|
|
Apr 20, 2012 20:00:05 GMT
|
I've got a load of stainless tubing I'm going to make my new exhaust out of, I need to flare a few bits on it to make some fairly tight slip joints. Yes, in an ideal world It'd get welded together, however, I know it's going to get beaten up and dented, so I want it easily removable, plus I can't TIG weld. It's 2" (OD) tubing with 1.5mm walls, I have (had) one of (well, now two of, will explain) these. 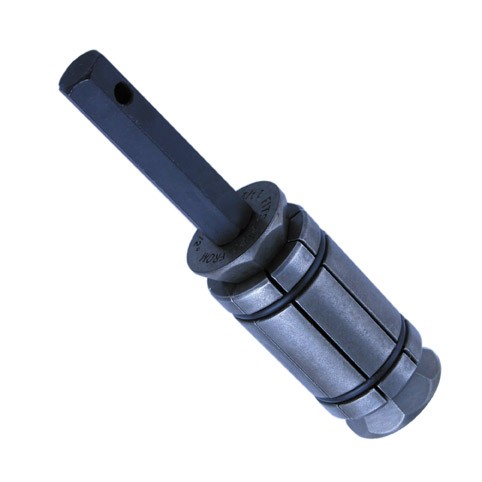 I'd be better of pulling at it with my teeth. First one, I got the down pipe joint perfect, I then went to do the bend (it needs expanding about 2mm, the other tubing will need to be expanded about the same) and it stripped the thread on the top nut. Second one did exactly the same, even after heating the pipe quite substantially. What did I do wrong? Are these things just not man enough for stainless steel? Is there anything else I can use to do this? I'm in the lovely position of being unable to drive right now and stuck in the middle of nowhere, so I can't take it anywhere else to get it done either. Any ideas? Or do I attempt to use a third one of these stupid bloody things. Also, MIJ exhaust boxes with 2" inlets, they're not 2". Annoyed. Cheers.
|
|
|
|
|
|
|
Apr 20, 2012 20:03:45 GMT
|
I understand that they're not really man enough full stop.
At the very least it would be worth cutting a few slots in the pipe so it's not trying to stretch the metal all the way, rather just expanding the gaps.
Beyond that, I don't know what to suggest, other than MIG-welding it up with mild wire. OK, so the weld will eventually rot out, but that's not the end of the world: you hae a welder. ;D
|
|
|
|
|
|
Apr 20, 2012 20:15:02 GMT
|
It started out with two slots, then I cut two more in, then heated it until it started to go blue (which melted the rubber o rings instantly, probably should have considered that first  ) then the tool died. The main problem with welding it is that it's a side exit, this car has sod all ground clearance and it definitely will get battered (I'm still not sure if it'll survive my driveway (1/3 of a mile, gravelly, pot-holey, cambered, bumpy mess). So I want it easily removable to be able to replace bits of it when I need to. Ironic statement. I did it this way because I thought it'd be simpler. Rookie error.
|
|
|
|
|
|
Apr 20, 2012 20:37:33 GMT
|
regarding the welding, just buy some ss wire and a bottle of argon 
|
|
|
|
|
|
Apr 20, 2012 22:24:37 GMT
|
If you didn't already, grease the tool threads and the "wedgy bits" with graphite grease. This will help the tool work better.
May be enough, may not. If it's going to get all dented up and need regular removal anyway, why not use mild steel?
Nick
|
|
1967 Triumph Vitesse convertible (old friend) 1996 Audi A6 2.5 TDI Avant (still durability testing) 1972 GT6 Mk3 (Restored after loong rest & getting the hang of being a car again)
|
|
|
|
Apr 20, 2012 22:33:28 GMT
|
Graphite grease, good plan. Will try that when I get a replacement bolt tomorrow, if it's not still chucking it down at least. Mild steel would have been a better plan really, I only thought about it getting ruined when a friend came to visit after I ordered the tube. His comments of "Your drive is an absolute nightmare in my car!" (lowered 106GTi) reminded me it's going to be problematic. Though I do already have a stainless down pipe and wanted it to match, I'm funny like that.
|
|
|
|
|
|
Apr 20, 2012 22:44:56 GMT
|
these are not man enough for stainless steel.
|
|
theres more to life than mpg & to much power is just enough.
|
|
|
|
Apr 20, 2012 23:38:44 GMT
|
these are not man enough for stainless steel. Damn. Any other ideas? I still don't know anywhere useful within walking/bike distance around here (Old Basing) either, so options are limited. Besides, walking around with 750mm of 2" polished pipe might look a bit weird... Might have to bite the bullet and weld the rest of it then. At least there's only the 60 degree bend to the box (Does anyone other than Jetex make these? Couldn't find them anywhere!) and then from the bend to the pipe... Just better get the cut right first time now... Does mean that all the Mikalor clamps I bought are now not needed though. 
|
|
|
|
RobinJI
Posted a lot
 
"Driven by the irony that only being shackled to the road could ever I be free"
Posts: 2,995
|
|
|
If you really want to keep it separate and you don't mind welding it, then I'd be tempted to cut a couple of inches off the end of the pipe, cut that small section into 3/4 sections, then open out the sections slightly so they'll fit around the end of the pipe overlapped a couple of mm, then weld them on and weld up the first little bit of the slits. That way you'd end up with a sleeve joint still. I'm not sure I've explained that very well, but hopefully you'll understand what I mean.
|
|
Last Edit: Apr 21, 2012 0:11:23 GMT by RobinJI
|
|
|
|
|
I follow what you mean Robin, excellent idea. I need to cut some of it off anyway as, err, I kinda threw it in frustration... A few times. Ok, ten. Will have a play with the welder on that bit and see what happens... I'm still rather annoyed that literally 2-3mm is all that's in the way here. This is the final mechanical obstacle in the way for me and budgetary restraints have kicked back in after my tyre guy pulled the carpet from under me, so I can't afford to order more bits in (anyone else know where you can get 4 fairly decent tyres fitted for £100? I don't anymore) I really would love to keep it separate if possible. I'm still not entirely convinced the noise it'll make will be nice. So I'd like to make it fairly easy to stick another box in, or replace the first one with something a bit bigger. Cheers.
|
|
|
|
|
|
Apr 21, 2012 12:54:41 GMT
|
whilst it wont expand it, your easiest way to join would be to use stainless rjt unions (google them!) and weld one part to each bit of pipe. That way you can undo and remove any time you liked
we use them all the time when making up pipework, don't know about exhaust temps but the viton seals we use handle 210 degree c fryer oil with no problems...
|
|
|
|
|
|
Apr 21, 2012 15:59:44 GMT
|
Managed to blag myself a lift down to my uncles workshop, so it'll be getting tigged together. Sod it. It better sound nice! Thanks guys.
|
|
|
|