|
|
Mar 19, 2014 19:29:28 GMT
|
I managed to do the underside welds of my second repair piece, had a job getting the setting right but got there in the end. Burnt an edge rushing but repaired it using the copper trick ;-) Here's the finished article (well at least the radius is finished): 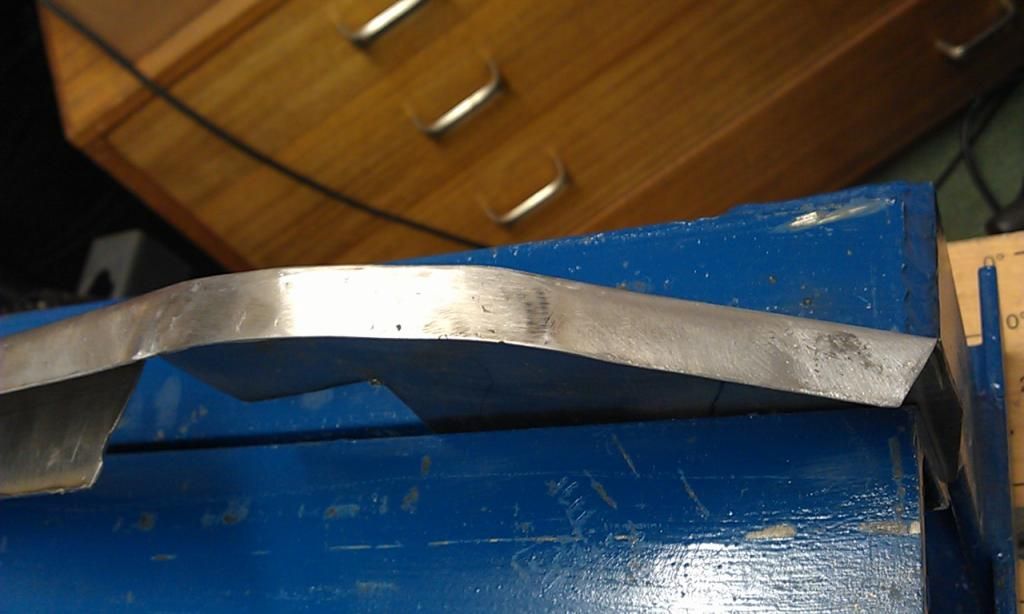 Here's the underside - what's the best way of cleaning this up, at the mo I only have some flap discs for my angle grinder and some hand files. 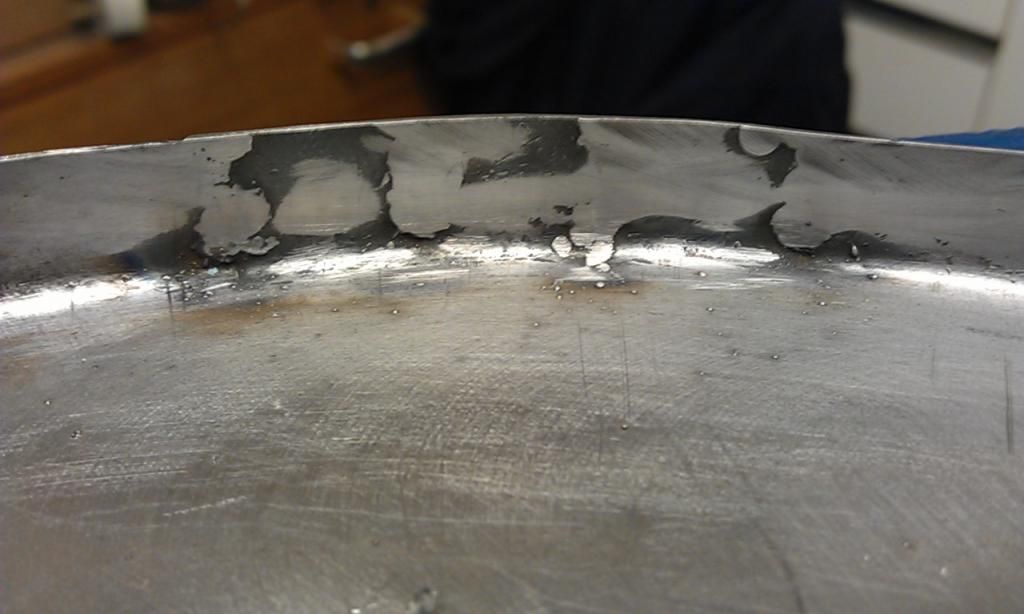 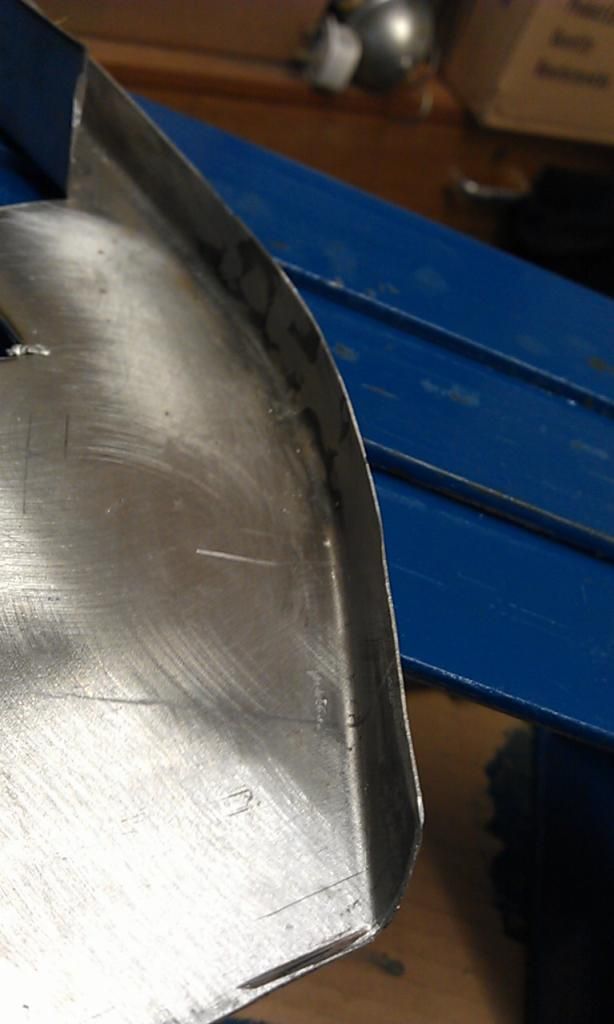 Its a right angled bend and I need to get in the corners, will I have to invest in a power file? Or dremel or are there small attachments for my drill?
|
|
|
|
|
bobman
Part of things

Posts: 109
|
|
Mar 19, 2014 20:45:45 GMT
|
A mini air grinder with 2 1/2 inch grinding disks are the best for tight spots like that, also a mini die grinder with a couple tungsten carbide heads work wonders for clean up! Awesome thread some nice old skool tips and tricks in here
|
|
|
|
Wild
Part of things

Mini Restoration
Posts: 12
|
|
Mar 19, 2014 23:50:03 GMT
|
I've had my mini for quite a while now and really haven't made much progress at all! I've been so motivated by this thread that I need to do her. I done these panels months ago before I read this thread and after taking the advice of some forums and people but I'm not happy with the results at all!  Photo isn't very clear but basically it's an inner wing flitch panel replacement as the old ones were basically knackered. I was told to do a lap joint and plug weld the new panel over the existing panel but I'm really not happy with the finish and want to it properly. I want to cut the lap joint part out and do it properly. Would anyone have any advice in how to go about fixing my rookie mistake :-( if I cut out the part of the panel that is overlapping and cut a new piece of metal to fit the hole that May or may not be there and seam weld it in would this be sufficent? Please any help would be grateful! I've also ballsed up the other side but hopefully once I've done this side I'll be able to rectify the other side much easier.
|
|
“On a given day, a given circumstance, you think you have a limit. And you then go for this limit and you touch this limit, and you think, 'Okay, this is the limit'. And so you touch this limit, something happens and you suddenly can go a little bit further. With your mind power, your determination, your instinct, and the experience as well, you can fly very high.”
- Ayrton Senna
|
|
Wild
Part of things

Mini Restoration
Posts: 12
|
|
Mar 19, 2014 23:54:03 GMT
|
Just encase you don't fully know what it looks like here is a photo of someone's mini who has successfully welded in a new one : 
|
|
Last Edit: Mar 19, 2014 23:55:29 GMT by Wild
“On a given day, a given circumstance, you think you have a limit. And you then go for this limit and you touch this limit, and you think, 'Okay, this is the limit'. And so you touch this limit, something happens and you suddenly can go a little bit further. With your mind power, your determination, your instinct, and the experience as well, you can fly very high.”
- Ayrton Senna
|
|
|
|
Mar 20, 2014 13:42:44 GMT
|
Wild any chance of a better picture from both sides? Very difficult to see what you are asking? Here's my build project on Mini Forums, one of the first repairs we did was the Flitch panel, this was done by a professional welder. I think the Flitch sits on top of the bulkhead (sort of double skinned). We seam welded the Flitch to the piece that we cut off. There is loads of Mini experienced advice on www.miniforums.co.uk if you get no joy here.
|
|
Last Edit: Mar 20, 2014 13:44:04 GMT by jonnyalpha
|
|
Wild
Part of things

Mini Restoration
Posts: 12
|
|
Mar 20, 2014 17:51:22 GMT
|
Forget my last few posts I've just been over complicating things!
I went out tonight and basically the exsisting panel that was there before that I had cut the rotten bit out I basically just ran a thing cutting disc down the back of the new panel from the inside and butt welded it so mega happy there's a little bit left to weld and grind down but nothing serious.
Hope to get cracking now :-)
|
|
Last Edit: Mar 20, 2014 20:18:44 GMT by Wild
“On a given day, a given circumstance, you think you have a limit. And you then go for this limit and you touch this limit, and you think, 'Okay, this is the limit'. And so you touch this limit, something happens and you suddenly can go a little bit further. With your mind power, your determination, your instinct, and the experience as well, you can fly very high.”
- Ayrton Senna
|
|
|
|
Mar 21, 2014 12:23:58 GMT
|
OK - I have started to form the second repair piece of my Subframe repair, bending the straight folds was simple: 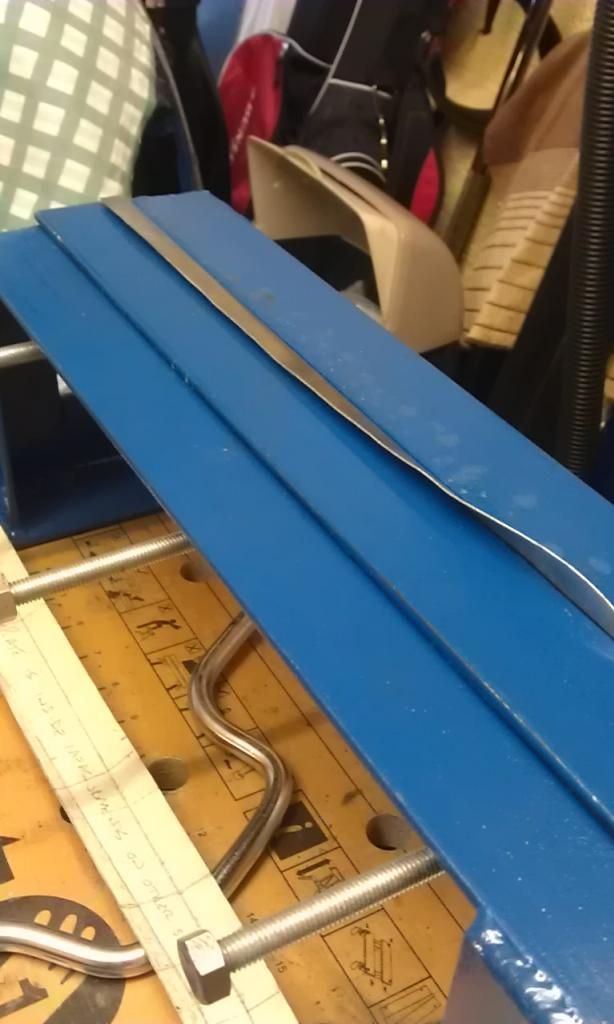 Only thing I would say is to bend more gradually as you might introduce stretching. In the photo (if I've quoted properly) you can see that at one end you've done almost the whole 90 degree fold, and at the other end there's none, but that puts a stretch in the flange section in the middle which can lead to the panel twisting. Do the whole length about 10 degrees at a time and it seems to help. Trying to bend the curved folds however proved a bit trickier, I could not do it in my bender due to the size of the panel, maybe if I had started with the curved folds first it may have worked but I needed to get the straight folds done to ensure the curved folds were correct as the piece I have cut off had already been repaired and was distorted in that area?@?@??@ Yes, often you have to think the whole job through to make sure that you don't end up blocking access and making the job harder. It's just experience, you'll remember next time. I've lost count of the number of jobs I've done on my project that would have been simpler if I'd done them in a different order. I then measured and marked the bottom fold and managed to start it off in the bender but due to the close proximity of the two folds could only bend to about 45 Degrees. I had to then clamp the piece to my workbench and using a piece of scrap sheet about 5mm thick wedged into the fold I managed to tap the remainder of the fold. Sorry no pics of how I did it but again any tips on bending close folds would be appreciated (The folds in the picture below to the RH side of the Mole Grips on the left). As you do more of this stuff, you'll gather scraps of stuff to put in the vice or bender to help make these closer bends. It's just a case of looking at it from all angles then figuring out what you can use to extend the reach or get into that corner. A straight bender isn't the cure for everything, bits of scrap angle iron and bar can come in very useful. You'll also notice that the metal on the top curved fold where it has been cut overlaps itself, this is because all I did was cut a line with a pair of snips. Should I cut a small 'V' to ensure that the metal lines up and then weld the gap? That's correct - because the metal in that section would be smaller (which is why you would have needed to shrink it if you'd folded without the cuts) you have to remove bits of it. I sometimes do what you've done, then fold it, then use a hacksaw to cut along the overlap, to make sure I haven't cut out too much of a 'V' shape.
|
|
|
|
|
|
Mar 21, 2014 21:42:08 GMT
|
Droopsnoot - thanks for the tips. OK now onto the next part of the second repair piece, I need some advice on fabricating this part of the panel: 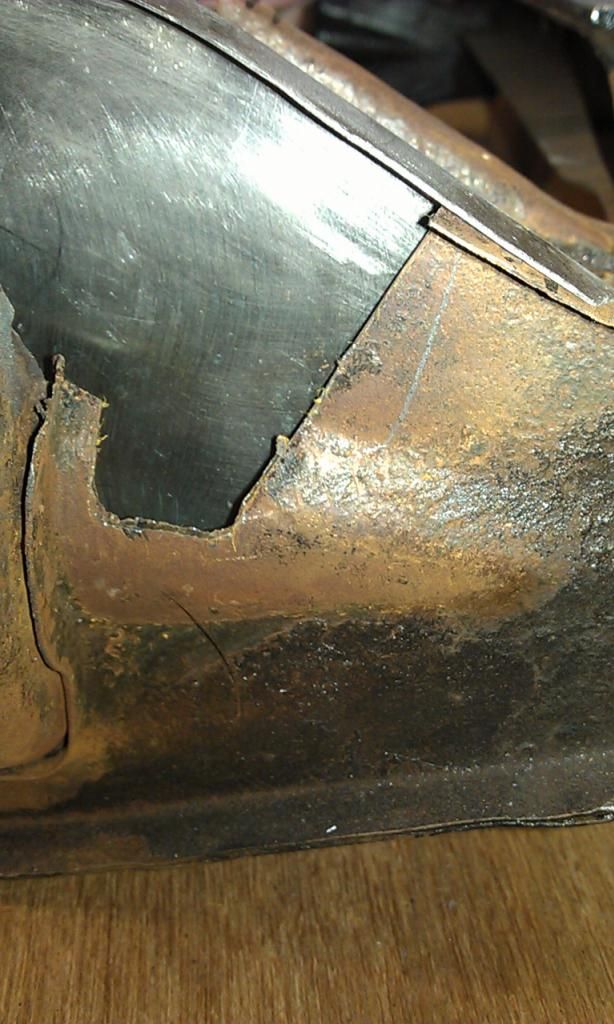 I will be completing the cut at the bottom. The bottom of the repair needs to have a curved fold, on the left hand side has a right angle fold which is the vertical curved piece to the left of the picture. Here is a picture of the opposite side (which also will be replaced) to give you and idea of what the panel needs to look like: 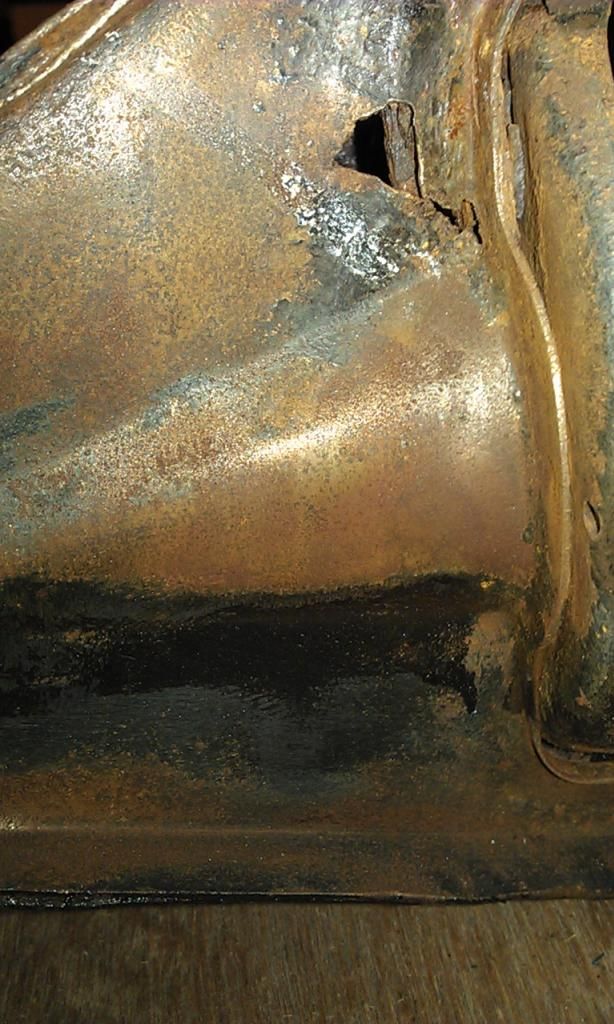 Heres my idea: 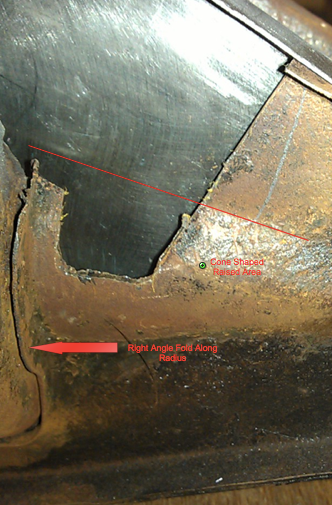 Option 1. One idea I have is to make an initial fold along the red line and form the radius of the cone using a round bar as a guide. After the radius has been formed I was then going form the right angle fold but as this will now be along a curved edge I will have to cut one or two V shapes bend the fold and then weld up the gaps. This option will ensure that the fold remains vertical. Option 2. The second idea was to make the fold along the red line but then also make the vertical fold and then stretch the metal in the second fold in an attempt to create a curve however, this will thin the metal along the fold and it would be difficult to create the correct cone shape. What do you guys reckon on how to tackle this? I am also going to joggle the right hand edge and bottom as there is enough room on the inside (hopefully) to lap weld.
|
|
|
|
|
|
Mar 22, 2014 17:21:21 GMT
|
I would first do the 90 degree bend (the flange on the cone), then cut a V into it (or shrink the metal, which might be hard to do in in such a short space) to create the bend along the red line in your picture, then stretch the metal to form the cone.
|
|
|
|
|
|
Mar 22, 2014 18:57:20 GMT
|
If you make the straight fold, then curve the cone shape, then try to fold the flange over, that will start to flatten out the cone a little. But if you then use the technique mentioned earlier in this thread to stretch the flange using a hammer, that should allow the cone to resume it's shape. The fact that it's a little thinner shouldn't matter as long as the steel starts out the right thickness - after all, the same happens when the manufacturer presses the original panel.
|
|
|
|
|
|
|
Mar 22, 2014 20:46:25 GMT
|
wheeler / droopsnoot; thanks guys, I think i'll try out both of your suggestions on a spare piece first to see which is easiest v best result.
|
|
|
|
|
|
Mar 23, 2014 21:51:31 GMT
|
I sort of did a mix of the two ways that were offered, I made the straight fold at the top of the cone, then I made the 90 degree fold and tried to stretch the metal to form the cone, it started to shape but in the end I had to make some cuts in the fold and used a large piece of metal tubing to complete the shape.
I then cut the repair panel to fit using a mix of joggled edges for lap welding and end on end joints for butt welding.
Made a few errors along the way but nothing that cannot be fixed, could have been better but not bad for a first real effort.
I'll post some pics tomorrow.
|
|
|
|
|
|
Mar 24, 2014 21:12:21 GMT
|
I sort of did a mix of the two ways that were offered, I made the straight fold at the top of the cone, then I made the 90 degree fold and tried to stretch the metal to form the cone, it started to shape but in the end I had to make some cuts in the fold and used a large piece of metal tubing to complete the shape. I then cut the repair panel to fit using a mix of joggled edges for lap welding and end on end joints for butt welding. Made a few errors along the way but nothing that cannot be fixed, could have been better but not bad for a first real effort. I'll post some pics tomorrow. Here's where I am so far: First after re-measuring I marked up the panel and made the initial fold at the top of the cone: 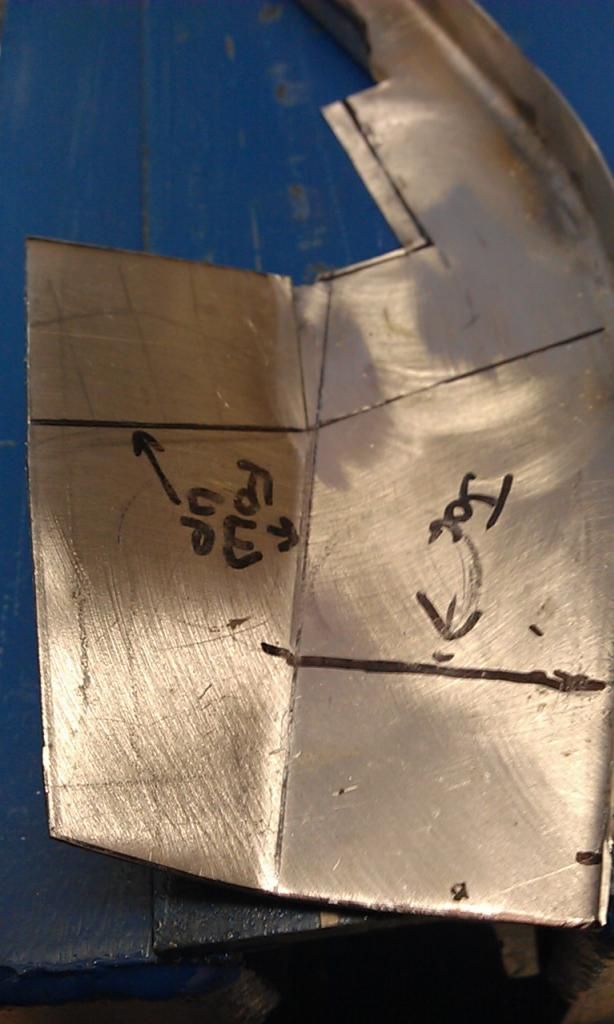 Then I made the 90 degree fold and tried to stretch the edge to form the cone, I had also made one cut before I made the 90 degree fold (first possible mistake I think: 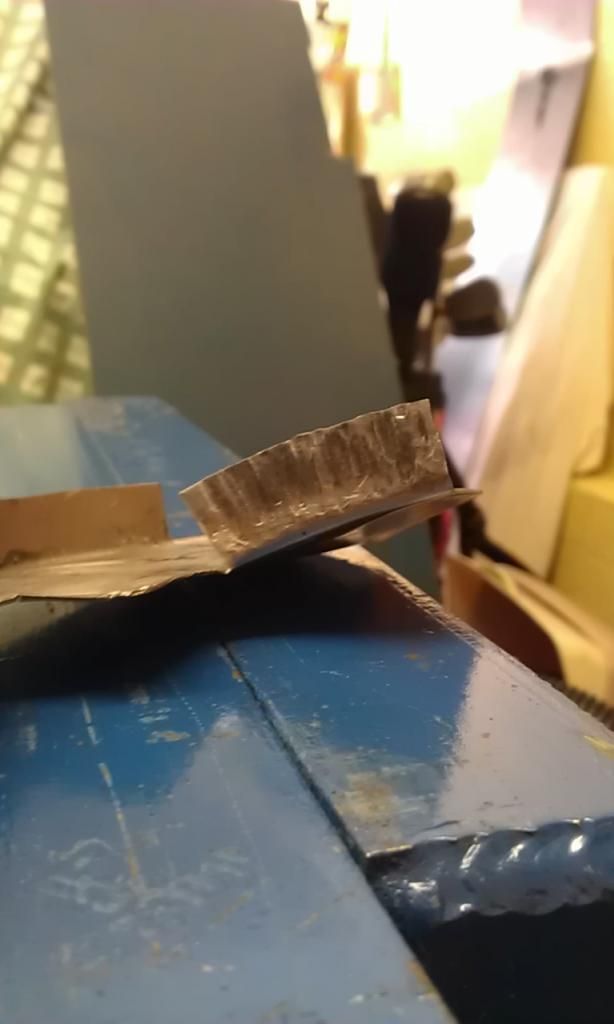 You can see it sort of wanted to form but not enough so I introduce a large metal tube: 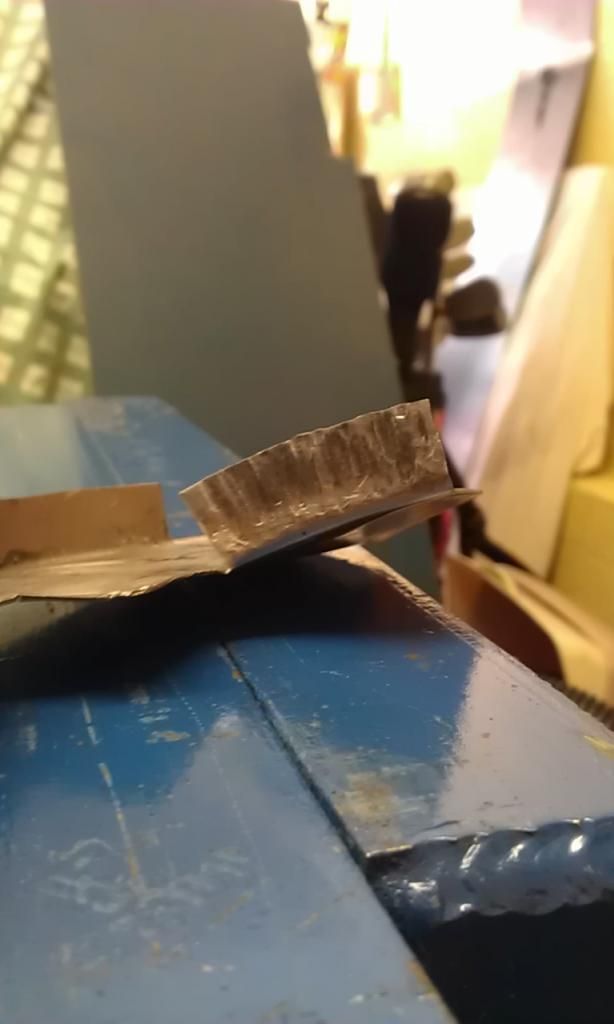 Two complete the cone shape I had to make another cut (poss another mistake) and then using a piece of bar forced down by hand / body weight I then completed the other folds with a light weight hammer, I also introduce more cuts rather than shrink the metal however I made a few boo boos (another mistake) 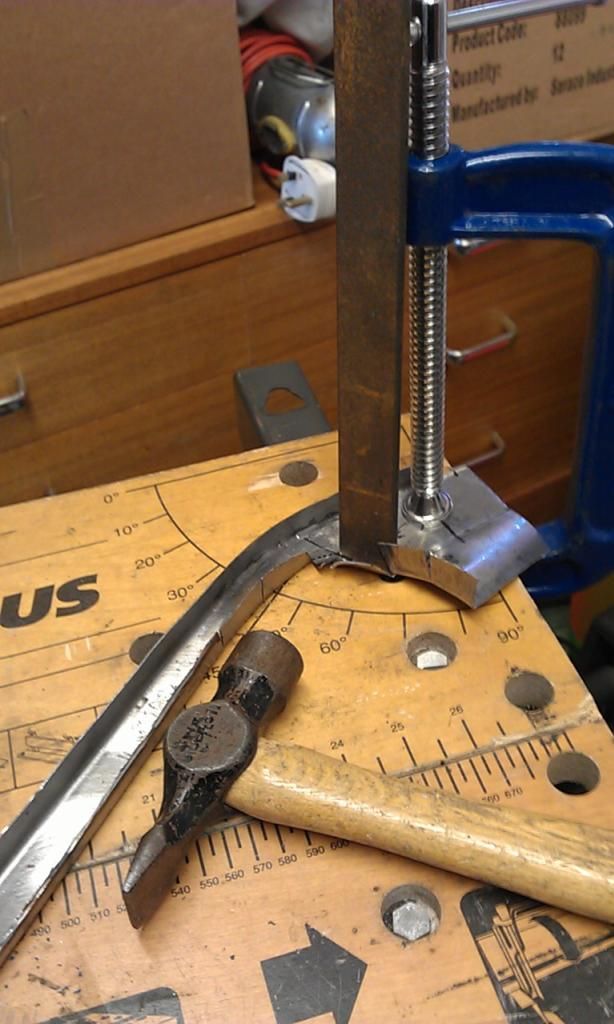 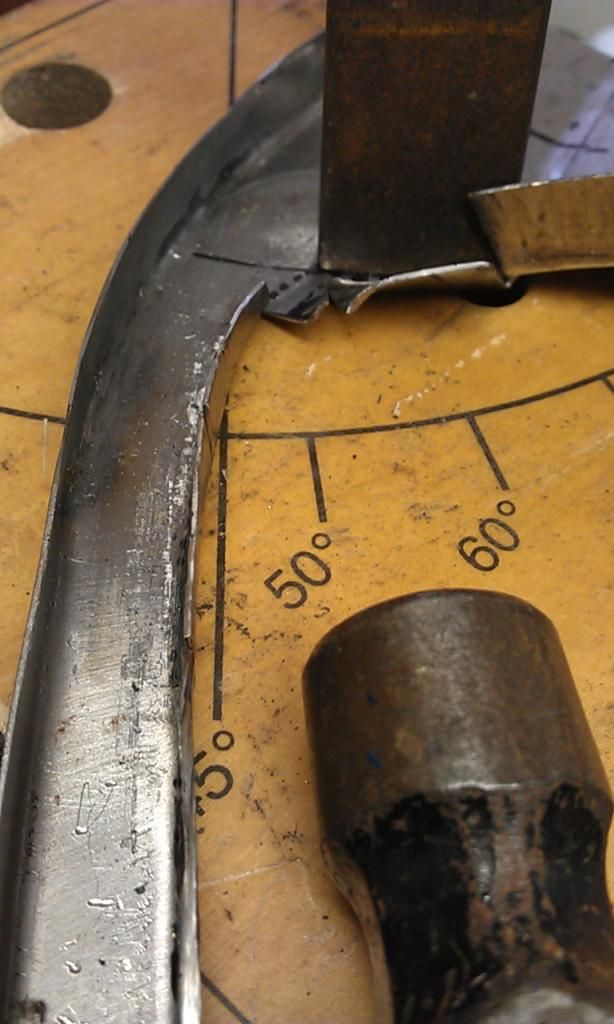 All the cuts however can be welded up so its not the end of the world, if I had been a little more bold and cut the underside fold to the correct size before it was folded I may not have needed the cuts but I didn't want to leave the folded edge too small, still everyday is a learning day!! Here's the panel being test fitted before the joggled edges and but edges had been introduced on the left hand side:  Here's a nice pick of the left hand side once the joggles and but edges had been marked and cut, I decided on a mix of joggled edges and butted edges to improve strength? ![]() 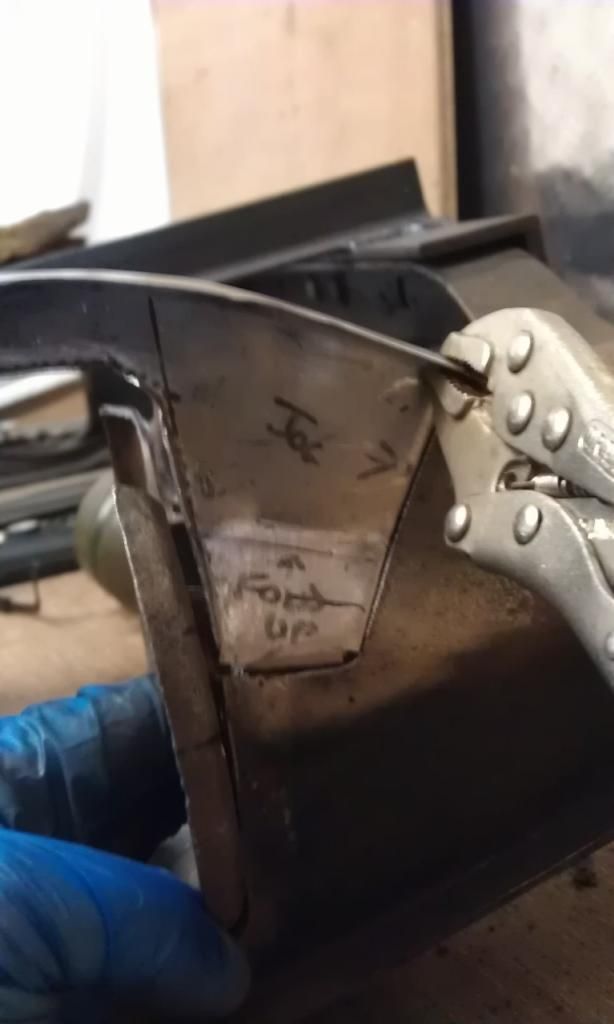 The top R/H edge and bottom edges are joggled and the R/H edge of the cone is a butt (I couldn't work out how to joggle on a radius without flattening the curve?@?@? And finally here is a close up showing the horrendous mess I made of the underside internal curved folded edge: 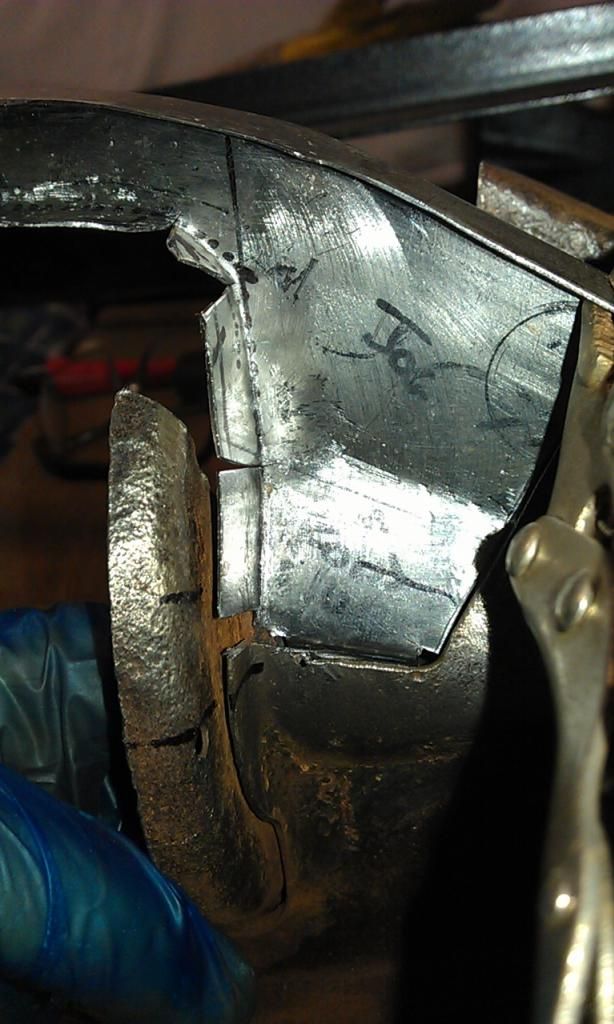 The panel itself is a pretty good fit, its just the folded edge that I messed up!!!
|
|
|
|
|
|
Mar 25, 2014 13:29:26 GMT
|
The top R/H edge and bottom edges are joggled and the R/H edge of the cone is a butt (I couldn't work out how to joggle on a radius without flattening the curve?@?@? That's where a "Rolastep" comes in useful, basically a pair of circular jaws like those in a bead roller, but in a hand-held tool that you wind along the edge of the panel to introduce the step. Around £45, so you you really need to use them a fair bit to make them worth the money. And you have to deal with the fact that the bit that steps 'down' in effect needs to be shrunk to sit properly, or make the curve too tight so that the other bit can expand. Very nice edge though, I get a nicer edge with these than I do with my standard one.
|
|
|
|
|
|
Mar 28, 2014 20:06:59 GMT
|
I am now making the repair piece for this area: 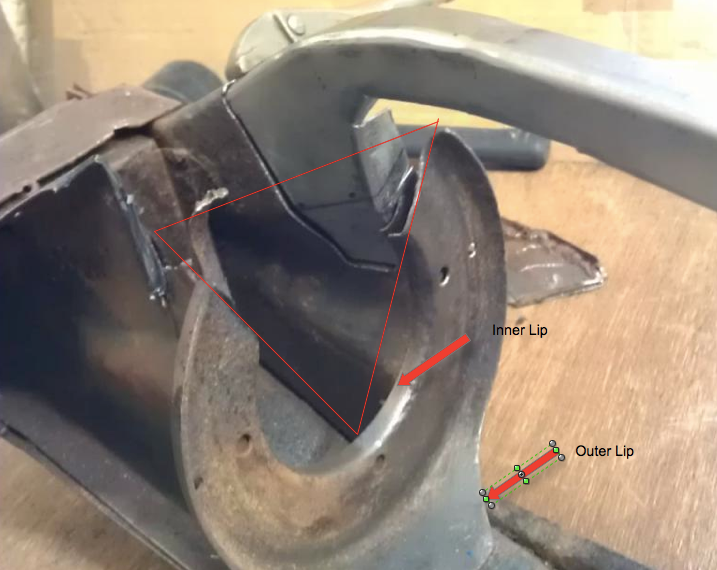 First I started by measuring the area to be repaired to make a template, I used the intact bottom area which is a mirror image: 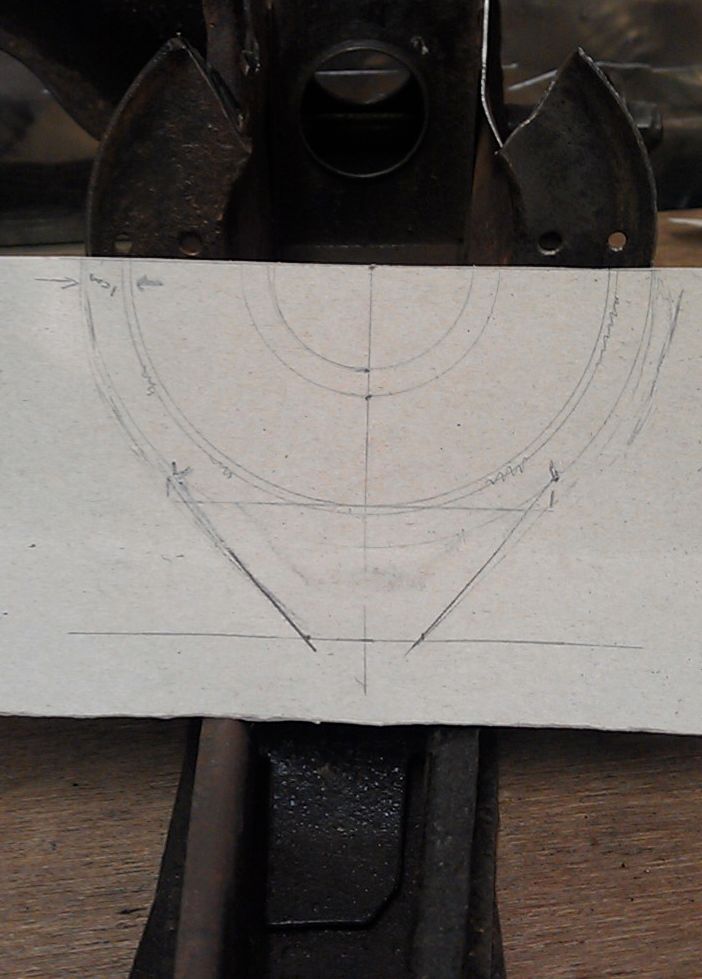 This template turned out incorrect, I had to make another one but you get the idea. I then transferred the measurements to a piece of 2mm steel: 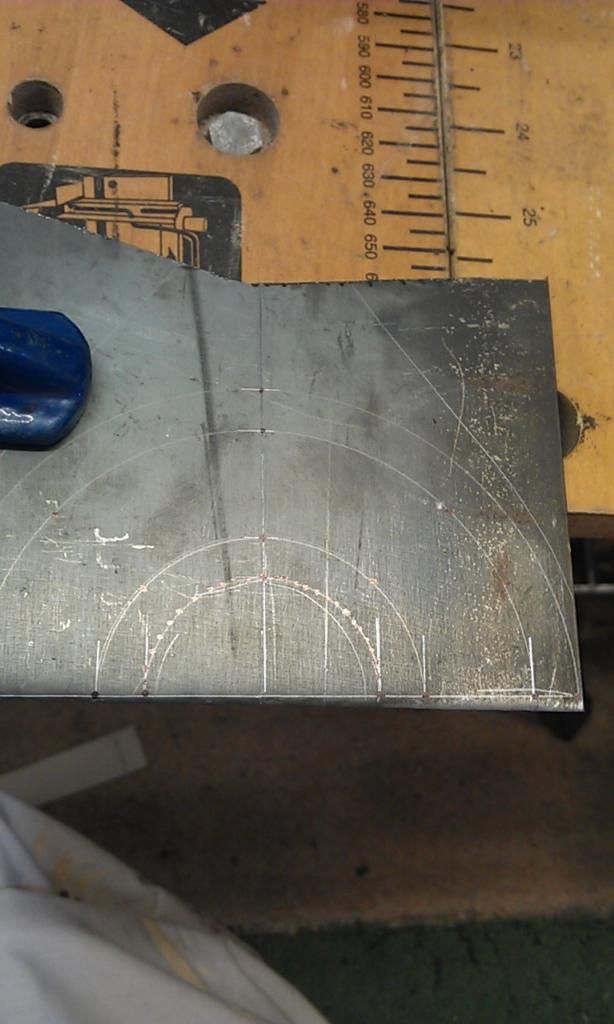 I cut the plate down first and did the first bend in my folder: 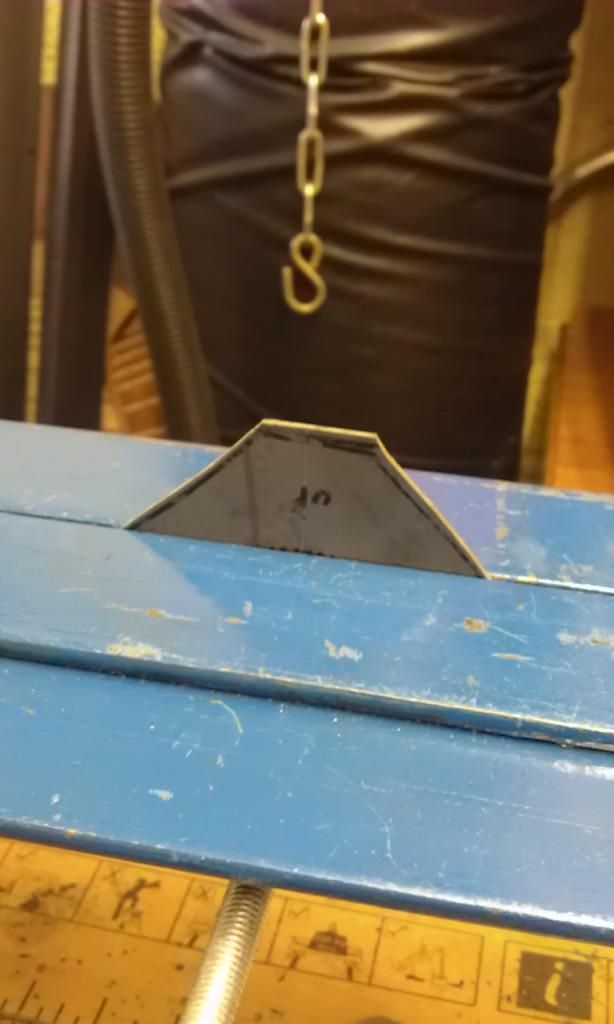 Form advice in this thread I new I would have to make the bends evenly and in small stages, once I did the first folds I then trimmed a piece of 4mm bar so that it had a radius'd edge the same as the radius of my piece to be bent. Using this held in place with a G Clamp I started to slowly apply the bends. To get better leverage I also placed the piece sideways in my bender with this 4mm piece clamped against my panel: 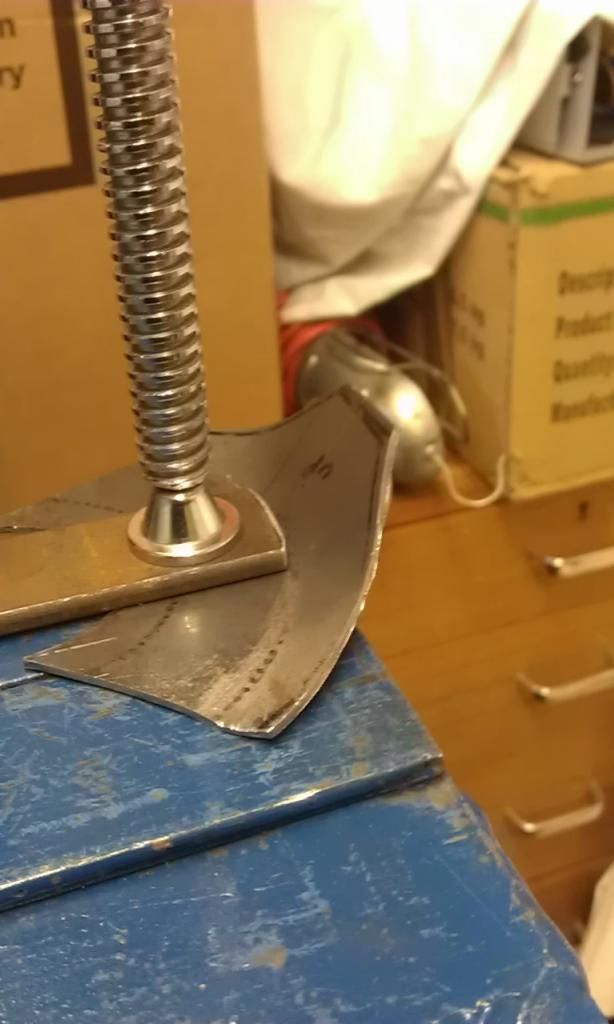 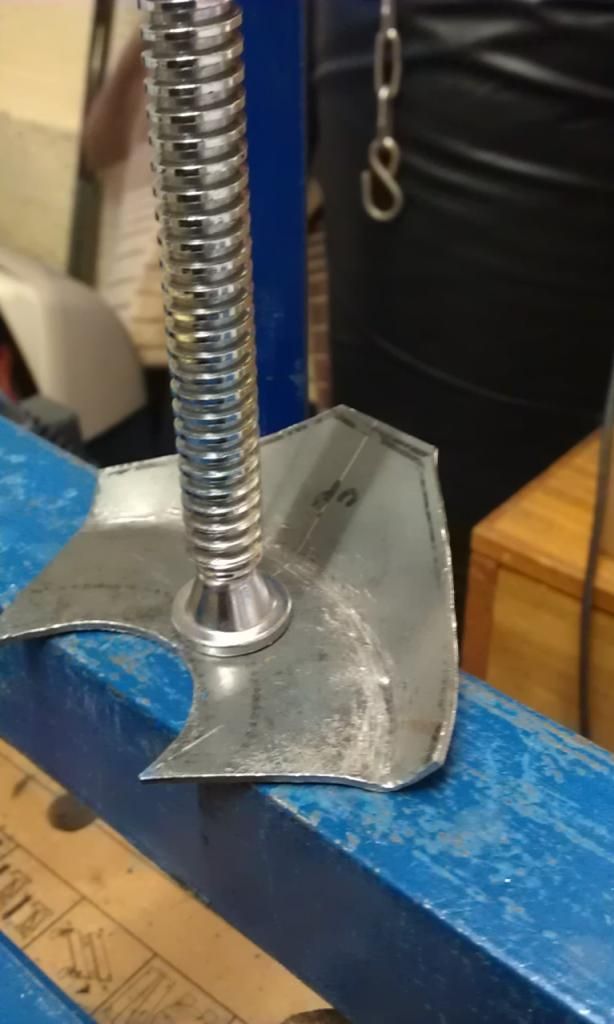 Slowly but surely the fold is forming, however as this metal is a lot harder to form and needed a lot more beating I managed to shear the welds on two of my captive nuts on my bender. I also kept having to hammer flat the area where the clamp is in the above pic as making the folds is trying to pull the flat area out of shape. I am trying to make this piece without having to cut and weld so its slow going but it looks like it will form without having to put a shrink in the edge?? The actual piece I need will be smaller than this but I did not want to cut it to fit before I had formed the correct shape.
|
|
|
|
|
|
Mar 29, 2014 19:48:21 GMT
|
More bashing today.............. And after a lot of work here it is: 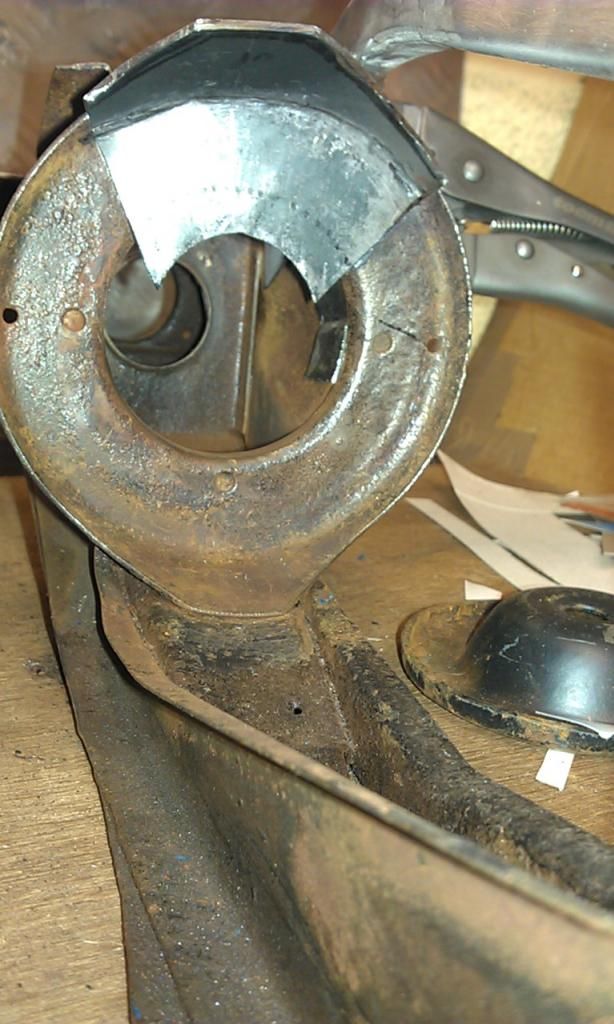 Just got the last fold, the internal one, which hopefully shouldn't be too difficult?
|
|
|
|
|
|
Mar 31, 2014 21:06:52 GMT
|
So after another half day in the garage I managed to complete the circular repair piece (less a small amount of minor adjustment before welding) I struggled at first to do the internal bend as I could not find a way of holding it in my bender or clamps to be in a position to fold it. In the end I managed to use part of the subframe as a pattern. Its the rear rubber cone that came off when I removed the trumpets, I think it was very poorly spot welded onto the piece that I am now repairing? Anyway using it as a template held together using 2 x G Clamps I started the fold. 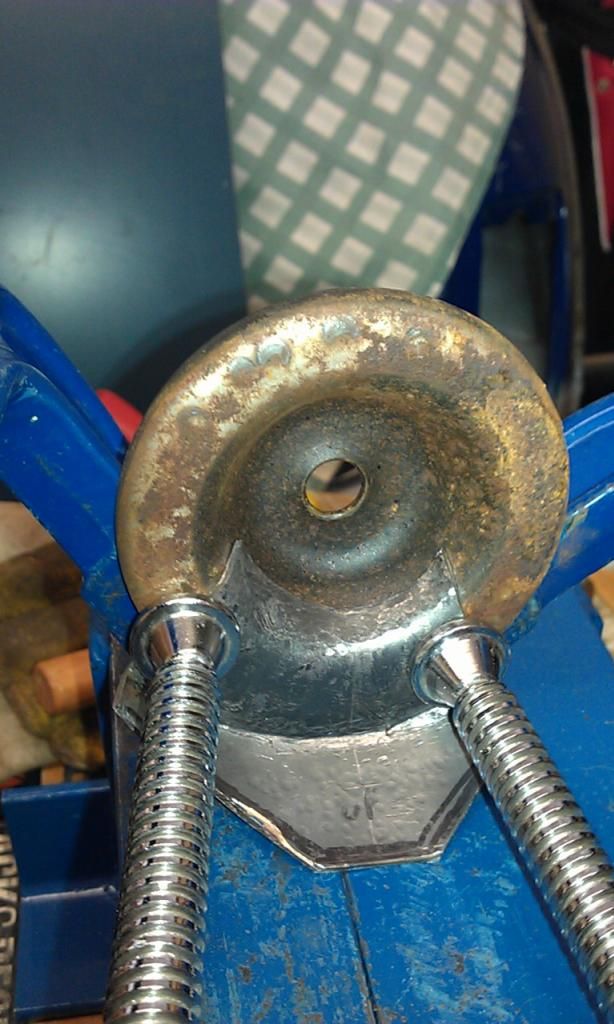 When I fitted it in place the diameter was slightly out but using my vice I managed to bring it in line, its not quite right but it will be hidden behind the the piece used as a template above: 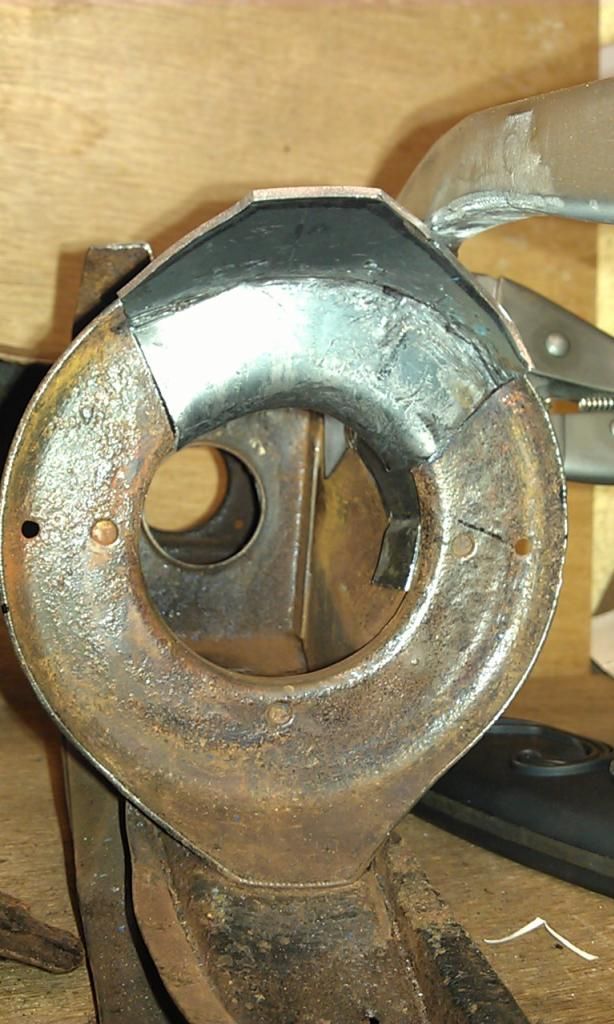 I also had to re-do about 15 - 20mm of the top RH edge external fold as it too was out of kilter so apart from trimming down the excess edges and a little fine tuning its ready to weld in place. I have to be careful however after I have fabricated all of the pieces for this side ensuring that I weld them in the best order otherwise I will find it hard to dress the welds where dressing is required. The piece above will probably be last to be welded? When I weld the circular piece which is 2mm thick I clean up the edges of the existing rusty coloured piece above and as advised i'll bevel the edges of both the repair piece and the existing piece that it will be welded to. To be honest I should have cleaned up the existing piece first in case cleaning it causes my repair piece to not fit as snug!! (lesson learnt for next time). To complete this side I have two pieces left to make, the LH main support (The RH one was the second piece I made) and the internal support piece that the circular piece I have just made sits on, you can see the intact one at the bottom of the pic above, its located between the two main spars.
|
|
|
|
|
|
|
Hi Jonnyalpa; i must admit that when you started this thread i thought you were nuts to try to restore this part! I can see that it is coming along great and it is fasinating watching you do this....Kudos keep it up!!
|
|
I would be rich if i had not spent so much money on Cars and fast women...oh, i did waste some of it as well!
|
|
|
|
|
Hi Jonnyalpa; i must admit that when you started this thread i thought you were nuts to try to restore this part! I can see that it is coming along great and it is fasinating watching you do this....Kudos keep it up!! Thanks - its always nice to get support, I thought I was nuts too however, as someone stated earlier in this thread (or was it on the Mig Welding Forum?) I started with a Subframe that was wortheless and may end up salvaging it, even if I don't, along the way i'll learn some new skills, so why not. So far its proving successful :-)
|
|
|
|
|
|
|
Spent a couple of days over the weekend making the second main spar, this time using some of the advice from this and the Retrorides thread, I thought i'd try and form the radius folds without reverting to cutting and welding. Sorry no photos of the stages but I did make a video (Sad I know) its not great quality and needs a little editing but if anyones interested i'll post it on You Tube for a laugh!!! Anyway the results were pretty good, I managed the underside radius without any cutting and only had to make one cut in the topside radius, heres the end result: 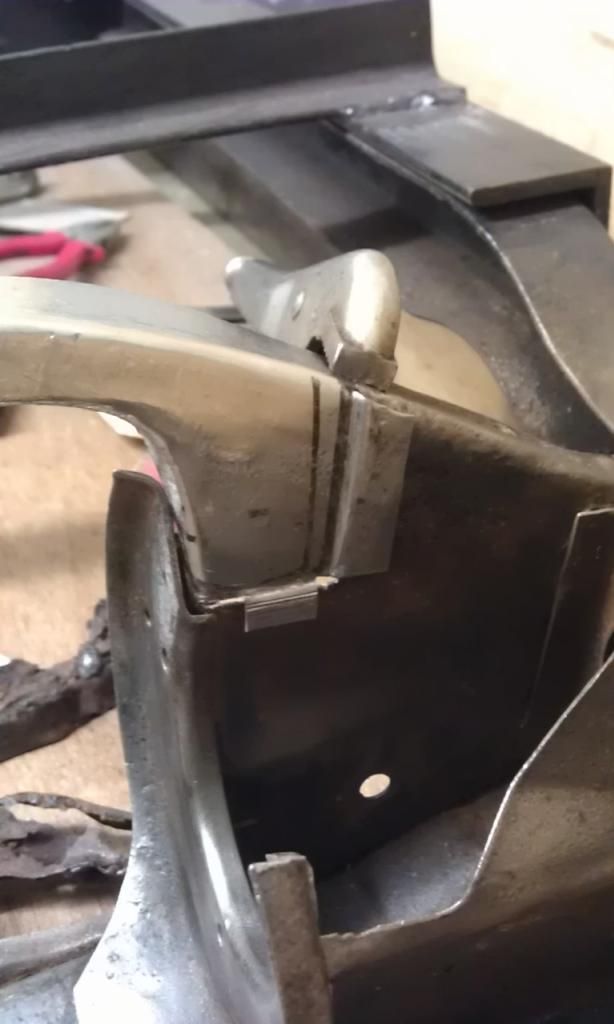 Sorry no pic from the other side, my joddled edges are not great (nearly bought an edge setter from Machine Mart, maybe I will soon :-) Here's all three parts in place (not yet welded): 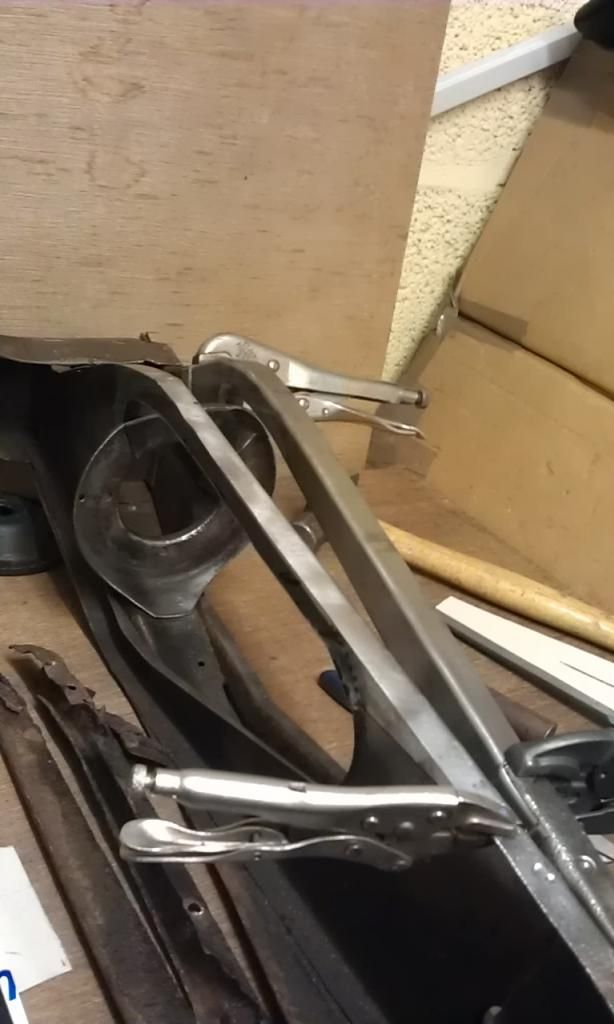 Only one more small piece to make for this side then it can be welded up. When its welded this area will be enclosed: 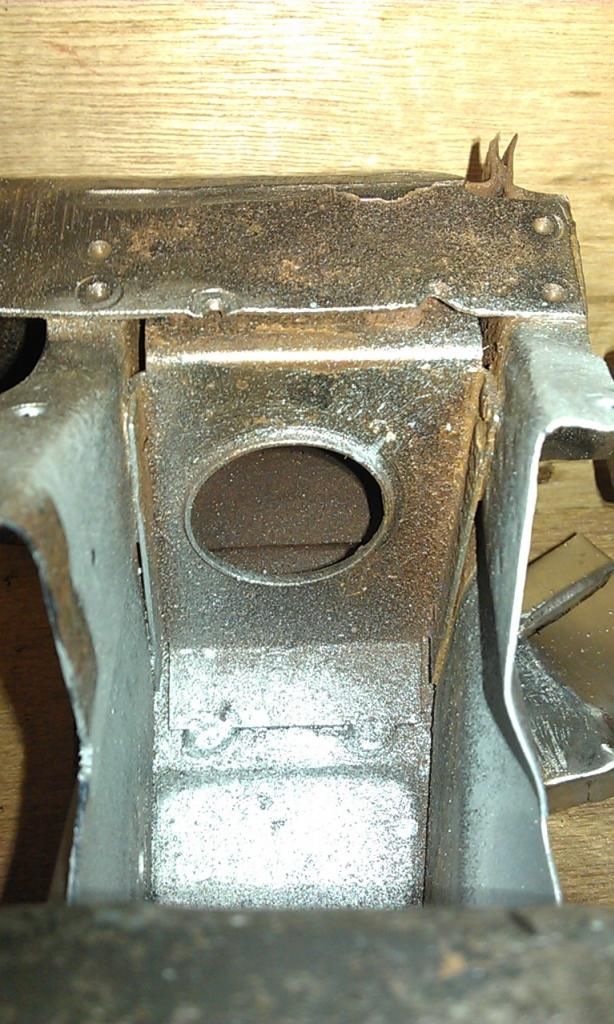 I'm not going to be able to clean it down to bare metal and still undecided (financially) on Acid Dipping / Galvanising the finished article, in case I decide to NOT galvanise and opt to POR15 the subframe should I bung some Hammerite KRUST in this area and coat with Red Oxide or U-POL Weld Through Primer? I already put a bit on in this pic on areas that I could clean up.
|
|
|
|
|