|
|
|
Mel is absolutely right, that is exactly what I meant, the size of your flange looks okay, it is just the the bend that needs to be tighter
If you post some photos of the area that you are trying to repair I can see if what you are trying to to is possible
Tony
|
|
Last Edit: Jul 13, 2010 5:41:08 GMT by tonybmw
|
|
|
|
|
|
Thanks Mel and Tony, I should have posted this first time around to give you half a chance. General view drivers side  Area for the new piece, the black lines are not relevant to this particular repair.  Repair piece that needs fettling. 
|
|
|
|
|
|
Jul 13, 2010 19:19:20 GMT
|
Andy
You definitely have the right idea re the repair panel, thats exactly how I would have approached it too.
All I can suggest is that you try my 3 points as previously mentioned, and just keep practising, the only other thing I can suggest is to make sure that you are hammering it against something really nice and solid, to make sure that your hammer blows are having the best affect
Tony
|
|
|
|
|
|
Jul 13, 2010 21:45:37 GMT
|
Tony
Thanks for that, at least I now know that I am going about it in the right way. Will post up the results in the next couple of days.
Andy
|
|
|
|
|
|
Jul 14, 2010 18:13:40 GMT
|
Pictures of the latest effort. I made the strip longer as was suggested and beat it nearer the edge, but it seems reluctant to bend. Is the right angle sharp enough and should the strip be longer?  This is it next to the template of the bend 
|
|
Last Edit: Jul 14, 2010 18:20:22 GMT by MacBeagle
|
|
|
|
Jul 14, 2010 18:47:37 GMT
|
Andy
You look to be doing everything right so not sure why its not working out, the bend looks tight enough now as well.
The only thing that I can think is that you said you were using 18swg, I have never tried this with 18swg, but I will try over the weekend and get back to you, alternatively do you have any 20swg you could try with
Tony
|
|
|
|
|
|
Jul 14, 2010 19:55:28 GMT
|
Thanks Tony. I will give it a go with 20swg as you suggest. I did a test piece in aluminium before I started all this just to get the idea of stretching and it worked a treat so perhaps 18swg might be pushing the boundaries a bit.
|
|
|
|
|
|
Oct 10, 2010 20:27:04 GMT
|
Sorry its been such a long time since a post, but had to do something yesterday that I thought would be worth sharing I was modifying an exhaust for a an E12 project that I am busy with retrorides.proboards.com/index.cgi?action=display&board=readersrides&thread=88328And wanted to replicate this type of hanger arrangement 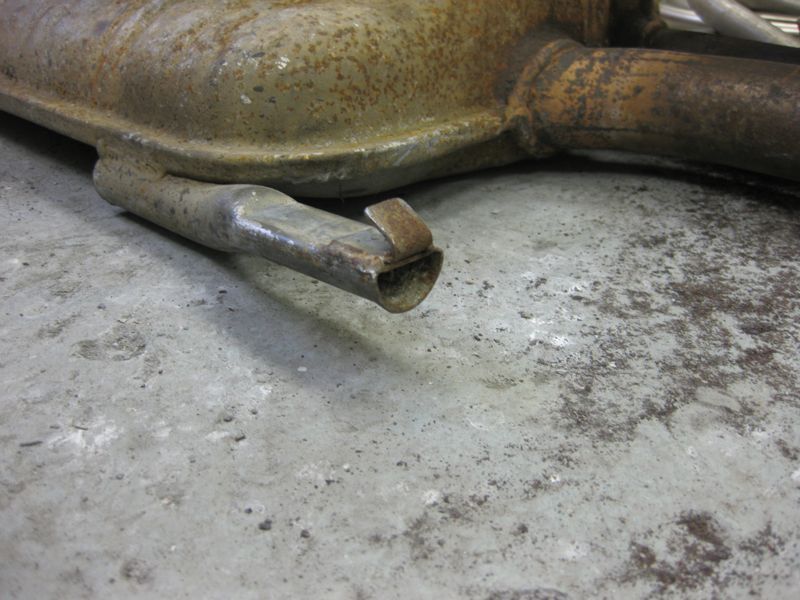 So I needed a bit of tube 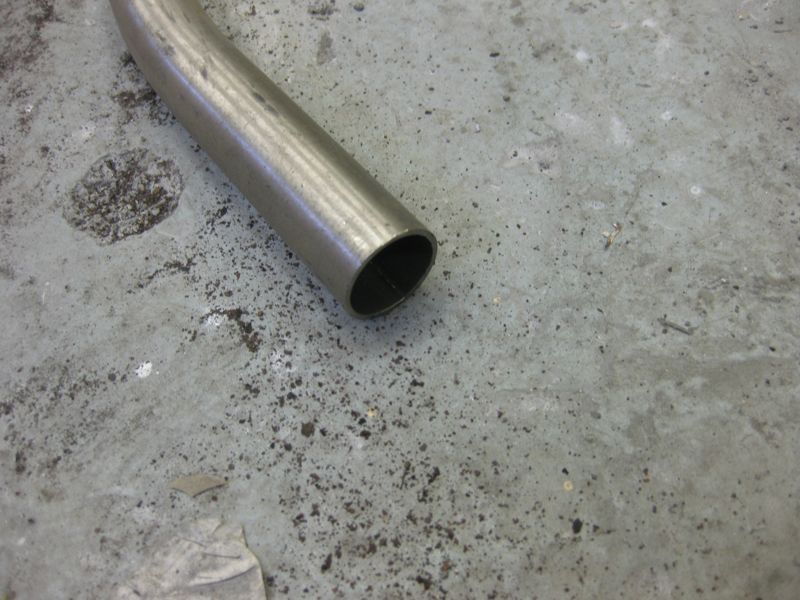 Now obviously to flatten it you just hit it with a big hammer, but how do you stop the bottom going flat too, What you have to do is provide more support on the bottom and sides, so that the top part that you want to flatten becomes the weakest part, and to do that you put it in a V block 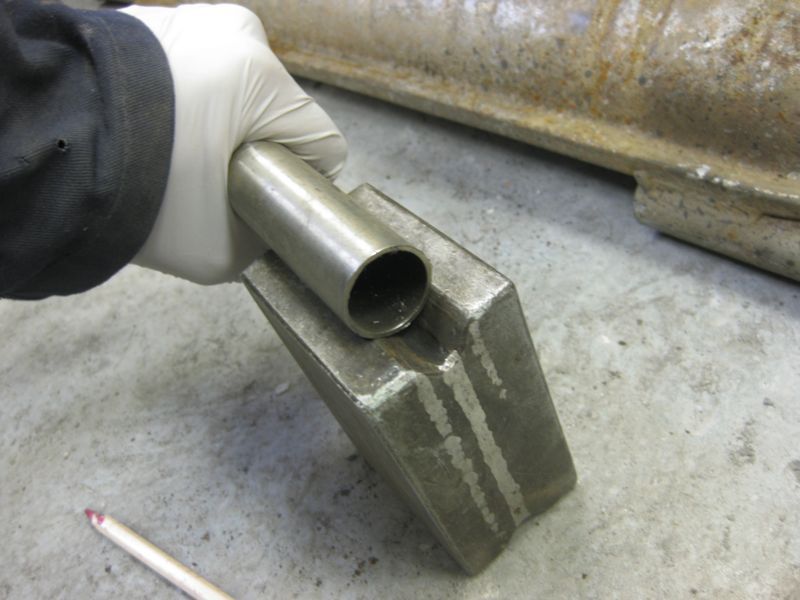 Alternatively if you don't have a suitably sized V block, you could use a bit of angle, the principle is the same Then take the hammer 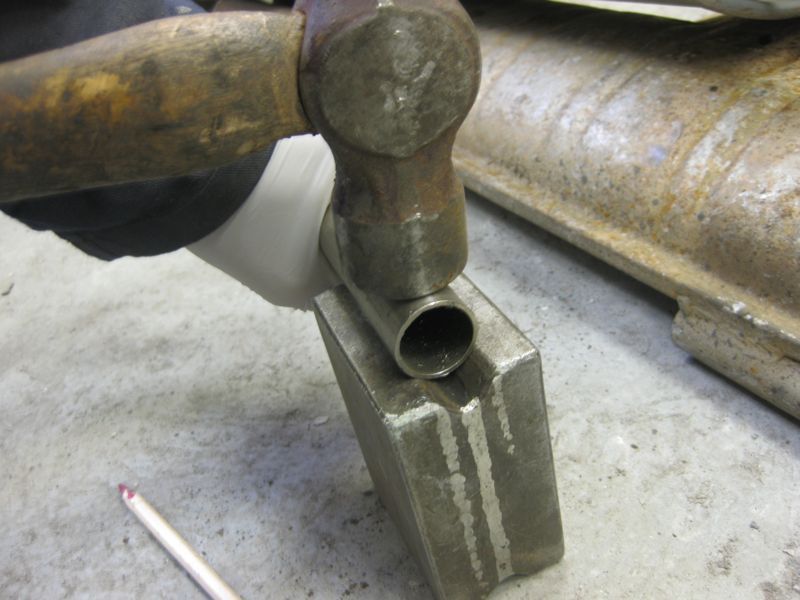 and hit 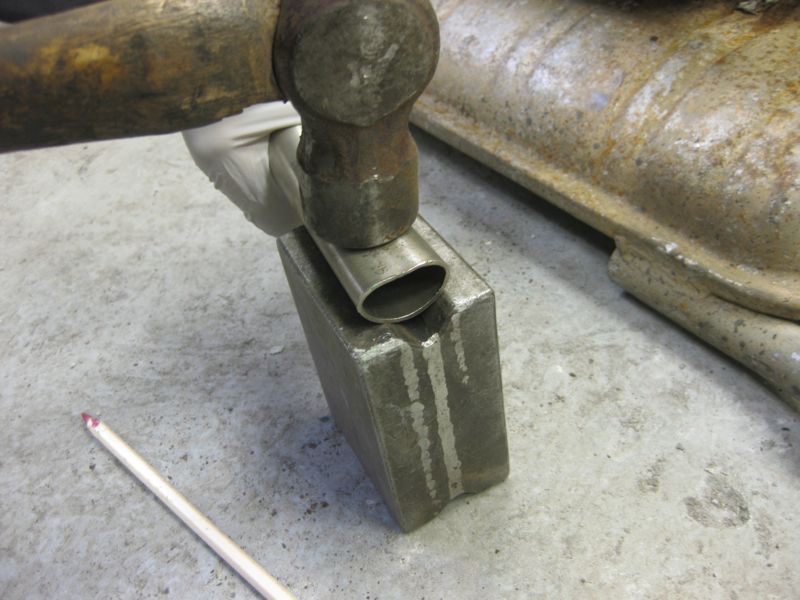 and that gives you the detail you need, 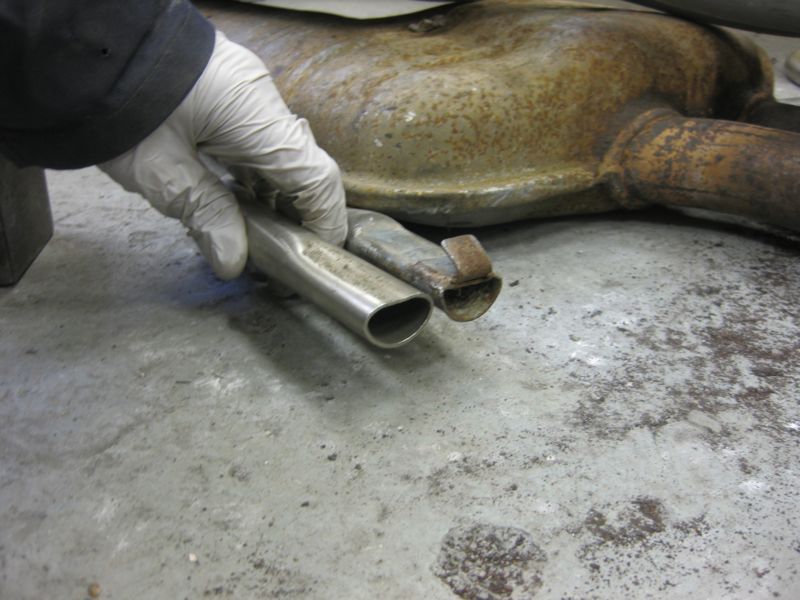 not sure what else you could use this for, but hopefully the principle could give you a few ideas 
|
|
|
|
|
|
Oct 12, 2010 18:43:54 GMT
|
I wish I had a workshop plus the tools. They happiness and fustration that could be achieved is limitless.
|
|
|
|
|
|
Jan 12, 2011 20:41:22 GMT
|
I've made some basic bits before, numberplate bracket for my motorbike, mounts and bits but a) I can't weld and b) I don't have a very solid bench but i'm going to try and sort it out a bit and have a go at some of the techniques mentioned here. Thankyou very much for your time. An amazing thread and a real eye opener 
|
|
|
|
|
|
|
Jan 13, 2011 18:53:02 GMT
|
Glad to have helped, make sure that you let us know how you get on and if you get stuck, just shout
Tony
|
|
|
|
fad
Posted a lot
 
Posts: 1,781
|
|
Jan 19, 2011 10:08:34 GMT
|
mazing thread! Gutted I didn;t find out about this earlier, I had no idea how straight forward forming panels could be! I scrapped my Baja because of a channel repair that daunted me and I felt was out of my league. I wish I had tackled it now! Still, I have my Moggy Minor which will doubtless needs more attention soon. I do have a question though, I was trying to weld a patch onto the floor, I cut out all the rot, it was a flat square that needed doing, but every time I tried to weld I burnt holes in the metal. Now, I've welded before, a couple exampes of my work are here: You can see where I mad a bulkhead from 2mm plate here and welded on a pair of beam supports:  And here, close up of the welding:  I had the welder turned right down but still no good, could it have been down to the thickness of the welding wire? I have a Clarke 151TE and 0.8mm wire. Every time I started to make a seam it just burned right through no matter what I did. In the end I paid a local carage to run a seam for me. Also, where in Northumberland are you? I've sent you a PM.
|
|
Last Edit: Jan 19, 2011 10:25:22 GMT by fad
|
|
hairymel
Club Retro Rides Member
avatar by volksangyl
Posts: 1,081
Club RR Member Number: 207
|
Making panels.......hairymel
@hairymel
Club Retro Rides Member 207
|
Jan 19, 2011 12:19:14 GMT
|
weld in the pics looks ok to my untrained eye  welding thin steel can sometimes be tricky if you try to run a continuous bead as the weld gets hotter and hotter until you blow through  have a look here www.mig-welding.co.uk/thin-metal.htm for a stop start technique that you may find useful 
|
|
whats that burning smell?
oh curse word :-(
|
|
|
|
Jan 19, 2011 20:30:30 GMT
|
I agree with Hairymel on both counts, on thin steel you would be best using a stop start technique, and your weld looks good, so its not your technique
I suspect that with the 0.8mm wire and the welder turned right down, it is taking a few seconds before you can get a continuous weld going, but by this time, its getting too hot and then burning through
This is because the 0.8 wire takes more power to melt, you will find it much easier with 0.6 wire.
After that its down to practice
Tony
|
|
|
|
fad
Posted a lot
 
Posts: 1,781
|
|
Jan 19, 2011 20:45:55 GMT
|
Will get some 0.6 and go from there then! Cheers matey!
|
|
|
|
funkyhunk
Part of things

Old Ford's R Us
Posts: 265
|
|
|
Hi, i'm going to continue welding panels and such to my Ford Taunus this spring, and I got a hold of some stainless steel sheets and some profiles at work with different thicknesses ranging from 0.7mm to 1.2mm. Is this good for making repairpanels such as floorboards, fendermounts, pieces of the sill and so on? I was wondering if mixing stainless with normal steel was a good idea? I have a mig gas welder with 0.6mm wire if that is of any help.
|
|
|
|
|
|
|
Not sure with this one, I was always lead to believe that it was not a good thing to weld stainless to mild steel, for several reasons 1 It causes the mild steel to become a sacrificial metal and it will rust more than it normally would 2 Stainless work hardens much more quickly than mild steel and will therefore crack and fail, quite often at the welded joint 3 Unless a dissimilar metal welding rod is used, the weld can be quite porous and therefore weak again But before I responded to this I read the following article on an official looking stainless steel website that seems to suggest that the above points are not a problem www.bssa.org.uk/topics.php?article=101Personally I would not do it, but I think that might just be from an old fashioned outdated viewpoint
|
|
Last Edit: Mar 4, 2011 19:41:46 GMT by tonybmw
|
|
funkyhunk
Part of things

Old Ford's R Us
Posts: 265
|
|
|
Thanks for the reply Tony, I think I'll try on some test panels first. Maybe try welding two different types together, and test the current vs wire feeds first, then try to bend and pry them apart to see what works best. And, keep the thread alive, I've got my inspiration renewed after reading this. I haven't worked on my Taunus in two years now because of loss of inspiration. And I've got the MK2 RS2000 and the mustang coming up after the Taunus :s
|
|
|
|
|
|
|
Let us know the results of your test, and glad to hear that you are re motivated, can anyone else shed any light or had any experience with the stainless to mild steel scenario ??
|
|
|
|
funkyhunk
Part of things

Old Ford's R Us
Posts: 265
|
|
|
I have a friend who cut up some old water heaters, and used the steel from the tanks to make repair panels on his Opel Kadett C. He said it went fine. He used TIG and stainless welding rods though, but he had no issues, and now two years later it still looks nice. I'm going to give some feedback when I try it closer to the middle of may. We still have lots of snow here and the temperature is still below freezing. My garage isn't isolated ,and I have no heating either 
|
|
|
|
|