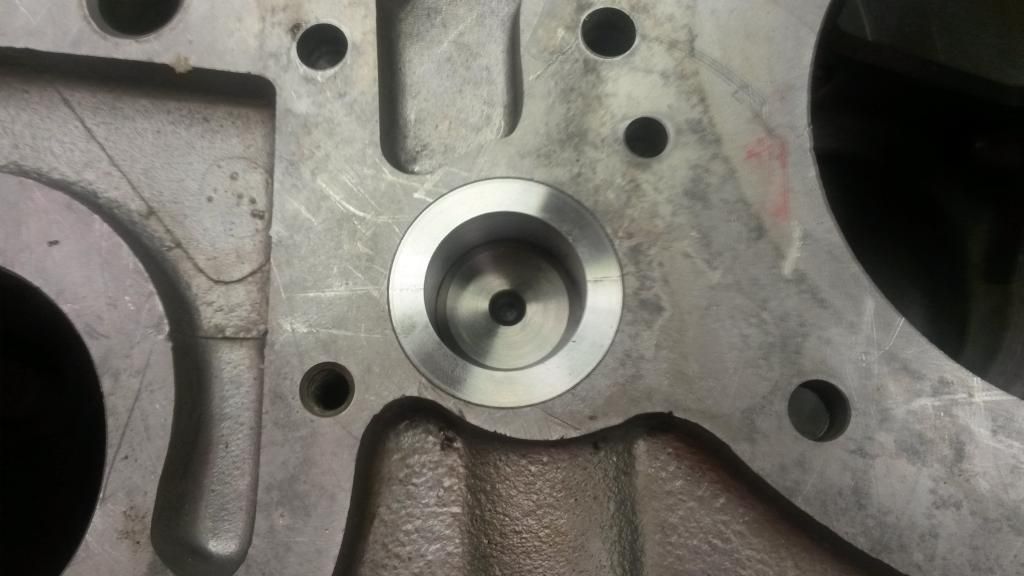 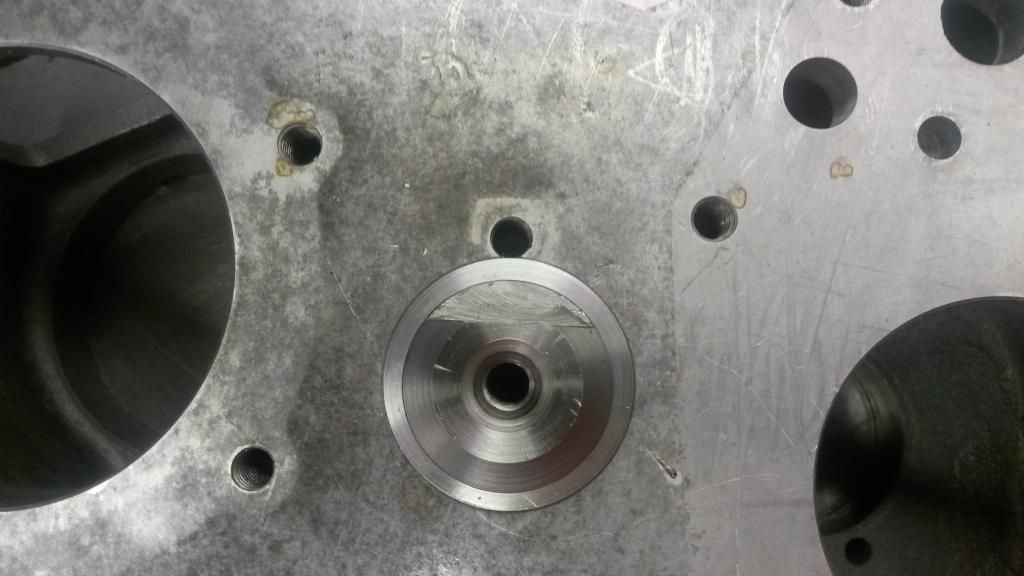 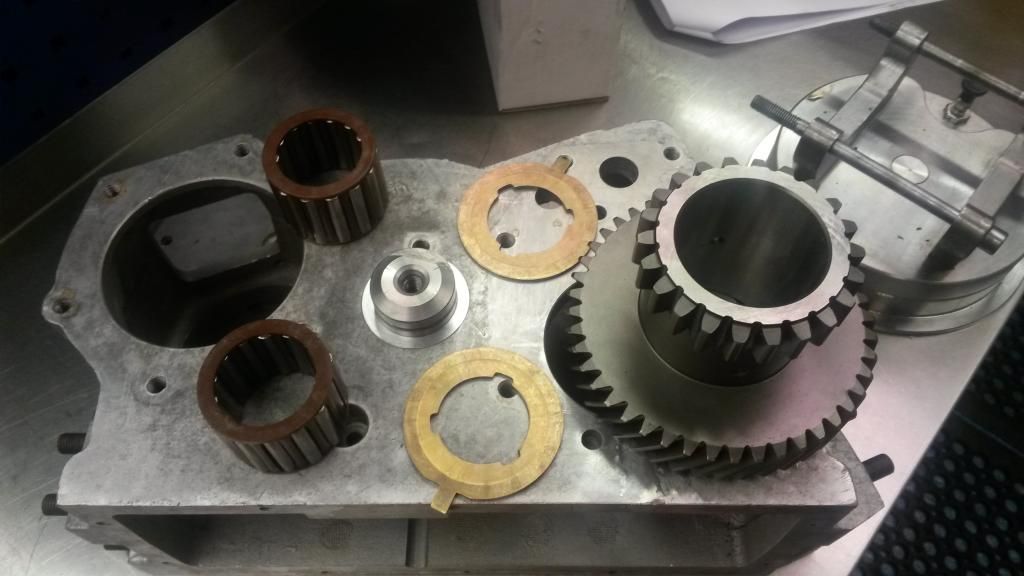 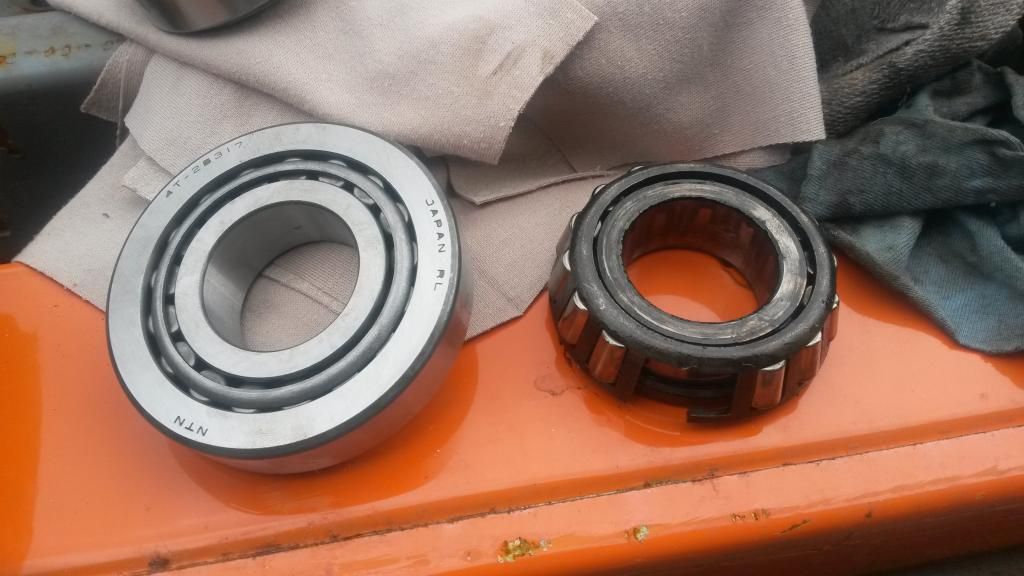 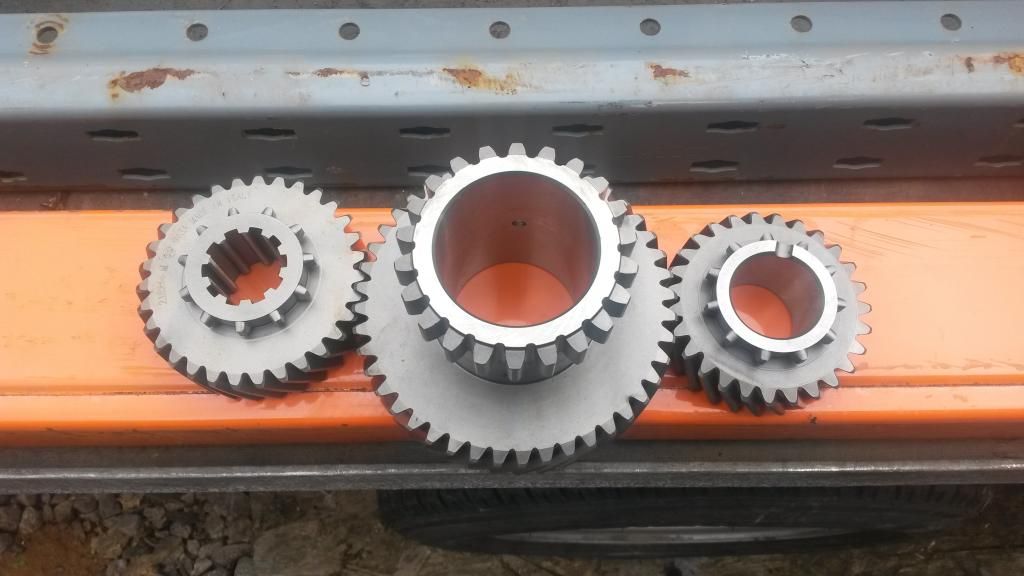 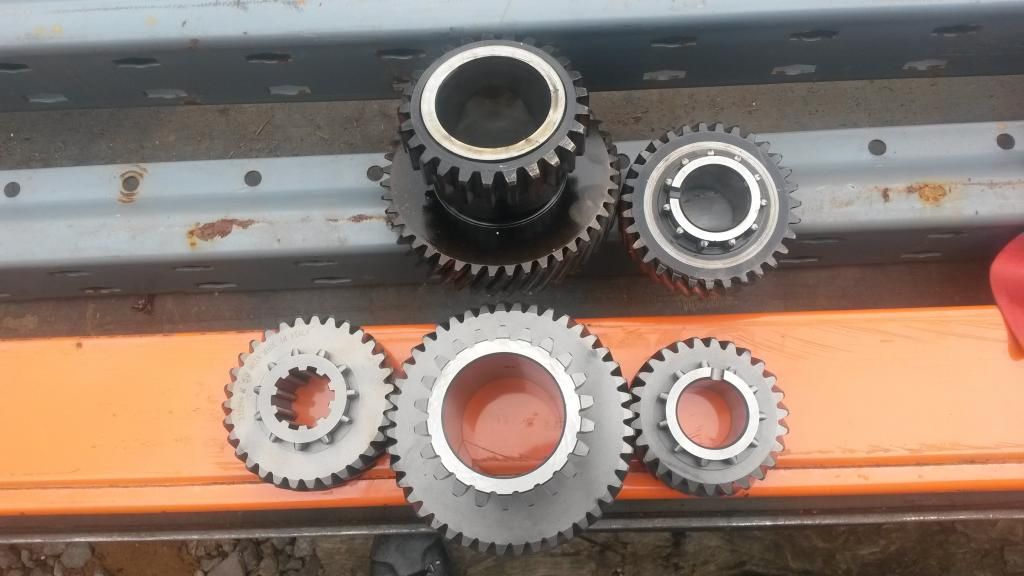 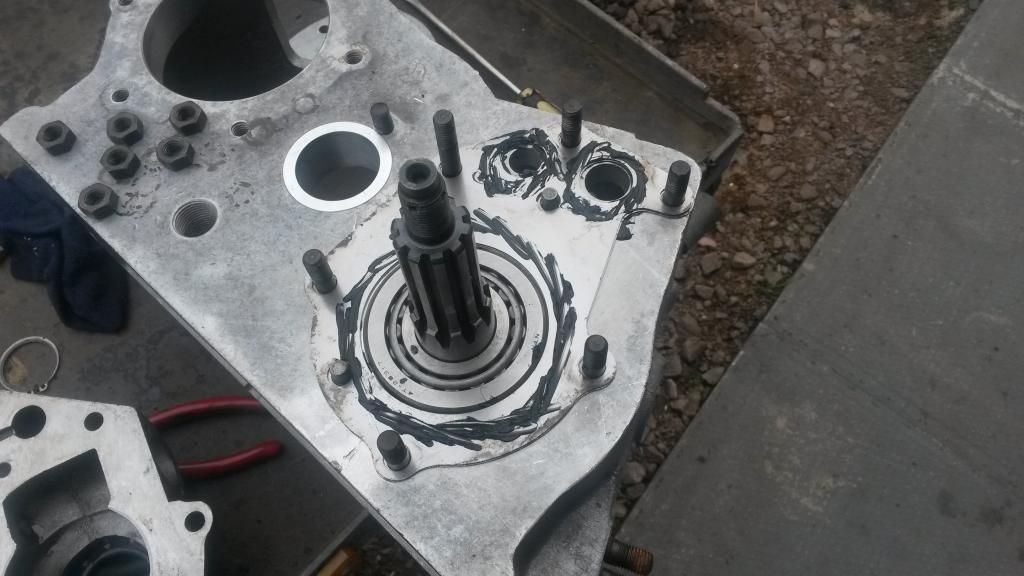  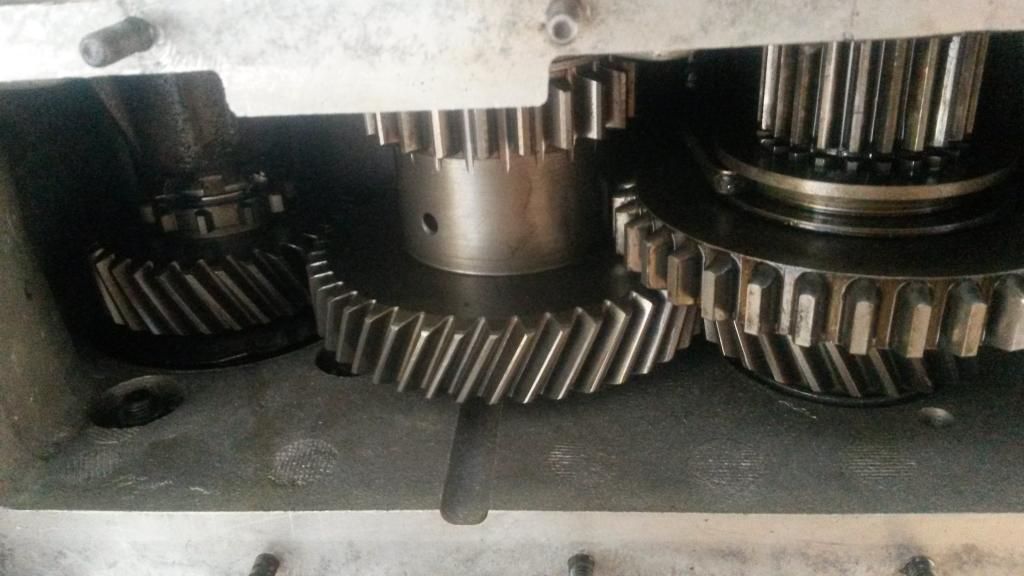 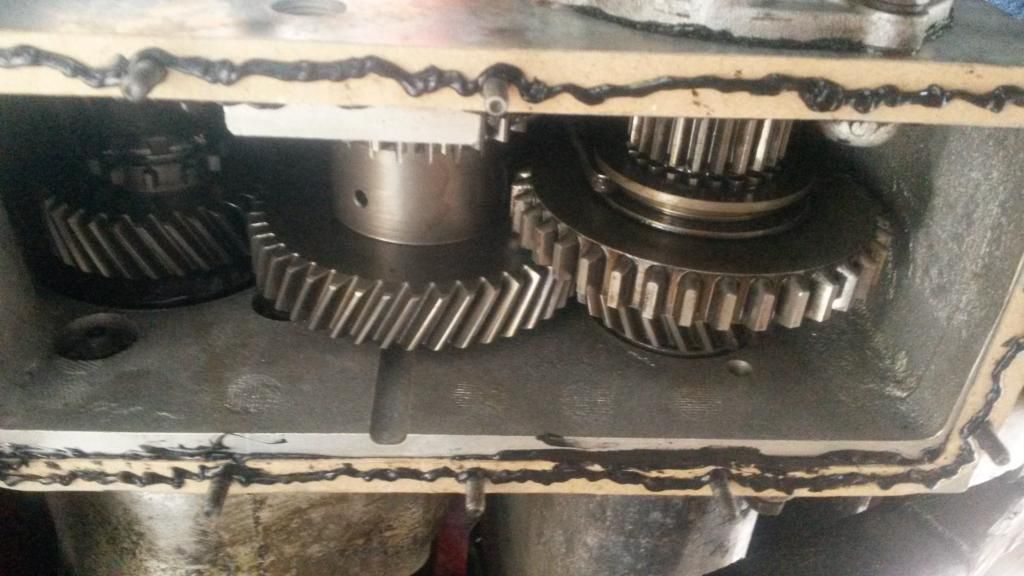
|
|
|
|
|