|
|
|
Started with plan b. I had a brilliant idea awhile back. Thought that was novel. Turns out some dude way before granny fell off the bus had the same idea. So much for that,haha. Anyway, what it all centred around were the pucker marks here, and how to stop them forming 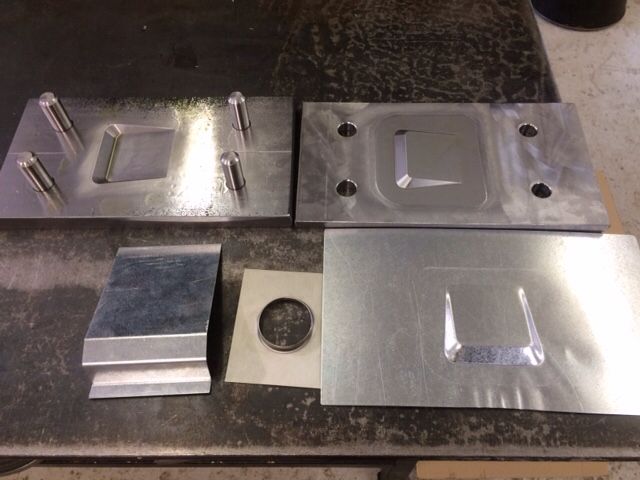 I had another look at the old sills and it dawned on me. Those two 8mm beads at the bottom,either side of the bit I was forming. Seen better on the drawing. 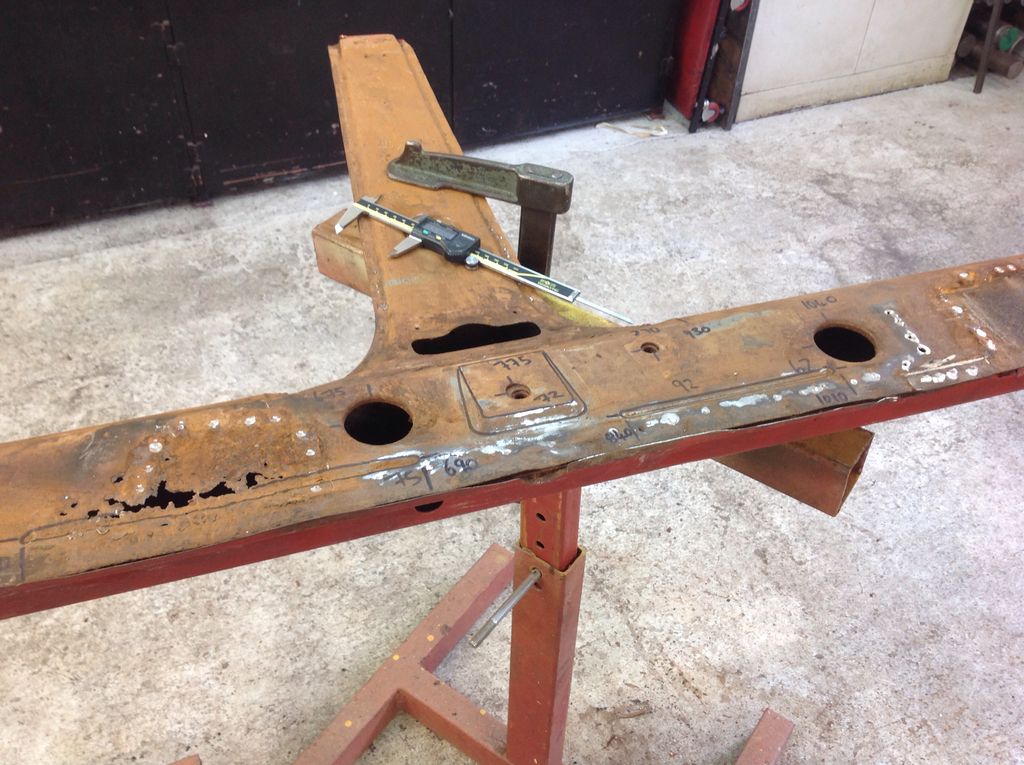  They are not there too look pretty. They serve no purpose once on the car,and are not seen. What they are are brakes. When you press metal into a shape, the metal has to come from somewhere. On my first attempt, the metal was drawn from the edge,hence the pucker marks. There isn't enough material there any more as its been drawn into the form. When production press tooling is made, this is taken into account. Your blank is clamped before you start the drawing process between stripper plates. These are spring loaded. So when the press closes, the material is clamped. The press closes more until the spring pressure on the stripper plate is overcome. Only then does the punch contact the blank and forming starts. How the brakes work is that the lower stripper plate will have a 10mm half round groove in it. The top stripper will have an 8 mm groove in it which had a bit of 8mm round bar pressed in it. As you start to form the material is drawn into this and the rate it can move is slowed right down. This results in the material having to stretch into the form....and your blank stays nice and flat, no pucker marks. Now that we are all still all unclear on that, I needed to try out my solution. I needed a simple way of clamping the blank before the punch started forming. Easier said than done without going to all the hassle of making a proper press tool with stripper plates etc. What I wanted to try was something that had been raced and rallied.....
|
|
|
|
|
|
|
|
So I started making the tool for the reinforcing inside the sill where the safety belt bolts on 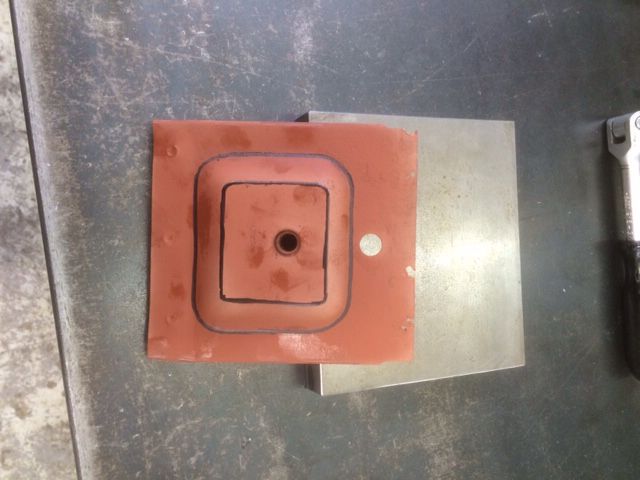 Roughed out a pocket 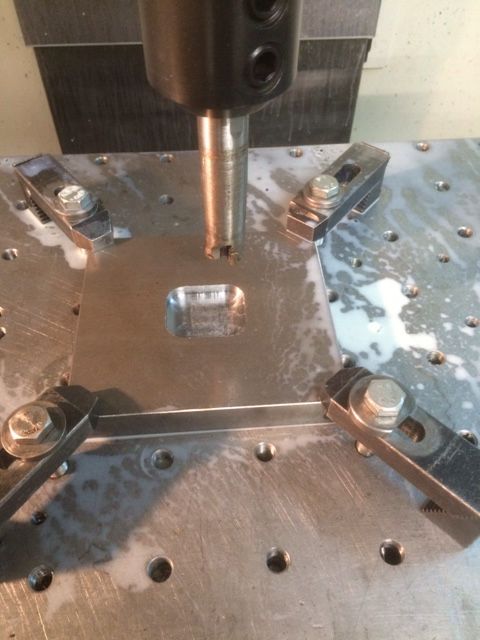 Machine the taper in and cocked it all up. For some reason the way I programmed it,the cutter was orbiting around in the corners and created a huge undercut in the sides. curse word. 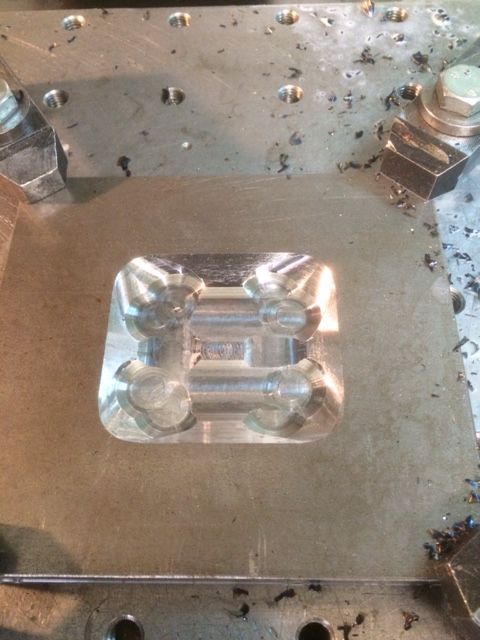 So welded it up and re machined.  The answer to my problem turned out to be an old mudflap ,suitably butchered,from a rally car..... 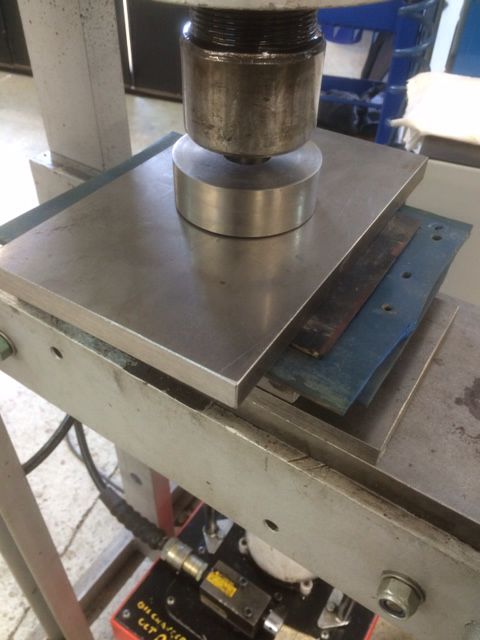
|
|
|
|
|
|
|
Slap a big bottle jack in it, pump the handle vigorously, and call it done? Seems like youre finding excuses not to wade in.  One step ahead of you there. Feel your pain. As did I when I realised my novel ,original ,idea was neither, and that it had been done already. Have already ordered something along those lines 
|
|
|
|
|
|
|
So, as for my novel idea, it turns out this was used during the WW2. It sped up production,saved material and made it quicker to manufacture the tooling. This is what I an enjoying about my build. Finding solutions to problems. Went off on a total tangent and looked at how this technique was used to manufacture aircraft parts. My idea was very similar, just materials used have changed in the last 70 odd years. They used rubber blocks, I used urethane. So, instead of drawing, making, polishing etc male and female parts of a tool, you only make the female side. It's quicker to draw and machine than the male side. You no longer need to work out clearances etc so that when the two halves of the tool are all the way closed,there is the correct space for your blank. First attempts on a sick press  More urethane added  Couple of bits chucked into the cavity. If press was working properly this could be pressed in one go. 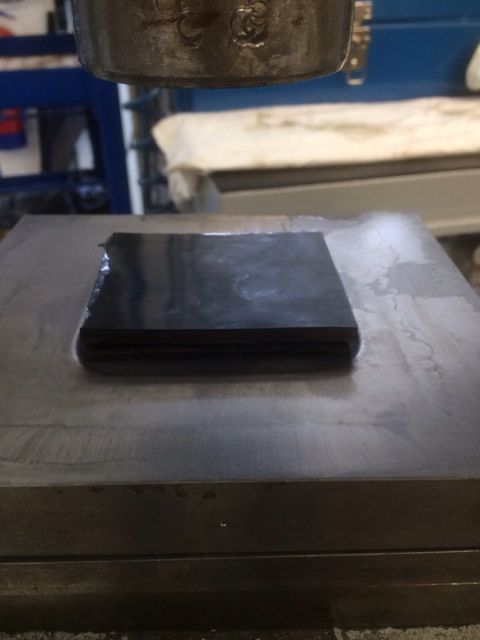 Finished part  No pucker marks and totally flat. Tool rough as hell, un polished. This speeds the process up so much. That part, including the drawing takes less than half the time to make.   Spurred on by the simplicity of all of this, it's made me totally rethink two panels I was dreading to do. Have ordered all the bits I need to make a new type of press..bit ghetto style, but sure it will work......
|
|
|
|
BiAS
Club Retro Rides Member
Insert witty comment here
Posts: 2,231
Club RR Member Number: 147
|
|
|
Beautiful! Loving your approach to this, I'm learning all kinds of stuff second hand through this thread and I'm definitely trying some of your pressing discoveries myself at some stage. I'd always hammered the puckers out and never really thought about how to not get them in the first place, thanks for the research and thorough picture taking. 
|
|
(car+wheels)-rideheight=WIN
|
|
|
|
|
Brilliant, thanks for taking the time to share your work, it's one of the best and most educational threads I've read.in years.
so are you just using a block in the middle and a flat sheet of urethane above? Results are great.
Brian
|
|
|
|
|
|
|
I'm glad I came across this thread, thanks for sharing!!!
|
|
|
|
|
|
|
Brilliant, thanks for taking the time to share your work, it's one of the best and most educational threads I've read.in years. so are you just using a block in the middle and a flat sheet of urethane above? Results are great. Brian Die plate on the bottom,blank on top of that. Couple of bits of urethane on top of the blank. Flat plate on top of the whole lot and into the press. Have ordered some thicker urethane and in a couple of different shore hardness's as I feel the one lot I have is a bit soft , and the blue stuff seems a bit hard. Very promising results so far....
|
|
|
|
|
|
|
Better seen here. Bottom two plates are part of the press,thicker plate on top of those is the die plate with the form machined into it 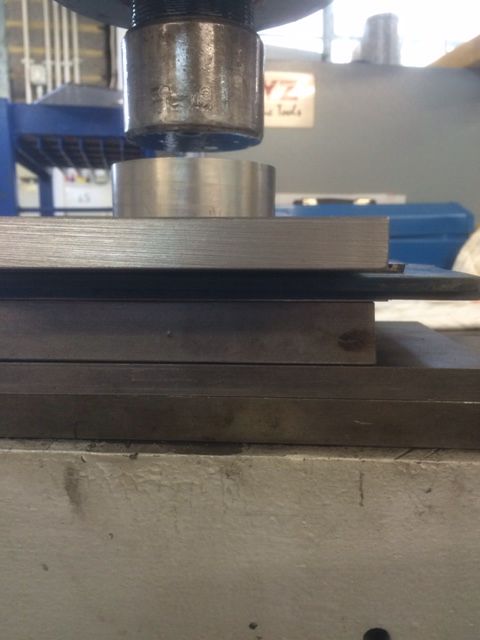 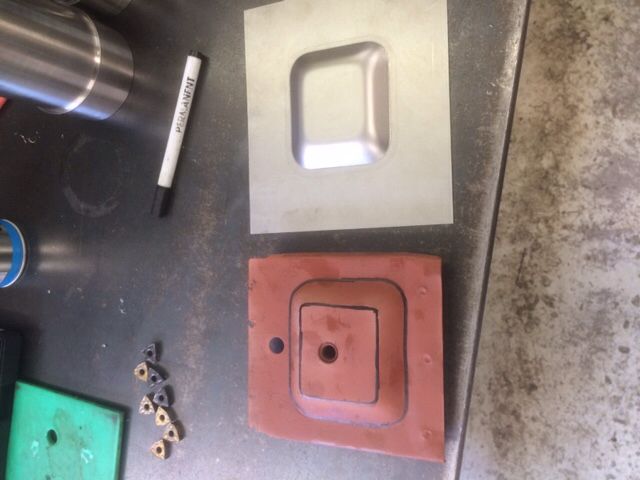 And in other news.... 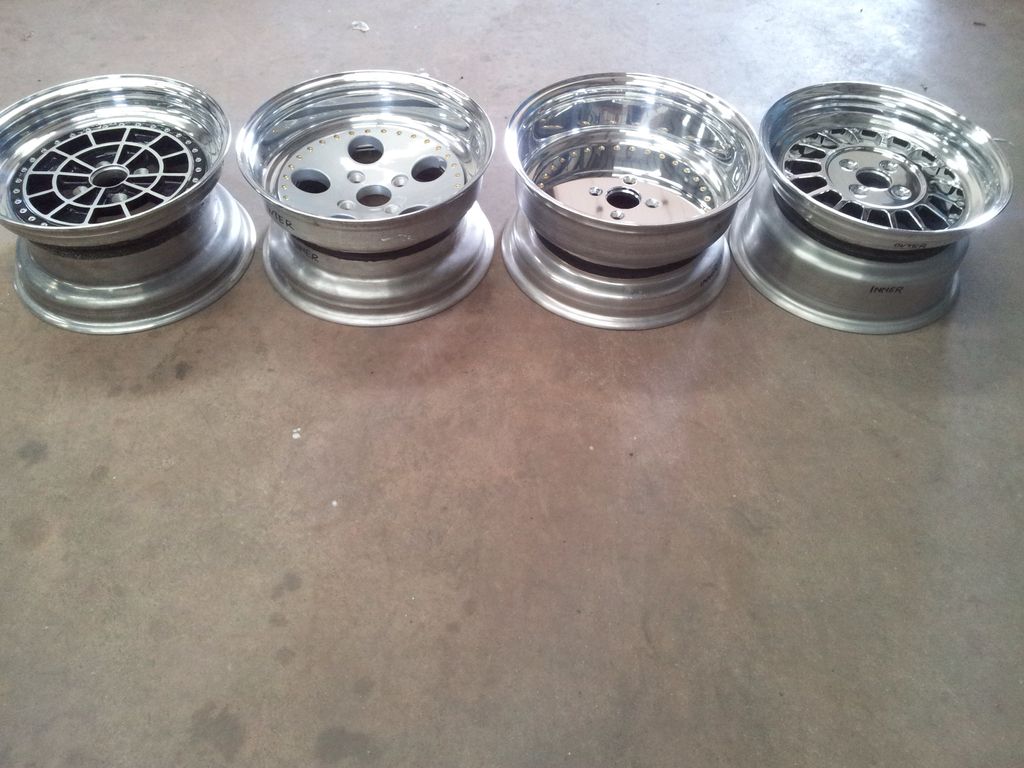 I have always wanted to make a set of custom wheels. So when these samples came up, I grabbed them. Unused, they are a great source of lips and barrels. A winter project to make centres .....
|
|
|
|
|
drexel
Part of things

Posts: 19
|
|
|
Absolutely incredible, jaw dropping stuff. I'm in awe, and feel massively inadequate.
|
|
|
|
|
|
|
I'm amazed that you have pressed that shape perfectly with only the female die and a big rubbery block. What sort of pressure is required? Could you press shapes with your general garage press with hand pump or do you require something with a bit more kick? Fantastic builds by the way.
|
|
Last Edit: Jun 9, 2015 19:03:47 GMT by jonsey
|
|
|
|
|
Hmm - your pressing appears to be of far better quality than the factory pressing 
|
|
|
|
|
|
|
I'm amazed that you have pressed that shape perfectly with only the female die and a big rubbery block. What sort of pressure is required? Could you press shapes with your general garage press with hand pump or do you require something with a bit more kick? Fantastic builds by the way. It's not using mega pressure. Press is well sick. It looks like a bit of a homebuilt press using a hydraulic power pack similar to an enerpac 10 000psi unit. Not sure on the tonnage of the ram. Looks terminally ill,have the ram apart and have sent the seal pack away to the company that supplies all our seals to see if they could match them up. Bear with me a week or so, have something I want to try out. It's in the post and should arrive the next couple of days. That should tell you wether or not a shop press would work. As a guess I would say at least 50% of your tonnage is used to deform the urethane block,so only about 50% of the Rams pressure is available to actually form your part. Think the absolute minimum tonnage would be about 20t. Time will tell.....
|
|
|
|
mylittletony
Posted a lot
 
Posts: 2,391
Club RR Member Number: 84
|
|
Jun 10, 2015 13:39:14 GMT
|
hero
think that sums it up nicely.
|
|
|
|
|
|
Jun 10, 2015 18:27:02 GMT
|
Just seen your thread for the first time. Wish I had of seen it end of last year, little old lady in Howick KZN sold her RX2 for R7000.so she could go visit her family. Last I heard it had been sold to a Mr Singh who pulled the motor to put in a Nissan 1400 bakkie (very sad) and the body sold on to another indian in Pietermaritzburg for R3000. Ive seen a couple of others in scrap yards around Mooi River and PMB. Will keep some eyes open for you as these are my regular haunts.
|
|
No my car is not modified its just had an update!!!!!!!
|
|
|
|
Jun 10, 2015 19:20:35 GMT
|
Just seen your thread for the first time. Wish I had of seen it end of last year, little old lady in Howick KZN sold her RX2 for R7000.so she could go visit her family. Last I heard it had been sold to a Mr Singh who pulled the motor to put in a Nissan 1400 bakkie (very sad) and the body sold on to another indian in Pietermaritzburg for R3000. Ive seen a couple of others in scrap yards around Mooi River and PMB. Will keep some eyes open for you as these are my regular haunts. Only started the thread couple of weeks back  Have pretty much what I need, but if you do find anything, give me a holler !
|
|
|
|
|
|
Jun 10, 2015 21:51:07 GMT
|
I saw those ex sample rims on ebay a week or two back , glad to see they've gone to a worthwhile cause . I seem to remember them on displays at VW shows on the dubmeister trade stand a few years ago !
|
|
You've been telling me you were a genius since you were seventeen ... in all the time I've known you I still don't know what you mean !
|
|
|
|
Jun 11, 2015 14:57:58 GMT
|
Had to register after lurking for some while and just say that I'm blown away by your skills. Enjoying the stories behind things as much as the fantastic fabrication
|
|
|
|
|
|
Jun 11, 2015 16:01:24 GMT
|
Thanks for the kind words , as always guys! So, it was time for plan b. Found a lump of 150mm dia steel, turned the end down and cut a 3"x 12 Unf thread on it. 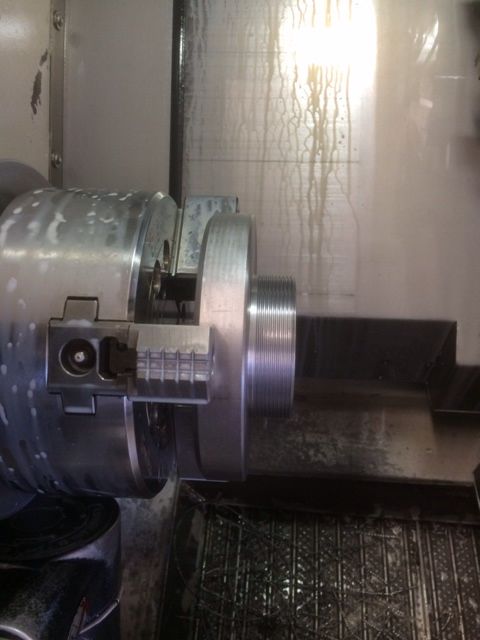 This got screwed into the top of the press where the hydraulic cylinder normally resides. Got an air over 20t jack from the bay of Flea. 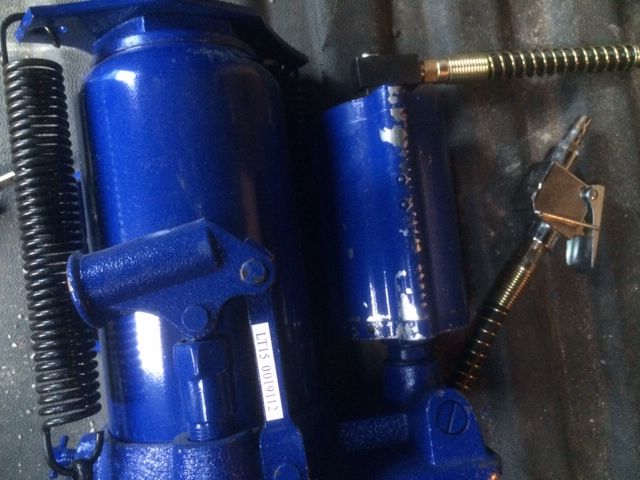 Supposedly CE approved, tuv gs approved. Now dip me in chocolate and throw me to the lesbians if I sound a bit cynical, but surely if it was all these things that it said in the ad,it might be marked as compliant? It might come with a certificate? Nothing. Nada. Zilch. Made in China, that's all, but at least China was spelt correctly. Tried it out. Boo. No joy. So, either you need more than 20t which maybe. Or maybe my press isn't as knucking fackered as I originally assumed? I do know the press isn't as strong as it used to be. So, think I need to consult a Chinese friend of mine. I know what won ton soup is. Maybe this jack was rated in soups.... Who knows.. So, plan b epic fail. Onto plan C. This just happened to magically appear. 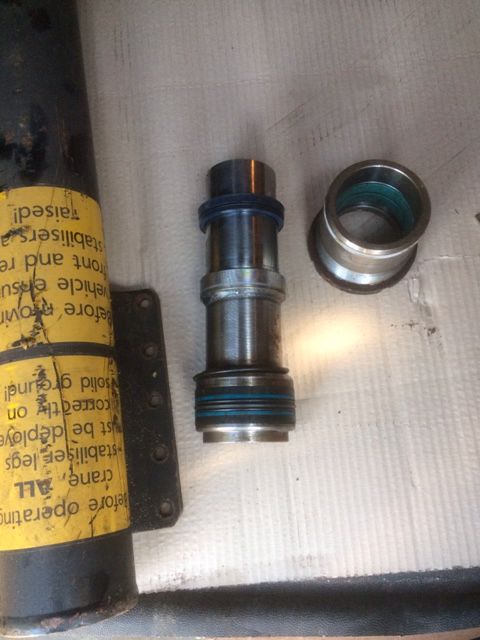 It's the remains of a hiab leg after said leg has been used to remove a gate , the gate posts and half a fence, lol It's nearly twice the diameter of the ram in the press at the moment. Seeing it was cheaper than stealing ,it would have been rude not to utilise it....
|
|
Last Edit: Jun 11, 2015 16:02:57 GMT by Deleted
|
|