|
|
|
A big thank you to blackpopracing for suggesting the 90 degree sander. I've just had a go with it and it really is a nice piece of kit and a bonus it coming with all the bits and pieces. I also took your advice and used WD40 as a lubricant and with the 50 grit disc it made short work of the unwanted weld penetration. 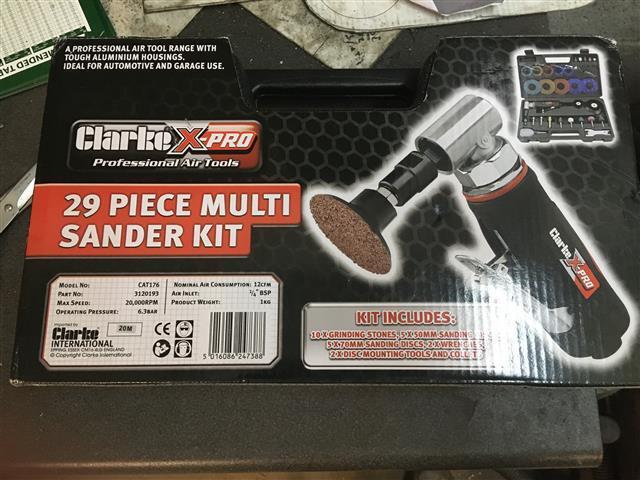 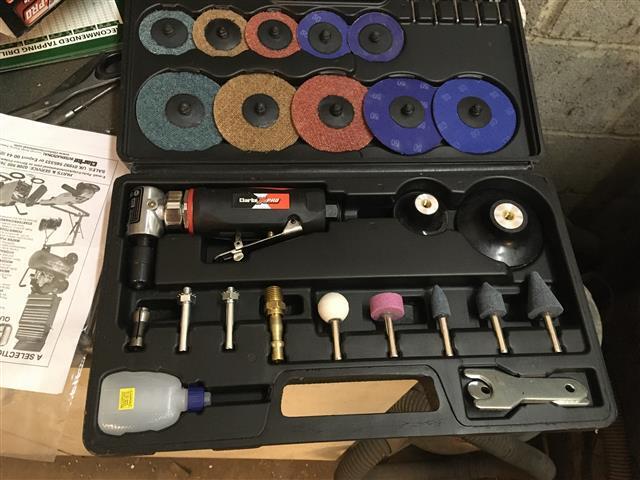 I wondered if the Octopus might be of interest. I made it some years ago and for some jobs find it very useful It does allow both hands free for planishing. Not my design, it came from Lazze who has a YouTube channel. It was simple to make using one inch diameter ball bearings onto which I welded the stainless steel bars with vice grips at the end. Being double ball jointed, it will accommodate just about any shape. 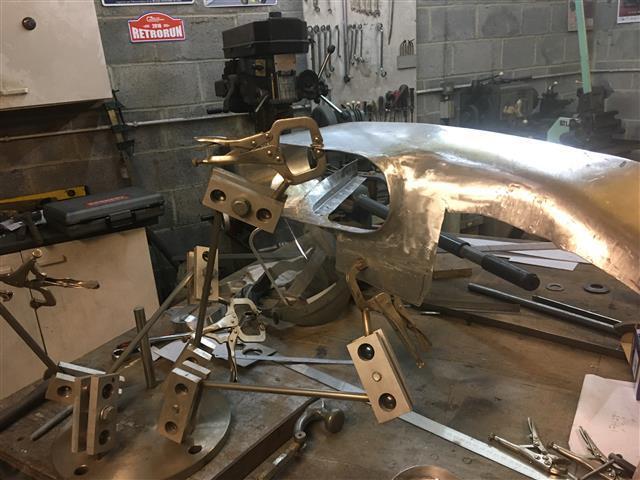
|
|
|
|
|
|
|
|
They are a really useful tool aren't they?
That Octopus looks very useful too.
|
|
|
|
|
|
|
I think there will be a Octopus building project in my future...
|
|
|
|
|
|
|
I think there will be a Octopus building project in my future... Well if you want some balls I'm your man, ha ha!! Actually, I had to buy a box of them so there are plenty over and you are welcome to have what you need.
|
|
|
|
|
|
|
I think there will be a Octopus building project in my future... Well if you want some balls I'm your man, ha ha!! . OH JOHN ! 
|
|
|
|
|
|
|
They are a really useful tool aren't they? That Octopus looks very useful too. I love tools and just cannot get enough, probably the same as most people here. Being 90 degrees it is so much more convenient to use than a die grinder and at fifty quid or thereabouts excellent value. A great recommendation, thank you. Actually I suppose it is only half an octopus having only four arms but I don't know what else to call it. I don't use it a great deal but for certain jobs where two hands are better than one it is very useful.
|
|
|
|
|
|
|
I think there will be a Octopus building project in my future... Well if you want some balls I'm your man, ha ha!! Actually, I had to buy a box of them so there are plenty over and you are welcome to have what you need. I may have to take you up on that.  A bit of innuendo is not going to scare me away... 
|
|
|
|
|
|
|
Well if you want some balls I'm your man, ha ha!! Actually, I had to buy a box of them so there are plenty over and you are welcome to have what you need. I may have to take you up on that.  A bit of innuendo is not going to scare me away...  Funny thing, I think that at nearly 80 I can get away with saying anything but my daughter say, "No you can't dad"
|
|
|
|
|
|
|
I may have to take you up on that.  A bit of innuendo is not going to scare me away...  Funny thing, I think that at nearly 80 I can get away with saying anything but my daughter say, "No you can't dad" Haha. You can... I will P/M you about your balls...
|
|
|
|
|
|
|
tell your daughter we have the last say , and ,since we are your audience, yes you can say anything .
|
|
|
|
|
|
|
Funny thing, I think that at nearly 80 I can get away with saying anything but my daughter say, "No you can't dad" Haha. You can... I will P/M you about your balls... Thanks chaps for the carte blanche metalshaps many thanks for your PM. Reply sent. Cheers John
|
|
|
|
|
|
|
I only found this thread a couple of days ago and have spent a few hours reading the whole thing from start to finish. I'd like to thank you for making it such an enjoyable read. Interesting, educational and inspirational too. All captured in such a pleasant writing style that builds respect for what you do. I'll be following this one for sure, so keep up the great work John.
|
|
|
|
|
|
|
outstanding work. Can we all come round for lessons?
|
|
|
|
|
|
|
Haha. You can... I will P/M you about your balls... Thanks chaps for the carte blanche metalshaps many thanks for your PM. Reply sent. Cheers John You are very welcome and I'll be very pleased to help you in any way I can. It was some years ago now when I made the unit but I had to buy 50 bearings and only used 16 so I have enough for two more. The balls are 1 inch diameter and the material chrome steel which hasn't rusted. They TIG welded satisfactorily to the stainless rods but I think I had to run my welder pretty well flat out from memory.
|
|
|
|
|
|
|
I only found this thread a couple of days ago and have spent a few hours reading the whole thing from start to finish. I'd like to thank you for making it such an enjoyable read. Interesting, educational and inspirational too. All captured in such a pleasant writing style that builds respect for what you do. I'll be following this one for sure, so keep up the great work John. You chaps are real confidence boosters thank you so much. I'm really pleased that the thread has created the interest that it has and of course I am indebted to everybody who has contributed by way of advice and useful suggestions. Horrido's incredible artist's impression just blew me away when I first saw it being so close to the vision that I carried in my head and it really has given me a target to aspire to. Mind you, I shall have to punch way above my weight to achieve it that's for sure. legend Avatar legend legend24 minutes ago outstanding work. Can we all come round for lessons? Of course you can come round, I'd be delighted but I'm not sure how much you would learn. I make most of it up as I go along and if one method doesn't work I try something else. It's a jolly good job I'm not trying to make money out of it because I'd very soon be out of business. But the thing is, I love what I'm doing and producing a nice double curvature panel to me is something very special and hugely satisfying. I'm really pleased with the rear light housings and I know I've spent far too long on them tap tapping away with a hammer and dolly to bring up all the lows and make them as good as I can. But however much I try they will never meet the standards of the chap who I use to paint my cars. I remember when I took the Lightweight to him he walked all round it and said, "Well Bonnett, your metal work hasn't improved I see". I had a good laugh but I'm not sure he was joking, probably not. He is a perfectionist at what he does and I have a huge amount of respect for him and the standard of his workmanship. A real character and a good bloke to know.
|
|
|
|
|
|
|
The whole shrinking stretching and english wheeling looks so fascinating to me, I'd love to learn, it does look one of the most satisfying things to do
|
|
Last Edit: Jun 6, 2021 19:59:00 GMT by legend
|
|
|
|
|
The whole shrinking stretching and english wheeling looks so fascinating to me, I'd love to learn, it does look one of the most satisfying things to do Every English wheel should come with a government warning because metal shaping really is addictive. So be warned! I did gloss over forming a reverse curve when I made the first piece but I'll go into a bit more detail when I get to the one for the other side. I've just started welding the left hand piece to the light housing which already shows promise of a lovely curve in this part of the bodywork. It's fascinating how with the addition of each new piece the shape of the finished car reveals itself. 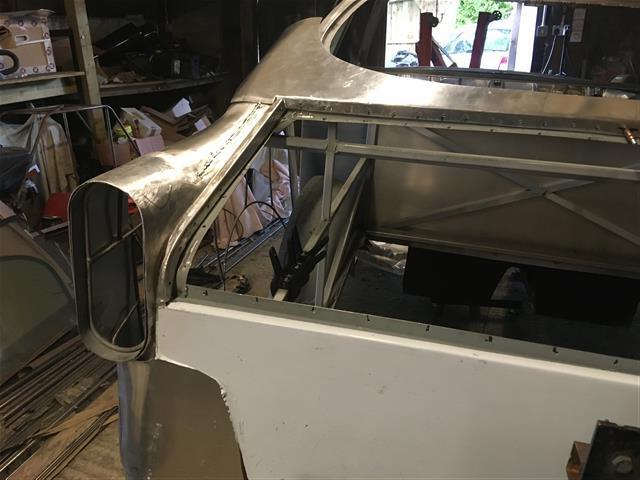
|
|
|
|
|
|
|
Well, today could have gone better but by the same token it could have gone a whole lot worse and by close of play the problem had been rectified and all was well. It still don't know how it could have happened but somehow I managed to bore two out of three 35mm holes for the rear lamps in the wrong place, not easy to do when the centres are marked through from a template. But wrong they were and measures needed to be taken. I scribed straight lines joining the three holes and cut the whole section out. It was then necessary to carefully shape a piece to fit the hole with no gaps if possible. Gaps mean more filler, more heat and an increased risk of distortion. I clamped the housing down on the surface table to try to keep everything flat and true and welded round. You can see from the height of the weld bead that the weld wasn't quite hot enough because of the huge amount of heat going into the table but it was good enough and after sanding it down we had an invisible mend. This time I was doubly cautious drilling the three holes and got it right this time. The Spire nuts that I got from Bresco are spot on which is very pleasing. 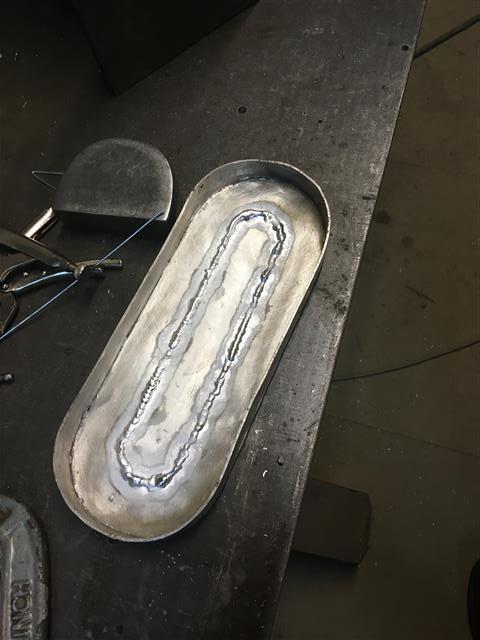 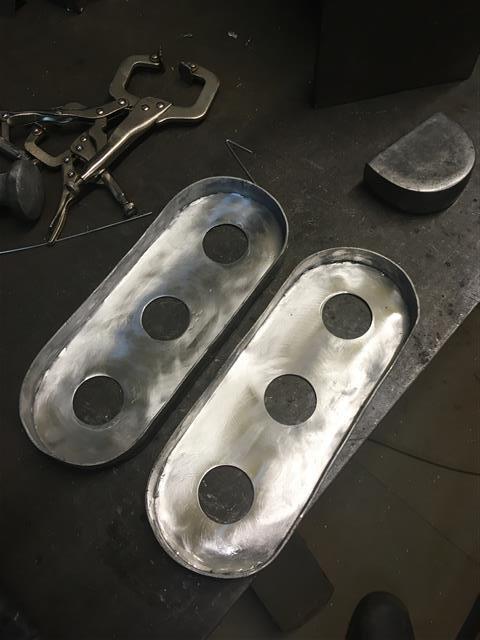 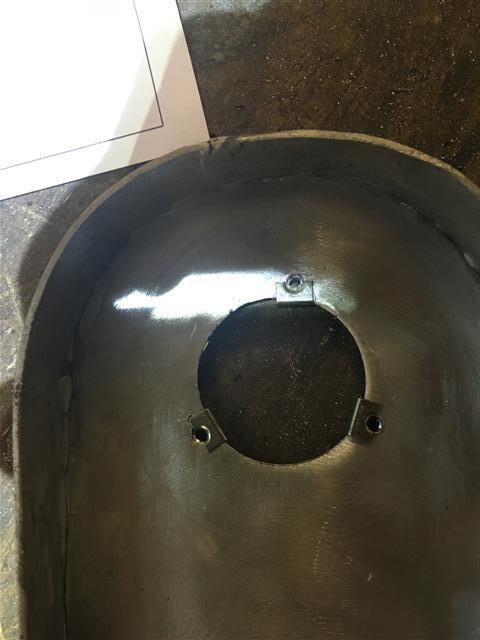 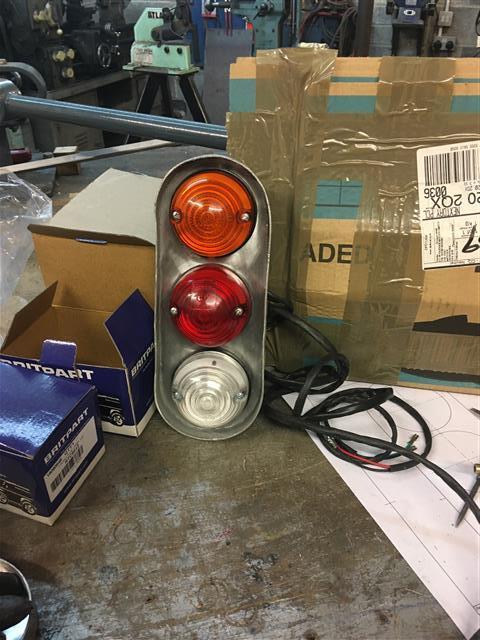 I set the lamps in by an arbitrary 20mm but having looked at the photo of the DB5 lamps, this does look a bit on the deep side so I may have to trim off 4 or 5mm from the flange which is going to be a pain. 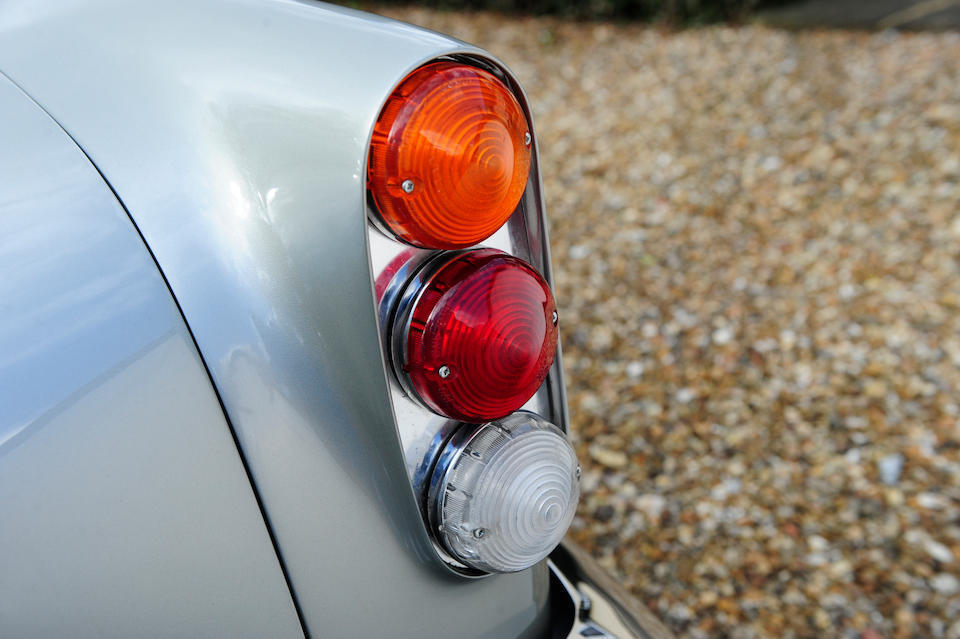
|
|
|
|
|
|
|
Ah, we've all been there!
Good save.
|
|
|
|
|
|
|
Looking good, could you not mount the lights on a 5mm alloy plate, you could then polish or anodise it.
|
|
|
|