col
Part of things

wut
Posts: 190
|
|
|
well i've got this stainless steel gear knob, i was told its out of an old jag or something. 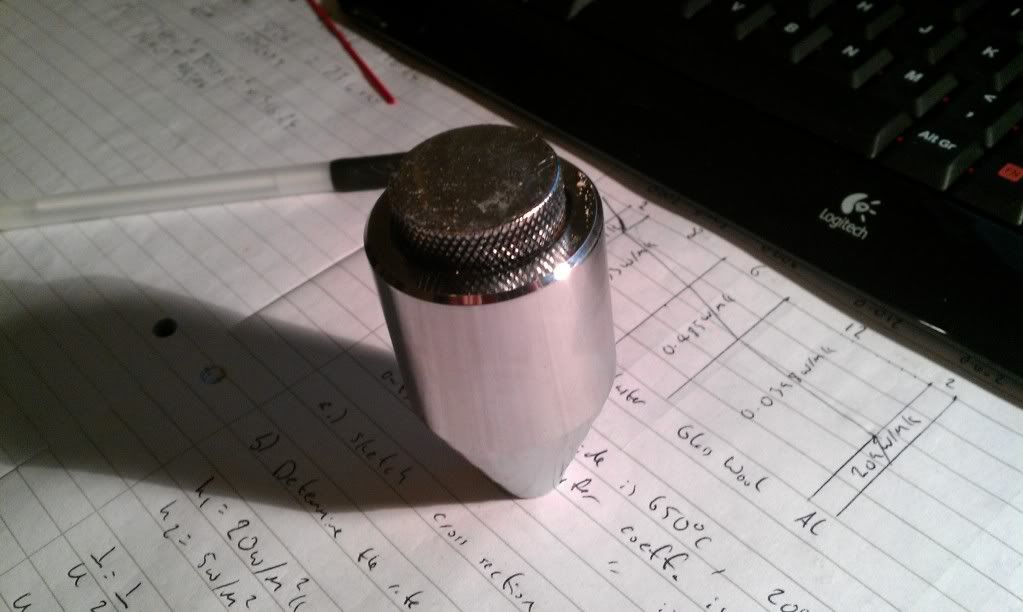 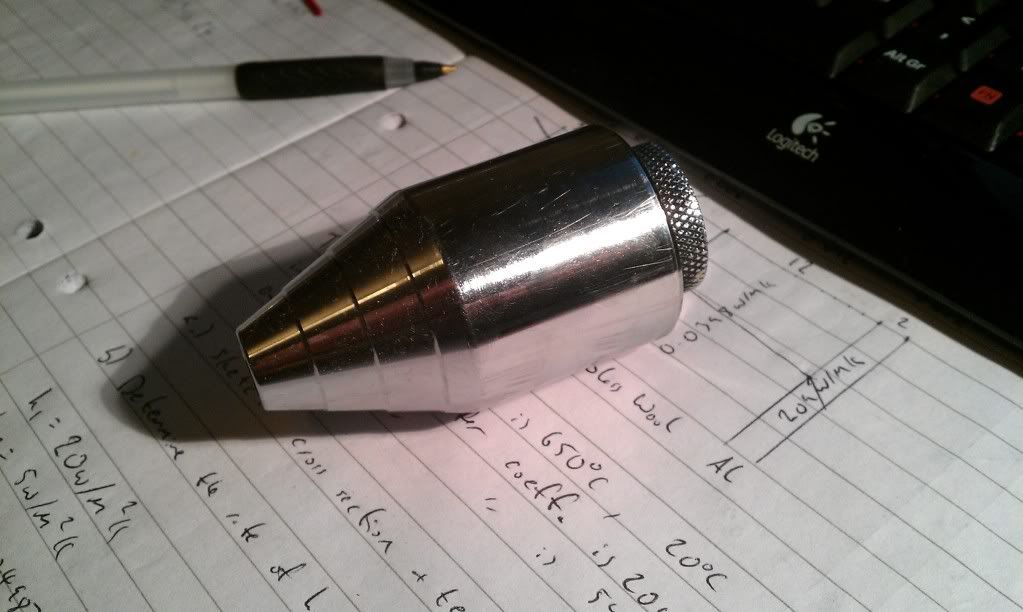 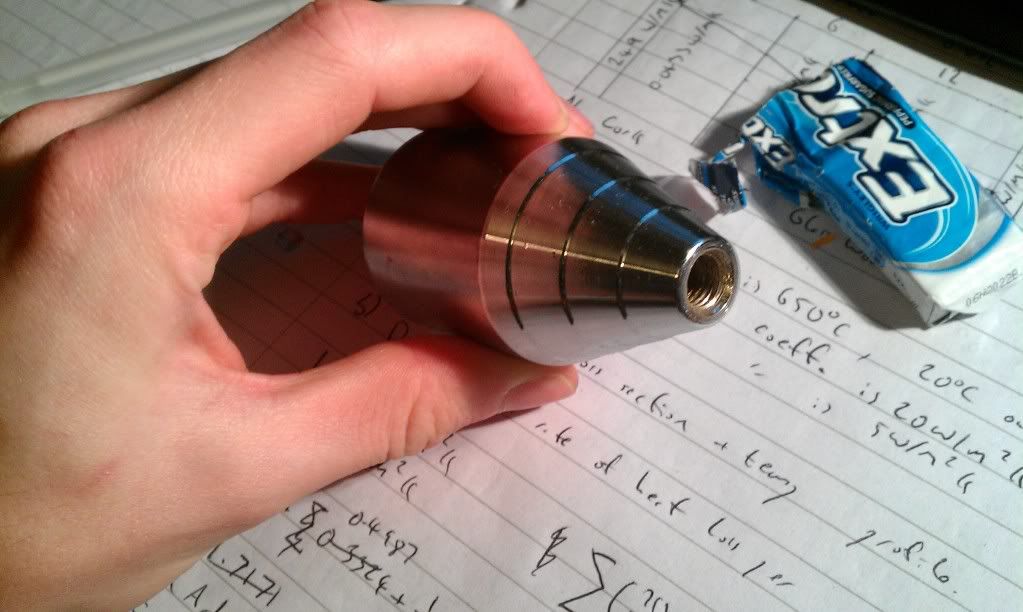 its a nice weighty lump. but the problem is that the hole is too small for the (vw) gear stick. so i need it boring out a few mil. the hole doesn't need to be tapped or really that accurate, i can just use a plastic thread insert for that. is there any easy way i would be able to bore the hole out, or is my only hope to take it to a machine shop / someone with a beefy lathe or drill press? cheers lads.
|
|
|
|
|
Copey
Posted a lot
 
Posts: 2,845
|
|
|
get it in a vice and take a drill with a decent drill bit to it
|
|
1990 Ford Sierra Sapphire GLSi with 2.0 Zetec 1985 Ford Capri 3.0 (was a 2.0 Laser originally)
|
|
|
|
|
You'll need a sharp HSS drill bit, a variable-speed drill so you can run it slowly, plenty of lube, and enough pressure so the bit cuts without slipping on the surface. If it slips, you run the risk of work-hardening it, making it much more difficult to drill and blunting the bit quickly. Do-able with a hand-held electric drill, but far easier in a drill press - and I doubt a machine shop would charge more than £5-£10 for drilling one hole. www.bssa.org.uk/topics.php?article=194
|
|
Last Edit: Mar 8, 2012 1:06:15 GMT by jrevillug
|
|
rodney
Posted a lot
 
https://www.facebook.com/RD-vehicle-transport-and-recovery-services-525622614268010/
Posts: 1,677
|
|
|
as copey said get it clamped up somehow, if it deffinetely is stainless then get some decent drill bits, some grease or oil to keep it cool and lubed and drill it as slow as you can, don't push to hard as stainless is tough and will blunt the drill bit easy soon as it gets hot, as stainless holds the heat longer than mild if remember right from my sheet metal days,.
|
|
facebook: rodney dean / rd transport 
|
|
MrSpeedy
East Midlands
www.vintagediesels.co.uk
Posts: 4,791
|
|
|
All Nimonic steels are difficult to machine. You MUST keep it cool and well lubricated. Use only GOOD quality tooling. Run at a slow speed and keep sufficient weight on the tool to cut, without over ffeding and causing it to 'grab' If you let it 'rub' without cutting and/or get hot, it will work harden!
|
|
|
|
|
|
|
if you were nearer i'd do it at work for you in the lathe. Have you got a local college who teach engineering? If you went in there and had a word with either the tutor or one of the lads in the machine shop theres no way you would be charged any more than a fiver, and you should get it tapped at that price as well.
|
|
|
|
scruff
Part of things

Posts: 621
|
|
|
What they all said but it looks a bit brassy in the threads, you sure it's not chromed brass?
I'd start with a drill big enough to take out the threads only, ie if it's an M8 thread a 8mm drill then a 9mm drill and so on. That will minimise the amount of material you are attempting to remove.
If it's brass then no lube. It'll chatter, squeal & grab like a b'stid but it'll cut in no time at all. Stainless as above, is the opposite of what you would think, heavy pressure, slow speed, loads of lube.
If it fails to cut FFS stop. If it work hardens it'll have to be ground out with something as worked hardend stainless is harder than Chuck Norris on a bad day.
|
|
1994 Lotus Esprit - Fragile red turbo with pop up lights. 1980 Porsche 924 - Fragile red turbo with pop up lights.
I spy a trend...
|
|
col
Part of things

wut
Posts: 190
|
|
|
cheers guys, i'll double check that its stainless when i get home, pretty sure it is though, i think its just a trick of the light that it looks a bit brassy. ive had trouble with stainless before and i'll make sure to heed all of your warnings, a while back i had to drill a hold in my bulkhead reinforcing plate to put a choke cable through.... i assumed it was ally, so just started drilling as normal. bad idea, about 5 drill bits after and lots of swearing, i eventually got through, i've learn my lesson.
I don't know why i didnt think of it, but i'm actually studying at sunderland uni so i can easily take it over to the machine shop and see what they have to say. i'll be around there tomorrow, so i'll bring it along. The gearstick is m12x1.5, so i'll make sure to bore it bigger than that.
|
|
|
|
scruff
Part of things

Posts: 621
|
|
|
If you can get into the machine shop go in with a problem not a solution. Workshop staff like to solve problems not do jobs: they will have it tapped in a few mins. Just go in stupid: Can you make this fit my gearstick please? I measured it at m12x1.5.... 4 tins of lager/bitter works too... I have managed several machine shops, a problem is always far more interesting that just another task 
|
|
1994 Lotus Esprit - Fragile red turbo with pop up lights. 1980 Porsche 924 - Fragile red turbo with pop up lights.
I spy a trend...
|
|
barty
Posted a lot
 
Posts: 1,088
|
|
Mar 10, 2012 17:24:43 GMT
|
it may be the wrong way round but why not just rethreat the gear lever, its a softer metal ? you could prob reduce the diameter with a file if you carefull and then run a new thread on it. If you have the taps and dies it would cost nothing just your time and you can do it in situ
|
|
|
|
10mpg
Club Retro Rides Member
Posts: 4,253
Club RR Member Number: 204
|
|
|
^^^ lateral thinking right there!
|
|
The Internet, like all tools, if used improperly, can make a complete bo**cks of even the simplest jobs...
|
|