|
|
Nov 23, 2017 21:58:37 GMT
|
i to use zinc primer and red lead , bare metaled everything zinced seam seal stone chip 2k paint , Nothing wrong with that - but I'm never surprised at what I see others doing - they get taken in by the claims that some of the product manufactures make - common one is slapping on a product that sets very hard - this is a foolish mistake has the harder the product the greater chance it will chip / fracture when hit by particles / road debris / stone chippings - underbody treatments need to be flexible / self healing - much like the stone chip that you have used.
|
|
|
|
|
|
|
Nov 23, 2017 22:24:36 GMT
|
Further surgery to deal with the rust ingress issues on the front inner sill Removed the forward sill section including the step Revealing this mess - inner sill repair to the left is reasonable & strong - it extends to the back of the drivers seat and just needs tidying up - section to the right is very poor and requires complete removal Repairs to the base of the A post closing panel / inner sill is also very poor Much careful chopping ensued Eventually Previous repairs although strong in some places but miserably weak in other areas - given the size of the mig bead around the repair areas they must have had the wire speed on the highest setting and it's a very hard bead to work / dress back The outrigger / jacking point has been replaced at some stage and is fine - I have had to remove the flanges from it and the floor area above it given the poor repairs around them - I will form and weld in new flanges as required
|
|
Last Edit: Nov 23, 2017 22:27:28 GMT by Deleted
|
|
|
|
Nov 23, 2017 22:34:50 GMT
|
When I did my Mk2 Cortina the crappy repairs were a bind. That front jacking point had been repaired 4 times with all of them just snobbed on top of the last. I attempted to unpick but in the end it was easier just to cut the section of floor out and start again. The whole car would have been done in half the time if it wasn't for the previous "repairs".
|
|
|
|
|
|
Nov 23, 2017 23:24:44 GMT
|
welcome to the real world of classic cars and RESTORATION , i always say when some one says , WHAT WILL IT COST me to restore ,
think of a figure . threble it . add half again ,plus 2k you ll be closer to the final price plus beer
|
|
Last Edit: Nov 23, 2017 23:25:20 GMT by shielsy68
|
|
|
|
Nov 24, 2017 22:52:19 GMT
|
Before proceeding much further I wanted to investigate on how good the repair section of the inner sill is Trimmed off the outer sill back to the B post Can of worms springs to mind Looks better once cleaned up However there is section of 100 mm beyond the previous repair that is weak and perforated, although the repair to the sill is strong with 1.3mm plate thickness - it is extensively rust pitted that reduces the plate thickness to less than half of this in places 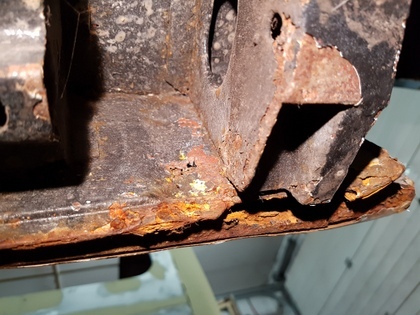 The rearward section of the inner sill is original and is good with exception of the area that abuts the rear jacking point The sills were the original and have done well to last the 50 years but have had several visits from a high density plastering team Although the forward section of the inner sill could be used - it's life is limited by the depth of the rust pitting - I can dress it and make it look ok, but is ok good enough ? obviously not has the plan is to chop it out - the problem is going to be avoiding any damage to the floor pan where the previous repairer has undertaken the welding to excess There is a non original return flange on to the floor pan that is part of the previous repair that will need to be removed in order to release the repair section - tricky little job but not a problem in the realm of things and have tackled far worse before today (I once had owner faint on me when he came to pay a visit and I had his car dissected like this one)
|
|
Last Edit: Nov 24, 2017 22:57:35 GMT by Deleted
|
|
|
|
Nov 24, 2017 23:10:08 GMT
|
Even with those repairs to remove, it's still not looking to bad. It's the same as all any old car the deeper you dig, the more you'll find to repair. At least the inner sills are really easy to remake as they are mostly flat with just the joddle near the bottom to fold. I'm looking forward to you welding something back in as all the cutting out is giving me flashbacks.
|
|
|
|
kenb
Part of things

Posts: 604
|
|
Nov 27, 2017 14:14:35 GMT
|
The same was done to mine both sides. Had to use a pattern sill on the passenger side though had a genuine panel for the offside. Not the front to rear curvature of the sill.
|
|
|
|
|
|
Nov 27, 2017 21:27:16 GMT
|
Drilled the spotwelds out on what was remaining of the original inner sill panel Which left a repair panel that was held on with about 3 times has much mig bead that was actually required Combination of a cutting disc on the angle grinder and some cold chisel action removed most of the panel What remained of the mig bead took some moving though - I was really cautious not to over thin the floor at all The flange edge of the floor pan having already seen previous work and for my liking is a little too narrow - the immediate edge is also a little weak - my plan is to replace the edge with a L shaped repair lapping 25mm into the floor pan and extending down 20mm to form the mating edge of the inner sill The outrigger will require new flanges - the old ones did not meet the inner sill face and just trapped rust Note the temporary support to the outriggers There is a ugly patch on the floor pan just above the outrigger and I shall replace this has matter of course whilst proceeding with the other repairs More tomorrow
|
|
Last Edit: Nov 27, 2017 21:48:06 GMT by Deleted
|
|
|
|
Nov 28, 2017 22:20:20 GMT
|
Peter had given me the heads up on the front jacking points basically their were non existent although it looks like it has jacking points attached to the side of the outrigger for a tube style factory jack 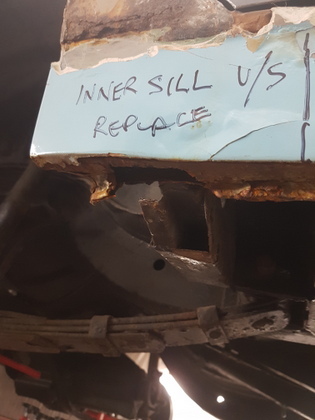 They are probably are a left over from the fact that the corsair was built on an extended Mk 1 Cortina floor pan - the factory jack for a Corsair has a locating pin The rear jacking points are intact and sound Locates thus The front outriggers had been replaced at some stage in the vehicles life and at that point it looks like the front jacking points were deleted - after talking it through with Peter we opted to modify the front outriggers slightly to accept the factory jack I made up a support sleeve from a bit of plate and welded a short length of 25mm box section to it Cleaned the inside of the outrigger up and welded the sleeve insitu - the floor pan is double skinned at this point and I managed to get a decent weld bead from the sleeve to the floor Then just drilled a locating hole to correspond in the outrigger underside Made up & trial fitted the new floor pan edge flange after removing the old one Utilised a combination of spot welding & mig to attach the flange Dressed back - I have the flange repairs for the outrigger ends cut & formed and have scribed the section up for the new inner sill so I should get that sorted tomorrow
|
|
Last Edit: Nov 28, 2017 22:20:56 GMT by Deleted
|
|
|
|
Nov 28, 2017 22:56:57 GMT
|
You give me inspiration to make sure I cut back the necessary rot and get to good metal when I think of future projects.....its not easy to comprehend the courage it takes to undergo this process, even though I have done the same thing on my own truck, but I seem to need to muster up courage every time I have the grinder in my hands!....
looks great!
JP
|
|
I know its spelled Norman Luxury Yacht, but its pronounced Throat Wobbler Mangrove!
|
|
vulgalour
Club Retro Rides Member
Posts: 7,120
Club RR Member Number: 146
|
|
Nov 29, 2017 13:36:59 GMT
|
You are not alone. That whole "but what if" of possible disastrous scenarios playing through your mind until you bully yourself into that first cut. Then you wonder what on earth you were worrying about as you start welding the repair piece in!
|
|
|
|
|
|
Nov 29, 2017 23:08:18 GMT
|
Sorted the end flanges for the centre outrigger Then did the repair section to the floorpan immediately above the outrigger - previously there was a ugly repair that overplated rust (seen adjacent in the image) - this was removed prior to the new repair going in - re-drilled the access hole to match the original Then did the flange ends for the front outrigger Made up the new inner sill and trial fitted it Checked that I could achieve a flush fit to the floor pan Then trial fitted the A post repair & bulkhead return panels Still some adjustments on the panels to make then I always like to make a few measurement checks prior to permanent welding
|
|
Last Edit: Nov 29, 2017 23:11:18 GMT by Deleted
|
|
|
|
|
thanks for showing the process...I can see where the car is getting its structure back again....giving everything the strength it needs. replacement panels look good from here!
JP
|
|
I know its spelled Norman Luxury Yacht, but its pronounced Throat Wobbler Mangrove!
|
|
|
|
|
thanks for showing the process...I can see where the car is getting its structure back again....giving everything the strength it needs. replacement panels look good from here! JP The panels are not too bad - a little work on the top flange for the bulkhead return and both the A post and the return panel will trimming back on the overlap / most forward face to allow the door hinge strengthening plates to be fixed - but I have seen and fitted far worse than this - I can even recall confining a repair panel to the scrap pile has it was such a poor fit and scratch made my own to replace it with
|
|
|
|
|
|
Nov 30, 2017 13:22:59 GMT
|
I hear ya,there...welding my sills on the truck, which were designed to be slip-ons, (just a quickie fix design welded bonded over compromised existing panels), I had to make quite a few modifications to get them to fit as replacements....so a combination of mindset there....
Do you have ideas of how these panels became compromised in the first place?
JP
|
|
I know its spelled Norman Luxury Yacht, but its pronounced Throat Wobbler Mangrove!
|
|
|
|
Nov 30, 2017 22:41:04 GMT
|
I hear ya,there...welding my sills on the truck, which were designed to be slip-ons, (just a quickie fix design welded bonded over compromised existing panels), I had to make quite a few modifications to get them to fit as replacements....so a combination of mindset there.... Do you have ideas of how these panels became compromised in the first place? JP It's a combination of poor quality fit from suppliers that don't care, some suppliers are sourcing from manufactures whose only concern is how cheap they can produce the parts hence lack any form of quality - combine that with poor storage and some repair panels are not worth fitting to start with - thankfully some of the UK market producers have stepped in with suppliers like Heritage, Magnum & Expressed to supply the market with good quality products - there are also quite a few specialist make / model specific that are supplying panels for the range that they support and some cases it's purely down to the owners clubs to source / commission & stock repair panels.
|
|
Last Edit: Nov 30, 2017 22:44:52 GMT by Deleted
|
|
|
|
|
I remember that most aftermarket mini panels were woefully thin and a rubbish fit.
|
|
Take the Next slot right coming up on the left.
|
|
|
|
|
After a careful checking of door aperture measurements the new inner sill was spot welded in Repair section for the bottom of the A post closing panel made up and let in Flange edge of the bulkhead is very weak - the upper flanges of the A post / bulkhead return panels affix to this Template and cut a new section 2 piece repair to ensure that I would not have a protruding weld bead that prevented a good fit of the outer wing at this point Both spot welded in - this will now allow for the joint between the new panel and the original bulkhead to be lead loaded and shaped in order to accept the outer wing with correct / matching radius profile at this point Then removed the outer A post skin from the door hinge reinforcing brackets To replace the A posts was a very wise decision on Peter's half - the amount of laminated / sandwiched rust between the plates and the outer A post skin had to be seen to be believed - pretty obvious that that the car had been suffering from water ingress above the hinges - there is small hole in the bulkhead but Peter also advised that it appeared that the windscreen had been leaking quite badly - things will now be slow over the coming week whilst I take break from the workshop to progress the kitchen (mammoth task) ready for the festive season.
|
|
Last Edit: Dec 1, 2017 22:19:05 GMT by Deleted
|
|
|
|
|
Amazing to see how quick you are doing these high quality repairs. The total amount of hours will still be high but very realistic. I did repairs to my Rover but it took me so much time adjusting/checking/aligning. If the A post is not fitted right one will face probelms later with panel gaps ect but i am pretty confident the repair panels you fit are oke. It is always a pleasure to read your posts and i enjoyed the shrinking video. I also made an attemp to straighten my rear wing but soon had the idea, i only caused more problems so left that to a pro. I may do another try with the next project whatever that may be.
Peter
|
|
|
|
matt311
Part of things

mk1 fiesta st170 zetec 5 speed conversion. 1967 1700 deluxe corsair restoration/modification.
Posts: 25
|
|
|
I have a 1967 1700 corsair that i am currently restoring, in many ways it is the same as your one. we have removed both wings and it has had repairs some of which can stay and some that definitely cant. I have uploaded some pictures in the reply after this one. you say the front panel is fibreglass? any idea where it came from? the front panel on mine has truly past the point of repair and we cannot find any replacements so far, as well as front wings which look like they will have to be repaired instead of replaced. otherwise we have remade the outriggers with some 50x50mm 2mm thick box section to add to the strength, and remade the sills from slightly thicker sheet to help with support. but any advice on where to find that front panel would be greatly appreciated. thanks matt
|
|
Last Edit: Dec 2, 2017 0:14:36 GMT by matt311
|
|