|
|
May 21, 2015 17:08:52 GMT
|
Anyway. I arrived at Schipol airport the following day. Had a 4 hour stop over. I had spent a fair amount of time searching the net in SA for parts and hadn't being paying much attention to the sites I normally monitor in Europe. So, with time to kill, that's what I did. It paid off! There had been an advert placed that morning. I emailed him and got his phone number. He sent more photos. We agreed on a price and I transferred the funds into his account. I arranged to have the parts collected, then caught my connecting flight back to the UK.
Next time I would see all the parts would be in a couple of months time. Still wondered if my ploy with customs would work, and what duty would be payable. I had a lot to do, needed to sort out my little garage and make space for the bits that would soon be on the water. The bits bought whilst still at the airport would take a little bit longer.
|
|
|
|
|
|
|
May 21, 2015 17:36:00 GMT
|
Taking a bit of a step back in time now. During the times when I was still undecided about carrying on due to finding more rust etc, I often left the car alone and had a bit of a tinker with the engine. Rotaries don't like to stand, the water seals give in, the apex and side seals seize and and the side plates can corrode because moisture condenses and it starts to rust. So, the engine will only be fully assembled once everything else is finished. That's not to say there wasn't anything to do.... First of all I wanted to lighten the rotors. So I measured it up and drew it. 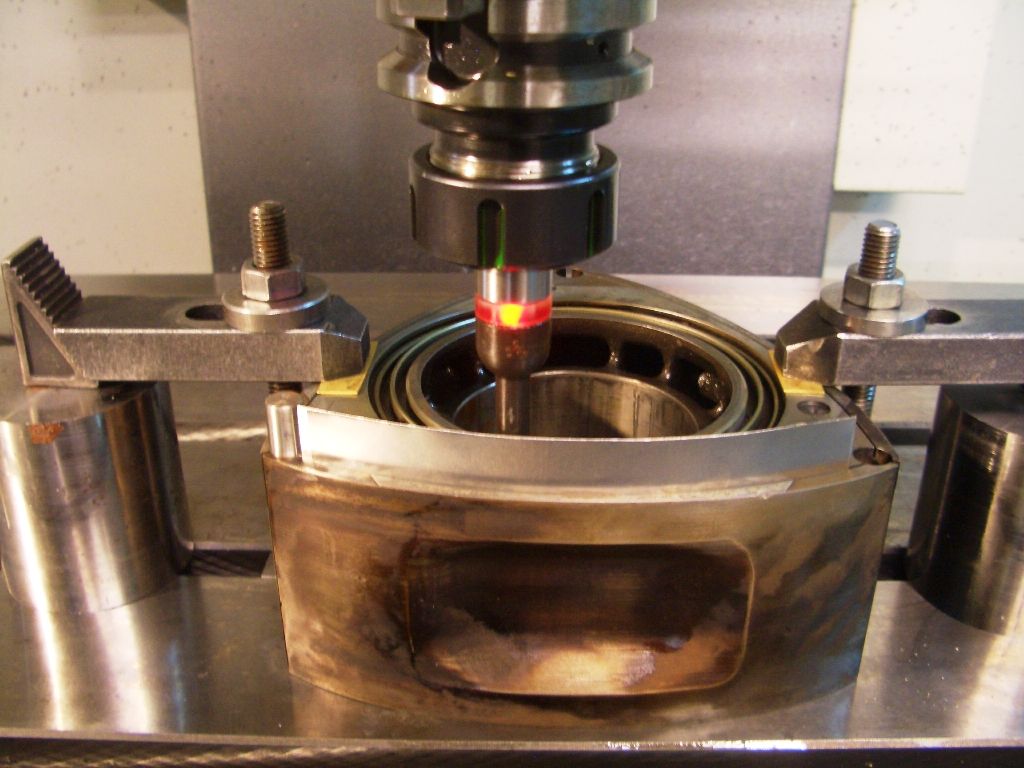 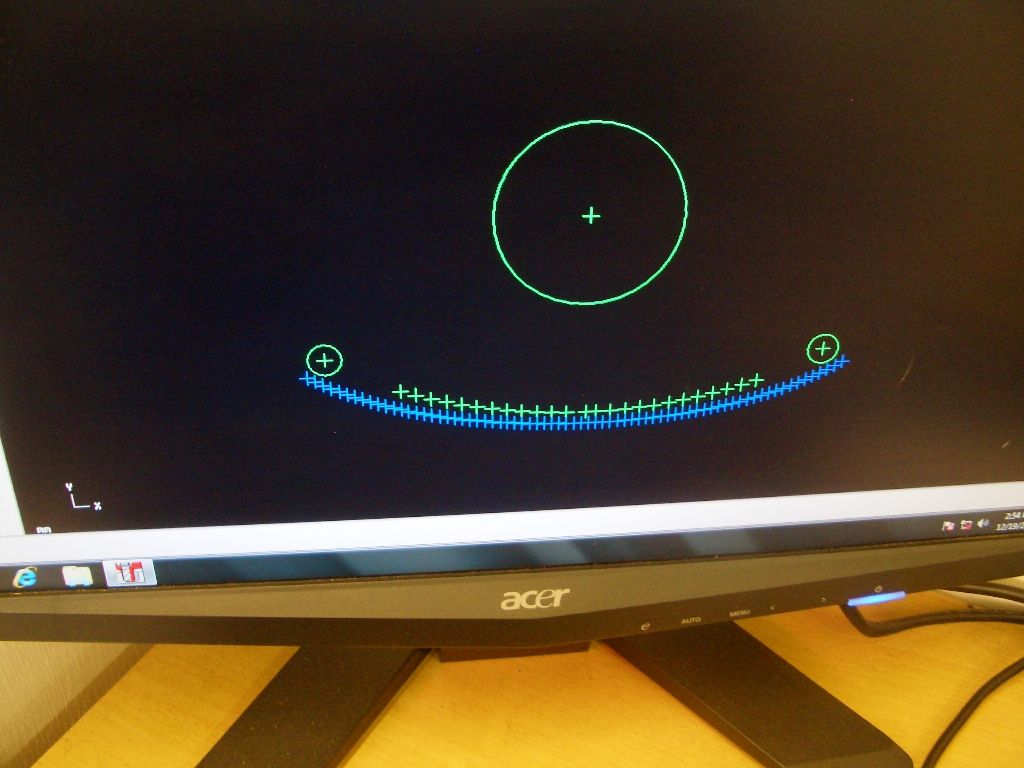 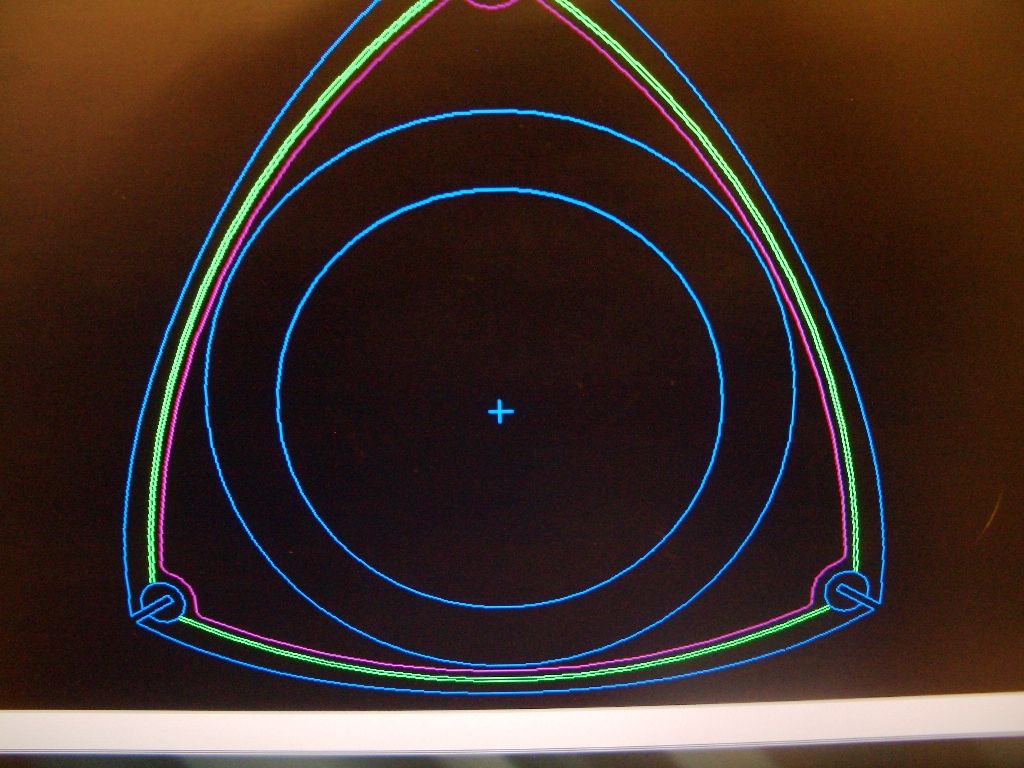 So first attempt 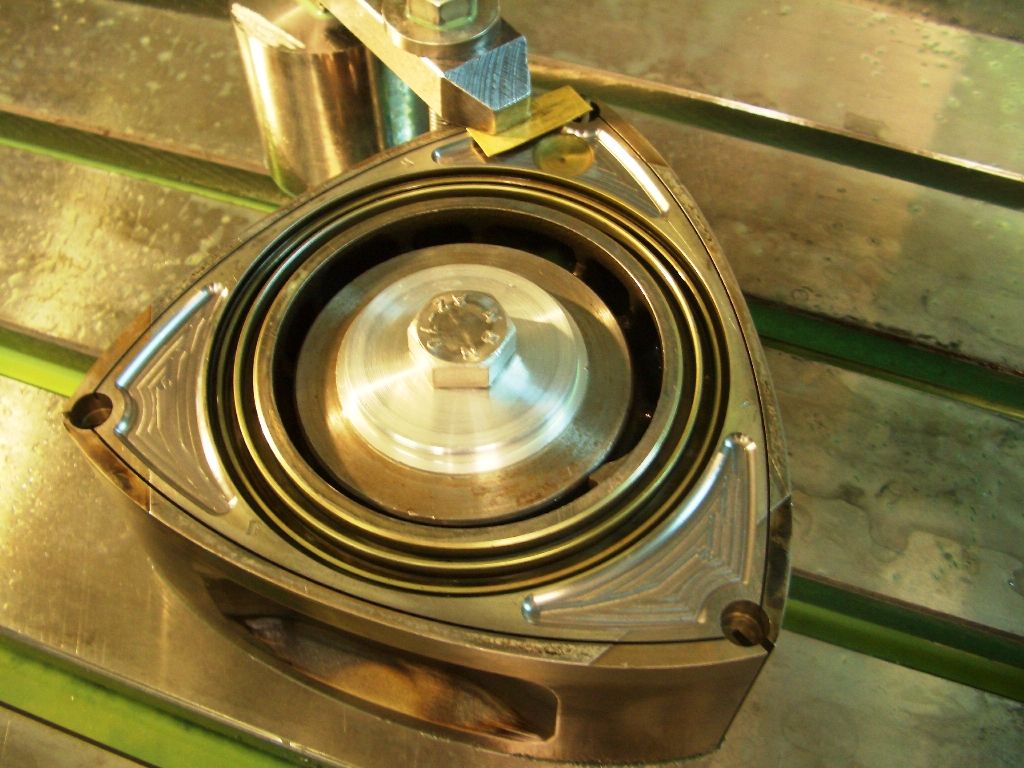 Decided I could take more out having cut a rotor in half to see how much meat there was 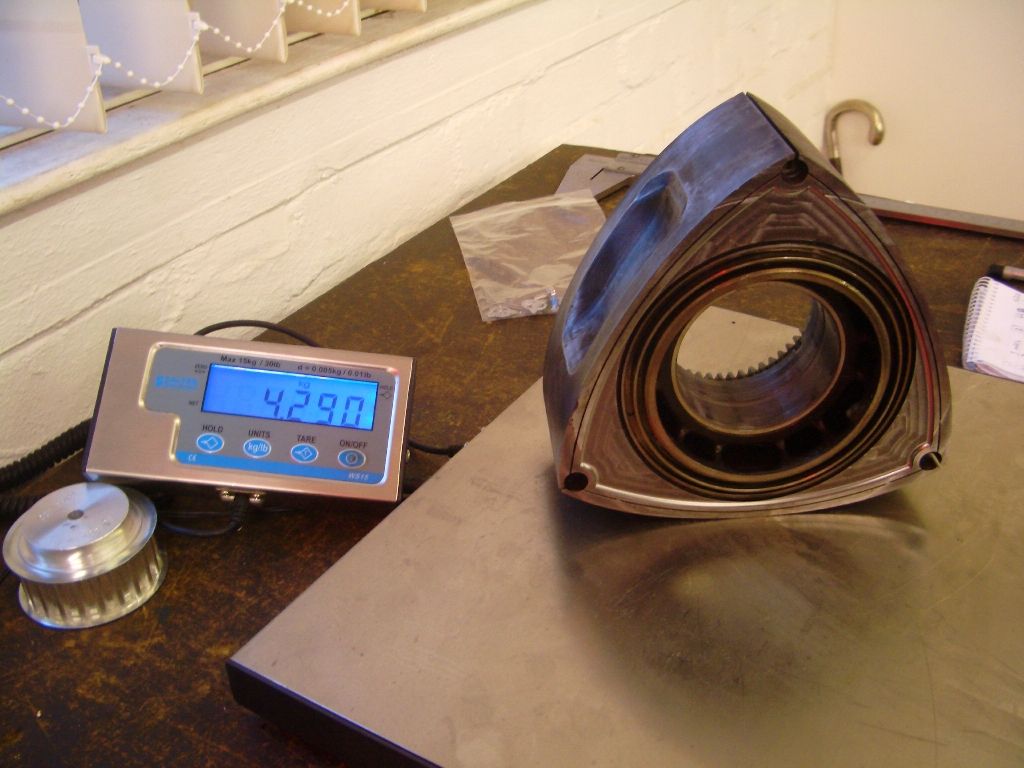 Also decided to do overall and tip clearancing at the same time. This helps with high Rev/ high boost applications.... 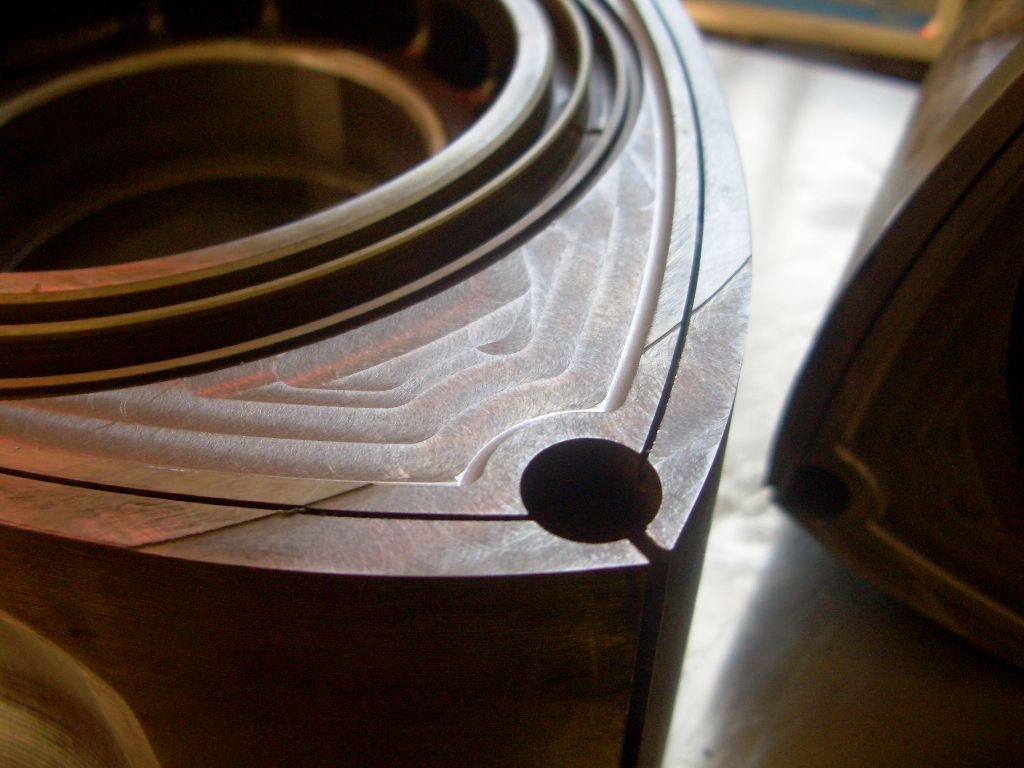
|
|
|
|
|
|
May 21, 2015 18:50:33 GMT
|
If I was going to build a bullet proof motor, there was work to do. I needed to measure a set of plates and draw them up  Found out where all the bolt holes were 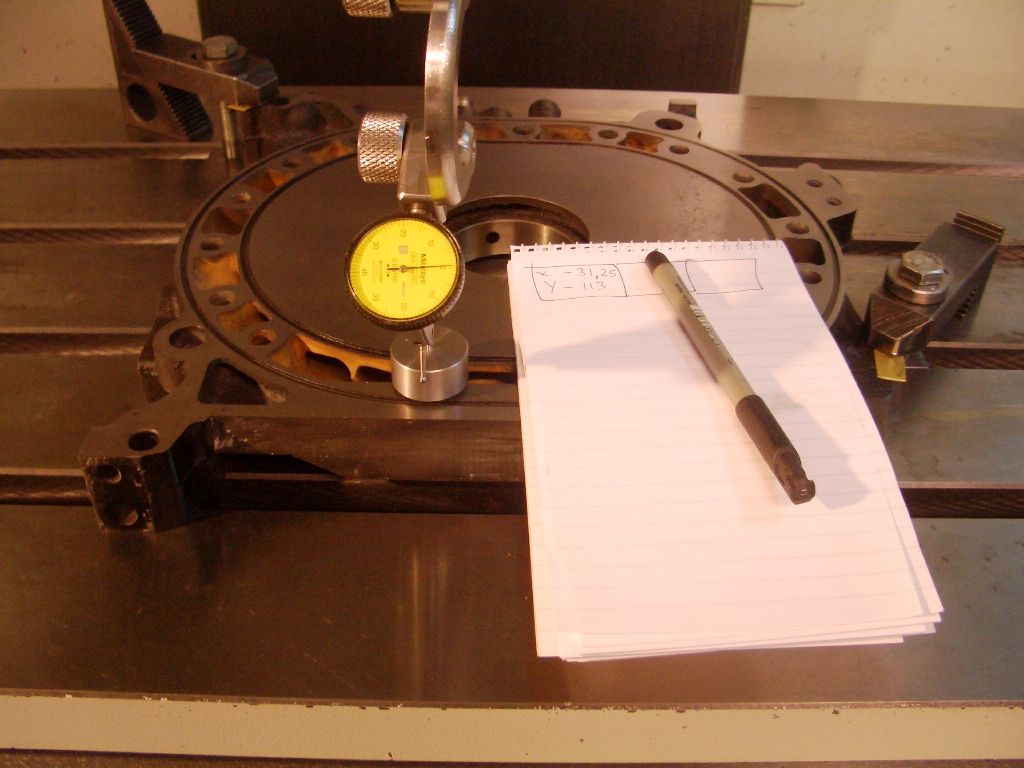 And drew it in Cad 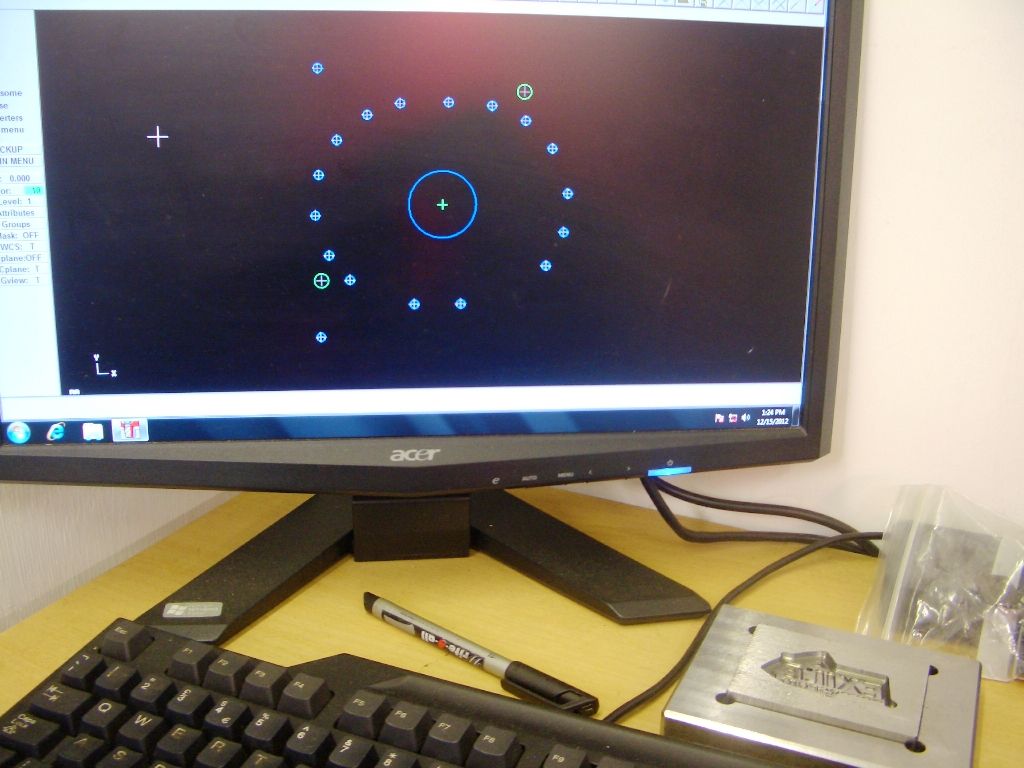 With that information now on hand, it was time to think about what approach to extra dowelling I would take. The easy way or the time consuming way.... Think you already know the answer to that.....
|
|
|
|
|
|
May 21, 2015 19:39:46 GMT
|
I used this info and hollow dowelled a motor 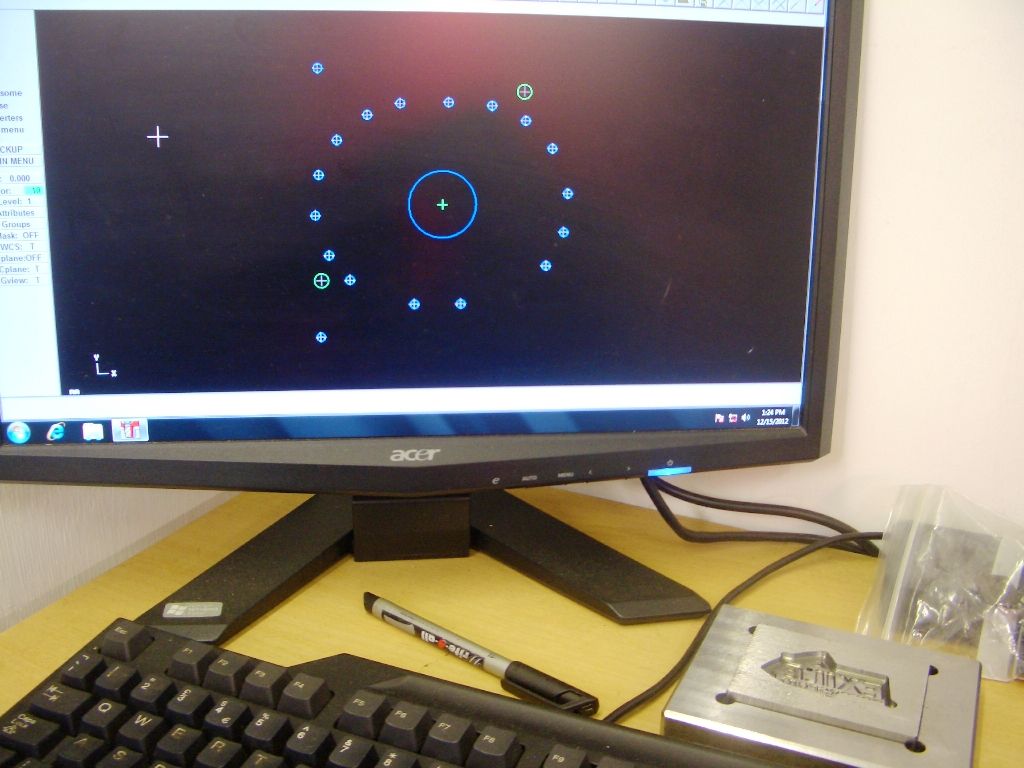 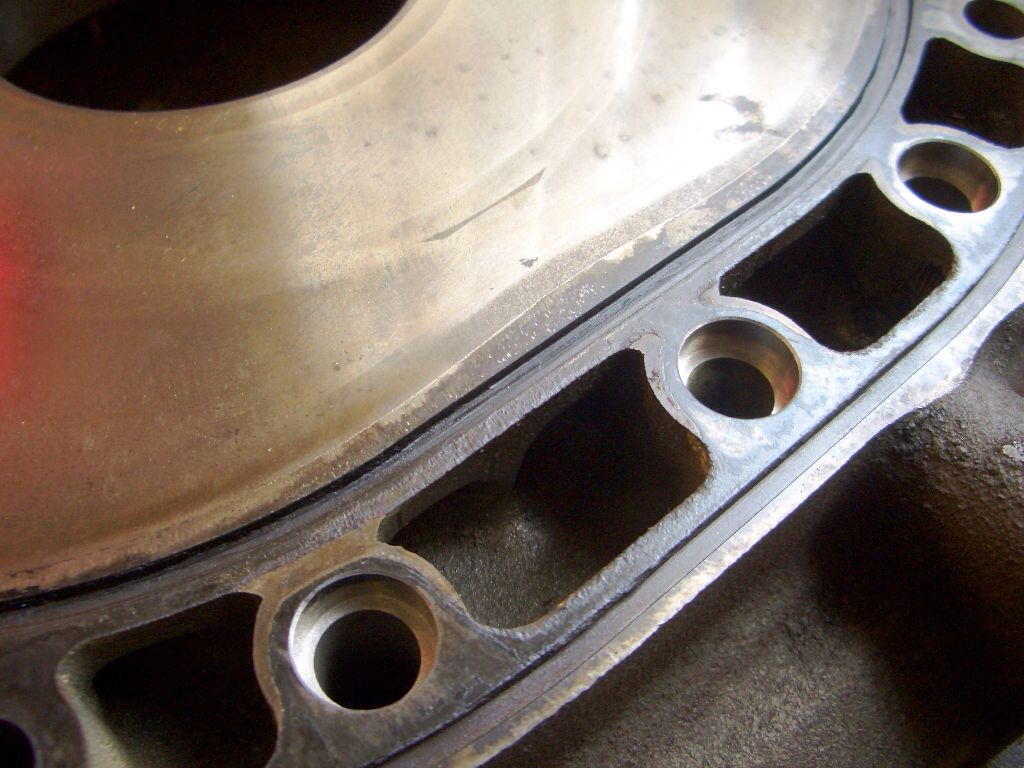 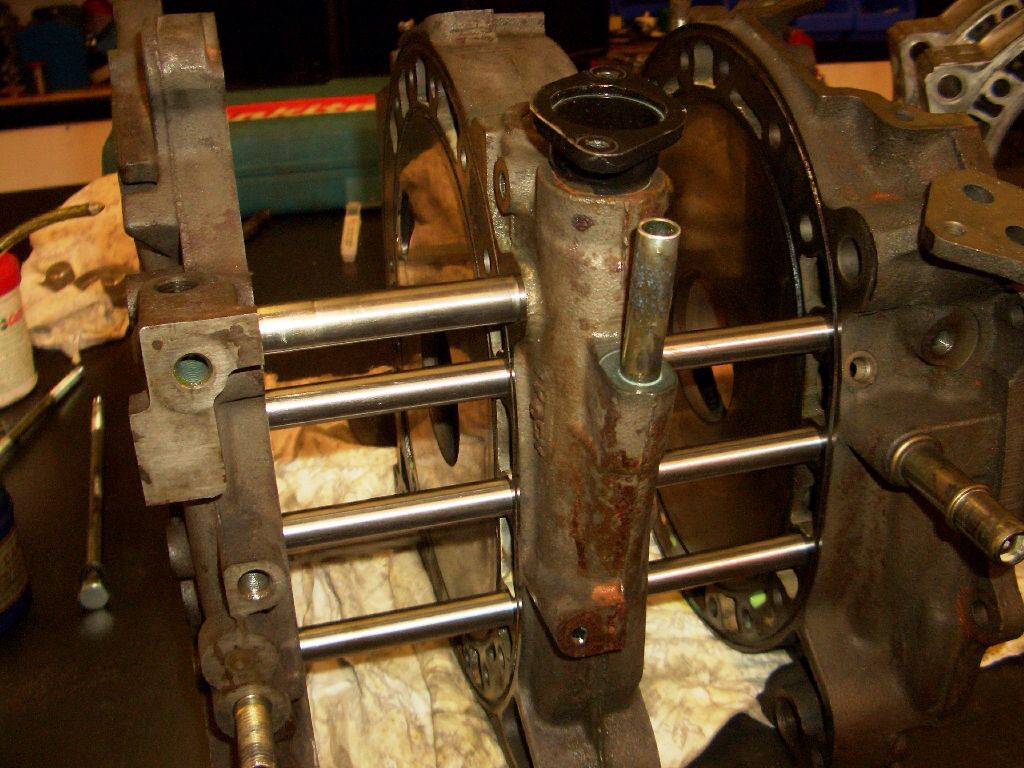 That's the fairly easy way. Decided against it. That motor was used in a circuit racing car for a season. Big Asthma pump, Motec engine management,dry sump ,all the bells and whistles. No expense spared, built by the top rotary engine builder in Europe. Had issues but stayed together, and numerous runs on the dyno developing over 640hp......on the wheels. On Owen Developments dyno. It proved a point.... My holes were in the right place, and accuracy/ fit was perfect....Pity it went to Aus as the problems were nearly sorted when it left....
|
|
Last Edit: May 21, 2015 19:45:44 GMT by Deleted
|
|
|
|
May 21, 2015 19:50:22 GMT
|
Decided on the hard way. High tensile studs all the way round. All holes machined to suit. It goes together like a Swiss watch. Can't wait for bodywork to be finished... Motivational.... 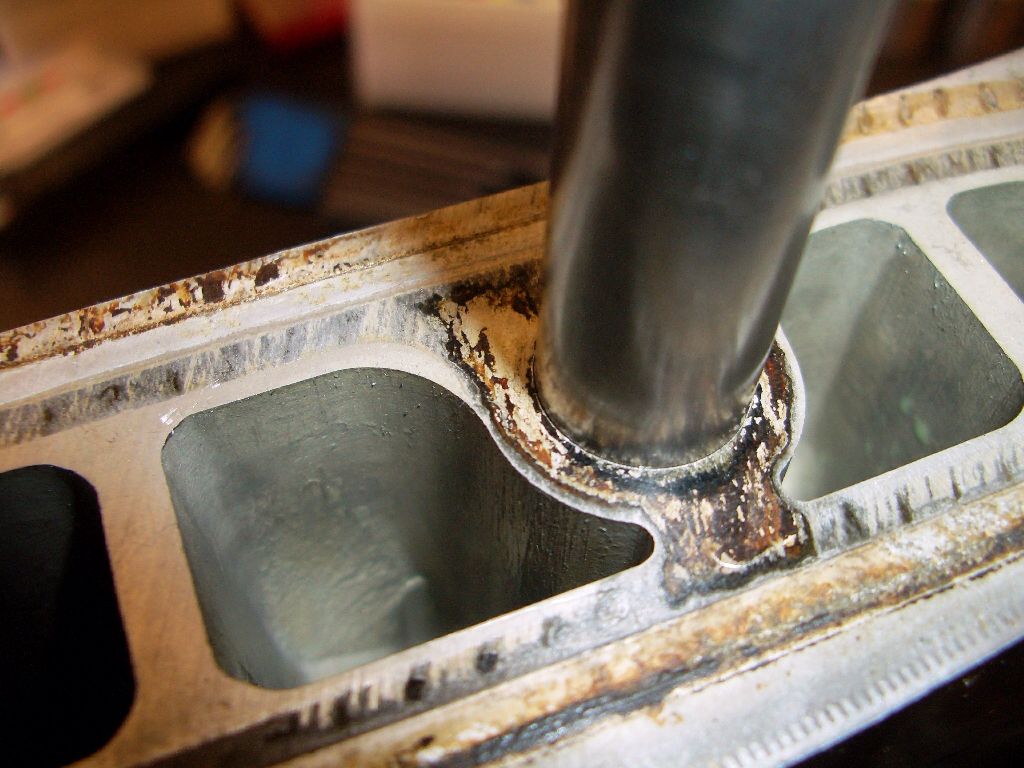 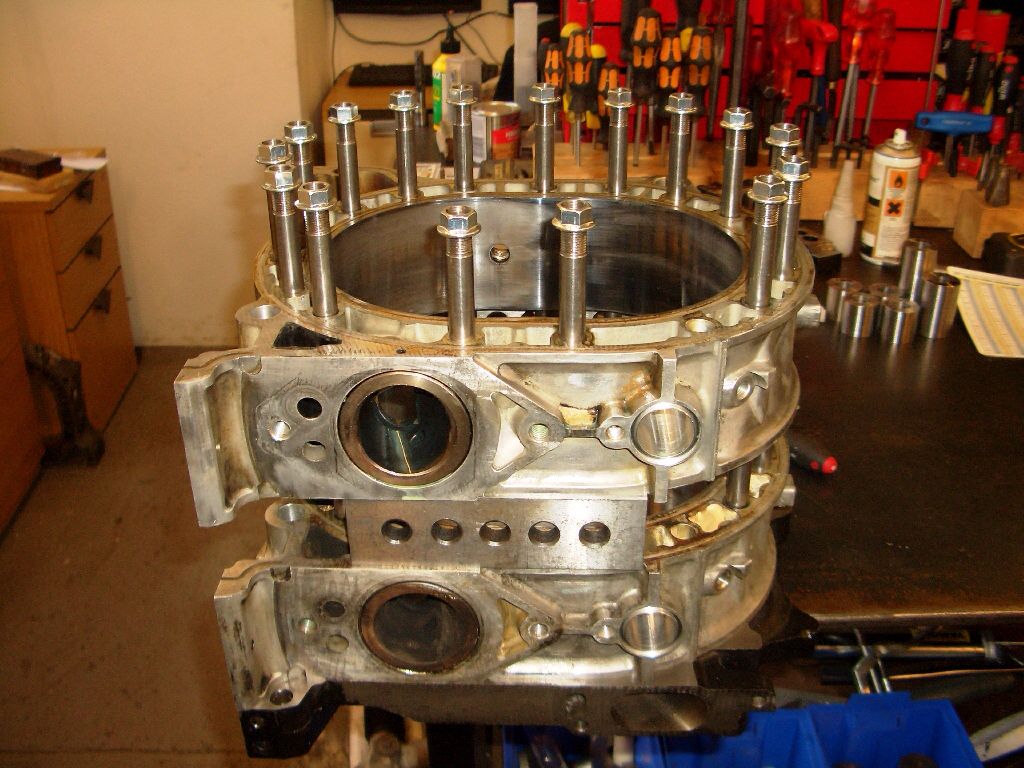
|
|
|
|
|
|
May 21, 2015 20:38:39 GMT
|
Have seen rotaries run in oval sprint cars in New Zealand, they sound insane and make unfeasible amounts of power. Can I ask what you do for a living you seem to have access to an awesome amount of toys at work  Looking forwards to your updates
|
|
|
|
|
|
|
Have seen rotaries run in oval sprint cars in New Zealand, they sound insane and make unfeasible amounts of power. Can I ask what you do for a living you seem to have access to an awesome amount of toys at work  Looking forwards to your updates I run the machineshop for an Engineering company in Kent. We have a very varied customer base, do a lot of stainless steel work. Our customers include a well know brand of Rice, a well known bakery, water/ effluent treatment companies. A very large bottling company, company that makes roof tiles,one that does building blocks, one that does yogurt. So very varied. I even do work for the biggest cannabis plantation in Europe.....all legal. They have spent millions on developing a drug for multiple sclerosis, which is looking very positive. Also have two customers that rebuild Second World War tanks, so get some cool projects to work on. Only downside with having the car there is often weeks go by when all machines are running and I can't get any machine time for myself. Also workshop not always available at the weekends. So, sometimes it may seem like I am chopping and changing on the car a lot, you need to bear the above in mind. If I can't get machine time, I draw parts up ready for machining. Sometimes their will be a gap and I will do a lot of machining in one go. It can be very frustrating, but well worth it as its a perk of the job that many would kill for. It makes it worth working for this company. I am very fortunate 
|
|
Last Edit: May 22, 2015 4:39:41 GMT by Deleted: iPad can't spell, poxy thing...
|
|
|
|
|
So a major tidy up happened. I drilled out some spotwelds 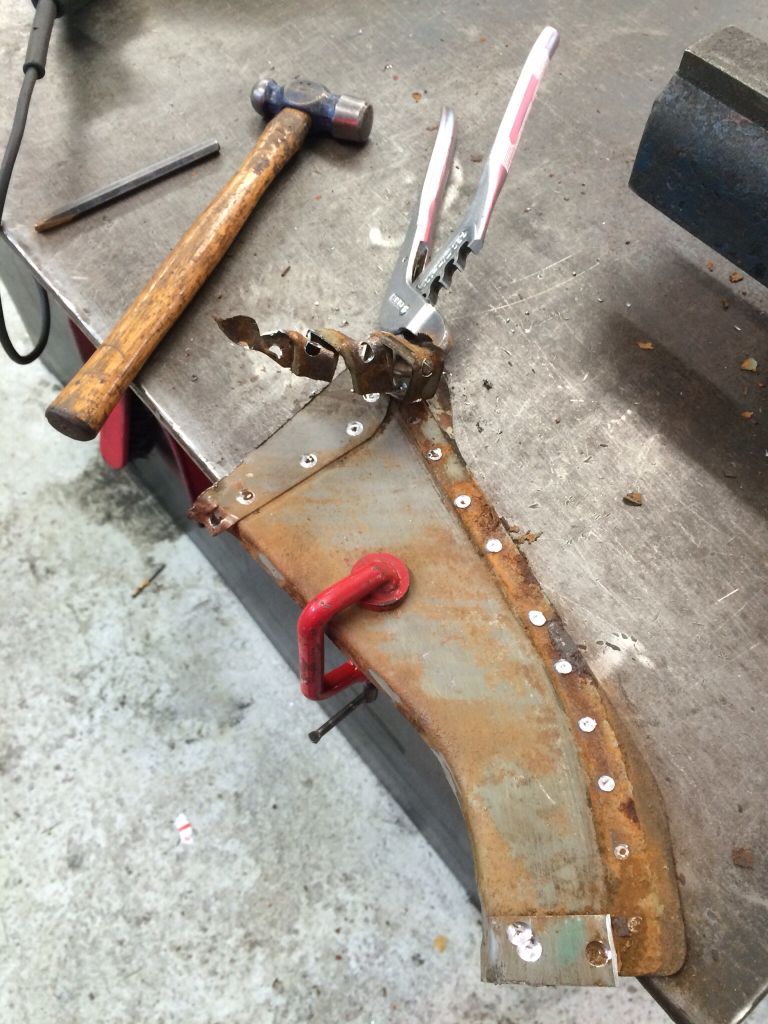 That's all that was worth keeping from the yellow front cut from Holland, along with the windscreen scuttle panel 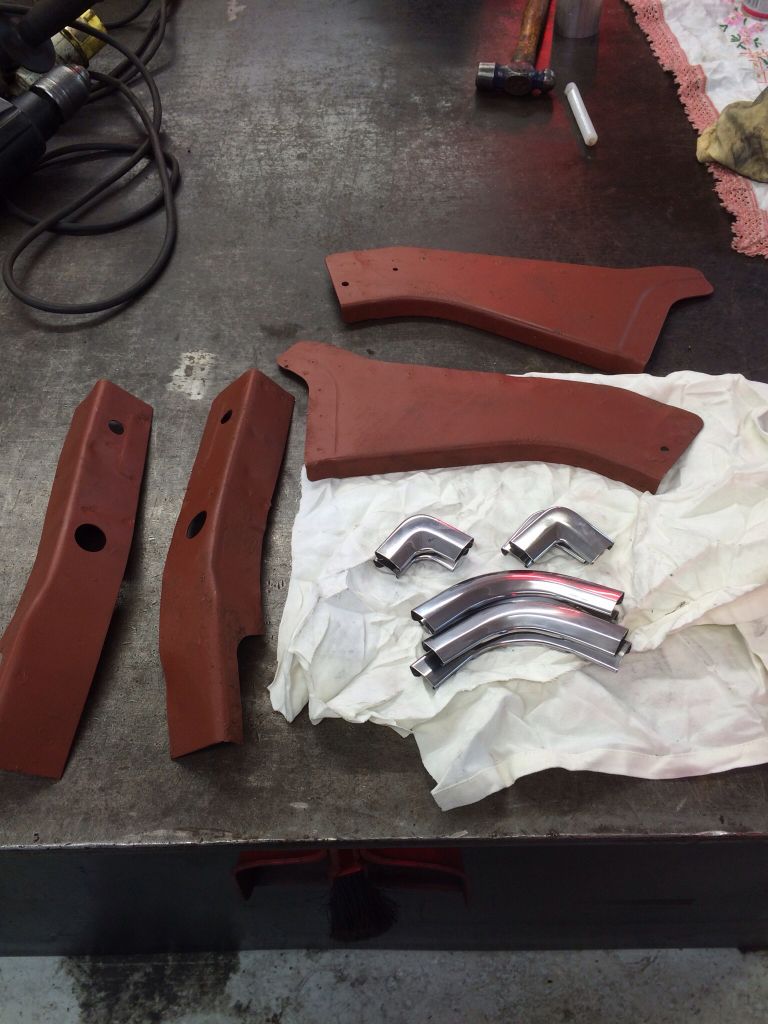 The beadings were the ones that came back in my hand luggage from SA. They polished up a treat. All the beadings are stainless steel,a metal I know how to talk to ! 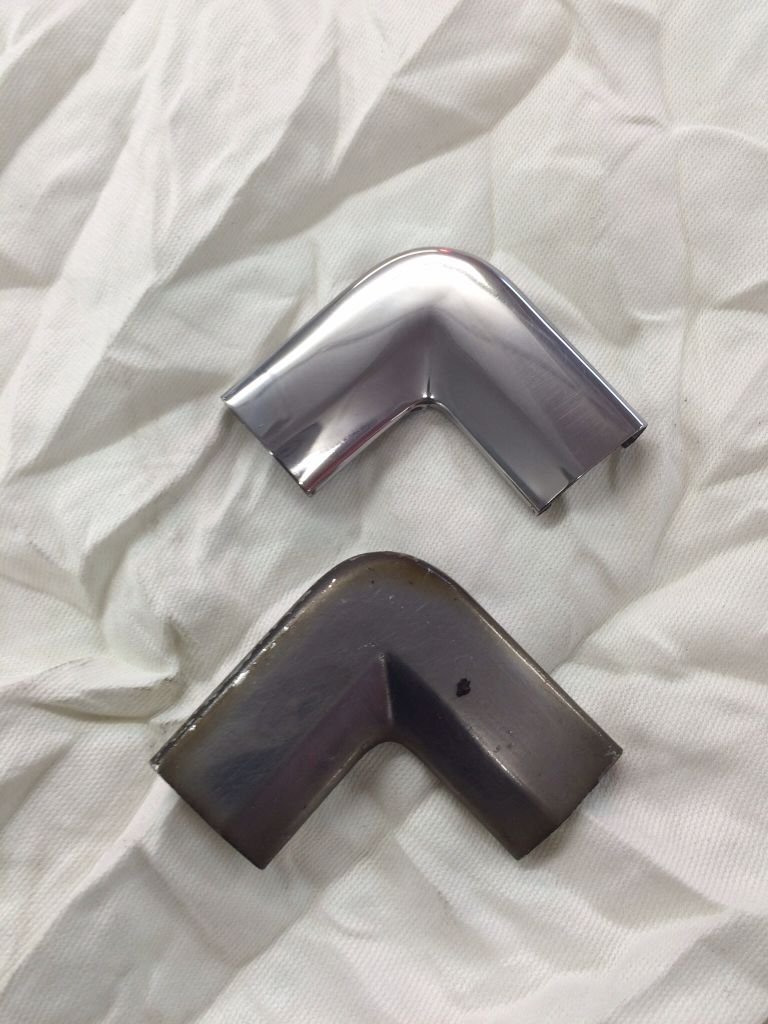
|
|
|
|
|
|
|
Had come up with a plan. Car would involve a lot more work than initial thought it would. The dolly arrangement wasn't ideal ,neither was the rotisserie. I needed to cut the front of the car off that would be front wheels and the mounting point for the rotisserie gone. Put it up again and had a good look 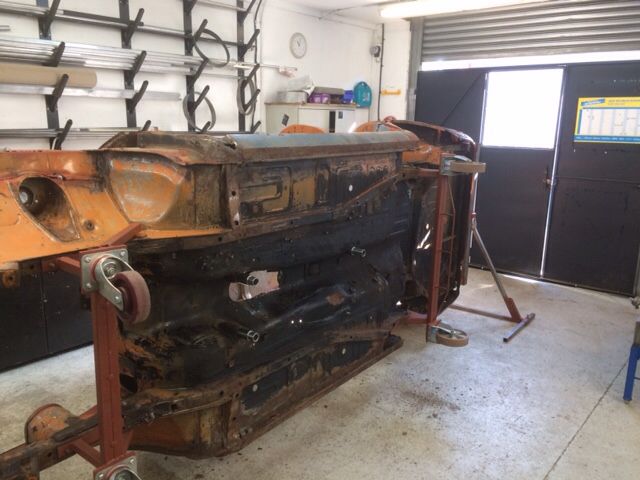 Decided that this needed to have a main structural backbone added to it, as once the sills and the side panels had been removed,it would have the structural rigidity of wet toilet paper. It doesn't help that the car needs to be moved back to the garage after each acupuncture session in my workshop, so what ensued may well be over the top, but belt and braces and all that. I decided on making a sturdy frame that would remain bolted on at all times. The wheels would be attached to this. I would brace up the boot and firewall,make a new rotisserie and brace up the door openings. Looked for door bracing or door restraints on the Internet. NOT a good idea. Most looked like all good fun,but seemed to involve scantily dressed ladies,lol. Door bracing needed to be remove able,so welding was out. Came up with a bolt in system that could be removed in part,but would always go back in in exactly the same place. 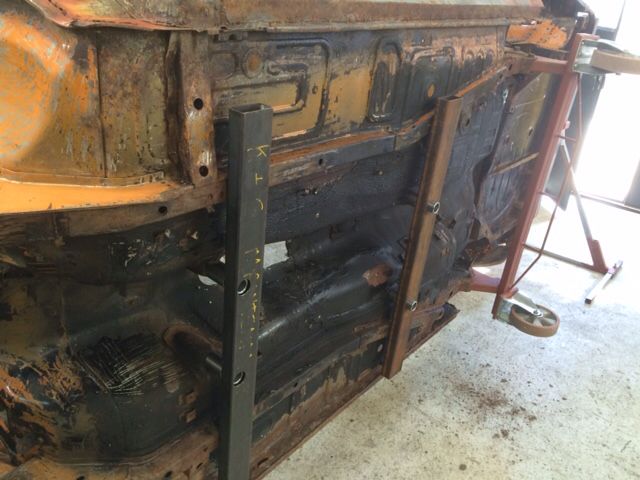 Then had 6 tonnes of 40mm square bar delivered.... For a customer job,lol, so that was workshop space over until it had all been cut and stacked away ready for machining. And we were flat out busy....Plan was to fabricate as much as possible in the next couple of weeks, and then weld it all together over the Easter weekend.
|
|
|
|
|
|
|
|
|
Last Edit: May 22, 2015 4:46:05 GMT by Deleted
|
|
|
|
|
Lathe became available so made the tie bar ends 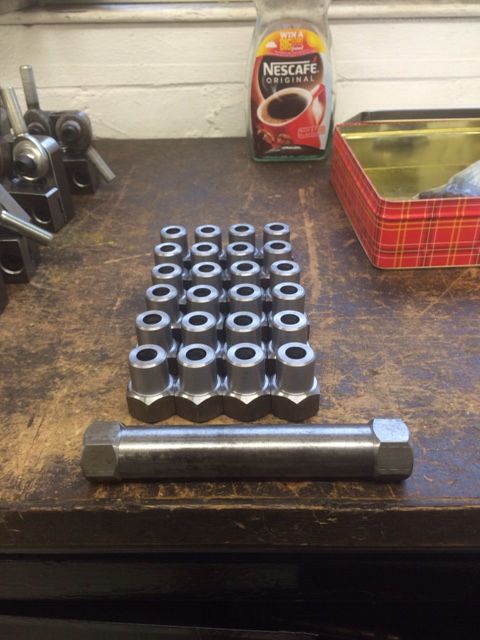 Decide to use cheap rose joints on either end,as no point fannying about making couplings when you can buy a perfectly suitable on for around 3 squids. Made bits for the firewall 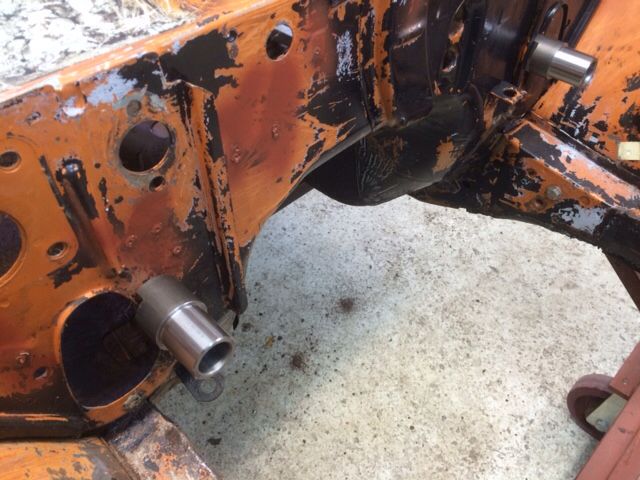 Bits to brace up on the inside of the firewall 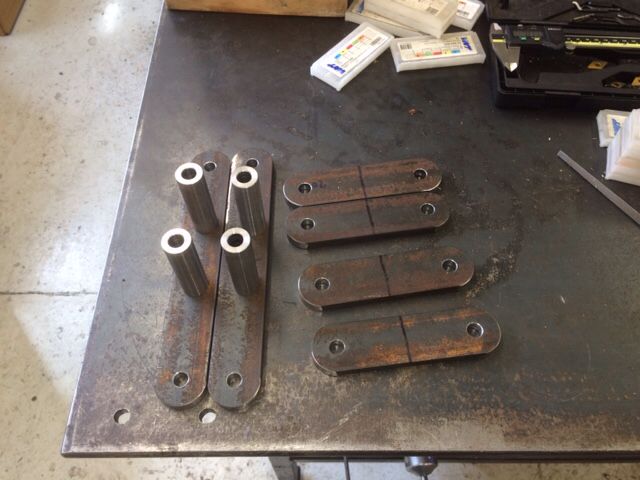 Started on the bracing in the boot 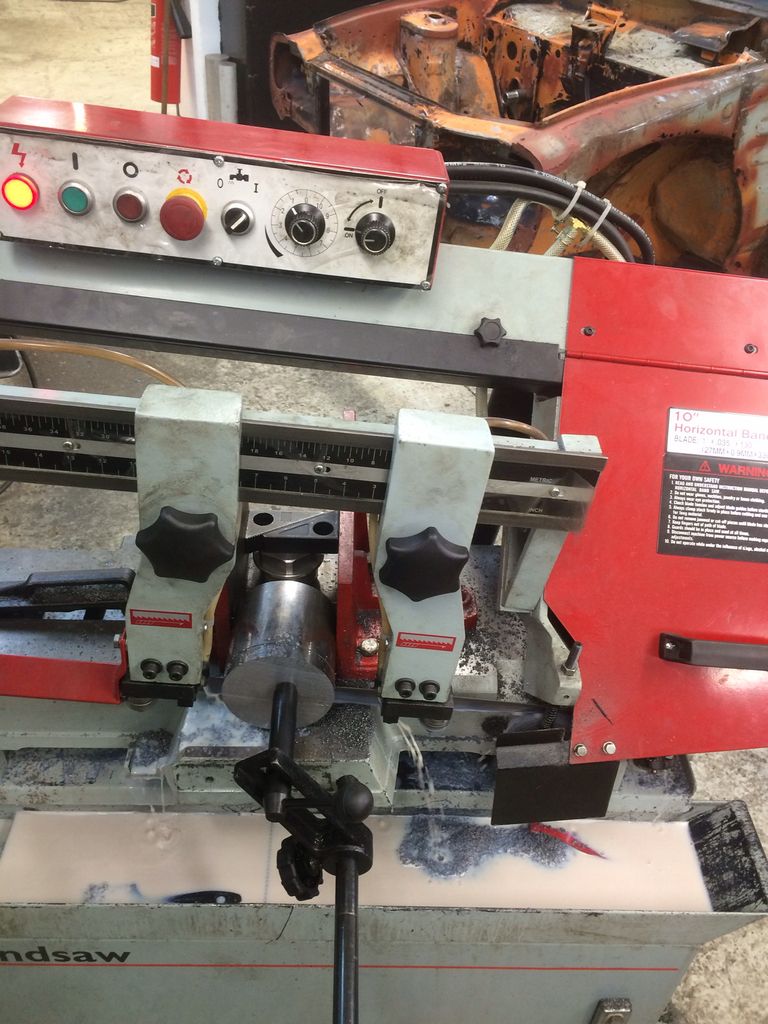 These would bolt onto the shock turrets. 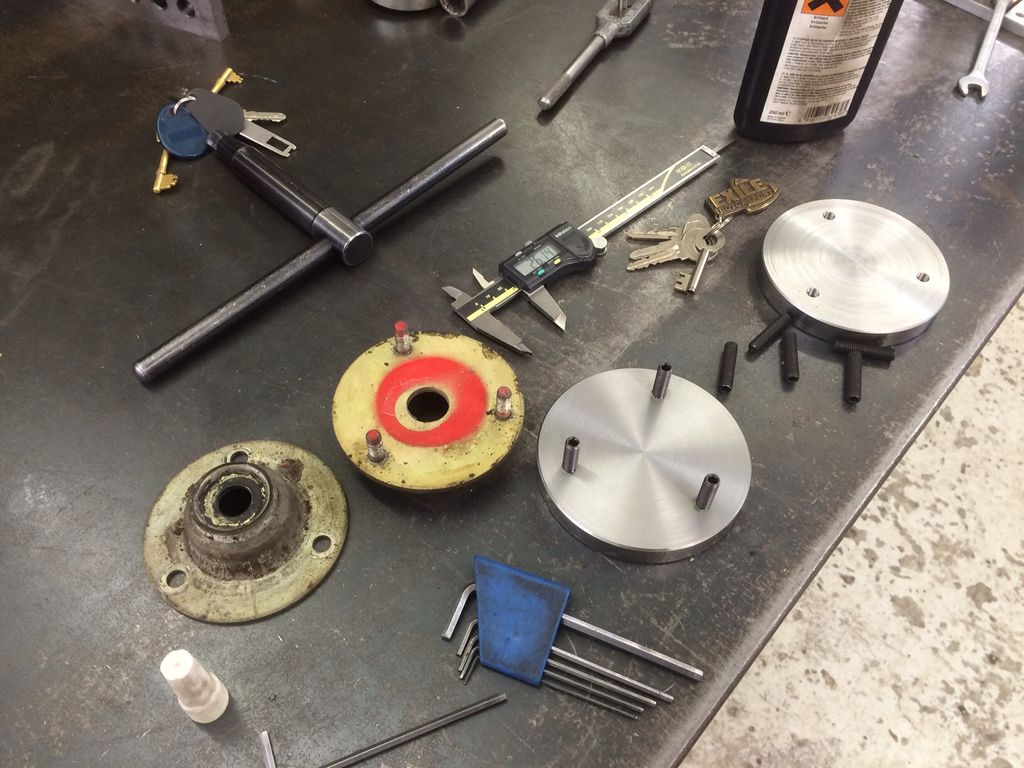 These would attach to the frame and the existing wheels would be bolted on. 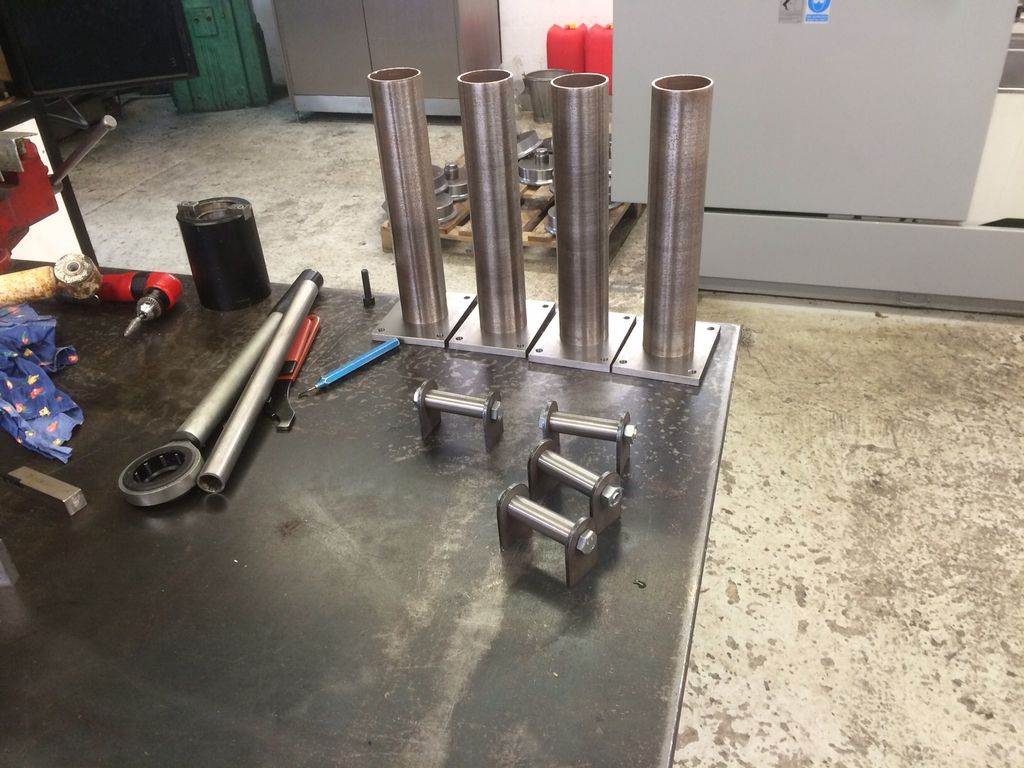 Basically machined up as much as I could, ready for the bank holiday weekend.
|
|
|
|
|
|
|
Dry fitted the bracing,cut all the tubes ready for welding over the bank holiday weekend. 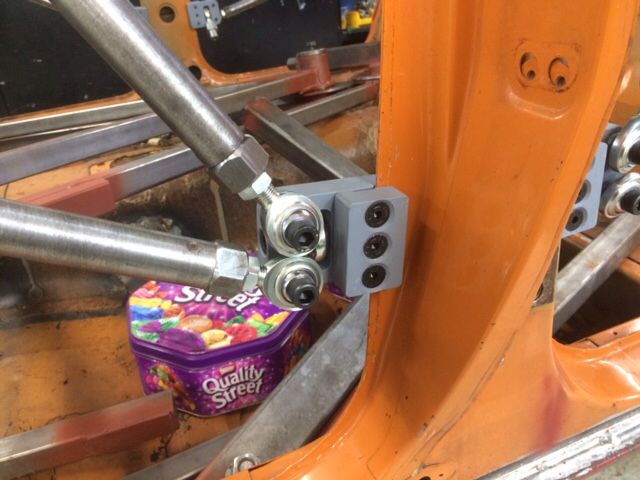 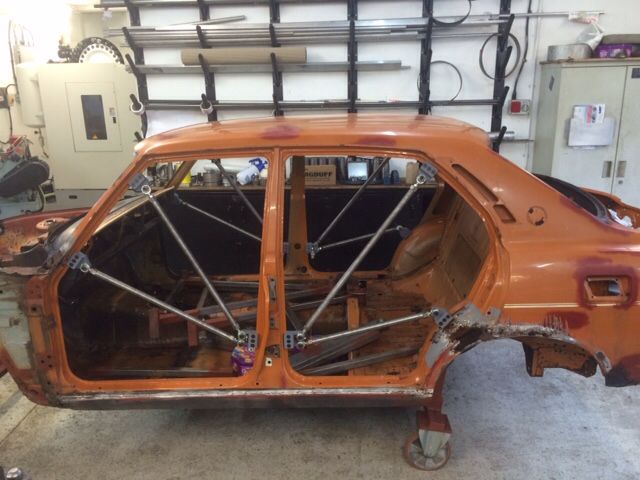 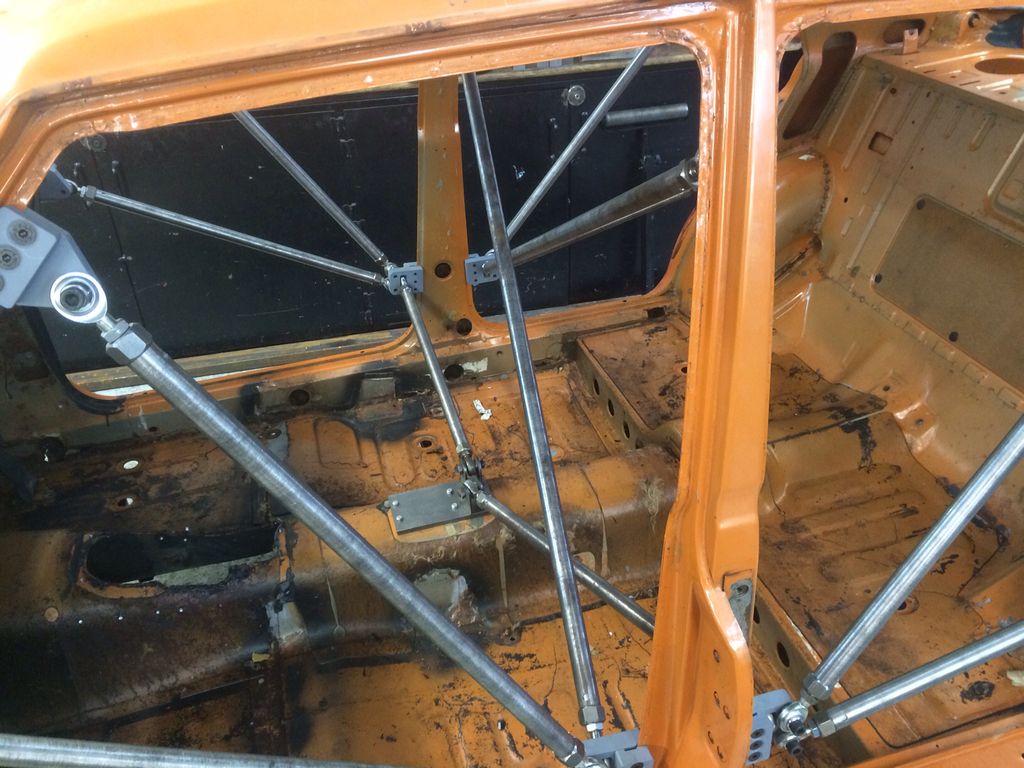 Bank holiday was still a week away. Found some cheap alloys on the Bay of Flea. Gave them a well needed polish... Ok, iis it cheating a little bit? Not in my book... It's called working smarter,not harder, hahaha. 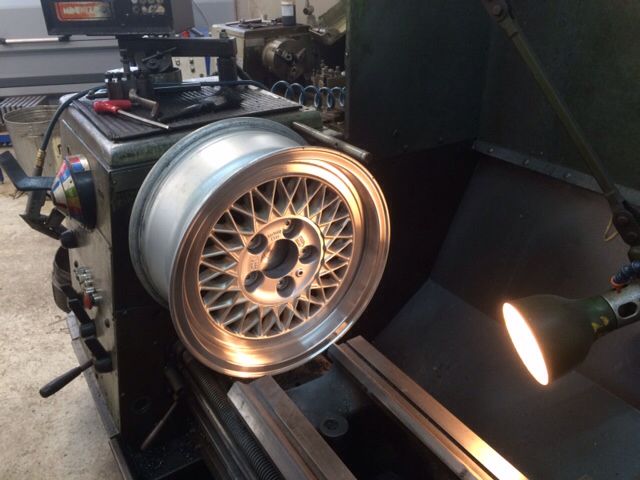 Not bad for a £60 set of alloys.... 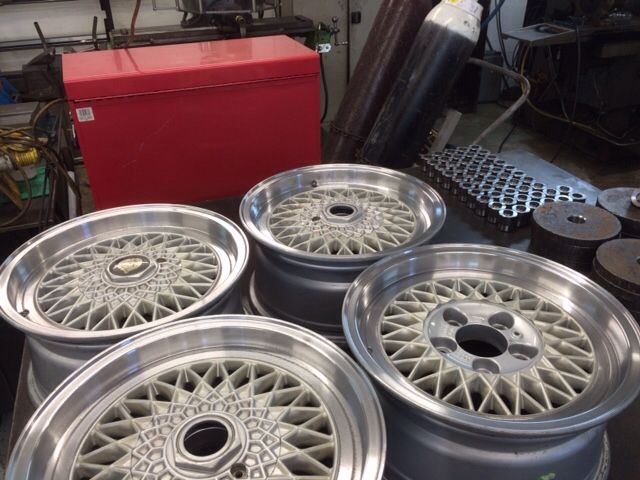 All the centre caps were there too. Result. Was running out of things to do. Made a list of things to do over the Easter weekend. 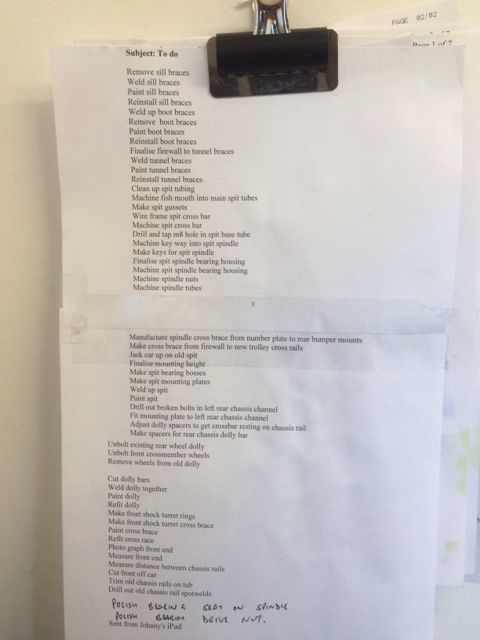 All set for the weekend. What could possibly go wrong with so much planning and forethought? What could go wrong indeed.....
|
|
|
|
smeden
Part of things

"Full throttle until you see God,then shift to second"
Posts: 356
|
|
|
This is Like all my favorit show's in one place! :-)
|
|
Jaguar xj6 S1 swb manual VW Bay Camper Audi A3 1998 1.8 VW Beach Buggy (sold) Ford Mondeo mrk I RS Celebration (written off) Ford Escort Mrk II RS 2000 (rust in peace)
|
|
v8ian
Posted a lot
 
Posts: 3,832
|
|
|
I'm liking this, I wish the machine shop I work in was as well tooled up at yours  I love the bracing of the shell, it does offer a amount of adjustment, I would be worried about when the struts are tensioned and the shell would move when the floor etc is cut, Might be me being over cautious, would the diagonals coming off the tunnel and top of B post be better mounted between the between the 2 clamps avoiding the possibility of the b post twisting? I have worked in a large Bottling plant is probably by Crittals Roundabout, and a spin off sub from a Tile company in Lenham,
|
|
Atmo V8 Power . No slicks , No gas + No bits missing . Doing it in style. Austin A35van, very different------- but still doing it in style, going to be a funmoble
|
|
|
|
|
Struts have left hand thread one end , right hand the other. There is zero play between the bolt and the rose joint as I sleeved 1/2" ball joints to suit M10 bolts. The struts are adjusted with no tension on them, you can take the bolt out easily and no wiggling required to get it back in. Front of right B pillar tied to tunnel and rear tied to top of left side B pillar. How will that twist  Only remove one sill at the time. Left B pillar tied in the opposite way , front tied to top right B pillar and rear tied to tunnel. Possibly not that noticeable in photo !
|
|
|
|
|
|
|
Not sure how unhappy face appeared. Was supposed to be a question mark. Pity phone isn't metal or I could beat it savagely with a hammer and knock some sense into it , lol
|
|
|
|
frosty
Part of things

Posts: 120
|
|
|
THIS IS EPIC!!
Bookmarked and eagerly awaiting more updates.
With the quality of work gone into the tools and bracing, I seriously can't wait to see how the fabrication and work on the car goes!!!
This is one awesome project and hats off to you for all your skills and knowledge.
|
|
1970 MGB GT 3.9 V8 efi Sebring
2007 Audi A3 Sport (Diesel)
|
|
|
|
May 22, 2015 11:06:09 GMT
|
probably the most thorough job on bracing i've ever seen. lets hope the shell was square in the first place  where abouts in kent is the business btw ?
|
|
|
|
|
|
May 22, 2015 15:22:08 GMT
|
What a well wrote out thread, had to sign up to post. And to add this to my bookmarks.
|
|
|
|
|
|
May 22, 2015 16:21:08 GMT
|
probably the most thorough job on bracing i've ever seen. lets hope the shell was square in the first place  where abouts in kent is the business btw ? Work isn't far from Maidstone Square? What's that? Think you have lost the plot. We are talking 1970's Mazda here....They didn't do square and they didn't charge extra for the panel gaps that you could stash your yellow pages in either 
|
|
|
|